Environmental Authority
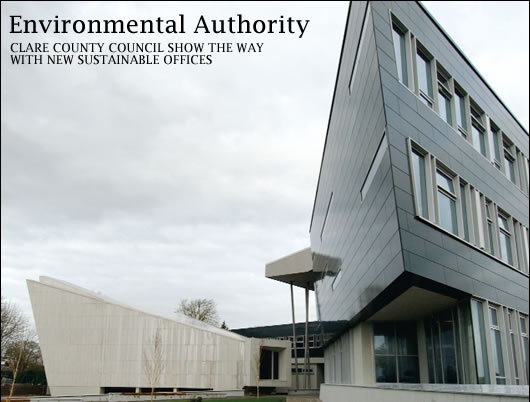
As long term readers of Construct Ireland will recall, the mainstreaming in recent years of sustainable design and construction has been exemplified in many innovative local authority offices. John Hearne visited Aras Contae an Chláir, and discovered a building which attempts to holistically minimise environmental impact, with attention paid to more than just energy performance and carbon emissions.
The new County Buildings in Ennis represent another bold step in sustainable design in Ireland, taken once again by a local authority. Behind the striking clash of angles along its façade, the range of innovations include a natural ventilation strategy, energy generation from locally grown and processed woodchip, solar water heating, a cutting-edge storm water control system, together with a carefully chosen suite of sustainable materials. Built on an existing site on New Road in the town, the building had to fit into a residential, low rise, low density context. A four-storey spine block runs north/south in the centre of the site, at the furthest point from the surrounding houses. To the west, and perpendicular to the spine, two three-storey finger blocks sit in a landscaped park. A public concourse runs along the western façade of the spine block, linking it to the eastern gables of the finger blocks. The southern most of these houses the council accommodation, incorporating a double height council chamber. And of course, just to prove that things haven’t changed all that radically, the design has also had to work in the necessary evil of 300 car parking spaces.
The public concourse which runs for 56m through the centre of the building operates both as its civic heart and its operational lung. “From the beginning the concept of the atrium was there,” says Roldan Jacoby, project architect with Henry J Lyons & Partners, “partly as a civic space, but it was also part of the natural ventilation strategy.”
M&E consultant Stefan Zielinksi of RN Murphy Consulting Engineers explains how it works. “Basically as the temperature inside the building increases, the windows open both on each floor and also at high level in the atrium. We have windows on the east and west side of the building, so depending on where the wind is, one set of windows is always closed and one is always open, causing negative pressure which helps pull the air through the building. Then, because of the difference in temperature through the floor plates, you get a natural stack effect up the building to the atrium, so you’ve got two components; you’ve got the stack effect due to the internal temperature of the building and you have the wind pressure. That’s basically how it works and the windows open and close to try and regulate the heat at a maximum of 25 degrees.” The ‘great hall’ of the atrium is wrapped by the open floors of the work spaces, which are linked by bridge walkways that cross the atrium diagonally. The inclined roof is raised above the office roof plate by two metres, providing continuous clerestory ribbons between. These clerestories are critical to the natural lighting and ventilation strategy, providing eastern and western light with automated vents to give cross flow natural ventilation to the public concourse. In addition, manually openable vents at low level throughout the building dovetail with this automatic strategy, while BMS override buttons give primacy of environmental control to staff. By using natural ventilation instead of air conditioning the county council estimates it has saved approximately 260MW of power and 120 Tonnes of CO2.
