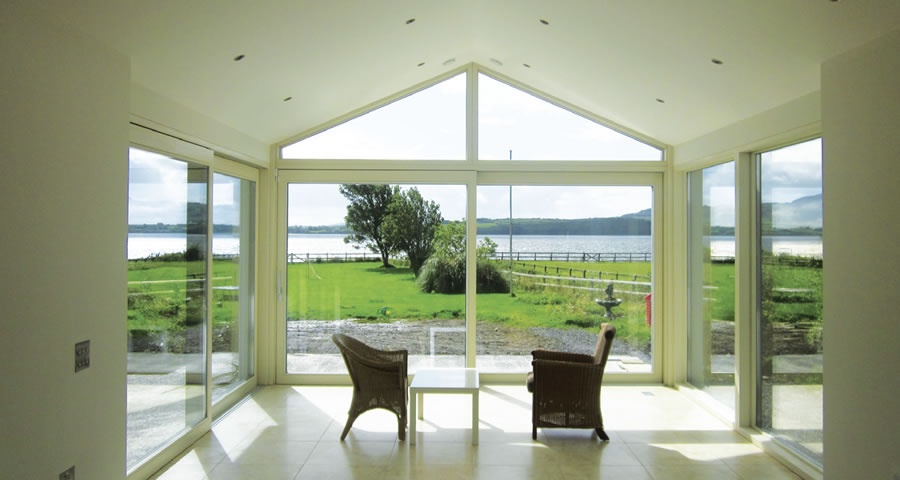
- Upgrade
- Posted
Detail key to low energy refurb on Sligo coast
How do you make an old building liveable on Ireland’s wind ravaged Atlantic coast? The answer lies in the envelope, with airtightness, super insulation and the eradication of cold bridges
Achieving high build quality in low energy design is challenging enough. Trying to make a legacy building perform to the same standards is doubly so.
Archie O’Donnell of Integrated Energy was the energy consultant on architect James Walsh’s deep retrofit at Rosses Point, Co Sligo. “It’s often said,” O’Donnell explains, “that when it comes to a low energy renovation, you’d have put together a tender package for an office block or an apartment block in half the time.”
Because every refurb is different, the architect has to come up with a range of solutions for all kinds of issues – from airtightness to cold bridging to preserving the insulated envelope – and very many of these will be particular to the project.
As is typical of so many low energy retrofits, the success of the Rosses Point building hinged on the fact that there was one man at the centre of the project to do two things – co-ordinate everyone involved, and drive the high standards required. Architect James Walsh took that role.
“We didn’t set out to design passive,” says Walsh, “but to deliver the principles of it.”
Eliminating cold bridges was the biggest challenge he faced. In particular, marrying the existing cavity wall with the new structure generated huge volumes of work. Walsh drew up well over thirty separate construction details specifically to deal with thermal bridging issues. These details covered the likes of new and existing rising walls, the eaves for both the flat and pitched roofs, along with chimneys, roof-lights and a lot more besides. The process of refining these details down from first draft through to final version was equally exacting, requiring extensive co-ordination between architect, engineer, builder and key installers, such as in the case of windows and external wall insulation.
The house in it's original condition
Once agreed beforehand, these drawings then became central to the day-to-day building work. “Communication with the builder happened on the drawings,” O’Donnell continues. “The architect insisted on that. He didn’t want to be trying to explain things over the phone to a builder on a windy scaffolding in Rosses Point. It was on detail, it was priced, it was agreed, it was workable.”
O’Donnell points out that passive house and EnerPHit (passive house refurb) buildings are in a different league to traditional Irish construction in terms of detail. “They’re not your Homebond solution, there’s no guidebook on it. Every detail seems to be unique, so it really has to be teased out before a builder sets foot on site.” Working out details in advance does bring obvious advantages though. “If the architect’s details are cognisant of airtightness and thermal bridging, it means you’re not going to get large cost variations on site,” says O’Donnell. “It makes for a smoother build process.”
