Part L changes
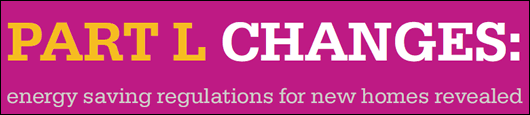
On 7 June 2011 environment minister Phil Hogan TD signed the latest changes to Part L of the building regulations into law, which will make it mandatory for all new homes to be 60% more energy efficient than the standards at the peak of the construction boom. Jeff Colley sheds some light on the key changes.
As Construct Ireland goes to press, the Department of the Environment are putting the finishing touches on the latest iteration of Technical Guidance Document L, which will instruct the industry in how to meet the increasingly strict energy efficiency and C02 emissions reduction requirements under the new Part L. But what will the new requirements look like? When Construct Ireland approached a source within the department to ask for detail on the new TGD we were told that, barring minor amendments, the final TGD L will be “substantially the same as that issued for public consultation” in August last year, so we can glean a lot from that document.
The new regulations are the second step in the transition to a zero carbon standard for all new homes, a target which the last government pledged to achieve by 2013. Changes to Part L introduced in 2008 brought in 40% energy reduction targets, while also making onsite renewable energy – a minimum of 10kWh/m2/a from thermal renewables or 4kWh/m2/a from electric renewables – mandatory for all new homes, along with a requirement for airtightness testing on individual houses, with sample testing accepted for multi-unit developments. This was significant progress, though the regulations were widely regarded as not going far enough when it came to telling the industry how to achieve the 40% reductions. Minimum requirements – which the department describes as “backstops” for airtightness and insulation levels were generally kept at mediocre 2002 levels, and to an extent it was left to the industry’s discretion to work out how to make the full 40% reduction.
So what requirements has the department made to achieve 60% energy and C02 reductions? Essentially the changes to the new TGD consist of significantly improved backstops for U-values, marginal increases in airtightness and boiler efficiency levels and more accurate treatment of thermal bridging. The backstop U-values are outlined in table 1 – and the version in the draft TGD provides useful comparison in that it includes the backstops from the 2008 version of TGD L, alongside the improved requirement.
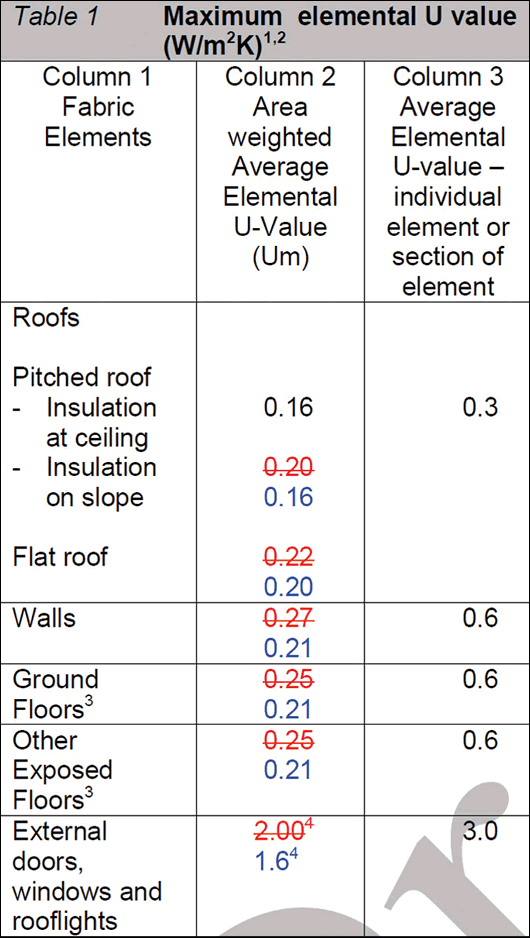
Tables 1 and 2 from the draft of TGD L 2011. Note the 2008 U-values in red in table 1 with the proposed amendments in blue in both tables
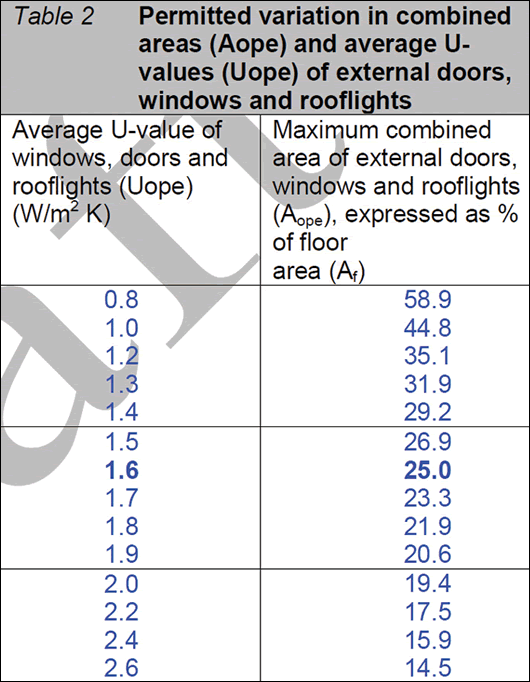
TGD L also stresses that the backstop U-value of 1.6 W/m2K for windows, doors and roof lights – which are aggregated together – is only applicable if their maximum opening area is 25% of a building’s floor area. If a building has a higher or lower percentage, the required U-value increases or decreases accordingly. The impact of this will be most keenly felt on heavily glazed buildings – where the combined area of windows, doors and roof lights is 58.9% or more, the backstop U-value reduces to 0.8 W/m2K, which invariably means the use of thermally broken triple-glazed windows and roof lights.
