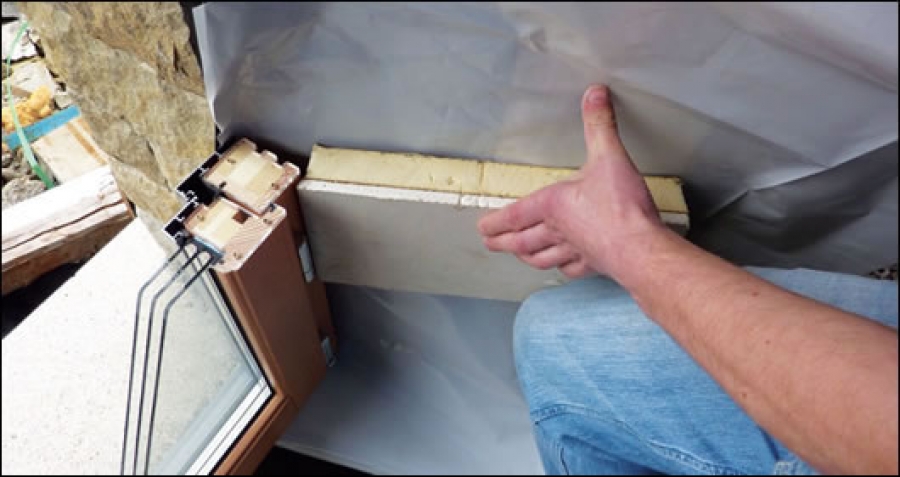
- Passive Housing
- Posted
Enerphit: the passive house approach to deep retrofit
While the principles of low energy building apply equally for new build and upgrades, the reality is that hitting passive levels becomes much trickier when retrofitting. The Passive House Institute have taken this on board and created a retrofit standard that is ambitious but achievable
Some of the estimates of the numbers of empty houses in Ireland are frightening. The RIAI reported last year that the figure could be anything up to 352,000. With so many resources invested in the existing housing stock, and with the banking system still dysfunctional, we’re unlikely to see any recovery in new build for some time. We now know too that large swathes of the housing stock built in the last decade is of very poor quality. If there’s going to be any revival in the building industry in Ireland, retrofitting is going to form a big part of its future. Tomás O’Leary of MosArt looks at it from another angle: “The existing housing stock is the elephant in the room as far as energy consumption worldwide is concerned.”
The Passive House Institute has been working on a way of dealing with this elephant for the past number of years. Finally, at last year’s Passive House Conference, founder of the institute, Dr Wolfgang Feist, launched Enerphit, a passive house certificate for the modernisation of old buildings.
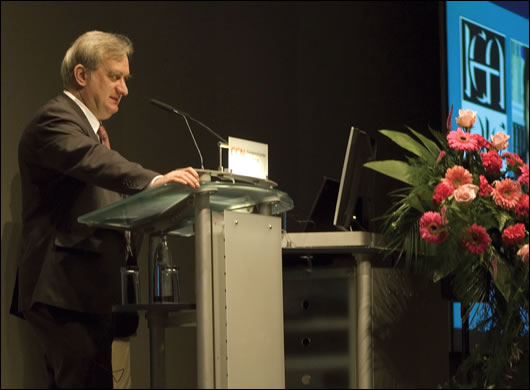
Passive House Institute founder Dr Wolfgang Feis, who launched the Enerphit standard at last year’s Passive House Conference
Speaking at the launch, Dr Feist pointed out that the energy consumption of old buildings can’t usually be brought to the level of new build passive house standard, because among other things, some unavoidable thermal bridges remain. "But the same components as for new passive house buildings can be used, and the building substance can thus be protected and sustainability can be improved significantly. In numerous projects, a reduction of 90% in the heating demand could be achieved.” As Feist implies, the institute recognises the multiplicity of building forms faced by retrofitters and as a result has stitched a significant level flexibility into the Enerphit standard. The thresholds are looser, and nor are there as many of them. Moreover, a form of certification is achievable even if these minimum values are not.
“Enerphit reflects the fact that when you’re retrofitting, the challenges are much greater,” says Tomás O’Leary. “With new build passive house, the space heat demand is 15kw/m2/yr. It’s 25 kw/m2/yr for Enerphit.” The other key parameter is airtightness. The 0.6 air changes per hour required by passive new build is retained as a target only, with a rate of under one deemed satisfactory for refurbishment. Those figures, O’Leary is keen to point out, are not plucked from the air, and nor are they solely arrived at through building physics. The pilot programme undertaken prior to the launch of Enerphit included extensive economic modelling which fed into the designation of the thresholds.
