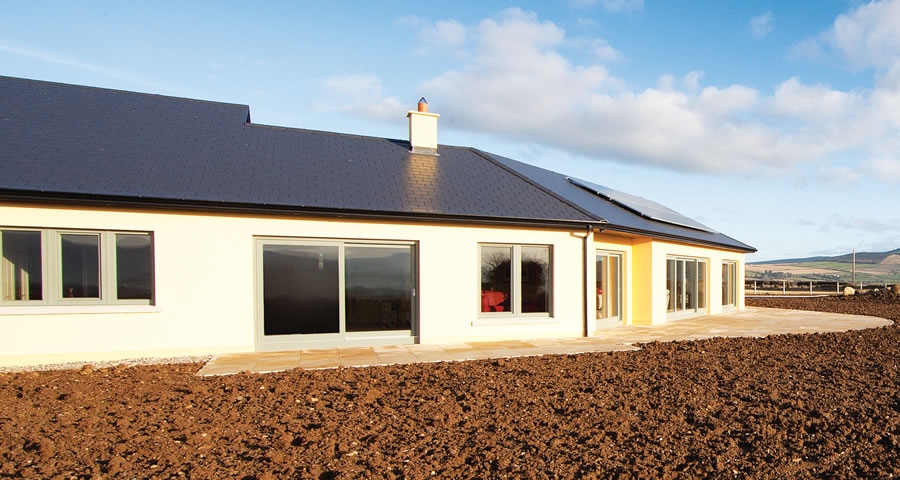
- New build
- Posted
Ireland’s most energy efficient building?
A new house in Wexford is the first in the country to achieve an A1 Building Energy Rating and certified passive house status – arguably making it the most energy efficient building yet built in Ireland. So why did a regulatory flaw risk rendering it non-compliant?
Francis and Brigid Clauson’s new self-build is arguably the most energy efficient house yet built in Ireland. Yet it almost failed to meet building regulations. When working through the calculations for his Building Energy Rating (BER) Clauson discovered that though his plan would comfortably meet the highly onerous passive house targets, it would actually breach the renewable energy obligation under Part L of the building regulations.
Long before he broke ground on his elevated site in Bunclody, Co Wexford, Clauson carried out an enormous amount of research. In addition to many hours on the internet, he talked to dozens of professionals and went to visit houses and sites to question people about the choices that they had made. “I’m absolutely maniacal on detail,” he admits. “I questioned every single individual extensively about what they were telling to fully validate their responses.”
An IT professional by trade, Clauson and the design team he chose used two software packages to design and model the energy performance of the building. Deap – the Dwelling Energy Assessment Procedure – is the Irish equivalent of the UK’s Sap software, and is used to calculate Building Energy Ratings and demonstrate compliance with energy efficiency targets under Irish building regulations. PHPP is the software developed by the Passive House Institute for the design of passive houses. In order to fully understand both, Clauson actually built a model which married them together. It was while working through the figures on his hybrid model that he turned up this startling anomaly: his house was so energy efficient he couldn’t generate enough renewable energy to meet minimum requirements set by the Department of the Environment. The house just didn’t have the energy demand. “If you need 50 to 75 kWh/m2/yr – as an A3 house would – then it’s easy to generate 10Kwh/m2/yr of renewable energy,” he said. “But as you reduce this demand to say 30 kWh/m2/yr the percentage of overall energy which has to come from renewables grows – and thus becomes harder to achieve.”
The problem stems from the changes to Part L of the Irish building regulations introduced in 2007, when renewable energy systems became mandatory for all new homes, along with unprecedented improvements in terms of both energy efficiency and carbon emissions. The regulation itself doesn’t go into detail. Instead it makes some general statements about energy efficiency, carbon emissions and renewable energy. It states that new homes must be designed and built “to limit the calculated primary energy consumption and related carbon dioxide emissions insofar as is reasonably practicable”. It then adds the requirements that a “reasonable proportion” of that energy demand must come from renewable sources. There’s a subtle but important point in this cumbersome language. The regulation says that energy demand and carbon emissions must be reduced to the greatest extent possible without going to unreasonable lengths, but it doesn’t go so far with renewables – it only requires that renewable energy makes up a reasonable fraction of the total energy demand.