One point that the industry must understand, in order to avoid being in breach: it’s not possible to comply simply by hitting all of the required levels in terms of U-value, airtightness and heating system efficiency. While the building must meet or surpass all of the backstop targets, one of the key legal requirements is to achieve a 60% energy reduction compared to the BER score the same building would have achieved if designed to TGD L 2005. This essentially involves inputting the dimensions of the building you’re designing – along with the energy performance details of each element of the building – into Deap (the Dwelling Energy Assessment Procedure, SEAI’s software for generating BERs and determining compliance with Part L). Deap tells you the energy consumption and carbon emissions are of the house you’ve inputted relative to the reference house in the 2005 regulations. It tells you the energy consumption in terms of kWh/m2/a, and tells you what fraction that is compared to the same house built to 2005 regulations. This is called the energy performance coefficient (EPC). To comply with the 60% energy reduction in the new TGD L, your maximum permitted energy performance coefficient (MPEPC) must be a figure of 0.4 or less, compared to a reference house EPC of 1 – this is how the 60% reduction is expressed.
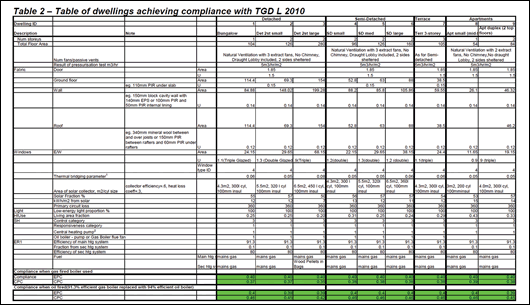
(Click for large view ) The nine house types which the Department of the Environment ran through Deap, to demonstrate a few of the vast number of approaches to compliance in each case. The proposed approaches are fairly conservative – the specifications are some way short of the standard Construct Ireland looks for when selecting new homes
“If you just hit the backstop values under the new regulations, you might expect to get an EPC of 0.8 or so, and you’d be non-compliant,” warns Gavin O’Sé of airtightness and energy consultancy firm Greenbuild. Tellingly, it’s only in the last few months that self-builders and developers are starting to enquire about provisional BERs as building control officers start clamping down on non-compliance with the 2008 Part L, based on Greenbuild’s experience. “In the last few weeks I have been getting my first ever requests for provisional BERs from self-build people in Wicklow,” he said. “I’ve had one house already where the people are completely loaned out, and to reach the 40% energy target and the renewables target they will have to do without a kitchen or something, simply because it wasn’t planned in. I’ve had a real hard time as the messenger of the news – u as if I was enforcing it – so the 2011 regulations will be even more of a shock for people,” he says. O’Sé says the clients had decided to insulate beyond the backstop levels in 2008 TGD L – for instance achieving a wall U-value of 0.23 – as well as installing a condensing boiler. “There was apoplexy as I tried to repeatedly explain the system to them – that just using the backstop values didn't mean they complied,” he says.
