From Policy to Practice
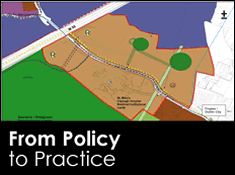
As policy makers start to set mandatory low energy and renewable energy requirements as conditions of planning, the ability of the construction industry to find sound low-cost ways of achieving the new standards is becoming a key factor. John Corless speaks to leading sustainable building consultant Jay Stuart of Delap & Waller EcoCo and Paul Gilmartin of Ecobead to discover an approach with enormous potential for en-masse usage.
Jay Stuart is an Architect and Sustainable Building Consultant. “I advise and work with developers, architects and contractors to design and build sustainable and low energy buildings,” he tells Construct Ireland. “I am currently working with two developers who need to meet the Fingal initiative. This initiative requires that within certain local area plans dwellings must use 60% less heat energy than dwellings built to minimum Building Regulation standards and 30% of that energy must come from a renewable source.“
Technically this is relatively easy to achieve so the main issue is cost and the ability of the industry to build to the required standards. However Jay believes the requirements can be achieved cost effectively and is about to prove it on a small project in Leixlip, Co. Kildare. Tenders have just been returned for 27 houses in this low cost housing scheme which are—coincidentally—designed to use 60% less energy (for space heating and hot water) at a cost of €100 per ft2.
Jay thinks this is excellent value for the high performance specification and not much above the costs of most speculative housing built to the minimum standards. “The added value and benefits are understood and appreciated by my clients and I believe the market is already aware of the need for higher performance housing.”
“My clients asked me to work with them to build energy efficient houses within their very tight budget. I researched and proposed the most cost effective form of construction I could which was airtight, well insulated and with designed ventilation. Before I knew about the Fingal proposals I had calculated these houses would use less than 50 Kwh/m2/yr using the HER software.”
Houses designed by Respond Housing Association. The houses in Jay Stuart's Leixlip project are based on this design and will be very similar
Calculating the Target
“Fingal started with 50 kWh/m2/year as a target together with 30% renewable energy. They then went to industry and several building energy experts to ascertain if their targets were achievable and cost effective for developers. To avoid confusion and to make their targets easy to calculate the advice they received was to use a calculation tool such as the Heat Energy Rating (HER) software and to move from an arbitrary 50 Kwh/m2/yr to a more flexible and sensible 60% reduction in energy use.”
The HER has been part of the Building Regulations for several years and is used in SEI’s House of Tomorrow programme to demonstrate compliance with the 40% reduction target of this programme.
However the method calculation is likely to change doe to the new Part L of the Building Regulations which came into force on 1 July. These new Regulations replace the HER with the Dwelling Energy Assessment Procedure calculation (DEAP) method which was released on the SEI website on the 29th June as an Excel spreadsheet. This new calculation methodology is being introduced as part of the implementation of the Energy Performance of Buildings Directive (EPBD) and will be used to calculate the Building Energy Ratings for dwellings. It is a more sophisticated calculation method based on carbon performance and includes, for example, methods for calculating the impact of solar thermal collectors.
Meeting the Target
Jay has been building to a high standard for several years now and has identified four priorities for cost effective construction to meet the Fingal requirement:
1 Airtightness
2 Designed ventilation with heat recovery
3 High performance glazing
4 Optimised insulation
So how is the superior performance achieved in his Leixlip project? Jay says that the houses started as standard 3 bed semis but have evolved with the clients into 27 different houses internally. The attics are now warm storage spaces with the insulation following the slope of the roof. Jay says the easiest and cheapest way to improve energy performance in new and existing houses is to add more insulation in the attic. “In Canada some people put 600mm of insulation in the attic. The building code wouldn’t require this amount but people wanting to lose less heat and be more comfortable do this. You don’t need this much in Ireland’s climate but 400 mm of mineral wool is probably optimum.”
The open fireplaces have been omitted as they are inefficient and the open flues lose too much heat. The envelope has a performance specification for airtightness of 1.5 air changes per hour (ACH) and Dwell-Vent, a passive ventilation system has been designed to ensure high air quality standards. Insulation standards exceed the Building Regulations using cost-effective construction methods.
The tender price of €100 sq ft. includes for airtightness blower door testing carried out by independent specialists. The builder will be present when the tests take place and any house that fails to achieve the desired performance has to be made good to the required standard. In practice this is not a problem with sufficient detail drawings, proprietary products for airtightness and some attention to workmanship on site.