Triple-glazed windows bracketed on to blockwork maintain a complete thermal layer, level with the external insulation
It’s also essential to bring everyone along with you. Contractor Stephen Taylor had worked on low energy buildings before, and he too pays tribute to James Walsh’s rigour in getting every aspect of the building nailed down on paper before a block was laid.
“I’m at the structure end of it and all I want to do is get the roof covered and move on. James will always be there asking ‘Well, if we put that piece of timber there, how does it affect my insulation?’”
Similar questions arose in relation to ventilation ducting. In an airtight building, ventilation is paramount. The heat recovery ventilation systems typically specified for low energy and passive structures require space for ducting runs.
New concrete floors were insulated with Xtratherm insulation with careful perimeter detailing
“To get it out of sight you’re going up across rafters,” says Taylor. “James asked, ‘Well ok, what does that do to the insulation? If it’s reducing the insulation at one part, how do we change the insulation there to compensate for that?’ So there’s a lot of thinking going on all the time.”
Taylor says that if eliminating cold bridges is the primary challenge in low energy retrofit, achieving airtightness is at least a close second. Everyone has to buy in to the idea.
“Me and the guys working with me, we’ve got to understand what we’re trying to do here, because before you ever work with it, airtightness seems silly,” he says. “You think, what are they trying to do here? It’s just more expense. It’s only when you go back to an airtight house afterwards and you feel the benefits that you realise how important it is.” Now a full convert to the process, he believes that airtightness may be more critical to delivering a comfortable home than insulation, particularly on the windy west coast.
There is a view emanating from some industry guidance posits that in mechanically ventilated buildings an airtightness of three air changes per hour under pressure test conditions represents “best practice” – an assertion which sounds dated given the growing number of buildings beating the passive house standard, which sets the bar at a level that’s a full five times more airtight. O’Donnell stresses that even if you don’t believe an air change rate of less than 3 ACH is needed, it’s still very useful to aim for passive or EnerPHit targets. It sets a visible benchmark for the project and sends the signal to everyone involved that quality is being monitored.
Attention to airtightness detailing was important throughout the build, with proprietary products used around floor and roof joists, and window junctions
“If a builder has a problem with that, then you need to look more closely at why he has a problem and what his agenda is. Most builders now do buy into that and when they go to the next job, they will find it useful to boast that they have achieved this level of airtightness because it’s now seen as the industry measure of quality.”
“Once upon a time, if you were asking someone about a builder, you’d ask, what are they like for variations? Now, the first question is what kind of airtightness are they getting.”
Architect’s statement
James Walsh, Low Energy Design
Refurbishing and extending your home can be a daunting challenge for the homeowner, even more so when embarking on a deep retrofit that involves upgrading or replacing the majority of the building fabric. The clients at Rosses Point embraced the concept of thermally upgrading, a decision made easier by their experience of the thermally poor building fabric – including a winter lived with frost on the inside of their single-glazed windows.
The original dwelling was a 1950s pitched roof cavity wall structure facing south that had flat roofed extensions to the east and west along with a conservatory that had been subsequently added. Some investigative work was undertaken at planning design stage to check the wall build up, leading to the discovery that the cavities were predominantly empty.
We retained the dwelling footprint while adding a small extension to the east for a bedroom, and replaced a single glazed conservatory with a pitched roof glazed family room.
External wall insulation was agreed as the most appropriate solution to thermally upgrade the existing walls with cavities filled with Ecobead. The existing roof spaces had very low ceiling levels, which were replaced to provide habitable accommodation that also takes advantage of the southerly aspect and views. Existing flat roofs were upgraded to warm roofs.
