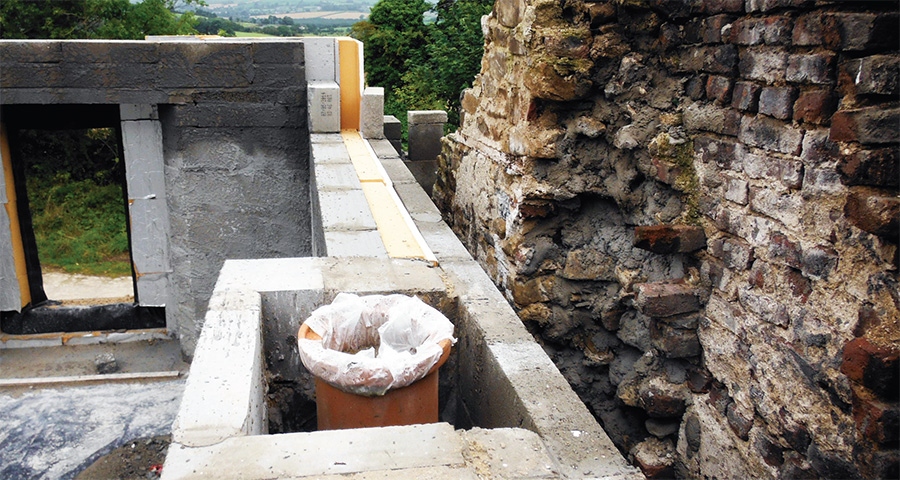
- Insight
- Posted
Will building boom see low energy failures?
Low energy building isn’t complicated, but it’s easy to get wrong. Since Irish house builders downed tools en masse when the last boom ended, energy efficiency standards for new homes have seen unprecedented rises of 40% in 2008 and 60% in 2011, shooting far ahead of the UK. But with signs of a new boom emerging, can the industry get to grips with this brave new world of insulation, airtightness and thermal bridging and deliver healthy low-energy homes — or are damp and mould set to become the norm in new build?
Simon Jones of ventilation technology company Aereco took a call recently from an architect looking for advice. The architect was working on a residential development that had just been completed, but there was a problem.
Jones drove out and met the architect, the engineer and developer at the site. “We took a walk around the houses and in dead space areas on the development, areas where you wouldn’t get free flowing air, we found mould and condensation. And this is before anyone had even moved in. Behind wardrobes and in corners near skirting boards; mould and condensation.”
Jones isn’t the only building professional to have run into mould in new houses in the last few months. Gavin Ó Sé of Greenbuild in Co Wexford was also called in to advise on an almost identical issue. “The contractor had installed good insulation and achieved good airtightness results, but in one or two of them, he had been called back for condensation build up,” Ó Sé says.
Simon Jones, commercial director UK & Ireland of ventilation technology company Aereco
And Archie O’Donnell of Integrated Energy and Coda Architects has also had recent experience of condensation and mould in new builds. In fact, all of the professionals interviewed for this piece had a ready stock of stories of how poor ventilation strategies in particular, and questionable building practice in general, continue to dog Irish construction.
These issues, Simon Jones points out, are not new. He’s been discovering condensation and mould in new buildings for at least the last five years. His concerns – and those of many others in the industry – centre on the tentative resurgence in building activity and what it implies for the quality of construction.
Jones points out that during the recession, most house building in Ireland fell into one of two categories. “One is council driven,” he says. “New builds for the likes of Ballymun regeneration or Limerick regeneration, where specs are being led by councils who have demanded certain performance levels. Or else you have the passive house, one-off builder who has been building ever better homes over the last half decade.” Both categories of builder have an obvious vested interest not alone in delivering a cost-effective project, but also in ensuring that the structures they build provide a safe, low cost, high comfort living space for decades to come.
But now things are changing. The Ulster Bank Construction Purchasing Managers Index, a measure of activity and sentiment in the sector, recorded an increase in construction activity for each of the last 13 months. Meanwhile, September’s housing market report from the Society of Chartered Surveyors said that 35,000 new houses will be needed to meet rising demand in Dublin over the next four years.
The risk that Jones and others have identified is that developer-led construction brings a whole new set of priorities to the equation. “Quantity surveyors get involved and begin looking for ever cheaper products. They start looking to cut corners, they start asking questions: What can we get away with? Do we really need that? The danger is that there will be a race to the bottom with specification, a race to the bottom with skills, with labour...This is a high risk time,” he says.
