- New Build
- Posted
Zero carbon
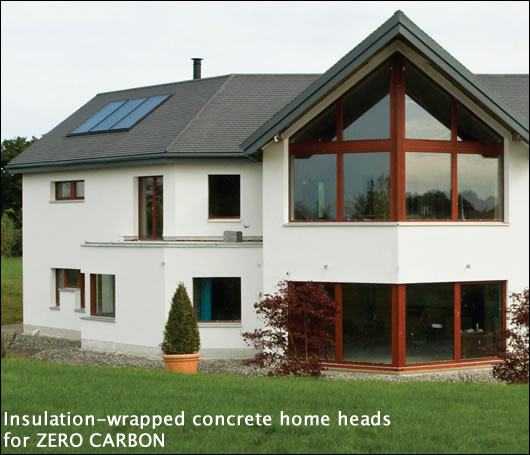
Energy efficiency is about more than just U-values – the building envelope must be airtight and virtually cold bridge free. Construct Ireland visited a single-leaf concrete house nearing completion in Moate which combines an excellent envelope with wind, solar and a range of green measures, with the aim of reducing energy and carbon figures to zero in the home’s BER score.
Self-builder Micheál O’Dowd says the one principal that guided him in the construction of his home in Moate, Co Westmeath was commonsense.
“I realised that if you put in more insulation, you’ve payback from day one and you won’t spend as much as you would have spent going for all these fancy technologies… People were spending €6,000 on underfloor downstairs, and another €6,000 for the first floor, then your heating system could cost you up to €20,000. Suddenly you’re down €32,000 and then you have the running costs after that. I said to myself what is the point of spending all this money? Why not just insulate instead and spend no money on any of that crack and have no heating bills at all?”
That was seven years ago. Since then, O’Dowd has gone to extraordinary lengths to discover the best possible way of achieving this goal. He has completed training courses, attended dozens of trade shows, been in and out of reference houses, travelled Europe and spent thousands of hours on the internet researching his specification. In the process, he’s secured sponsorship from the Irish Concrete Federation (ICF) together with support from several other materials suppliers. Though neither a builder nor an engineer, some of the techniques he has developed to avoid thermal bridging have been taken up by suppliers and used in other building projects.
The overall design concept is to wrap the house in an envelope of insulation. The raft foundation sits on high compressive strength polystyrene. The external walls are of masonry construction; traditional concrete blocks laid on the flat, to give a wall thickness of 215mm. 300mm of insulation is installed externally while a wet plaster finish internally provides most of the airtightness. The external insulation extends down to overlap with the insulated raft and extends upwards to meet the roof insulation, completing the envelope.
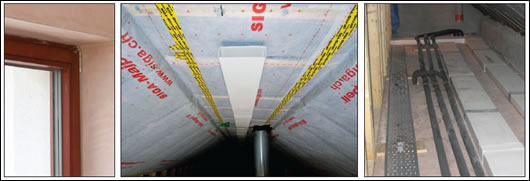
(left to right) the airtightness strategy combines wet plastered walls with a range of Siga products; the HRV duct run was kept as straight as possible to boost efficiencies and trays were installed to keep the electrics neat; (above) strategic planting of trees reduces glare and prevents overheating
Though the project is sponsored by the ICF, O’Dowd says that he had settled on this building method long before the federation was brought on board. “After researching many forms of construction, I always came back to blocks. It’s the most cost-effective way to build,” he argues. “The most important thing for me is it absorbs and stores heat during the day and releases it at night. This gives us a more comfortable living environment by avoiding temperature swings…In this house the block is my radiator, the sun comes in, it’s absorbed into the wall and the house heats up slowly.” O’Dowd says that using a concrete first floor and block-work for the internal walls also gave him flexibility when it came to internal design. He could move internal non-load bearing walls right up to the last minute. O’Dowd points out too that building with single leaf block-on-the-flat walls provides sufficient structural strength for a concrete first floor. “Normally if you’re building cavity wall construction and you want a concrete first floor you’d have to go with block on the flat for the inner leaf anyway. You’d also have a cavity and external leaf of blockwork, which this approach cuts out,” he says. The job relied very much on local knowledge and materials. While minimising energy in use was the u driving imperative of this project, embodied energy wasn’t ignored.