Methods of Construction
He is still at the preliminary stage of investigation with the developers he is working with in Fingal. “I find the developers are embracing the Fingal initiative in a very positive way and they are investigating the best way to achieve the requirements and build better buildings. They are very aware the Fingal initiative is moving them towards building dwellings which are likely to receive ‘A’ ratings when the Building Energy Rating system is introduced. This is something they would aspire to anyway.
“To meet the requirements I have been recommending target U-values for all the building elements and together we are analysing the costs and merits of different building methods to achieve these targets. I’ve advised them it may cost about 8% to 10% more to achieve the required performance depending on the methods chosen. There are so many different ways to build a wall, and the wall construction is the most critical element to decide how to build.”
The Solar Air Windows open to show vents at top and bottom
Jay says the best place to locate wall insulation, from a thermal performance point of view, is externally. “You then benefit from the thermal mass of the walls, the insulation is continuous and cold bridging is minimised or non-existent. The structural wall is covered externally in insulation with a waterproof finish on top. This is usually a proprietary coloured render system.
“The next position for the insulation is in a cavity. Partial fill cavity walls are the norm here, but they don’t achieve the thermal performance that the theoretical calculations suggest. It’s almost impossible to install rigid partial-fill cavity insulation correctly. Due to the impossibility of ensuring air cannot get to the warm side of the insulation there is always thermal looping with convection currents in the cavity which reduces the insulating properties of the wall by about 50%. I do not recommend partial fill cavity walls for this reason.
“One solution to this is to use full fill cavity insulation which is very cost effective and has other advantages.” , says Jay. One of the advantages is the insulation is not installed by the blocklayers during wall construction but is installed by specialists afterwards. The cavity is wider to allow adequate insulation to achieve lower U-values. Jay is using 200mm cavities on the Leixlip houses and several other projects to achieve walls with U-values of 0.15 to 0.17 W/m2K.
The quantity surveyors on several projects have compared the costs of a Building Regulation minimum standard partial fill block wall with a 100 mm cavity and 60 mm rigid insulation with a high performance 200 mm cavity full fill block wall. The minimum standard wall costs about €140/m2 while the high performance full fill wall is costing €160/m2. “Given that the partial fill cavity wall doesn’t work very well and the full fill cavity wall works very well it’s worth paying the extra.
“Builders that I am working with have looked at ICF (insulated concrete formwork), timber frame and other options but the full fill cavity is one of the best options in terms of costs and benefits,” Jay says. “When the product came on the market years ago there may well have been problems with it, but now the technology is better and I understand it’s accepted by Homebond, the DoE and Premier Guarantee insurance.”
Jay stresses that air tightness is very important too. “Ordinary concrete blocks are not airtight at all, they’re quite porous and air moves through them quite significantly,” he says. “Traditional dry-lining does not seal the blockwork and they require 15mm of wet plaster to make the blocks airtight. The other possibility for block walls is aerated cement blocks on the inner leaf (Quinn-Lite or similar). They are inherently airtight due to the method of manufacture so you can chase the wall for services without compromising the airtightness. You still have to wet plaster the inside face of the wall because the mortar joints are not airtight.”
Renewable Energy
There are several options to satisfy Fingal’s 30% renewable energy requirement but Jay believes he has found a cost effective solution. “I am proposing developers use wood chip boilers in a community heating system with heat meters for each dwellings.” With wood chips currently selling at around half the price of natural gas Jay says that this is a viable arrangement, but it depends on the density of the scheme.
“Gas is due to go up significantly in price next October and this will make wood chips even more cost effective,” he said. “Over time woodchips will probably track the price of fossil fuel at a lower level, but in the short to medium term, I expect they will remain considerably cheaper. Unless it remains a cheaper energy source it will not be used as the capital costs are higher and it is less convenient than gas or oil.”
“Solar thermal collectors complement biomass heating very well. They are simple, effective and the technology lasts a long time,” Jay says. “The only moving part is the circulating pump which is cheap to buy and easy to replace. I think solar is an excellent option. It means that in the summer, when you have more solar hot water than you need, the wood chip boiler doesn’t have to run at all. In the winter when there isn’t much heat from the sun, the wood chip boiler is working efficiently and is producing both hot water and space heating. In the winter the solar collectors will preheat the water before it goes to the boiler. So it’s an efficient combination and is something I have recommended to the builders I am working with.”
Energy Efficient Boiler
Where renewable energy is not required then it is important to look for the most efficient means to heat water. “Combination boilers,” he says “don’t have a hot water cylinder – these are just tanks where your heated water cools down. It’s more efficient to heat the water just before you use it. I would recommend properly installed condensing combination boilers to optimise the use of gas.”
