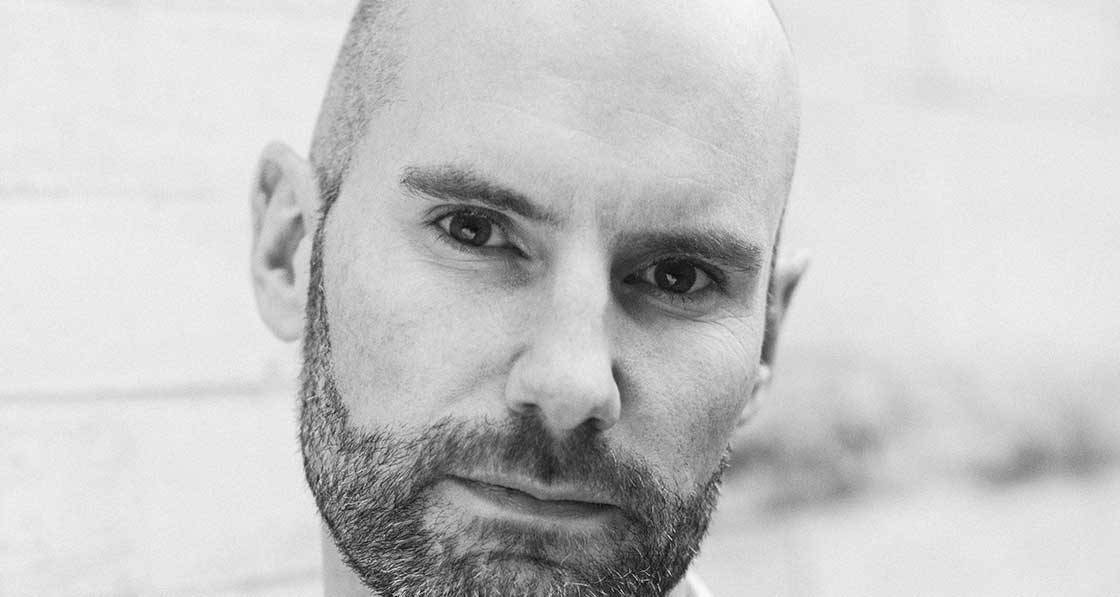
- Blogs
- Posted
How will today’s buildings perform tomorrow?
Richard Tibenham of Greenlite Energy Assessors says a case of two highly energy-inefficient and ‘hard-to-treat’ buildings, built in 2013, should serve as a warning to the whole construction sector.
This article was originally published in issue 31 of Passive House Plus magazine. Want immediate access to all back issues and exclusive extra content? Click here to subscribe for as little as €10, or click here to receive the next issue free of charge
During his time in office, David Cameron promised a bonfire of the regulations in the building industry. His government even operated a ‘one-in, two-out’ rule, specifying that for every new regulation imposed, two existing regulations had to be removed. Since then, the regulation of energy efficiency in the built environment has roughly plateaued, with the free market and planning authorities taking the lead on energy efficiency and carbon emissions.
Consequently, this has given rise to a new phenomenon: that of the new building, often fitted with solar panels and on-site renewable energy generation, which paradoxically eschews energy efficiency in a way that seriously hinders the transition towards a low or zero carbon economy.
The consequences of greenwash are letting themselves be known.
The term ‘hard-to-treat’ is usually applied to older buildings with solid masonry walls. These require internal or external insulation to improve their thermal efficiency, a disruptive and costly process. But now hard-to-treat characteristics are creeping their way into new and superficially ‘green’ buildings.
Recently, I was consulted on the measures necessary to achieve zero carbon operation for two modern buildings, built in 2013 under the building regulations Part L2A 2010. They were equipped with photovoltaic (PV) arrays, as well as reasonably efficient air source heat pump systems. Lighting, including external floodlights, contributed the lion’s share of the site’s energy demand, but internally, space heating was by far the highest demand.
Lighting was pretty much the only low hanging fruit that could be addressed. Low wattage LED alternatives offered a low-cost fix, though poor consideration of daylight availability meant that some areas incurred lighting loads year-round, irrespective of lighting efficiency. The client wasn’t quite ready to go knocking large holes in the walls and roof, so taking things further required a bit more head scratching.
Despite the heat pumps, wintertime heating energy demand remained high. The buildings’ lightweight steel frames were insulated to minimum standards and incurred high levels of air leakage. The bolt-on ‘fixes’ of PV and heat pumps where applied as a substitute for form and fabric efficiency. This resulted in two new buildings which just about satisfied the building regulations, yet proved hard to treat so far as further improvements were concerned.
In energy efficiency, as in health, prevention is better than cure: maximising efficiency and preventing high energy demand is far better than masking inefficiencies with the short lived cure of renewable energy generation.
Concerningly, buildings like this are the norm in the UK. Under the current building regulations, commercial buildings especially all too often adopt a ‘fabric last’ approach — an inversion of the conventional wisdom of fabric first. The falling cost of PV cells has made them a cheap alternative route to compliance, avoiding the riskier business of good airtightness. To boot, a bit of PV on the roof also ticks the boxes for local authority planning policy requirements for renewable energy generation, allowing local councils to make bogus claims about delivering supposedly ‘sustainable growth’.
A fabric first approach, integrating form and fabric considerations, offers reduced operational demands during the periods of the year when it most matters, i.e. during the winter, when grid energy demand and carbon intensity are at their highest. The best that can be done for these two buildings is ‘theoretical’ carbon neutrality via a large PV array, providing excess to required energy generation during the summer, yet still incurring high energy demand during the winter. There is only so much summertime demand that can accommodate this dynamic, making it an unsuitable approach for broader city and regional zero carbon aims, unless vast capacities of expensive energy storage is included.
If prior considerations had been given to these buildings’ orientation, form and fabric, then heating and lighting loads could have been minimised, cooling loads eradicated, and roof pitches and orientations optimised for solar energy generation. In the event, zero carbon operation will likely remain a pipe dream for these buildings and others like them.
The UK is sitting on a growing infrastructure time bomb, in the form of an unnecessarily inefficient built environment. The industry is crying out for better leadership as consecutive governments’ aversion to better regulation leads to avoidable defects in the UK’s building stock. A report by the Business, Energy and Industrial Strategy Committee (BEIS) states that energy efficiency is the cheapest way to reduce carbon emissions, suggesting that time is hopefully being called on this wasteful endeavor. If we are to avoid carpeting the country in solar and wind farms, then a fabric first approach is needed to ensure that the buildings of today are future proofed for the needs of tomorrow.