![]() |
O’Dowd took great care to minimise thermal bridging, working with Aerobord to create a circular insulation that snapped in place around two steel pillars at the front of the house; stainless steel rods and Aerogel were used to avoid thermal bridging in the bracket for the brise soleil |
Environmental design consultant Patrick Daly of Besrac was engaged at the planning stage, at which point O’Dowd’s aim was to get the house to an A3 standard. “The wall construction is very simple,” says Daly, “and because you’re not using a cavity, it enables you to use a lower embodied energy insulation. It allows the use of just white polystyrene, which in embodied energy terms is significantly lower than the high performance one.” Much of the concrete used was of lower embodied energy than traditional Cem1 or Cem2.
Elements of the design fly in the face of passive principles. It’s large – 4,000 square feet – and has an extremely diffuse footprint and a very high ratio of external wall to floor area. The building’s layout and orientation do however optimise solar gains. An open plan living space on the lower floor gets sunlight throughout the day, while extensive use of internal windows brings this southern light into parts of the house with a northern aspect.
When Daly came on board, the first thing he did was amend O’Dowd’s plan because of serious overheating issues. He reduced the glazing significantly and introduced extensive shading elements, including brise soleil and roof overhangs. A horticulturalist by profession and supplier of mature trees, O’Dowd used his expertise to provide much of the shading Daly specified. The house, which is oriented along a north-south axis, sits at the lowest part of the site. Strategic mounding and pinpoint planting will prevent both glare and over-heating at the height of the summer.
Once O’Dowd had settled on his plan and his building specification, he approached the concrete federation for support. Coincidentally, the ICF were on the lookout for a project which would showcase the use of concrete in sustainable construction. It was the ICF who raised the bar from A3 to zero carbon.
Patrick Daly explains how this changed the spec. “Once the heating demand was in the passive range, water heating becomes the significant energy load. It was really about reducing that through solar.” They then settled on a typical passive house spec: mechanical heat recovery ventilation with biomass heating backup. “We specified what would need to be generated to achieve the zero DEAP (Dwelling Energy Assessment Procedure software) carbon because it’s ignoring appliances. Given the size of the site, wind was really the optimum.”
The raft foundation was designed by O’Dowd himself, and manufactured by Aerobord, a company which provided extensive support, materials and consultancy throughout the project. It combines two types of polystyrene of varying compressive strengths, with a conventional raft foundation sitting above the insulation. The concrete supplied for both the raft and the structural screed in the first floor was a 30 Newton Cem2 from Cemex, with a 50% ground granulated blast-furnace slag (GGBS) content dramatically reducing CO2 emissions. Traditionally, says Liam Smyth of the ICF, u
architects and engineers tend to specify concrete with a 45 Newton strength, purely for safety reasons. “Using a 30 Newton mix,” he says, “is a bit of lean design.” Cemex also supplied the 100mm blocks used. These had a 15% pulverised fuel ash, or PFA content. A byproduct of coal burning from the ESB’s Moneypoint station, the inclusion of PFA reduces emissions in the production of the cement. The wide slab installed on the first floor came from Flood Flooring in Co Meath.
Irish Cement also supplied cement used for mortar in the project. ”In our bulk cement,” Richard Bradley of the company explains, “we replace approximately 12% of the clinker with limestone and in our bagged cement, there’s a substitution rate of 18%.” Clinker, he explains is the active ingredient in cement; replacing it with limestone improves the environmental profile of the product. Bradley argues that using a locally available, plentiful resource like limestone improves the sustainability of the cement industry.
Extensive research led O’Dowd to conclude that Aerobord provided the most cost-effective way of achieving the 0.1 W/m2/K whole-envelope U-value he sought.