Curiously, though the department refers to a 60% carbon emissions reduction to match the energy target, Deap doesn’t multiply CO2 emissions by 0.4 – the maximum permitted carbon performance coefficient is 0.46. Construct Ireland understands that this is because the reduction is made relative to the 2005 reference house, which includes a gas boiler. As gas is a cleaner fuel than oil, this therefore creates the impression that the minimum compliant house in 2005 emitted less CO2 than in reality. Achieving a 60% CO2 reduction relative to the gas heated reference house would be significantly tougher to achieve with an oil boiler.
Electrical energy consumption will also have less of an impact on the BER score and Part L compliance, due to reductions in primary energy use and C02 emissions in electricity production and transmission. Up till now, every kilowatt of electricity used for lighting, heating or cooling in Deap has been multiplied by 2.7, to take into account the amount of energy used at the power station. The figure is set to be revised down to 2.53 or 2.54 – meaning a house that runs entirely on electricity would see a reduction of over 6% in terms of BER score. Equally the carbon intensity of electricity is set to drop from 0.643 to 0.561 kg CO2/kWh – a change which will make it considerably easier for more electricity-reliant buildings to achieve the MPCPC. These figures will be subject to future changes over time, and given the transmission to more efficient, low carbon power generation and transmission in Ireland, it seems that the green credentials of appliances which can use electricity efficiently – such as heat pumps or mechanical ventilation systems – will start to put fossil fuel boilers to shame.
In terms of reducing heat loss through infiltration, the new TGD would appear to be only a marginal improvement on the previous regulations – the air permeability requirement has increased from 10 to 7m3/hr/m2 at 50 pa. However, once again it’s worth bearing in mind that this is simply a backstop, and that it will invariably make sense to aim for substantially better performance, as airtightness will be amongst the most cost-effective ways to reduce energy consumption down by the required 60%. “If a house is built correctly, it will achieve 5m3/hr/m2 or better, just through attention to detail,” says Mark Shirley of airtightness testers and energy consultants 2eva.ie. “If you want to go down to very low air leakage rates, then you have to pay attention, using proprietary membranes and seals. If you're going to have a heat recovery ventilation system, it should be installed in buildings that are at worst 3m3/hr/m2,” he cautions.
TGD L 2008 introduced a mandatory requirement for airtightness testing, though builders were only required to test a sample of each house type on multi-unit developments, causing some concerns that standards would be lower with the houses that weren’t subjected to the rigours of a pressure test. The new TGD tightens up on this requirement. A source in the department told Construct Ireland that the revised TGD states: “If you’re claiming the default value, you can do the sampling test as per table 4. Where an air permeability value better than the backstop value of 7m3/hr/m2 at 50 Pa is claimed for use in Deap, a test should be performed on each dwelling claiming that value.” It may prove prohibitively expensive to attempt to comply with TGD L by relying on the backstop airtightness figure. If so, it means that airtightness testing has effectively become mandatory for all new homes.
This is exemplified by the nine example house types highlighted in the regulatory impact analysis produced by the Department of the Environment last August to coincide with the consultation on TGD L. In this exercise the department took nine examples representing the most commonly built house types – ranging from a 280m2 detached home to a 54m2 mid-floor apartment – and came up with some examples on how to make them comply with the new regulations. In each case they stipulated an air permeability of 5m3/hr/m2. While this is a reasonable improvement on the back stop level of 7m3, the example given by the department places much greater emphasis on insulation levels, proposing U-values that are well beyond the backstops. In each of the nine house types they have opted for a wall U-value of 0.14 W/m2K – going considerably further than the backstop U-value of 0.21, or the 2008 backstop of 0.27.