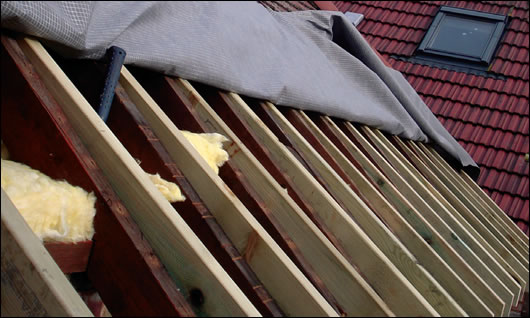
At Grove Road specific heat energy requirements will be reduced by 95%, while also minimising primary energy use. The project – which included stripping back and airtightening the roof – is still due to have its final air test and so has not yet been submitted for Enerphit certification
While the 25kWh/m2/a represents a relaxation from the new build standard, it’s still a very ambitious target for retrofit and won’t be achievable in all circumstances. Enerphit certification is still possible however through the use of what the PHI call "passive-house-suitable components".
“There’s a full Enerphit and there’s a partial Enerphit.” Tomás O’Leary explains. “The idea basically is to encourage people to do the very, very best that they can whenever they’re doing any work on a building. Let’s say your budget is limited and you want to do a big job on a project. Rather than putting in Mickey Mouse windows and Mickey Mouse insulation, you concentrate on one particular area or element of the build. The philosophy is: spend all your budget on one or the other and do the best that you can, because in time you might get more funds and you can do the other elements.” This approach is exemplified in the Ballynagran case study accompanying this article. With a budget of just under €60,000, MosArt zoned in a particular area of the school and achieved a great deal more than had they deployed the budget across the entire school. The official PHI documentation puts it like this: “The measures should be carried out in consultation with the certifier in such a way that maximum energy efficiency can be achieved, provided that, for the duration of their life cycle, the measures result in a financial net profit under the normally expected boundary conditions for the building owner and users collectively.”
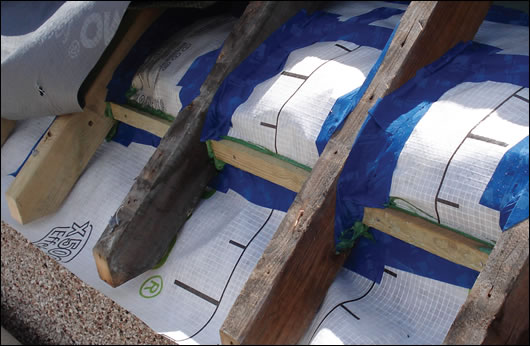
In order to maintain the integrity of the standard, any partial certification will state exactly what measures were undertaken and how these measures impact the energy performance of the building. “The client must appreciate,” says O’Leary, “that they can’t go round claiming that it’s a passive house if they’ve gone the partial route, but they can be very proud of themselves knowing that they’ve done a world class upgrade on those particular elements.”
On the ground, architects and engineers all say the same thing when it comes to passive house refurbishments. Airtightness and thermal bridges represent the biggest challenges. “I’d say the trickiest detail for the majority of Enerphit projects is airtightness in general,” says Cathal O’Leary of OLS architects in Wexford, “and in particular around the eaves detail, where you’ve got an existing cut roof or prefabricated roof truss sitting on an existing cavity wall.” With their first Enerphit project currently at the design stage, OLS are in the process of researching the best way of achieving airtightness.
Installing a continuous insulated envelope is much more difficult on retrofit. With cavity walls or block walls descending all the way to the foundations, thermal bridges cannot be designed out as they can on a passive new build. “It is tough to achieve,” says Tomás O’Leary. “Lets say your typical bungalow might have a footpath going round it on the outside, what you’re talking about to create a thermal bridge free connection is taking up that footpath or digging away the soil and running the insulation right down to the foundation. Those are the kinds of lengths that you’d often need to go to.”