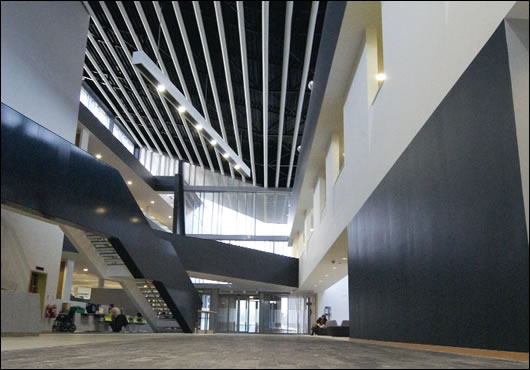
Aside from being the building’s main circulation area, the atrium acts as the lungs of the building’s natural ventilation strategy
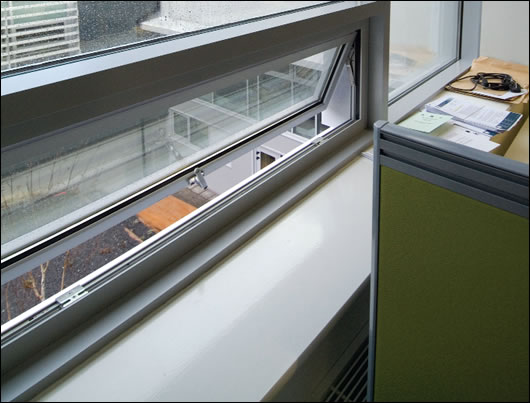
Low level windows open manually, while high level windows are operated by the BMS
The passive stack natural ventilation system removes the need for air conditioning in most areas of the building, serving approximately 65% of the gross floor area. Mechanical ventilation was required in the communications room, the council chamber, some meeting spaces as well as - because it was a late addition to the design – the mayor’s office. These systems are however fitted with heat recovery units. The efficacy of natural ventilation is facilitated by the open design; air can move unimpeded from one side of the building to the other. Where enclosed offices are required, the design team came up with an elegant solution to avoid mechanical extract and bring these spaces into the natural ventilation strategy. “This is a bespoke system we developed with McNamaras (main contractor Michael McNamara & Co).” Roldan Jacoby explains. “It’s based on a typical partition system. We incorporated a timber panel which has an acoustic absorption material in the centre, and that will aid the natural ventilation from the room using a transfer grille…The air can still pass through but there’s this acoustic absorption system for privacy.” With the building yet to see a summer, the team relied on thermal simulations to assess the efficacy of the passive stack system. Setting 25 degrees as a threshold comfort value, they estimate two to three days a year during which temperatures will creep above that value.
In a building of this nature, the cooling load is more onerous than the heating load. To that end, the materials used seek to mitigate against heat generation. Exposed pre-cast concrete slabs in the ceiling, together with in-situ concrete pillars absorb heat during the day, then release it slowly during the night. Substantially glazed facades in combination with high (3.2m) ceilings and relatively shallow plan depth mean that the need for artificial lighting and the consequent electrical load is significantly reduced. Conversely, the requirement to control solar glare and overheating becomes more important. The relatively close proximity of the parallel finger blocks limit solar gain, particularly in the lower storeys. “The finger blocks are laid perpendicular to the main spine block.” says Jacoby. “The main criteria here are that you would have north/south facing working spaces with courtyards in between. We have brise soleil fitted to the windows on the southern aspect. This is glare prevention and also heat gain control; you don’t want to get direct sunlight in there.” Circulation spaces in the finger blocks are sited along the southern perimeter, with working spaces inset into the building to avoid problems with direct sunlight. “Most of the offices, the cellular offices are on the north side, where they have better light for working, also less glare and less heat gain, which is vital in an office environment where you get loads of heat gain from computers and lighting.” The design also takes into account the fact that western light is one of the most difficult to deal with. “We located all the cores: toilets, kitchens on the west to avoid having windows towards the west.” says Jacoby. “You can see most of the western elevations are pretty much blind, so as to avoid this heat gain from the west.”
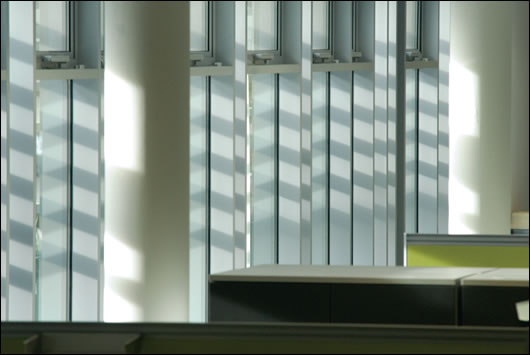
Shadows cast by the brise soleil into the offices and one of the concrete pillars which contributes to the building’s heating and ventilation strategy
To conserve energy Clare County Council decided at an early stage in the design process to increase thermal insulation thicknesses in the building to exceed the current requirements of the domestic Part L building regulations. This, according to the engineer, will result in an annual energy saving of 16MW. While there were over 50 different fabrics used in the build itself, basic wall construction is 215mm blockwork with 12.5mm foilback plasterboard and 100mm of Kingspan K15 insulation. Flat roofs contain 150mm of Stryozone extruded polystyrene insulation board. The atrium roof is Tegral Aluseam with 180mm of Knauf glasswool quilt insulation. Concrete was dressed in Elotene, a rainscreen breather, along with the K15 boards. “A belt and braces job” says John Dickie of McNamaras.
