- Retrofit
- Posted
From the ashes...
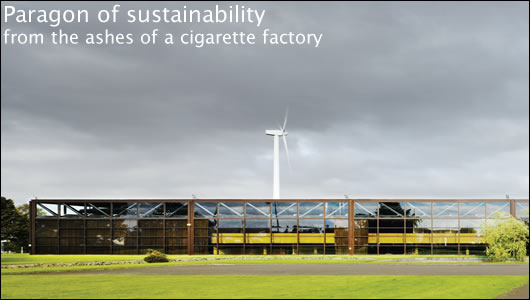
Energy conservation and CO2 emissions were not design concerns when Scott Tallon Walker’s Carroll’s cigarette factory in Dundalk was created over 40 years ago. The modernist landmark has been reborn for Dundalk IT as an avant garde exemplar of wind energy storage and an ingenious approach to integrated heating, ventilation and cooling, as sustainable design expert Chris Croly of BDP explains.
The strive towards the zero carbon design of new buildings is making progress but even if legislation immediately required all new buildings to achieve a zero carbon rating, the overall effect of Ireland’s buildings on the environment would be limited – due to the significant stock of existing buildings.
The good news is that older buildings do eventually need to be refurbished and we are then presented with an opportunity to address their energy performance. For non-domestic buildings, this opportunity forces itself on building owners every 25 to 30 years as heating and electrical systems of this age can become problematic and start to fail due to their intensive use. There are currently a huge number of buildings in Ireland that are approaching or have reached this key refurbishment opportunity.
As with all environmental topics, the refurbishment of an old building generates debate on which approach will have the least environmental impact. Should it be demolished to allow a new low energy solution to be created? Should as much of the existing building as possible be retained to take advantage of the energy embodied within the building’s materials and avoid unnecessary waste – at the risk of compromising the building’s energy performance?
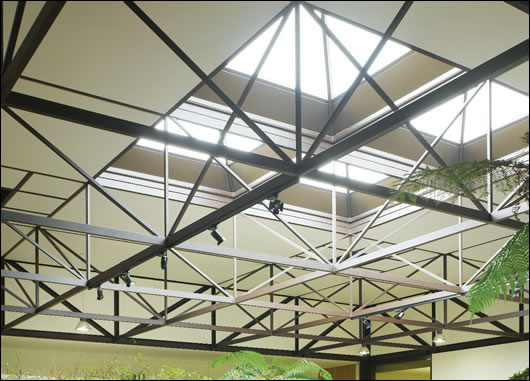
The atria provide open space and allow natural light into the building
How far can the energy performance of our existing building stock be improved? To explore this question we will select one of the most challenging refurbishment projects we can find and review its transformation.
Constraints
The PJ Carroll & Co factory in Dundalk was obtained by Dundalk Institute of Technology (DKIT) for conversion to a third level educational facility. DKIT embarked on a major refurbishment of the Carroll’s building to provide teaching spaces for computer science and performing arts courses, covering an area of 11,000m2.
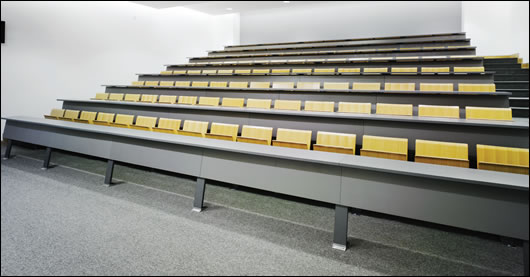
In the larger lecture theatres air is supplied through grilles in the floor, using a system that detects occupancy in the room and monitors air levels
The factory was a very large industrial building, designed in 1967 as a cigarette factory. While the building’s energy performance was not a top priority in 1967, its design was of exceptional architectural merit. The building became known as one of the finest examples of Miesian architecture in Europe and was therefore listed, preventing the modification of its appearance or design principles during its refurbishment. This listing prevented the modification of the façade, including the areas of high level single glazing.
The refurbishment of the building was also constrained by its deep plan, which would inevitably generate a large number of internal rooms that required potentially energy-hungry air conditioning systems to be used. As a further constraint, the project budget was limited and it was necessary to maximise the amount of teaching accommodation produced for the funds available.
The final significant constraint is the building’s span – the massive 20m distance between steel supporting columns – which was designed in order to provide the largest possible unobstructed area of factory floor. This span however leads to significant building movement between columns meaning that any changes to the building must be able to accommodate this building movement.