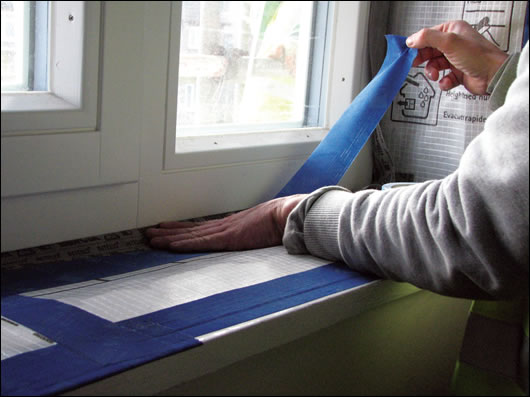
Passfield Drive has achieved an airtightness level of 1.9 air change per hour at 50 pascals – an excellent figure for a new build, let alone a retrofit, but some way short of the Enerphit standard. The architects are exploring further improving the airtightness to conform, or alternatively exploring the route to gaining certification though assessment of the building elements – the project is achieving the required specific space heating demand of 25kwh/m2yr
In choosing how to spend the budget on a passive retrofit, PHPP, the passive house software, becomes a very powerful design tool. In their Enerphit project in Monkstown, Brendan O’Connor of Joseph Little Architects says that the software was first used to see if the Enerphit standard could be reached and where the design was falling short. “It gave us a template for changes from an earlier specification. There are often compromises with existing buildings; the key thing is to know their significance. For instance we thought thermal bridging through internal masonry walls bypassing new insulated floors would be problematic, but thermal bridge analysis of our details and inputs into PHPP proved the additional heat loss would be insignificant.”
The Monkstown retrofit began life as a low carbon project that morphed into Enerphit after the Low Carbon Homes scheme became defunct. The transition from one design approach to another was revealing. The embodied energy of measures taken undoubtedly crept up, but the change forced greater uniformity in insulation, better control of thermal bridging and a big improvement in airtightness. In order to achieve a punishing airtightness target, there’s a natural tendency to strip the existing building right down, especially if airtightness was the bugbear of previous low energy retrofits. “We felt we almost needed to overdo the strip-out to reach the standard,” says Joseph Little. He accepts that there may come a tipping point where you ask, is it better to raze the building completely and start again?
“The Passive House Institute created Enerphit because the Passivhaus Standard is so much harder to achieve in retrofit,” says Little. “We had a very interesting discussion with them about the Monkstown project relating to what level of strip-out can still qualify for Enerphit and what level is virtually new-build, and therefore should achieve the higher standard. It’s much easier to achieve really high levels of thermal performance with new build. It’s a clean slate and so much more controllable.”
The question thrown up by the Monkstown project centres on resources. Are greater levels of waste – even if it’s properly processed – an acceptable by-product of achieving airtightness? “I think we’re in the infancy of trying to understand the impact of going either way - greater retention of materials or higher standards,” says Little. “But I would be suspicious of an argument that said knock everything, just start new each time.”
Tomás O’Leary agrees. “We often have clients who want to hang on to the shell of their house. They’re emotional about it. It’s all stripped back down to the bare walls and in truth in some cases, it might be more practical and easier to tear it down and start again, but there is a whole question about resources and where does the waste go? So there’s a broader sustainability question that needs to be tackled on that,” he says.
O’Leary believes that larger schemes provide the perfect application for Enerphit. “I think what it’s ideally suited to is local authority, low income housing units, especially those in poor condition. You can picture them; they’ve got single glazing, they’ve got old heating systems, they’ve got no insulation. I’d be anxious that this isn’t just for those who can afford to upgrade their private home. We should be looking at the larger projects, when there is a lot of fuel poverty. That’s the direction I’d like to see government policy take.”
Inset: the value of passive retrofit
In the pilot phase of Enerphit, the Passive House Institute carried out a number of case studies, which incorporated economic modelling on the impact of specific energy retrofit measures. One such case, the refurbishment of a commercial building in Germany, saw the heat load drop from 200 kWh/m2a to 26kWh/m2a. While it doesn’t quite meet the Enerphit threshold of 25 kWh/m2a, the refurbishment nonetheless saw an 85% improvement in the building’s energy performance. The institute went on to demonstrate the value of each element of the refurb. As you would expect, the building measures (as opposed to the renewable technologies) turned out to be the most cost-effective. Taking the cost of 1kWh as produced by fossil fuels at a very conservative 5c, they found that it took only 1.7c of spend on wall insulation to save the cost of that kWh. Each 2c spent on roof insulation saved one kWh, while the equivalent figures for floor insulation and thermal bridges were 2.6c and 4.5c respectively.
To read further case studies of passive retrofit click here.