The external envelope is clad in a rain screen formed by dark grey Trespa TS-300 panels on hidden aluminium rails, allowing moisture to escape the building through the cavity, providing a healthier working environment. Andy Bester of Trespa, whose products are supplied in Ireland by façade specialists Williaam Cox, explains that the panels are manufactured from timber grown in sustainable forests, including FSC and PEFC certification. “Because we’re using fibres rather than paper, we can use 99% of the tree, we can use all the bits and pieces, all the twigs, and there’s no chemical preparations. The only thing we use to clean the fibres is water, so we bring it into the factory in chips, we grind the chips into small fibres, we inject them with hot water to take out all the grit, so straight away from day one, it’s a very friendly process…and the way that we make it means we can take waste Trespa, we can regrind it and put it back into the mix.” While the Ennis project uses 100mm of K15 under the panels, Bester suggests that by increasing the standoff between the panels and the walling, you can insert additional insulation and even further boost the thermal performance of the wall.
Sections of external wall were dressed in the Sto Therm Classic External Wall Insulated system, incorporating 120mm EPS as the insulant core. This provides a cement-free decorative render finish which delivers a U-value of 0.27 W/m2K. “The system,” says John Sudron of Sto Ltd, “prevents heat from escaping from inside buildings…By using an external wall insulated system onto single leaf wall construction for new build.” The system has the advantage of freeing up internal space while avoiding the risk of thermal bridging. “The system protects building structures by maintaining a constant temperature in the masonry. The entire structure is encapsulated in a protective weather-proof envelope which can help to reduce heating and cooling costs as well as pollutant emissions.” Ecocem was specified for all in-situ concrete while columns, beams, retaining walls and slabs were precast concrete. “The glazing used has a U-value of 1.3 W/m2K,” says Stefan Zielinski, “and solar correction factor of 0.31. This glazing has been used throughout the building to help reduce heat gains and losses.” The glazing was supplied by CareyGlass and fitted into windows by Season Master.
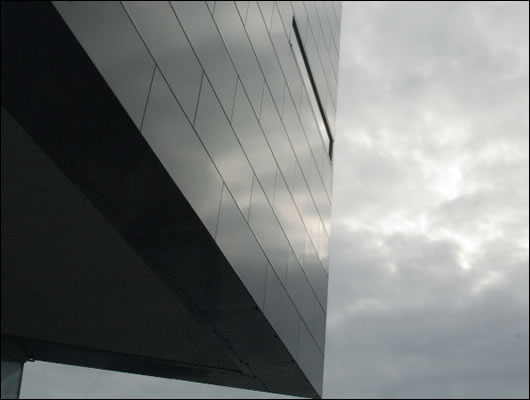
The external envelope is clad in a rain screen formed by dark grey Trespa TS-300 panels manufactured from timber grown in sustainable forests
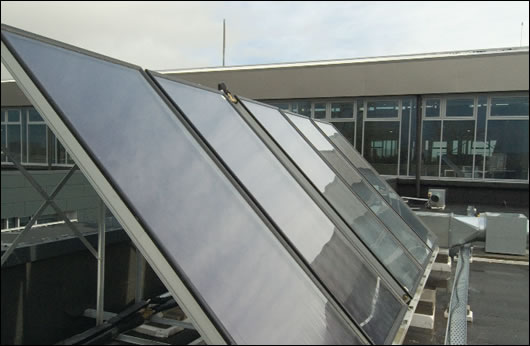
One of the decentralised flat plate solar arrays, which contribute towards domestic hot water supply, with a separate array for each department of the council
110m2 of Calpak flat plate panels on the roof will provide around half of the building’s hot water requirements. Provided by RVR in Kerry, the panels are divided between the finger block and spine block roofs, and form groups of self-contained, decentralised arrays, each of which serves an individual department. “It’s a twin coil system.” Des Flynn of RVR explains, “so it’s indirect; a loop up to the collector where antifreeze is pumped around it, and the other coil then is connected back to the main heating system. The controller is on the solar side of the system, and it basically has a sensor in the panel itself and in the cylinder. When the heat available from the panel is six degrees greater than in the cylinder, it starts pumping the fluid around. Then, when the panels cool down and the cylinder is warm, it stops pumping. It also has an output where it can call on the backup system as well, so it can basically send a control signal to indicate that there isn’t a solar load there”. 500L tanks are provided for larger departments with 210L tanks for smaller ones. Contribution to the total hot water demand depends on usage patterns in each office, varying between 30% and 45% in the smaller departments and between 45% and 50+% in the larger. Backup comes from the central heating system. “The real reason we went self-contained,” says M&E consultant Zielinski, “originally even before we went solar, was the fact that we didn’t have room to put big storage in. We didn’t want a central system because we didn’t want to have to run miles of copper pipe to get to the extremities of the building, so we decided on a decentralised system.” He estimates that the solar system delivers an energy saving of 50MW along with 10 Tonnes of Carbon Dioxide.