These general statements are fleshed out into clear targets in the technical guidance documents (TGDs). When the new Part L was published in 2007, TGD L was also updated. It defined the energy and carbon saving targets as 40% reductions in primary energy for space heating, hot water, cooling and lighting, rising to 60% reductions in changes to TGD L from December 2011. But both changes to TGD L set the renewables target at a fixed number – 10 kWh/m2/yr of thermal renewable energy, or 4 kWh/m2/yr of microgenerated electricity. This wasn’t a widespread problem for people building to scrape compliance with TGD L 2007, as for most building types the 40% energy reduction target still left a reasonable chunk of primary energy, meaning renewables still had a demand to help meet. For some smaller house types a fairly small solar thermal array could hit the 10 kWh/m2/yr target. Biomass boilers could typically comply, as could many heat pumps in spite of being penalized for various reasons outlined below.
According to the Department of the Environment, meeting the targets set out in TGD L indicates “prima facie” evidence of compliance – a legal term which means that building to the levels set out in the TGD ensures compliance with the regulation. The department is on record as saying that the only way to actually guarantee compliance is to hit the targets stated in the TGD. When pressed on this point by Passive House Plus editor Jeff Colley at the See the Light conference in Dublin in September last year, a department spokesman said that people who’ve built very low energy homes and therefore failed to meet the renewables target would need to take their cases to court if they’re to prove compliance.
Clauson had determined that the most pragmatic way of heating his super low energy house was by using a heat pump. The problem however is that the house is so well insulated, so airtight and so cold-bridge free that very little heat is actually needed. Clauson’s solution was to choose a heat pump capable of being programmed to match the building’s actual heat loss on a live basis: a Danfoss air to water heat pump installed by Heat Doc Ltd. “For super low energy houses that ability to auto adapt and adjust minute by minute is key to maintaining comfort levels,” says Mike Teahan of Danfoss distributors Heat Pumps Ireland. “Most modern heat pumps have this built in functionality.”
But both Deap and the new regulations give heat pumps a hard time. TGD L stipulates that only energy above a seasonal performance factor (SPF) of 2.5 can be counted towards the 10 kWh target to take account of the primary energy of grid electricity due to generation and transmission losses. According to Deap, every kilowatt used by the heat pump takes 2.42 kilowatts of energy use at the power station – 10% lower than the 2.7 kilowatts Deap listed till 2011.
Energy from the heat pump to provide hot water can be counted towards the 10 kWh target, though this portion of the heat pump’s output is subject to a 25% penalty to take account of efficiency losses at higher temperatures.
But other penalties are due to the software’s difficulties handling non-traditional heating approaches. Deap assumes intermittent heating – where the building first goes cold and is then quickly loaded with high temperature heat. “The problem is that Deap is treating your heat pump as if it’s a boiler,” Mike Teahan explains, adding that the problem would have been exacerbated if Clauson had paired the heat pump with radiators. “When you plug a heat pump running on rads into Deap it automatically assumes you have an on/off cycle of heating up and cooling down. If you heat a building in this way you’ll have to use the heat pump at high temperature to bring the building back to the desired temperature quickly. But if you use a heat pump with rads, full weather compensation, and minute-by-minute control, you don’t have to have the rads at high temperatures. The temperature of the rads changes subtly as the weather changes.”
client Francis Clauson on-site during the build
Teahan has a word of caution regarding how many people think the renewables obligation works. “Most people seem to think that if you work out the size of the house times 10 kWh, that’s what you need to provide from renewables. That’s not the case at all. What you’re actually required to do is bring the BER result of the house down by 10 kWh/m2/yr.”
Clauson worked out in Deap that his heat pump would provide just 5.21 kWh/m2/yr towards the renewables obligation whereas his total energy demand is 42.64 kWh/m2/yr, so the proportion of energy provided by renewable technologies needed to be 23%. The big question is, does this 23% represent a ‘reasonable proportion’? What if Francis Clauson decides that it does but the building control officer decides that it doesn’t?
Once he’d discovered this flaw, he went on to conduct a series of experiments on Deap. He reduced his thermal bridging values back to default figures, thereby seriously compromising the integrity of the building envelope. The exercise pushed the heat pump’s contribution to the energy needs of the house up to 9.3 kWh/m2/yr. Still not enough. Then he reduced the air tightness from the passive standard target of 0.6 air changes per hour to the default 7 m3/hr/m2, and this finally pushed his renewables contribution above the TGD L threshold, to 15 kWh/m2/yr.