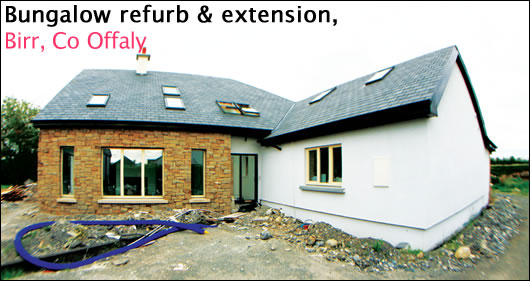
This 1970s bungalow provided Steve O’Leary with his refurbishment challenge. He is in the process of adding a large extension onto the original 1,000 square foot bungalow, and ensuring both are highly insulated and airtight. The plan, says O’Leary, was to minimise cost and waste, maximise value for money and do as much DIY as possible. “I want the house to be filled with light, maintain a stable temperature all year round, and favour insulation and cold bridge removal as an upfront cost rather than investing in heating systems that would need ongoing maintenance and eventual replacement.” O’Leary invested a huge amount of his own time researching and assisting on the build, and introduced a wide range of materials in order to deal with the differing conditions in the new and old parts of the house.
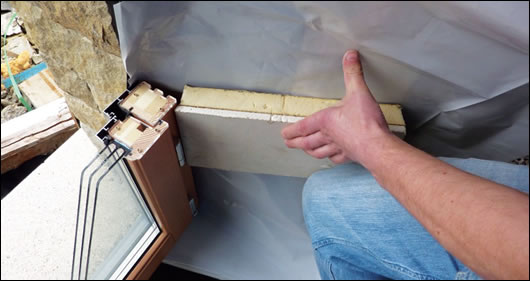
Working out a window detail
According to O’Leary, the involvement of Archie O’Donnell of Integrated Energy had a key influence on the energy efficient approach and the overall success of the build. “I got in contact with him through the Construct Ireland forum. He brought considerable industry knowledge of what worked and what didn’t work,” he says. “A lot of people try to go it alone and turn their nose up on paying someone to advise them on insulation and energy efficiency, but I think it was money well spent.”
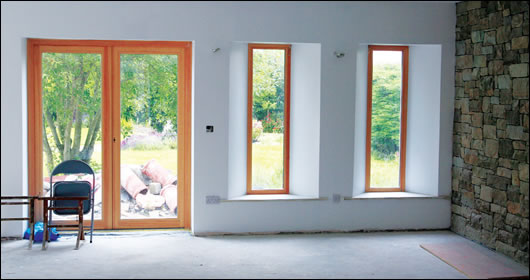
Triple-glazed Unilux windows and doors
He also relied heavily on carpenter/roofer Andrew Griffin on site. “He almost became a co-project manager and he was an invaluable source of contacts and expertise,” said O’Leary.
Training was one of the central elements of the project. “Engineer Hugh O’Rourke of Thor Designs in Birr and I visited Liam Keating’s (of Keating Insulation) low energy 200mm cavity wall house in Wexford to look at structural issues, together with issues such as window installation and cavity closing. Hugh, Andrew Griffin and I attended the one day Siga airtightness course so all of us were up to speed on that. For €50 including lunch, it was a bargain. Later in the build I attended an Itho one day heat recovery ventilation installers course in the UK, and afterwards I installed the Itho unit myself.” PHPP calculations are showing a heat energy load of 25kWh/m2/yr, right on the Enerphit target.
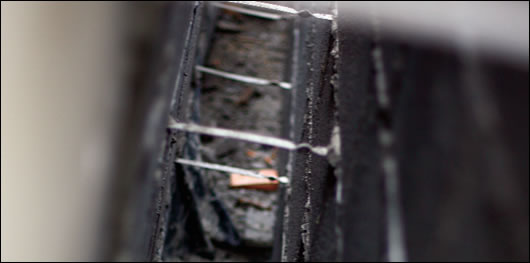
225mm cavity walls with stainless steel ties
Selected project details
Client: Steve O’Leary
Energy consultant: Integrated Energy
Roofing contractor/carpentry: Andrew Griffin
External insulation system: Powerwall
External insulation applicatoe: Paul Cahalan Plastering
Thermal blocks: Quinn Lite
Cavity insulation: Eurobead
Natural insulation: Gutex
Airtightness tapes: Ecological Building Systems /Isover /Siga
Roof lights: Unilux
Windows: Velux
Heat recovery ventilation: Itho
Ssolar: Ecologics
Project overview:
Building type : 238 square metre detached two storey timber frame house. Extension of small bungalow to 400m2 detached block built two storey house
Location: Birr, Co Offaly
Completion date: September 2011
Budget: pending
Space heating demand (PHPP): 23kWh/m2/yr
Heat load (PHPP): 14 W/m2
BER: pending
Airtightness: approximately 1.5 air changes per hour when tested two months ago, next test expected to get below 1 air change per hour
Ground floor: 300mm EPS strip foundation with aerated Quinn Lite concrete blocks on inner leaf up to one block over ground floor and cut for angled window reveals.