Primary heating comes from a KOB Pyrot 540kW woodchip boiler supplied by Clearpower and backed up by a 380kW gas boiler located in an underground boiler room located between the carpark and the eastern edge of the building. “The gas boiler is an assist boiler” says John Heffernan of Clearpower. “The maximum design load of the building is between 600 kW and 700 kW, so that means that on a very cold morning, the woodchip boiler may not provide the entire load, and the gas boiler will provide the additional heat… That’s the best way to design woodchip installations: To have the boiler running consistently at the base load, then to have a flexible means of providing the peak. Woodchip boilers, they take a little longer to get to temperature and they take a little longer to modulate up and down. A gas boiler, you just switch it on and you get 380kW straight away. Because burning wood takes a little longer, it’s better to run the boiler all the time.” In this mode of operation, the boiler can achieve 92% efficiency on woodchip with a 25% moisture content. Getting the woodchip down to 25% is Pat Moloney’s job. Through the winter months, his company, Clare Wood Chip Ltd will be supplying the council with 10 tonnes of chips per week. The raw material comes from forestry thinnings which he collects and takes to his Flagmount premises in East Clare for drying and chipping. At harvest, the moisture content in the pulp stands at around 60%. Getting it down below 30% takes between twelve and eighteen months of drying. “Its air-dried,” Maloney explains. “It’s covered with a special recyclable paper that you can chip with the pulp. Once I’ve my timber stack outside, up on a high hill, the wind will dry the timber down to below 30% moisture.”
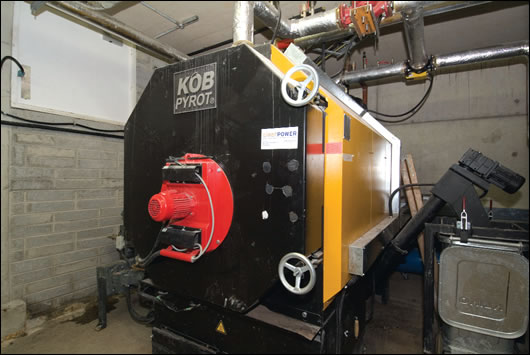
Primary heating comes from a KOB Pyrot 540kW woodchip boiler backed up by a 380kW gas boiler located in an underground boiler room, between the carpark and the eastern edge of the building
His company is one of the two kick-started by the Clare Wood Energy Project, a leader-funded rural development initiative set up three years ago to look at different ways of harnessing Clare’s forestry resources. “Clare has the second highest forestry cover in the country after Wicklow.” says Dóirín Graham, CEO of Rural Resource Development Ltd. “We’ve a huge forestry resource, and a large proportion of that is owned by farmers…We looked at the forestry and we knew a lot of it was coming to the stage where it needed to be thinned, so there was all this pulp wood, which can be used for chip, = coming onto the market.” Three years ago however, there was no viable market for chip, so one of the first tasks for the project was to tackle the demand side. “We knew too that without a local supply chain in place that it wouldn’t be possible for people to make the commitment to woodchip because security is hugely important. It’s always the first question that people ask us; is there enough pulpwood in the county and will there be plenty to supply me? Not just this year and next year but in the future, in fifteen and twenty years time years.” Tying those two strands together – demand and supply – is now starting to pay off. Two supply companies are up and running, while the new county council installation will bring to three the number of large, industrial size boilers in the county. The project takes a pragmatic, arms-length approach on the demand side, providing independent advice to assess the financial and technical feasibility of the wood chip option for particular = sites, rather than blindly advocating the solution in all cases. In addition, the suppliers themselves do not sell woodchip as such, they actually sell heat. The price paid depends on the heat generated by the fuel as opposed to the tonnage, thereby incentivising the production of high quality fuel. “If we can get, over the lifetime of the project, half a dozen commercial size boiler installations, the market demand, the critical mass that you create is enough for the supply chain to develop with some sort of commercial foundation.”