He chose the Baumit external insulation system, provided by CPI in Dublin. “The concept of external insulation,” Alan Haugh of CPI explains, “is wrapping the outside of the building in insulated material and then finishing it and protecting it with a reinforced rendering and finished coat.” In Moate, the insulation material was Aerobord Platinum expanded polystyrene, bonded and mechanically fixed to the wall at the corners and windows. “The typical build-up on top of the insulation,” says Haugh, “is reinforced base coat. When that is cured and dried, there’s a primer put over it and then the final finished coat is typically a silicone resin-based render.” This finishing render – called Nanopore – is both breathable and self cleaning.
Though not strictly necessary, O’Dowd went round the house as the insulation system was being installed and filled any gaps in the insulation blocks with a PUR 7 foam supplied by Contech. “Our foam stops expanding once it meets resistance,” says Andrew D’Arcy of the Dublin-based company. “For example, the B1 foam only expands by 20% its own volume…It’s also unique in that it hasn’t got a limited life. You can use it to the last drop.”
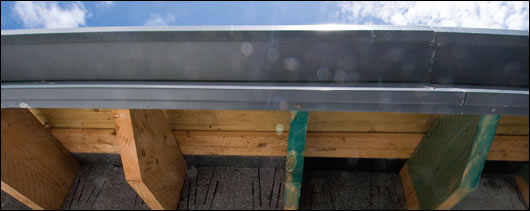
The external insulation continues into the eaves to ensure a completely wrapped envelope
One of O’Dowd’s first innovations was in the installation of the down pipes. “Micheál didn’t want to clutter the house,” Brian Cahill of Aerobord explains. “He wanted a clean façade, so he fitted the down pipes in the wall insulation. That’s quite an unusual step. It has been done before but you tend to have some air movement behind the pipe and it can lead to thermal looping and problems down the line because you’re interrupting your building envelope.” O’Dowd designed a carrier for the downpipe, and lined it with Aerogel – a light, high performance insulation which more than compensated for the insulation taken out to house the pipe. In all, O’Dowd designed and made up six different moulds which allowed insulation installers to cut the Aerobord to fit tight spots and areas where thermal bridging issues arose.
To deliver the required U-value in the roof, the first step, says O’Dowd, was to ensure that the carpentry was right in order that the Aerodorm insulation would fit perfectly. “The carpenter,” says O’Dowd, “was under strict instructions from me that he had to be exact, otherwise, I’d have had a lot of hardship fitting the insulation…Starting from the bottom, you have your slab, then your airtight membrane, then 60mm Aerobord, then 225mm of Aeordorm in the rafter, then 60mm Aerobord high strength, then breathable membrane taped down, then parallel battens, counter battens, then slates.” These slates are concrete ‘3 in 1’ tiles from Condron Concrete. “It’s a slim tile that uses less concrete than a conventional tile,” says O’Dowd. “It’s one big slate tile, which is cut to look like three.”
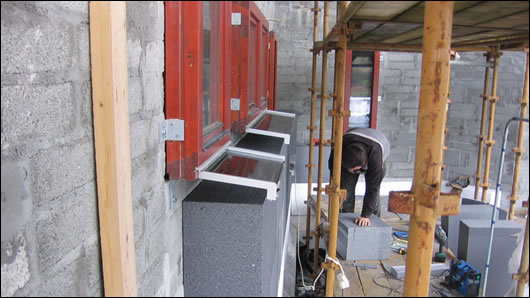
The triple glazed windows are bracketed onto the wall
Given the diffuse layout of the house and the extensive external walls, thermal bridging challenges kept arising. Brian Cahill of Aerobord worked closely with O’Dowd throughout the build to deal with each one as it arose. “Micheál was an absolute demon for sniffing out a thermal bridge and doing something with it,” says Cahill. “It was an absolute pleasure to work with him because he challenged us like never before. He made us go away and rethink some of the things we had taken for granted and come back with better detailing. Some of that innovation has stood to us in developing products in the UK and across Europe.” In response to cold bridging issues, Aerobord and O’Dowd worked together to create circular insulation that snapped into place around two steel pillars at the front of the house. Further cold bridging issues arose at the balcony which extends over much of the southern elevation. Working with TMC Fabrication in Moate, the design team came up with a solution that provided sufficient structural strength without compromising the thermal envelope.