Extension walls: 225mm block cavity wall pumped with EPS platinum beads and robust Vartry Engineering stainless steel wall ties on extension. 0.16 U value W/m2K
Original house walls: pumped 90mm cavity wall bonded bead insulation and externally insulated with 150mm EPS.
U-value: 0.14 W/m2K
Roof: Nova black Brazilian slates externally on 50x35 battens/counter battens, followed underneath by breathable roofing underlay, 60mm Gutex soft board, 9 inch joists fully filled with cellulose insulation, 15mm taped & sealed OSB, 100 mm insulated service cavity where space allowed, 12.5mm plasterboard ceiling.
U-value: 0.14 W/m2k
Windows: triple-glazed Unilux alu-clad pine with argon filling and PIR thermal break built in to frame. Windows fitted flush with exterior wall on old part of house so EWI forms new reveal to minimise cold bridging.
Overall U-value: 0.78 W/m2K
Heating system: original 75% efficient grant oil boiler, did not upgrade as heating load was so low. Clearview Pioneer 400 stove 5kw with back boiler. Zoned radiators with full thermostatic control. 300L hot water tank and 60 evacuated tube solar array
Ventilation: Itho HRU 4 heat recovery ventilation system
Green materials: cellulose insulation, Gutex soft board
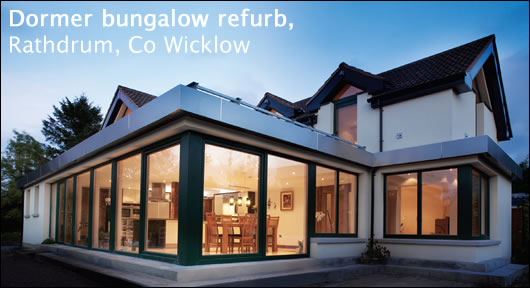
Randy Ralston and Mel Cronin were about a third of the way through the refurbishment of their 1970s dormer bungalow in Rathdrum when they decided that they would try for passive. They began their project before Enerphit was established, which meant that trying for passive involved aiming for the Passive House Institute’s exacting new build targets – annual heating demand no higher than 15 Kwh/m2/yr and airtightness of under 0.6 ACH. Though they just missed these targets, the project remains an exceptional refurb. A heat energy load of 17.9 kWh/m2/yr and an air change rate of 0.92 ACH comes well within Enerphit parameters. Moreover, the addition of renewable technologies including a wind turbine and PV panels mean that the house, which was featured previously in Construct Ireland, is actually a net energy contributor, with a BER rating well in excess of the A1 threshold. Earlier this year, the project was a runner up in the Isover Energy Efficiency awards.
Achieving airtightness is one of the biggest challenges faced in a passive refurb. A rate of 0.92 ACH took a huge effort. "It's true we did get a bit carried away with ourselves when we realised that actually going full passive seemed within our grasp," Ralston told Construct Ireland in September 2010. "At one point we completely downed tools and spent two weeks with a team of six people doing nothing but searching for and sealing air leaks using the blower door, air pens, smoke machines and even incense."
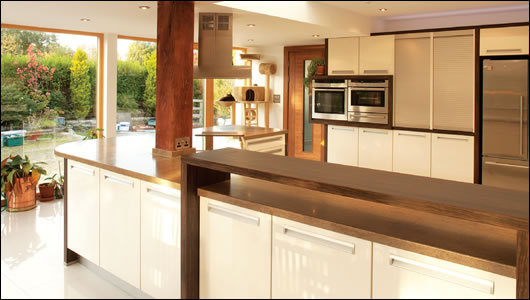
"We invented ways of sealing the recessed lighting using silicone rings, and used gargantuan amounts of fireproof acoustic mastic." He said. "We even had representatives from the various airtightness materials manufacturers visit the site during that time to advise us how we could improve and they could offer nothing, saying we were doing ‘everything right’”.