None of this is to imply that a return to growth isn’t welcome, and Jones, while pointing to the risks, is also quick to point out that the industry stands to benefit from the commercial rigour that professional developers will bring. One of the central challenges facing the industry as it begins to pick itself up again centres on skills. The 93,000 houses that went up at the peak of the cycle in 2006 were subject either to the 1997, 2002 or 2005 versions of Part L. Many of the builders responsible for those houses were abruptly sidelined by the property collapse. Now, as they return to building sites, they’re being asked to build to a much more demanding standard.
“A lot of builders struggled through the last five or six years,” says energy consultant Mark Shirley of 2eva in Carlow. “They got by doing extensions or small refurbishments. Now they’re looking at coming back, and the landscape has changed completely in all sorts of ways.”
Energy consultant Mark Shirley of 2eva
The revised building regulations 2011 have effectively upgraded the minimum standard from a B3 rated property in 2005 to an A3 today. Backstop U-values have been radically overhauled, thermal bridging has been addressed. While the airtightness requirements remain weak, they are still far more strenuous than ten years ago. Builders must now deliver a 60% overall improvement in the energy performance of new dwellings compared with 2005. The question is, can they do it?
Martin Flattery runs Mulberry Properties, a development company which just finished an estate of A2-rated houses in Straffan, Co Kildare. He says his decision to aim higher than the building regs was predicated on commercial reality: build better and your investment will pay off. “Customers are a lot more educated than they used to be. There are a lot of A-rated houses out there, A3 is becoming the norm, so we decided to push beyond that,” he says
for this piece share. Developer Joe McGowan, who is currently building 154 passive houses in Abergele in Wales, says that he can charge more for houses which are cheaper to run. This isn’t just wishful thinking. A 2012 Oxford University research paper1 found that A-rated properties commanded an 11% price premium over D-rated houses, while a 2013 Department of Energy & Climate Change report2 found that A or B-rated homes sold for 14% more than G-rated homes. “Delivering that standard does not require a huge amount of money,” says McGowan, who adds that he has faith in the industry to rise to the challenge and deliver these higher specs.
Others aren’t so sure. Martin Flattery says that the current building environment is fraught with risks. His concerns centre on the lack of any real scientific rigour in many of the building methods that are being deployed to reach these higher standards. “Builders are adding a bit here and there, making up their own thing and ticking boxes to comply with regs,” he says.
He points out that cavity block construction with partial or full-fill cavity insulation has long been the staple of the industry. But because filling a standard width cavity with insulation alone will no longer deliver the 2011 backstop U-values, builders, instead of exploring new methods, are typically adding a warm liner to the inner leaf. Flattery points out that this piecemeal approach to achieving the new standards is far from optimal.
“A lot of the builders are sticking to what they know,” says Flattery, “and then they’ll simply supplement it to comply with regs and get an A-rated house. But you ask them where the dew point is and they haven’t a clue.” He laments the fact that there is no neutral agency to provide unbiased information on the best ways to achieve the standards required.
Condensation build-up on a window in a home built during Ireland’s construction boom – the clear spot is due to a leaking air seal in the window
“An insulation company will come in and push insulation all day long with you, but they don’t care about your dew point or ventilation or fresh air or anything like that. That’s a big problem. The only education that people are getting out there comes from manufacturers.”
Another industry professional, who works for a building supply company, also cites the influence of manufacturers as a drag on standards. For obvious reasons, he didn’t want to be identified in this piece. “What we have seen in recent times is builders using a combination of insulations to achieve the regulation U-value, and it’s the cheapest way possible quite often...We see a bit of partial fill, pump or fullfill, and then a thermal liner board on the inside. It achieves the U-Value but you end up with quite a strange condensation profile in the wall.”
He points out that the cavity wall, introduced originally to prevent moisture ingress, is a hard habit to break. Because it has a long tradition in Irish building, it’s an easy sell for the industry. “The reaction is from the insulation companies of this world to get the sale of their board or their thermal liner for the inside. It’s all pushed on by them.”
The other issue with cavity insulations is moral hazard. “Builders tell you that there’s bits around corners and windows that are quite tricky to do and quite often they say, ‘sure once we get up another five or six courses of blocks, no one will know’.”
Archie O’Donnell also has concerns about dry lining your average cavity wall. In an email to Passive House Plus, he said: “It appears a sensible approach to achieve 0.18 to 0.2 Uvalue walls: build 100 - 120mm cavity with 60 - 80mm insulation, and then dry line it with a 50mm composite board. While this method has big advantages in that it gets very good U-Values and uses familiar skills and materials, it comes with inherent problems.”