The specially constructed subterranean silo in which the chip is stored and automatically fed to the boiler presented particular difficulties to the construction team because of the sheer hardness of the rock. In order to counterbalance the energy used in rock breaking during construction, an onsite crusher processed all of the material removed for reuse in other parts of the site.
John Heffernan of Clearpower says that final decisions on how exactly the woodchip and gas boiler will co-operate have yet to be nailed down. In principle however, if the temperature in the building falls below a set point – if the temperature in the common return header falls below say, 60 degrees, the gas boiler is set to come on, and will stay on until the temperature in the header rises to another set point. “If the temperature in the return goes above a third set point,” says Heffernan, “then that means that the woodchip is providing more than enough heat and the boiler will go into slumber mode, which means it’s ticking over, then when the temperature drops below that set point, the woodchip gets the signal to turn back on again.” Clearpower also provide remote monitoring services across a broadband connection integrated into the boiler’s control system. And of course, all of the heating systems are controlled by the BMS. According to the engineer’s calculations, the wood chip boiler accounts for approximately 90% of the annual heating requirement, saving approximately 93 Tonnes of CO2 compared to a traditional building of similar size.
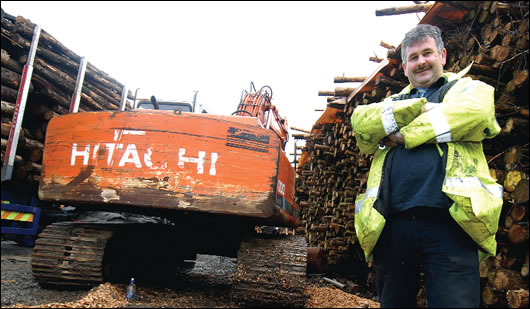
Through the winter months, Pat Moloney’s company, Clare Wood Chip Ltd will be supplying the council with 10 tonnes of chips per week
Heat is distributed via three air handling units in the areas that require air conditioning, while underfloor heating has been installed in the 650m2 Atrium. This is Pecs piping with an oxygen barrier. “In the main offices,” says Stefan Zielinski, “we have convector heaters with a low water content, so they’re fast to heat up. They’re 90% convective and 10% radiant.” This system was chosen primarily with the natural ventilation strategy in mind. “You don’t want ordinary radiators,” he goes on, “that once they’re hot, they stay hot. With these ones, once you turn off the flow they very quickly cool down. You don’t get the massive swings you do with a radiator…so it should give us better control of temperature in the building.”
The lighting installation uses T5 fluorescent lamps where possible, incorporated = in a suspended fitting with direct/indirect lighting. Due to their greater lumens/watts ratio over the current T8 lamps, they’re far more energy efficient. All individual and open plan office areas include both manual and automatic controls. The light level detectors will ensure that lighting levels are maintained within the office area, allowing artificial lighting to dim while taking advantage of natural daylight. The use of lighting controls as described above should result in an estimated annual energy saving of 26MW and 16 Tonnes of Carbon Dioxide.
All of the carpeting used through the open office spaces is provided by Interface FLOR, a multinational with a strong environmental ethos. Energy efficiency programmes and a commitment within the company to renewable energy has resulted in a 60% reduction in CO2 emissions on an absolute basis since 1996 and further changes to their production process have allowed for an 80% reduction in water intake per square metre of production for modular carpet. The company runs a carbon offsetting programme to complement employee travel requirements and places a strong emphasis on sustainability through internal training programmes. For a service cost, the company will collect used carpet tiles on the purchase of one of their products and will deliver these to a local partner – in Ireland this is Arc Recycling in Kildare – for reuse or recycling. The tiles themselves are manufactured in a plant in Craigavon, where that same sustainable ethos is continued. ISO 14001 accredited, the site runs off 100% green electricity, while every by-product of the production process is re-used.