Selected project details
Clients: Randy Ralston & Mel Cronin
Architectural & passive house consultant: Archie O’Donnell
BER assessment: Energy Matters
M&E: Robert Hassey Electrical Ltd
External insulation: Aerobord
Service cavity insulation: Rockwool
Cavity wall insulation: Warmfill
Blown cellulose insulation: Ecocel
Insulated foundation system: Viking House
Windows & doors: Ecoglaze Ireland
Roof windows: Tradecraft
Airtightness products and Gutex insulation: Ecological Building Systems
OSB board: Medite Smartply
Solar evacuated tubes, air-source heat pump & buffer tank: C-MC Energy
Rainwater harvesting: Rainharvesting Ireland
Wind turbine: Sunstream Energy
Solar PV & Emma controller: Coolpower
Heat recovery ventilation: MTD Solutions
Project overview:
Building type : 1970s detached two-storey house gutted and extended to 339 square metre house
Location: Rathdrum, Co Wicklow
Completion date: December 2010
Space heating demand (PHPP):
17.9kWh/m2/yr
Heat load (PHPP): 12w/m2
Airtightness: 0.92 air changes per hour
Enerphit certification: pending
BER: Upgraded from an F to an A1 rating
Ground floor: existing concrete floors dug out and Viking House insulated foundations installed with 300mm of EPS.
U-value: 0.12 W/m2K
Extension walls: timber frame walls – 140mm & 90mm twin-wall studs filled with cellulose, with 15mm of pro clima tapes sealed to OSB inside & outside, 200mm of EPS insulation externally & a 100mm Rockwool-filled service cavity internally lined with Intello vapour check & Fermacell board.
U-value: 0.11 W/m2K.
Original house walls: the cavity walls were pump-filled with bonded-bead & externally insulated with 200mm of EPS, then lined internally with Intello vapour check, followed by Fermacell board.
U-value: 0.14 W/m2K
Extension flat roof:150mm EPS insulation under a fibreglass roof membrane, followed underneath by a plywood deck, nine inches of cellulose insulation, taped & sealed OSB as vapour control layer, & 100mm of Rockwool in the service cavity below.
U-value: 0.13 W/m2K
Existing roof: 60mm of Gutex soft board placed under the roof tiles, cellulose insulation between the rafters & a 100mm Rockwool-insulated service cavity underneath. U–value: 0.13 W/m2K
Windows: triple-glazed Internorm windows replaced single glazing throughout. Edition & Edition 4 models were specified — the latter includes a controllable blind between the triple-glazing & a fourth separate outer pane. Both models are timber alu-clad with argon fill.
The Edition units have a U-value of 0.86 W/m2K overall, while the Edition 4 has an overall U-value of 0.8 W/m2K with the blinds rolled & 0.7 W/m2K unrolled
Roof lights: timber-aluclad, krypton-filled Fakro units.
Overall U-value: 0.94 W/m2K
Heating system: 120 solar evacuated tubes meet 70% of domestic hot water requirements & supply underfloor heating, backed up by an Emmeti air-to-water heat pump with a COP of up to 4.49 based on Eurovent conditions (air in at 7/6C, water out at 30/35C). Hot water is stored in a three coil Akvaterm 2,000L insulated tank.
U-value: 0.22 W/m2K
Ventilation: MTD ERV 500 heat recovery ventilation system
Green materials: cellulose insulation, Gutex soft board
Electricity: a 2.9kW solar PV array consisting of 14 Sanyo HIT panels & EMMA controller paired with a Skystream 3.7 wind turbine rated at 2.4 KW in wind speeds of 12 metres per second (m/s), equivalent to 27mph
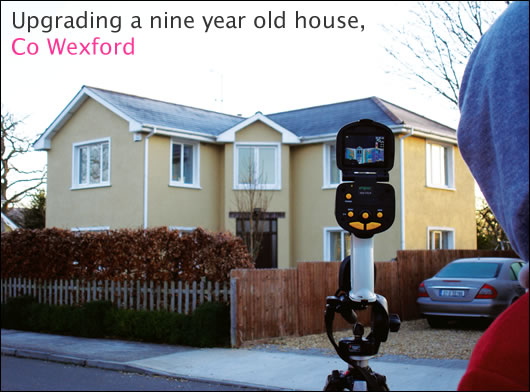
OLS architects in Co Wexford are overseeing an Enerphit refurbishment of a two-storey house located in a built up area in Castlebridge, Co Wexford. The usual challenges are in evidence here; poor orientation, window distribution and overshading are all issues, mitigated somewhat by the house’s relatively modest size. While the client wants the refurb to deliver a comfortable home that’s cheap to heat, he also needs to address very serious damp issues. Cathal O’Leary of OLS says that the house is full of mould. “There’s mould all around the perimeter of every window. Upstairs, there’s mould where the first floor walls meet the ceilings. The whole place is terrible really. You pull back a chair and there’s mould growth in the corner.”