It’s important to emphasize that the department has only given one example here of how to comply with the regulations, and that setting U-value and airtightness levels better than the backstops were just some of the many aspects chosen to achieve compliance. The department makes its position clear in the regulatory impact assessment document:
While the proposed Part L requirements substantially improve the energy performance requirements for a new dwelling, designers, developers, builders and consumers have been left considerable discretion in choosing their own individual approach to achieving the overall standard required for compliance. In this way, no individual technology or system should or will be either favoured or disadvantaged. This will incentivise suppliers of building elements and components which have a significant impact on energy performance to innovative and adapt their existing products or develop new ones as the amended Part L /TGD L requirements should fully recognise the contribution of such products to reducing energy demand and CO2 emissions.
The specifications for the nine house types do however betray a degree of conservatism in the department’s thinking. Essentially, the example specification they outline is a partial fill cavity wall structure with added internal drylining, with basic natural ventilation and an oil or gas boiler. It could be argued that this is a wise or pragmatic move on the department’s part – they’ve chosen an example that the less progressive elements of the construction industry are unlikely to balk at. Construct Ireland readers may however be unsurprised that prominent eco architect Joseph Little takes issue with the example wall, which consists of a 150mm cavity with 100mm PIR or 140mm EPS partial fill insulation, along with 50mm internal dry lining.
"Internal wall insulation can hide a multitude of sins,” says Little. “My concern is what happens when you allow a builder to build badly – particularly with insulated plasterboard on dabs. To what degree is the masonry behind the plasterboard on dabs chased for services, to what degree are the mortar beds filled, and how is the potential air leakage into the resulting void minimised from outside or even from other parts of the building, for instance the intermediate floor area or roof above? In too many cases you find the resulting air leakage from there being distributed under skirting the whole way around the room and beyond. Effectively you end up disguising the problem in one area, and end up with a harder to solve problem everywhere else.
Little points out that he’s not dismissing cavity wall construction outright, and suggests an approach that could be more conducive to reducing heat loss: “If you want to build cavity walls, you'd be better off widening and full-filling the cavity, perhaps with autoclaved aerated concrete blocks on the inside face and a wet plaster finish – it gives a much more predictable result. It also adds to the certifiability of the construction method, as the architect can inspect the cavity, just prior to fitting of top cavity closer, to make sure it's clear of any rubble or mortar for its entire height and length. Only then should the insulation be blown in,” he says.
TGD L also sets requirements for existing buildings undergoing renovation and extension work, including modest U-value requirements. Joseph Little raises concerns about a diagram in this section of the TGDs. Through the use of arrows, diagram 2 – which has been used unchanged in five editions of TGD L since 1997 – suggests significant heat loss at the window junctions of an uninsulated wall, but not through the plane elements of those walls. “In fact the additional heat loss – in other words thermal bridging – at these points would be relatively little, because the U-value itself is so poor,” he says. “The absence of the arrows in the other diagrams showing insulated alternatives suggests that heat loss is controlled there, despite the additional heat loss in all junctions shown becoming worse. In the case of the internal insulation shown the coldest spot could actually become colder after the insulation is applied and surface condensation and mould risk at that point could become greater than ever. This was poor guidance in 1997. Given the heightened standards required in TGD L 2010 it's crazy.”
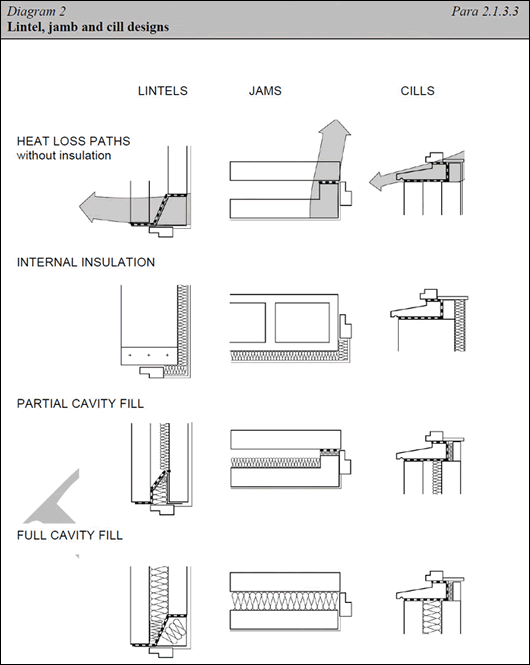
Joseph Little claims TGD L ‘s diagram 2 is misleading and should be removed
Little also emphasises the importance of “Limiting Thermal Bridging and Air Infiltration – Acceptable Construction Details”, a supplementary document on typical construction details issued by the department on reducing thermal bridging – the values of which are included in tables D1-D5 in the new TGD.