These vents facilitate the passive solar pre-heating of fresh air, which is then drawn into the building
Ventilation
Jay says “When a building is made airtight it is essential that a designed ventilation system is used and that the minimum requirements of Part F of the Building Regulations are exceeded. The Building Regulation requirements assume the dwelling is not airtight so it is important to increase the designed ventilation rate to ensure high standards of air quality.”
A mechanical heat recovery ventilation system (MHRV) is one way of providing this ventilation and reducing fuel bills according. “If you choose a mechanical means of heat recovery the unit with the fans and heat exchanger is located in the attic or at high level in a cupboard. You can distribute the ducts to each room above the ceiling or in the floor voids. It is separate from the heating system and it provides fresh air which is pre-heated by recovering the heat from the air which is being extracted. The system can recover up to 90% of the heat in the air that is being extracted. ”
The only down side of the HRV system is that it uses electricity to run the two fans. “It doesn’t use much electricity,” Jay says, “but Irish electricity is very dirty, in that it has a high carbon content, is also expensive and it’s going to get more expensive. Although you are saving energy with an MHRV you’re using electricity to make the saving. It’s a heat energy saving but the net carbon saving is not as good as I would like.”
The passive ventilation system, Dwell-Vent that Jay is using in the Leixlip project uses no electricity. The specially designed high performance windows that are part of the system are now available as a proprietary product from Dwell-Vent Ltd. These windows use special trickle vents to bring fresh air into the house. The air that passes between the panes of glazing recovers the heat that is trying to pass through the window and is preheated. The window U-values are less than 1.0 W/m2K. The air moves out of the house in passive stacks which exit from the ‘wet’ rooms of the house, the bathrooms and kitchen.
“This is a passive heat recovery ventilation system with no moving parts or electricity. I used this system in a building at Dublin’s Mater Hospital and it is performing well. I look forward to building the Leixlip houses and demonstrating how well the system can work in housing.” Jay says.
Full Fill Insulation
Paul Gilmartin supplies Ecobead Platinum full fill cavity insulation throughout the country. The insulation material consists of polystyrene beads pumped into the cavity through holes drilled in the wall at regular intervals. In new houses, this process is carried out when the windows are fitted but prior to plastering. The system is self-draining, and a bonding agent keeps beads intact if someone ever opens the wall again, perhaps to retro fit an extractor fan.
“We install in a lot of older houses with pumped wall insulation. Many of the houses have no insulation at all, others have some but it’s not sufficient. These would typically be houses with 40mm of insulation already in place,” he said. “We need 50mm minimum cavity to install our system. This increases the U-value of the wall considerably,” he says. “Existing 60 mm insulation in a typical 100mm cavity will give a U-Value of .37,” Paul says. “Our full fill in the same cavity will give .29.”
Ecobead Platinum full fill cavity insulation. The insulation material consists of polystyrene beads pumped into the cavity through holes drilled in the wall at regular intervals. As can be seen here, there are no air gaps in the cavity, a problem that is difficult to avoid with conventional partial-fill cavity wall insulation
Polypearl is the master distributor in Ireland for Ecobead – a brand now owned by CRH. The company has distributors throughout the country. The polystyrene beads may not be completely environmentally friendly as other techniques used to achieve the requirements of the scheme aren’t either. On the plus side is the fact that it is a move in the right direction and in time building practices and materials will improve their environmental performance.
Good News
The good news is that Wicklow County Council has followed Fingal's lead in bringing energy conservation and renewable energy requirements into Local Area Plans. Dun Laoghaire Rathdown are considering introducing the same requirements into their planning process and others are following this initiative. Fingal County Council now has 7 LAPs adopted which will lead to buildings with a 60% improvement on Building Regulations in terms of heat energy (for hot water and space heating) and a 30% renewable energy supply. In total eight such Local Area Plans are now in place. These are small but significant steps. It’s a pity it takes politicians so long to legislate for the necessary change.
Related items
-
Why airtightness, moisture and ventilation matter for passive house
-
Airtight delight
-
Partel’s airtight membranes now certified for passive house construction
-
Mass timber masterwork
-
Partel obtains EPDs for airtight membranes
-
When is an A-rated home really A-rated?
-
Manhattan modular apartments feature Wraptite membrane
-
Thinking inside the box - Victorian semi retrofitted as a house within a house
-
Partel’s Izoperm Plus achieves passive house ‘A’ cert
-
Superb airtightness result for Manchester ICF house
-
Liquid membranes transforming airtightness work — Blowerproof UK
-
AECB launches new retrofit standard