Though these changes moved the renewables contribution from 5.21Kwh/m2yr to 15 Kwh/m2/yr, they made the building less energy efficient. “This is barmy,” says Clauson.
The other alternative – and the one Clauson chose – was to add additional renewable technologies to his house, in this case a solar photovoltaic array. “If I threw away my window certificate and threw away my heat recovery certificate and just reverted to default values, I wouldn’t have needed to put the PV panels on the roof,” he says. “You could say that my PV is eco-bling but I had to put it in place to comply with the regulations. But that said, at Christmas it enabled me to cook my turkey and ham for nothing!”
Ironically, Clauson’s original intention hadn’t involved passive house, or even low energy. “The whole point of the house was really to capture the sun throughout the day, but as we got further through the process, we realised that the difference between part L of the 2011 regs and passive is insignificant. That’s when we decided to go for it.”
He engaged architect Zeno Winkens and Archie O’Donnell of Integrated Energy as energy consultant, and got a local contractor, Chris Gahan of GR8 Construction to do the work.
Zeno Winkens says that at the outset, Clauson provided him with a sketch together with a highly detailed brief – “nearly down to the hooks on the back of the door in the children’s bedroom” Taking this brief as a wish list, Winkens carefully assessed the site and came up with a design that married the client’s needs with passive principles. “The site wasn’t 100% north south, it was coming in at an angle, that’s why I chose the L design with a cut-off corner,” he says. “Though it’s quite a large house, from the road, it still manages to look quite modest.”
With design, orientation and layout agreed, the design team moved on to how the house might be built. “I followed the mantra of the four Ps,” Clauson explains. “Passive, pragmatic, price-conscious and practical. Any measure we took had to hone into those four.”
He investigated both timber frame and externally insulated options but elected in the end to go with a conventional building method – a standard block built wall, albeit with a wide, 250mm cavity. The robustness of the block was a big attraction for Clauson, plus the way it dealt with the Irish climate on what would be a very exposed site. The fact that it is such a long established construction method and that there was extensive local expertise was also a deciding factor. “What’s critical about this project is that it’s been built by local trade using local materials,” says Archie O’Donnell of Integrated Energy. “When we started doing passive house a lot of the techniques and technologies would have been copied from central Europe and I think what’s useful about this is that the construction details and the solutions are ones that are familiar to a lot of Irish tradesmen.”
Chris Gahan of GR8 Construction says that the exhaustive research and huge level of preplanning that Clauson put into the project was central to it success. “Francis had weekly or fortnightly meetings, complete with agendas, so it was run more like a commercial job than a one-off house,” he says. “To get to passive, you have to be detail oriented, we all knew that starting out. To be honest it ran very well.”
Thermal bridging issues at foundation level were dealt with through the use of Quinn Lite blocks in the rising walls. Thereafter, designing away cold bridges and ensuring airtightness with a wide cavity construction involved the drafting of more than twenty individual details in a painstaking, iterative process. “Each detail was investigated by the design team,” says O’Donnell. “They would have been improved, they would have been put through thermal analysis, further improvements would be made, then we’d coordinate with say a plumber or an electrician and improve those details yet again.”
Installing the windows did present particular problems. Alan Tier of Integrated Energy explains that their initial aim – for aesthetic and budgetary reasons – was to install non-thermally broken ‘lift and slide’ windows as opposed to passive certified, thermally broken ‘tilt and slide’ windows. It is, he explains, theoretically possible to install non-passive standard windows and still achieve a passive standard performance, so long as no point of the internal screen is allowed to fall below 13 degrees. Tier modeled the windows exhaustively with this aim in mind, but in the end, he had to concede that due to the surface area of the building, it just wasn’t possible. Instead, a combination of both passive and non passive certified windows were installed.
“Probably the biggest challenge was getting the airtightness membrane around the reveals and getting that to interface with the internal leaf of block work,” says Chris Gahan.