"The ACDs last time around were considered to be best practice,” he says. “In this version, they're the bare minimum required to meet compliance – and in some cases they would fall short of compliance. We need to be building to at least the ACD level of care and thermal conductivity for conventional construction. Given the fact that the ACDs are now the minimum standard for new build and that we have the Ψ-value for each, we should be abandoning a default Y-value of 0.08. We can now use the values given in tables D1-D5, and manufacturer's values and values from thermal bridge assessors to easily calculate a Y-value.” This, Little argues, will allow much more accurate and often better BER results. “It’ll mean that if you deal well with heat loss at junctions, it’ll be easier and cheaper to make the whole building comply, in many cases without having to add additional insulation.
"However it's clear the ACDs need to be expanded for a wider range of forms, construction types and also to accommodate a higher standard of details. Currently if you only want to calculate a Y-value of 0.08 (as opposed to using the default value) you may have to abandon the ACD details, for certain dwelling geometries and construction types. If you want to go further, as the department felt obliged to do to prove compliance [in the regulatory impact assessment document], you may not be able to use the ACDs all. Most of the nine house types they show have a Y-value of 0.05. Without guidance how is the designer or builder meant to reach that value? The sooner the ACDs are revised and the sooner certification for thermal bridging assessors is introduced, the better.”
Little also points out that the reference dwelling in TGD L may make compliance tougher for smaller, more compact buildings. “The notional 'reference dwelling' used to prove compliance in TGD L 2010 is a serious problem,” he says. “Mid-mid apartments are going to be virtually unbuildable. Its characteristics are skewed. That wasn't a problem when we had poorer insulation standards, but as we tighten up on insulation levels it'll make certain more compact dwelling types much more difficult to build. Ironically, a 'Southfork' type mansion will be easier to make comply than a small apartment.”
According to Little, the new TGD has made some limited progress on assessment of interstitial condensation. "TGD L 2010 at last mentions IS EN 15026 – the European standard for interstitial condensation assessments using numerical simulation. However in the TGD it's clearly listed as a secondary or alternative tool to interstitial condensation assessment under IS EN 13788. The problem is that methods that meet the latter standard are long-established but over-widely used. The scope of IS EN ISO 13788 makes it clear that this standard shouldn't be used where masonry or hygroscopic building materials are present, and where construction moisture or short term events like driving rain or freeze-thaw cycles are relevant.” He points out that 13788 does still makes sense as a basic assessment method for timber frame.
"If we're trying to build to higher levels of airtightness and insulation, the risks grow,” he says. “Traditional buildings had many gaps and cracks so air could move everywhere. Equally air temperatures were generally lower due to lack of insulation and uneven heating though much of the heating that was used was radiant. Unless an actual water leak was at fault, whenever condensation occurred constant air movement would generally ensure it dried-out. As we move to higher standards air leakage becomes an enemy to energy-efficiency but it also deprives us of a 'safety net'. We need to ensure that our buildings are designed to take account of the reduced tolerance by using the right standards and proper assessment tools. This affects all guidance for the industry, all products to be used in the thermal envelope and every building we're constructing or retrofitting. Quite simply, the emphasis needs to be placed on IS EN 15026 as the principal method for assessing every building, and the only method for assessing masonry buildings.”
Construct Ireland understands that SEAI are currently producing a 2011 version of Deap – due out over the next few months - to support TGD L 2011, and plan to release the new software before the regulation kicks in on 1 December to allow designers to get to grips with it.