The brackets required to hold the brise soleil were a similar headache. Using a combination of stainless steel rods – which have a much lower thermal conductivity than steel – and Aerogel, O’Dowd was able to design and manufacture a bracket which did not disrupt the thermal envelope and introduce cold spots into the structure.
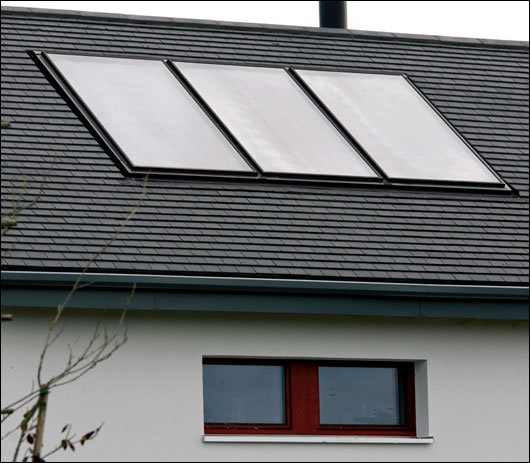
The house features flate plate solar panels supplied by Aerobord
The windows used were the triple glazed, super-insulating wood-window system Energate 1042, which carries certification from the Passive House Institute. These windows are stepped out from the blockwork using a cantilevered system, again in order to avoid thermal breaks.
Airtightness in the structure was achieved primarily through the wet plaster finish. A range of Siga products were also used at junctions and service penetrations. The Majpell membrane was installed at the underside of the roof, Jason Byrne of Siga explains. “This was taped and joined then using Sicrall. Then to connect the concrete to the actual membrane, we used a mastic – a tape flat directly onto concrete or sand and cement doesn’t give it as good a u bond.” Siga’s Rissan 100 was used around pipes and penetrations and the tape Corvum 12-48 was used to seal windows.
The initial air permeability test – carried out by Energy Matters in June – returned a result of 0.7 m3/m2/hr at 50 Pa, equivalent to 0.66 air changes per hour (ACH) at 50 Pa. Extensive thermal imaging was conducted after this test, weak spots were identified and remedial work carried out. Six weeks later, a second test reduced that figure to 0.44 m3/m2/hr at 50 Pa or 0.41 ACH. “This result meets and exceed the PHPP target design result of 0.6 ACH at 50 Pa,” says Ronan Rogers of Energy Matters. “Given the scale and complexity of this dwelling, this result is truly exceptional. I was aware of the challenges in achieving the target result and I was pleasantly surprised when the dwelling actually exceeded that target. It is a credit to the persistence and attention to detail Micheál O'Dowd inputted into this project.”
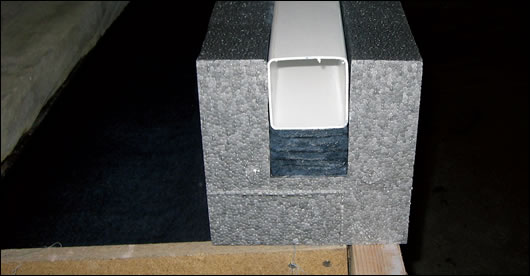
The unusual detail O’dowd came up with to run the rainwater system behind the insulation, using Aerogel to prevent cold bridging
Finding the right HRV solution was one of the biggest challenges O’Dowd faced. “Six different companies told me six different stories,” he says, “so I went off and did a heat recovery course and I eventually settled on ATC in Dublin and I installed the system myself.” There are two Vort Prometeo HR400 heat recovery units in the house, fitted with the rigid ductwork necessary for optimal performance. Sensors pick up increased CO2 levels and increased humidity and boost system operation automatically. O’Dowd installed the system before electricity or plumbing in order that the pipework would have the straightest runs possible. “It’s very important that you put the HRV in before the plumbing or anything else because air needs to have nice smooth flowing lines.”