In rooms with a lower requirement for fresh air, fan coils are used for heating and cooling the air
If it can be shown that these many constraints did not prevent the achievement of a low energy refurbishment then there is surely hope for the sustainable refurbishment of any building.
Adapting the building
The original factory design was carefully planned to offer ease of access to all of the plant that supported the factory’s operations. The building was clearly divided into two levels, with the ground level housing the factory equipment and an upper, half height floor containing the air ducts, pipework, and electrical distribution systems. A network of steel walkways snaked around the upper level providing a hidden access route to all the building’s air ducts, pipework, and electrical cabling. In places it’s necessary to crouch under ductwork or squeeze through the structural frame while exploring this labyrinth that sits above the ground floor ceiling.
The upper level is lined with a large strip of single glazing which was intended to celebrate the building’s engineering services systems by providing a clear indication of them from outside the building. As the principle of a support level was a key part of the building’s architecture, it was not appropriate to add insulation behind the glass or to replace it with double glazing. It was, however, vital to address the significant leakage of heat through this glass. The challenge was resolved in an innovative way by defining an insulation and airtight layer at ceiling level instead of roof level when redressing the buildings uninsulated structures. This was a courageous approach by the design team because the generation of an airtight layer at ceiling level is particularly complex to achieve. There are a significant number of services that must pass through the ceiling layer and must each be air sealed, but this process is further complicated by the movement that occurs at ceiling level due to the large building span.
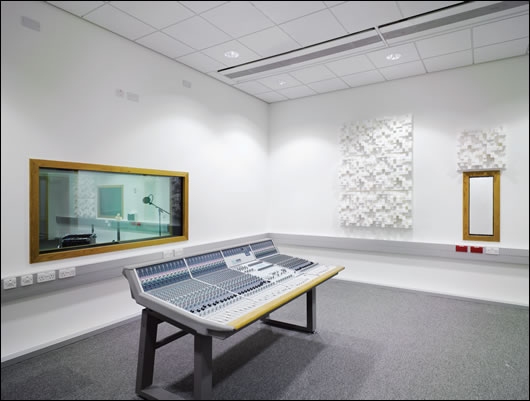
In rooms with noise constraints, such as the sound recording rooms, large finned pipes are mounted in the ceiling which can heat and cool the air quietly,
using low amounts of energy
This insulation layer offered significant protection against heat loss and was combined with the addition of insulation to the walls and the replacement of the lower glazing with double-glazed units. The U-value of the replacement glazing was limited by the existing frame width as it was not appropriate or cost-effective to replace the window framing.
Refurbished buildings are rarely air tested due to perceived complexities of making an existing building airtight and the unknown level of leakage of the existing structure. It is often thought that the contractors will shy away from a specific airtightness target in an existing building, but in this case a two-part airtightness target was set to overcome this difficulty. The contractor was required to achieve an airtightness of 10m3/m2/hr at a test pressure of 50 Pa, or to achieve a 75% improvement in the first test result if there was a significant failure. It is to the credit of the contractor, Sisk that they fully embraced the target and exceeded the target with a result of 8.4m3/m2/hr. While this target would not be impressive for a new building, it is a remarkable achievement for such an old and complex building and was one of the most important elements of reducing the building’s energy consumption. This project will hopefully generate acceptance that it is both reasonable and cost-effective to improve the air leakage levels of existing buildings.
While it was inevitable that mechanical assistance would be required to ventilate and cool internal rooms, there were several large spaces in the building where natural light and ventilation could be achieved. A large number of new roof lights were introduced and a completely naturally ventilated winter garden and canteen space were created, bringing natural life into the core of the building.
The systems
While mechanical systems were required, the key to minimizing their energy use was to ensure that the systems installed could automatically detect how the building was being used and quickly respond. Three different systems were used. In the larger lecture theatres air was supplied through grilles in the floor by a system that is only turned on when it detects that people are in the room and adjusts the amount of air supplied by measuring the levels of carbon dioxide in the air. Carbon dioxide sensors provide a very good indication of the number of people in the room and allow the fresh air volumes to be tuned precisely to maintain the required air quality. Reducing air volumes to the minimum required is vital to reducing fan energy as even a 20% reduction in air flow results in a 50% reduction in fan energy use.
In rooms with a lower requirement for fresh air, fan coil units are used which can heat and cool the air locally by recirculating room air over coils that are fed with hot and chilled water. The fans in these units are provided with ECDC motors (electronically commutated direct current) which operate much more efficiently than traditional fans at part loads. Both the fan coil and fresh air supply fans constantly measure the room air quality and adapt to the number of people in the room and its temperature so that energy isn’t wasted when the room is only partially occupied.