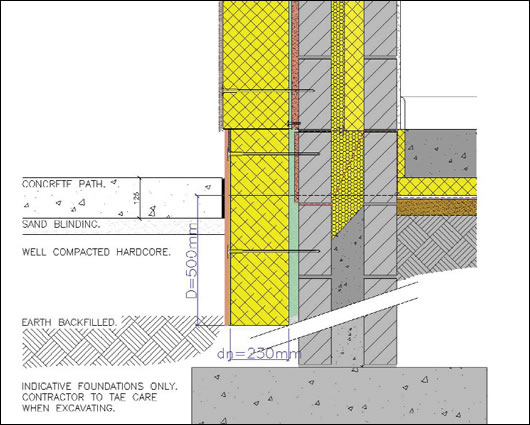
OLS’s sub-floor level external insulation is designed to solve the mould problem
The Passive House Institute’s Enerphit criteria for refurbished buildings deals specifically with this issue: “Without exception, all standard sections and connection details must be planned and implemented so that there is no excessive moisture accumulation on the interior surfaces or in the building component structure.”
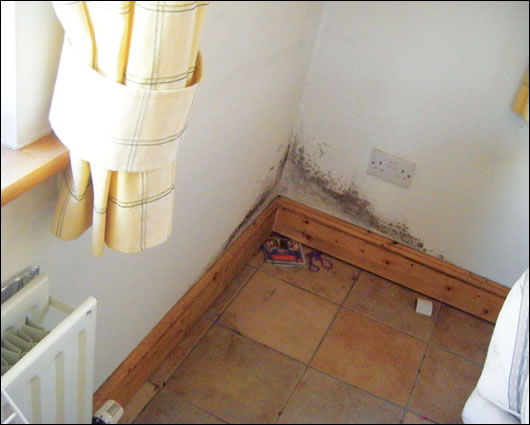
Cathal O’Leary says that the initial thermal bridge and condensation risk analysis calculations for the house showed that the internal surface temperature in the mould affected areas was around 10 or 11C. “The rule of thumb is if the internal temperature drops below 12C, you have a condensation or dew point, which leads to moisture and mould growth.” Proposed thermal bridge details will bring those temperatures up to around 17/18C. This, together with better ventilation and insulation will combine to provide the right conditions to remove interstitial and surface condensation that’s causing the problem. “This house was built in 2002,” says O’Leary. “It’s a shocking indictment of the housing boom and the supposed good times.”
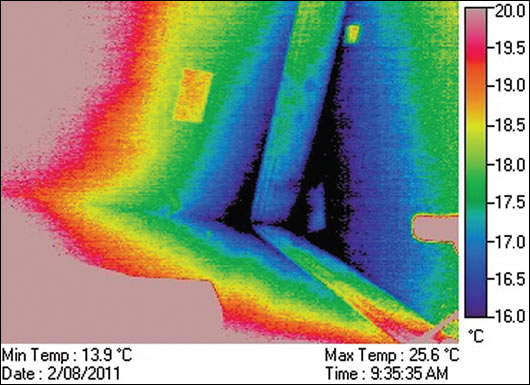
The survey revealed significant cold spots at skirting level
Selected project details
Client: Brian Meaney & Karen Daly
Architect: OLS Architects
Main contractor: Creedon Construction
Heating & ventilation: Heat Doc
Window supplier: Munster Joinery
Airtightness testing & thermal imaging: Greenbuild
Specialist external insulation system: Smart Facades
Project overview:
Building type : 150 square metre detached two-storey existing house, constructed in 2003
Existing construction: traditional partially filled cavity wall blockwork construction, which was filled with bead insulation by the owners in 2005. Traditional pitched cut roof with slate finish.
Location: Castlebridge, Co Wexford
Completion date: November 2011
Enerphit certification: pre-submission
Space heating demand (PHPP): 25 kWh/ m2/yr
Heat load (PHPP): 10 W/m2
Airtightness: target of one air change per hour at 50 pascals pressure. An airtightness test was carried out on the existing house with a result of 4.59 air changes per hour at 50 pascals pressure
BER: pending
Ground floor: existing 150mm concrete floor slab, with 55mm expanded polystyrene insulation, on radon barrier, on sand blinding, on compacted hardcore.