O’Dowd ran DEAP calculations on six different solar thermal panels before settling on a three-panel, flat plate 2kW system from Schueco, represented in Ireland by Aerobord. The biomass stove is a Fondis, provided by Flame By Design in Cork. It has a catalytic converter and is fitted with an air box, from which heated air flows by convection through pipes to the main bedroom and the second floor living room. “Based on energy calculations,” says Liam Smyth of the ICF, “Micheál will need the stove during December and January, and for about one week in November and February.”
The 6kW Proven turbine provided by RES which sits atop a 15m tower on the site is the power behind the house’s zero carbon target. Paul Carbery of RES explains that because a 9m tower would not facilitate the generation of sufficient power, planning permission had to be sought to allow the design team to erect a 15m tower. “We anticipate getting between 11,000 kWh and 12,000 kWh per annum from that,” says Liam Smyth. “But we’re only putting 9,000 kWh into the BER so we’ll probably meet our zero energy target.”
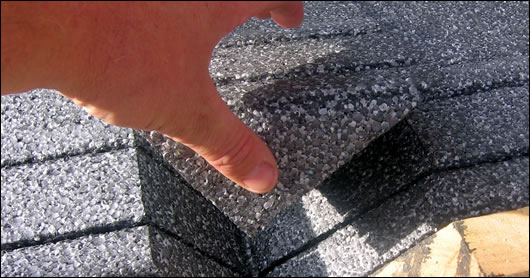
A timber mould made by O’Dowd to cut the insulation to exact dimensions
The project meanwhile is to be monitored for a two year period by the UCD Energy Research Group, which has installed a post-occupancy building energy performance and indoor air quality monitoring system on site. “Together with temperature and humidity,” Donal Lennon of UCD explains, “the monitoring system will also record electricity consumption required to run domestic appliances and systems and electricity exported from the wind turbine. Data gathered at the zero-carbon house is captured on an online data management system providing internet based live monitoring.”
The house also features a rainwater harvesting system from Shay Murtagh. “This is a 9000L concrete tank in the ground,” Raymond Smyth of the company explains. “The water comes off his roof, down his downpipes and into a pre-tank filter.” This removes the heavy debris and scum before it enters the tank. The water is then used for flushing toilets, for the washing machine and outside taps.
Energy Matters generated a provisional BER cert for the house in June, says Ronan Rogers. “The dwelling achieved an A1 with an annual energy consumption of 13.42 kWh/m2/yr and annual CO2 emissions of -0.38 kgCO2/m2/yr.” The turbine will now be monitored for a year and the results incorporated into the final BER cert.
Micheál O’Dowd estimates that final build cost will come in between 10% and 15% higher than a conventional build. “Everyone was telling me no, you’re going against the rules, this is not the passive way, it’s too big and too long and narrow. u That made me more motivated to do it, because if I can do it in this form, anybody can do it in a smaller form…It’s easy to build, it’s just not the norm. I’m not a builder and I built it.”
The house is open for tours through the Irish Concrete Federation. Contact Micheál O’Dowd at This email address is being protected from spambots. You need JavaScript enabled to view it. or visit www.irishconcrete.ie for more details.
![]() |
A section shows the comprehensively insulated roof, wall and foundations |
Selected project details
Client: Micheál O’Dowd
Airtighness tests and BER: Energy Matters
Energy consultants: Besrac /UCD Energy Research Group
Blocks (15% PFA) & concrete (50% GGBS): Cemex
Cem 2 cement: Irish Cement
Windows and doors: Energate
Insulation and solar array: Aerobord
External insulation system: CPI
Airtightness system: Siga
PUR foam: Contech
Wind turbine: RES
Heat recovery ventilation: ATC
Biomass stove: Flame by Design
Rainwater harvesting: Shay Murtagh