A third type of system is used in rooms where there are noise constraints such as the sound recording rooms. These rooms use chilled beams which are large finned pipes that are mounted in the ceiling and can heat and cool the air with a low level of noise and a very low energy use as they don’t require a large amount of fan energy.
All ventilation systems are provided with thermal wheel based heat recovery systems which are over 80% efficient.
Wind storage
Anyone who has driven close to Dundalk will have seen the 850kW wind turbine that provides approximately half of the institute’s electrical energy requirements from a renewable energy source. This turbine, which was the first urban-based wind turbine in the country, is a highly cost-effective form of renewable energy (paying for itself in approximately seven years) in addition to offering a useful teaching aid for the institute. The turbine is openly accepted as a local landmark and it is a wonder why more institutes have not followed suit where appropriate sites exist.
While a large amount of the energy from the turbine was used directly in the campus, an amount was also exported to the grid during times when there were high wind levels and low on-site demand. The exporting of electricity from the turbine achieves a payment that is considerably below the market rate for electricity and it is therefore preferable to minimize the amount of electricity exported.
Even if all of the electricity generated by the turbine were to be used on site, the turbine still affects the national grid as the amount of make-up electricity drawn from it fluctuates as the wind speed changes.
It was important that the refurbishment of this building addressed the existence of the wind turbine and demonstrated how a building can smooth the electrical generation from it – an approach that is not just of interest in the context of this campus but in terms of its national implications.
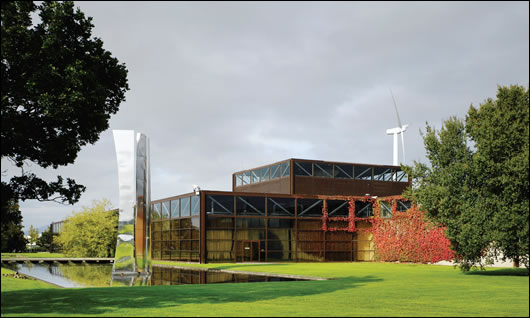
A large ice bank is situated in the basement as a means of using water to store energy, both from the wind turbine and to avail of cheaper night tariffs from the grid
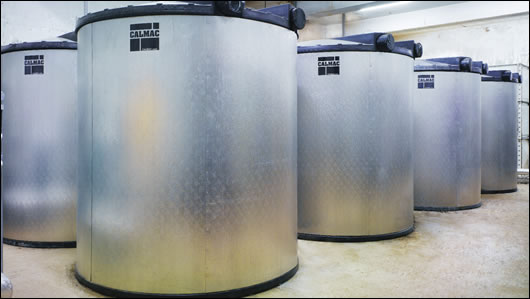
As Ireland increases the amount of wind energy connected to the grid, there will be increasing difficulties matching supply and demand. The control of Ireland’s demand for electricity is almost as important as the need to decarbonise electrical generation as green electrical generation cannot occur in the scale planned without a recognition that we need to match availability and usage. One method of adjusting demand that is currently being promoted is the use of electric cars to store energy when it is available. Buildings also have a role to play in the regulation of electrical energy demand. When smart metering is finally rolled out, offering electricity at different charge rates depending on availability, it is inevitable that large buildings will offer a response. BDP were keen to use this building to provide a demonstration of two methods by which buildings could respond to smart metering; firstly by adapting their electrical demand to the availability of the grid but also by offering a cost-effective method of energy storage that is more environmentally sensitive and has a lower cost than the use of batteries.
A large ice bank is provided in the basement as a means of using water to store energy. The ice bank consists of water tanks that have coiled pipework arranged within them. A chilled antifreeze solution is passed through the coils and a layer of ice builds on the coils during the charge cycle. The charge cycle is activated whenever there is excess wind available from the wind turbine, but it is also activated during the night when it is known that the national grid has excess capacity and electricity is available at less than half its normal price even with the current tariff system. Ultimately, when a smart metering tariff is available, the ice bank would charge whenever the meter informs the controls system that the grid has excess energy available. During the day, when there is a demand for building cooling, the antifreeze circulates through the ice and recovers the cooling from it. It takes as much energy to change water to ice as it would to heat it from 0C to 80C. This is known as the latent energy of fusion and is the reason that storing energy in ice requires a relatively small space requirement. Water is also a free, low maintenance and environmentally sensitive means of storing energy.