Attention to airtightness detailing was paramount throughout the build. Membranes were dressed around floor and roof joists at an early stage to ensure simple sealing further on. Close cooperation and detailed discussion – involving contractor Stephen Taylor, Sto external insulation installer Michael O’Donnell of Atlantic Plastering, Brian Raftery of True Windows and myself – ensured the main junctions were constructed to a high standard of airtightness and thermal performance. Éasca approved airtightness consultants Ecoscan tested the fabric at first fix stage and the building achieved 1.94 m3/hr/m2 at 50 Pa. A slight improvement on this could be expected if the building had been tested post completion. A heat recovery ventilation system from another Éasca approved company – Tuam-based manufacturer ProAir Systems – delivers fresh air to provide health benefits to the occupants.
The building has been elevated to an estimated A3 Building Energy Rating. If the existing oil boiler was replaced, it would achieve further improvement.
The owners hope to enjoy the benefits of a comfortable warm healthy home for their family for many years to come.
Selected project details
Clients: David & Louise McCabe
Architects: Low Energy Design, James Walsh
Contractor: Stephen Taylor Builders
Civil/structural engineer: Jennings O’Donovan & Partners Consulting Engineers
Services consultant: Meed Building Services Ltd.
Energy consultant: Integrated Energy Ltd
BER assessor: Brian Fitzpatrick
Airtightness tester: Ecoscan
Windows & doors: True Windows Ltd
External wall insulation: Sto, installed by Atlantic Plastering
Additional insulation: Xtratherm, Ecobead, Rockwool & Warmcel
Rockwool & Warmcel insulation installer: Abbey Insulation
Roof lights: Velux
Airtightness products: SIGA
Thermal breaks: Quinn Lite blocks
Solar thermal installer: Solar Energy Ireland
Heat recovery ventilation: ProAir
Additional info
Additional info
Building type: 331 sq m detached two-storey cavity wall dwelling
Location: Rosses Point, County Sligo
Completion date: August, 2012
Budget: private
Passive house certification: not certified
Space heating demand (PHPP): no PHPP analysis carried out
Airtightness: 1.94m3/m2/hr at 50 Pa
Pre upgrade Building Energy Rating (BER): D2 (247.18 kWh/m2/yr)
Post upgrade indicative BER: A3 (69.98 kWh/m2/yr)
Thermal bridging: course of Quinn Lite blocks for any new build walls at floor insulation level, aluclad window frames with insulated reveals, externally and internally, and adhesively fixed external insulation. Y-value (based on ACDs): 0.08 W/mK
Ground floor: new concrete floors insulated with 120mm Xtratherm thin-R XT/UF insulation. U-value: 0.15 W/m2K
Walls: EcoBead Platinum blown bead EPS insulation to existing cavities with 160mm of Sto K System (adhesively fixed) external wall Insulation. Average U-value: 0.19 W/m2K
Pitched roof: Tegral fibre cement slates externally on 50x25 battens/counter battens, followed underneath by breathable windtight roofing membrane, SIGA Majcoat, 225mm timber rafters at 400mm centres fully filled with Warmcel cellulose insulation, SIGA Majpell airtightness membrane, 50 mm Rockwool Flexi insulated service cavity, 12.5mm plasterboard ceiling. U-value: 0.17 W/m2K
Flat roof: Soprema Flagon SR mechanically fixed roofing membrane on Xtratherm XT/FR-ALU 130mm on WBP plywood fixed to furring pieces on 150mm roof joists at 400mm centres with SIGA Majpell airtightness membrane and a 12.5mm plasterboard ceiling. U-value: 0.16 W/m2K
Windows: Doleta triple-glazed aluminium-clad pine windows with argon filling. Average overall U-value: 1.15 W/m2K
Heating system: existing 70% efficient oil boiler supplying underfloor heating and radiators, with a six sq m 36 evacuated tube Ritter solar CPC12 Inox system supplying Joule 400 litre twin coil unvented stainless steel insulated water tank for domestic hot water
Ventilation: two ProAir PA600 heat recovery ventilation systems and associated ducting, with a Sap Appendix Q certified efficiency of 90%
Green materials: cellulose insulation