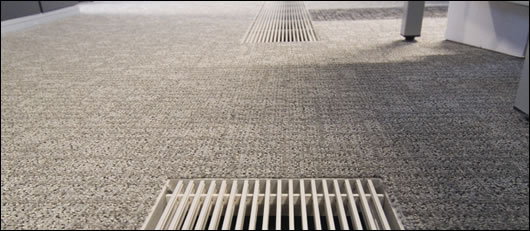
Interface Flor, who have long been committed to reducing their environmental impact, supplied the Metallic Weave carpet used throughout the open office space, seen here with a trench level low water content convector heater
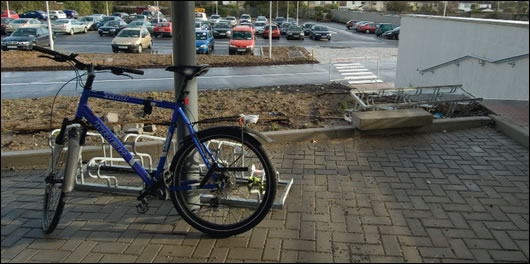
A solitary bicycle reveals the extent of the environmental challenge in terms of affecting behavioural change. As with the car parks, the bicycle parking area is paved with Aquapave, a sustainable drainage product
Much of the furniture used in the building embodies a high degree of sustainability. Humanscale Liberty Task Chairs, supplied by Bob Bushell Ltd in Dublin are manufactured from 50% recycled materials and are more than 95% recyclable. Recycled and/or recyclable materials account for approximately 85% by weight of all materials used in Humanscale products shipped in 2004 and their packaging contains approximately 40% recycled content. Desks and storage are from Konig and Neurath, another company with ISO environmental accreditation and detailed environmental policies in relation to all materials used in the manufacturing process. The company says that composite materials are not used in production and all furniture can be recycled after use.
Other noteworthy features of the Ennis development include an office recycling system designed by the architects, and also sheltered bicycle parking facilities adjacent to the carpark. On the day we visited however, one lone bike languished here.
The good news about the carpark is that it features a highly innovative sustainable urban drainage system. Provided by Roadstone, the Aquaflow storm water source control system consists of permeable paving blocks which allow surface water to drain through a pollution control filter bed over an Inbitex geotextile into an underground stone sub-base storage area. “The sub-basestone nominally consists of 250mm depth of 63-10mm & 100mm of 20-5mm,” Gay McGrath of Roadstone Dublin Ltd explains, “both produced to a specification which ensures 30% voids for the storage of the storm water. The total area of 2,200 m2 gives an actual storage capacity of approximately 440,000 litres. The ability of the Aquaflow system to filter out harmful pollutants before discharge into rivers and lakes has been proven by extensive research over the past fourteen years.” In addition to replicating the natural dispersion of water through the ground, the system removes the need for manholes, gullies, drains, pipework or any of the other works associated with conventional systems.
All in all, Clare County Council should be proud of their new home’s environmental credentials. Encouragingly for such a building, efforts to become more sustainable are no alone restricted to minimising energy consumption for heating, cooling and lighting. An attention towards reducing environmental impact runs through the building’s design and specification, including everything from furniture, to carpets, to many of the building materials used.
Project details
Client: Clare County Council
Main contractor: Michael McNamara & Co.
Architect: Henry J Lyons
M & E engineer: RN Murphy
Façade glass: CareyGlass
Rainscreen: Trespa /Williaam Cox
Insulation: Kingspan
External Insulation: Sto
Solar thermal: RVR
Wood chip boiler: Clearpower
Wood chip supply: Clare Wood Chip
GGBS: Ecocem
Permeable paving: Roadstone
Carpets: Interface FLOR
Furniture & fit out: Bob Bushell
- Articles
- Sustainable Building Technology
- Environmental Authority
- Aras Contae an Chlair
- Clare county council
- office
- BMS
- building management systems
- interface flor
Related items
-
Seal of office
-
Adaptation sensation
-
Office romance - Passive house supplier walks the walk with new office & factory
-
Mies en Scéne - Iconic Dublin offices get deep green treatment
-
It pays to invest in healthy, green offices — WorldGBC
-
Opinion
-
Thermal bridging
-
Isover awards
-
Carlow A1 upgrade
-
Zero waste
-
Clonakilty eco house
-
Cutting oil dependecy