He explains that when you split the insulation in two, the temperature of the inner leaf can drop below dew point temperature. People assume that the foil layer on the back of the composite insulation is a vapour control layer, but that layer is compromised at joints, intermediate floors, party walls and at sockets and pipes. Moisture laden air can get through the composite insulation layer and condense on the block inner leaf.
He goes on: “We’ve noticed in recently built houses where works would be done to extend or replace windows, when we remove the dry lining, we find black mould behind it.” He says that when considering insulation strategies, you have to consider vapour management and ventilation strategies simultaneously. “The emphasis on achieving high performance airtightness and vapour control cannot be compromised.” In July 2010, the Department of the Environment published a regulatory impact assessment (RIA) on the proposals to amend Part L of the building regs. The document included a table which listed nine separate dwelling specs as a guide to achieving compliance with the new regime. The spec for all nine included the following example: block-built cavity walls with 100 to 140mm partial fill cavity insulation in a 150mm wide cavity, and 50mm of dry lining on the inner leaf. This is exactly the kind of build-up that the experts interviewed for this article describe as problematic.
One of the most worrying aspects of the mould and condensation problems that appear in new builds is that in many cases, these houses comply fully with the requirements of the technical guidance documents, and therefore meet prima facie compliance with the building regulations. Simon Jones says that in the development where he pulled back wardrobes to find mould growth, the builder had complied “to the letter” with the technical guidance document for Part F, the section of Irish building regulations that deals with ventilation. “They have all the right holes in all the right places, the right undercuts under doors, the right fans that come on at the right times and so on, but the buildings simply weren’t ventilating adequately.”
Very bad practice in terms of how to close a cavity, respectively using blockwork and an SIG insulated cavity closer
In the aforementioned regulatory impact assessment from 2010, the sole ventilation strategy detailed in each of the nine house types was natural ventilation with between two and three extract fans – a common ventilation strategy unsupported by evidence of its efficacy, as Kate de Selincourt’s detailed investigation in issue 6 of Passive House Plus reveals. Jones says: “The technical guidance documents which support the building regulations lists just natural ventilation with intermittent fans and mechanical ventilation with heat recovery ventilation. It provides no guidance for any mechanical extract ventilation or passive stack ventilation.”
When asked why mechanical ventilation was not include in the RIA, the department issued this response: “Mechanical ventilation in the Irish residential sector is a new and growing approach. Its use is not mandatory. Regulatory impact assessments and guidance in the first instance concentrate on the most commonly used or typical approaches.”
The department’s response goes on: “The general approach taken in building regulations and the accompanying technical guidance documents is to set appropriate performance requirements and to leave it to designers to specify the appropriate solution for a particular building.”
By creating the impression that natural ventilation supplemented by extract fans in wet rooms will be sufficient to maintain indoor air quality in super-insulated, airtight homes, the regulations are making air quality hostage to commercial expediency. If a developer isn’t required to spend money on delivering a working ventilation strategy, he won’t.
“All of the evidence that we see on a weekly basis,” says Simon Jones, “and all of the evidence we see through modelling shows that there is a point at which natural ventilation and intermittent fans don’t provide adequate indoor air quality.”
Mark Shirley agrees. “Part of the problem at the moment is that DEAP [the software used to calculate building energy ratings and demonstrates compliance with Part L] can’t account for any of the kinds of systems that companies like Aereco or Partel in Galway are bringing in, where you have a mechanical room vent operated quite often on a humidity sensor or carbon dioxide sensor. These are good technologies, but unless the builder is going to reap some benefit from making the investment, it’s hard to see them becoming more common.”
Note that the mould growth issues identified in this article all occurred before occupancy – granted, while the buildings were drying out. Add people into the mix and the potential risks may increase dramatically. In this climate, drying clothes inside is more the rule than the exception – especially in apartments – while Irish homeowners have a long history of blocking up holein- the-wall vents. Over-occupancy and what the industry calls ‘excess’ furnishings can further compromise a natural ventilation strategy.
“It’s my belief that at anything below five air changes at N50,” says Simon Jones, “a ventilation strategy needs to be in place that takes a large element of control away from mother nature and away from people. There’s too much at stake when it comes to indoor air quality.”
It is vital to point out that the problem here is inadequate ventilation, not airtightness. The common misconception about airtightness is that it is solely about the improvement of thermal performance. The reality is that it’s about structure —after extensive research, the Passive House Institute settled on 0.6 air changes per hour as a target to mitigate the risk of interstitial condensation and its implications for the structure of buildings.
Moral hazard raises its head again and again in this debate. Brian Shannon of Building Envelope Technologies in Wexford says that cheap make-shift airtightness products are going into new houses all the time. He notes that while these products may deliver a target airtightness level in the short term, they will ultimately fail. “If you gave me a house that’s achieving an air permeability of 20 and gave me a box of masking tape, I’d get that house down to passive standard for you, no problem, but that masking tape just won’t last.”