Aided by the day lighting benefits that tend to come with passive houses – an orientation and form which tracks the sun will also yield a natural light benefit – the house’s electrical lighting requirement balances energy saving with atmosphere. “The brief from the client was for the lighting design not to be dictated purely by energy efficiency," says lighting designer Rocky Wall of Wink Lighting, "but to create atmosphere and mood using energy efficient light sources." The design mixes CFLs, LEDs, IRCs and fluorescent bulbs to find the right tones of light for the house’s various spaces. The control system is simplicity itself: conventional switching and dimming.
Coming up with a mechanical package for the house was another painstaking process during which various combinations of technologies were modeled and tested – from oil, gas and solar thermal through to the combination of heat pump and PV panels on which Clauson eventually settled. Speaking to Passive House Plus just two weeks after moving in, he says that so far, the house has performed exactly as modeled on paper.
“Every nut, every bolt, every screw was thought out and put down on paper beforehand,” says Archie O’Donnell. “That meant that it was a dream to go on site. If there was one guiding principle that Francis brought to the project, it was that if you don’t have everything thought out on paper beforehand, you’re on a hiding to nothing. Nothing was left to chance, and there was no ambiguity about what was required.”
For more information on this build visit the website set up by Francis Clauson: www.low-energy-construction.com
Selected project details
Owners: Francis & Brigid Clauson
Architect: Zeno Winkens
Energy consultant: Integrated Energy
Main contractor: GR8 Construction
Quantity surveyors: Patrick Breen
Structural engineer: Deane Turner
Heating engineer: Heat Doc Ltd
Airtightness & cellulose installer: Cliomahouse
Airtightness tester: Greenbuild
Lighting design: Wink Lighting
BER assessor: 2eva.ie
Passive house certification: Peter Warm
Airtightness system & cellulose insulation: Ecological Building Systems
Airtight plaster: Gyproc
Windows & doors: True
Windows Insulation: Isover/Kingspan/Xtratherm
Cavity insulation installer: Bunclody Insulations
Thermal breaks: Quinn Lite
Heat pump: Heat Pumps Ireland
Heat recovery ventilation: Versatile
Kitchens: Andrew Ryan
Interiors: Doyle Design
Additional info
Building type: 359 sq m bungalow built to take in the panoramic views stretching to over 30 miles and to maximise the solar gain.
Location: Bunclody, Co Wexford
Completion date: December 2012
Budget: not disclosed
Passive house certification: certified
Space heating demand (PHPP): 13 kWh/m2/yr
Heat load (PHPP): 10 W/m2
Airtightness: 0.54 ACH at 50 Pa
Energy performance coefficient (EPC): 0.099
Carbon performance coefficient (CPC): 0.091
BER: A1 (14 kWh/m2/yr)
Thermal bridging: great attention to detail throughout the build including first three courses of Quinn Lite blocks on all rising wall to reduce heat loss to the ground, very detailed window and door installation detail with PIR insulated reveals, thermally broken windows, sloping roof to wall join to ensure continuous thermal envelope
Airtight layer: Gyproc Airtite Quiet plaster applied to inner leaf block work. Pro Clima system including Intello membrane to ceiling and tapes at all junctions and penetrations throughout. Ceiling fixed to metal furring inside airtight layer to avoid breaching airtight membrane
Ground floor: standard sub floor construction with 200mm Kingspan insulation under screed. U-value: 0.098 W/m2K
Walls: 100mm regular block, 250mm wide fully filled with Ecobead platinum bonded bead pumped cavity insulation and 100mm regular block. U-value: 0.15 W/m2K
Roof: Plaster board / 250mm service cavity / airtight membrane / 500mm pumped cellulose U-value: 0.084 W/m2K
Windows: triple-glazed Passive House Institute certified Miratherm windows – with a typical U-value of 0.8 W/m2K
Heating system: Danfoss air to water heat pump with Harp registered SPF of 4.13. Under floor heating system across the whole building which has been left open circuit (i.e. no thermostats) except for the bedrooms which are kept cooler. Wood burning stove in sitting room
Lighting: a mix of low energy lighting including CFLs, LEDs & IRCs with dimmers and fluorescent bulbs
Ventilation: Passive Institute certified Zehnder Comfoair 350
Renewable Electricity: 16m2 solar photovoltaic array with average annual output of 4.2kW
Green materials: cellulose insulation, all timber furniture from PEFC certified sources