The second method that the building employs to adapt its electrical demand is to store energy within the fabric of the building by allowing a very small change in room temperatures to occur when required. When there is a low availability of electricity, the building not only ensures that its chiller is turned off (relying on the ice bank entirely for cooling) but also decreases the cooling set points of all rooms in the building. This has the effect of reducing fan and pump energy in the building temporarily. As it is not currently possible to obtain a smart meter for the building, the building goes into electrical reserve mode by sensing when the building’s electrical usage approaches a maximum set point and smoothing out the building’s demand on this basis. As the college is charged for exceeding a peak electrical figure, this control routine can be used to protect against this scenario.
Heating
SEAI had intended organising the installation of a 4MW biomass based district heating system, using the old plant room of the Carroll’s building to serve several buildings in the area, including the Carroll’s building. It was envisaged that SEAI would arrange for this system to start generating heat in the spring of 2009, and the refurbishment of the building therefore contained a gas-fired heating system that was intended as a temporary installation until the district heating scheme was complete. The completion date for the biomass scheme is not currently known but it is hoped that it will eventually serve the Carroll’s building which would offer a large proportion of the total load to the system.
Results
In order to demonstrate the effect of the refurbishment, an energy certificate was produced before and after the modifications. Before any modifications were made the factory achieved an energy cert of G and after all refurbishments were undertaken the revised energy certificate was a B1 – which is comparable with a good new building and demonstrates a dramatic improvement. This achievement in a complex listed building suggests that it may be appropriate to reconsider existing legislation on the refurbishment of buildings.
The building refurbishment was completed in the summer of 2010 and its controls system is connected through the internet to BDP’s offices in order to allow the building’s performance to be monitored and tuned. Energy performance results will be available at the end of the teaching year.
The monitoring of the ice bank has shown that it is capable of ensuring that the chiller never turns on during periods of high energy demand. While initial testing shows that the building energy does offer the ability to reduce the buildings electrical demand by 25% under some scenarios, further testing is required to fully determine the effectiveness of this new concept.
This project clearly demonstrates that there is a potential for buildings to play a significant role in adapting Ireland’s electrical demand to be more suitable for the integration of wind energy. It also demonstrates the need for smart energy tariffs to be made available to large buildings as soon as possible, in order that buildings can play their part and start adapting to a new era of energy supply systems that is not always available at maximum output. The payback period on the building’s ice bank is eight years, even with current night rate tariff schemes, and there is therefore a significant potential for ice bank storage to be used in buildings throughout Ireland that have large cooling loads. These systems would not require any grant funding to be viable; all that is needed is a realistic smart metering tariff.
Selected project details
Architects: Scott Tallon Walker (Wayne Rothwell)
Sustainability advisor/M&E engineers: BDP (Chris Croly and Edel Donnelly)
Civil & structural engineers: ARUP
QS: Healy Kelly Turner Townsend (Derek Niven)
Main contractor: John Sisk and Son Ltd
Electrical contractor: Update Technology
Mechanical contractor: T Bourke & Co
Overview
Location: Dundalk Co. Louth
Building: 11,000m2 ex-cigarette factory originally constructed in 1967, converted for educational use. Single storey with services zone above, steel frame construction
BER: improved from G to B1
Airtightness: improved from non-existent to 8.4m3/m2/hr in spite of restrictions posed by listed façade and significant building movement caused by steel structure
Insulation: walls were improved from 1.6 to 0.27 W/m2K, the roof improved from 2.8 to 0.22 W/m2K and windows improved from 6.3 to 2.2 W/m2K. While the existing floor could not be insulated, the significant plan depth of the building provides a naturally well insulated floor
Heating: gas boilers, with the intention of the future connection to a biomass district heating system, housed within the Carroll’s building
Ventilation: demand-based variable speed air handling units with thermal wheel heat recovery systems
Cooling: chilled beams, ECDC fan coils, and displacement ventilation, fed from an ice storage system which links to an on-site wind turbine
Green materials: the complete re-use of the majority of the 1967 building structure, façade and floor structure
Important features: airtightness improvement of an existing building, the innovative selection of an unusual insulation and airtight layer location, the use of significant load sensing controls to limit plant loads, the use of an ice bank renewable energy storage linked to an on-site wind turbine, and a grid smoothing system. The use of building controls to regulate and smooth building electrical energy demand, providing an example of one possible response to smart metering