Good practice in terms of how to close a cavity
Then there’s thermal bridging. As houses become more thermally efficient, thermal bridging becomes more important. If it is not adequately dealt with at key junctions, it can have a severely negative impact on the overall performance of a house. TGD L’s response is that the Yvalue – the total thermal bridging factor for the building – can be derived in several ways. A default Y-value of 0.15 W/m2k can be used, though this would be punitively bad in the case of buildings with even moderately good thermal bridging details, and would make compliance tricky. Building fabric consultant & NSAI accredited thermal modeller Andy Lundberg of Passivate warns that TGD L stipulates that thermal bridges must not cause mould growth. “You can use a value of 0.15 in any case, however in doing so you’re stating that none of the junctions present a risk of mould growth and surface condensation, and therefore must have been assessed in accordance with the relevant standards and conventions for thermal bridge assessment. That’s absolutely not being done. As one of only two NSAI certified modellers, I’ve not once received a phone call from anyone seeking to have junctions assessed so they can use 0.15.”
Lundberg points out that the National BER Research Tool – which contains detailed information on all published BERs, including information on Part L compliance – shows 140 dwellings built in 2014 with a 0.15 Y-value listed. “One can only assume that the BER assessor in each of these cases has the relevant documentation on file to demonstrate that all junctions (non-ACD/catalogued) are free of any mould growth and surface condensation risk, which they are required to!”
Another option is to commission a certified and registered thermal bridging modelling assessor to calculate the Psi-values for each thermal bridge – potentially adding significant additional costs just to establish how good or bad the chosen details are.
Alternatively a Y-value of 0.08 can be used for details in accordance with the acceptable construction details (ACD) created to support the 2008 regs. But as Lundberg points out, the ACDs are incomplete – they don’t include a door threshold detail, or other common details such as a roof insulated on the ceiling plane with a rooflight installed at rafter level. “Where a dwelling has a roof-light installed but uses a 0.08 Y-value, the conclusion can only therefore be that the BER assessor or client has had thermal modelling carried out to determine the psi-values of this and any other junction requiring assessment, and the Y-value happened to work out at 0.08 by pure coincidence.” As Shannon adds, compliance with the ACDs is not independently validated.
“In DEAP, you can enter a figure of 0.08 for thermal bridging, and that will increase your thermal performance dramatically [compared to the 0.15 default]. To use that value, all you need is a letter from the developer or the architect which says you built to ACDs.” He cites a recent development he visited in which extensive thermal bridging issues were utterly misrepresented in the energy rating assessment.
Energy efficiency standards for dwellings in Ireland have come a long way over the past ten years. But one developer is critical of the standards he now has to meet. Again, he asked to remain anonymous. “There’s a law of diminishing returns on this environmental stuff,” he says. “If you went out to buy a new car for your family, your first thoughts wouldn’t be a Bentley or a Rolls Royce, you’d buy a Toyota Corolla or a middle range car... From a builder’s point of view, we have now been forced to create a level of administration and that has to be paid for by the customer.”
Strictly speaking, this is incorrect. As leading property economist Tom Dunne explained in this magazine’s predecessor Construct Ireland3, the market determines what price it’s prepared to pay for property, and new homes must be considered as a part of the available stock that’s up for sale at any given time. Buyers may be prepared to pay more, as the aforementioned reports indicate, but suppose the developer bidding to buy the land wasn’t convinced. They’d work out what price they reckoned each unit might go for, deduct the construction costs – including cost of compliance with Part L – and the remainder is what they’d bid for the land. So higher construction costs aren’t affecting the total development cost, but are rather causing land prices to fall to absorb the construction cost rise. Which is substituting economically unproductive spend on land for job-creating construction activity, with additional benefits in terms of reducing national energy imports and carbon emissions fines.
This kind of clamour for a relaxation in standards worries Mark Shirley. “We’re building exponentially better houses now than we were five or six years ago,” he says. “I think if the regulations were rolled back in any way, that would be a disaster. We have come so far.”
1 Hyland, M; Lyons, R & Lyons S; “The Value of Domestic Building Energy Efficiency – Evidence from Ireland”; Oxford, 2012
2 Fuerst, F; McAllister, P; Nanda, A & Wyatt, P; “An investigation of the effect of EPC ratings on house prices”; London, 2013
3 Dunne, T; “Safe as Houses”; Construct Ireland Issue 5 Volume 3, 2006