U-value: 0.62 W/m2K
Block walls: 10mm Parex Lanko render to 200mm EPS Aerobord external insulation, to existing rendered blockwork fully filled insulated cavity wall.
U-value: 0.11 W/m2K
Brick walls: 10mm Parex render to 200mm EPS Aerobord external insulation, to parge coat, to existing brick outer face of fully filled insulated cavity wall.
U-value: 0.11 W/m2K
Roof: Existing slated traditional cut roof, insulated at ceiling level, with foil backed plasterboard to ceiling. New Intello airtight breather membrane applied to existing ceilings, with new 12.5mm Gypsum plasterboard ceiling with skim finish. 200mm additional mineral wool insulation added to existing ceiling insulation.
U-value: 0.09 W/m2K
Windows: new Munster Joinery triple-glazed PassiV Future Proof certified windows, argon filling, with an overall U-value of 0.78 W/m2K
Heating system: Danfoss DHP-AQ 6.2kw air to water with a COP of 4,0 (according to EN14511 – including circulation pumps) & Maxi unit 180L TWS technology hot water cylinder providing faster, hotter water.
The heat pump operates on a floating condensing control and will be coupled to the existing radiator system. Heating system by Heat Doc Ltd
Ventilation: Zehnder Comfoair CA350B heat recovery ventilation system — Passive House Institute certified ventilation system by Heat Doc Ltd
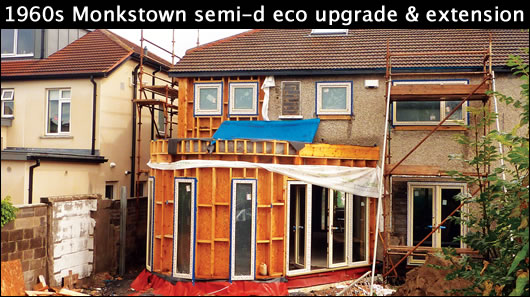
This Enerphit refurbishment and extension of a two-storey semi-d in Monkstown, Co Dublin started out with green upgrade intentions under SEAI’s now defunct Low Carbon Homes programme. “The client wanted an exemplar building,” architect Joseph Little explains. “She wanted a building that was highly energy efficient and highly sustainable.” Following the demise of the short-lived grant programme midway through the project, it was decided instead to go the Enerphit route. While the building methods essentially remained the same as proposed, the change of focus highlights significant differences between low carbon and passive house approaches.
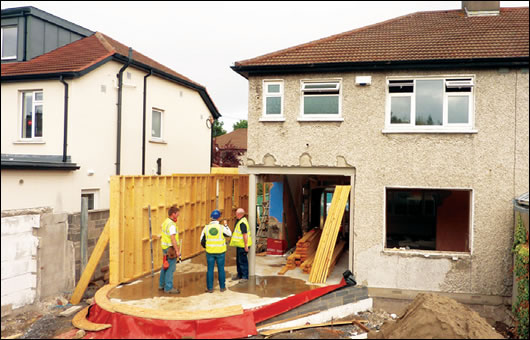
“The Low Carbon Homes programme focused on U-values,” says Little. “We had low thermal bridge and excellent U-values but we realised when we went passive house that we had to have no thermal bridges – as measured from the outside – and excellent U-values.” Little’s approach also involved the specification of low carbon products, though Enerphit does not impose any such restrictions on materials. The Enerphit approach also introduced tough airtightness requirements to the project. “We were already going to an airtightness of one air change per hour [at 50 pascals pressure], but we now need to get to an airtightness below that,” he explains.
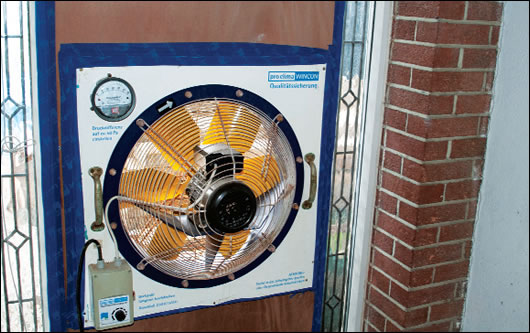
Proclima Wincon fan to help quality control on site prior to blower door testing
The most significant changes were those imposed by the more exacting approach to thermal bridges. The original plan, for example, had involved retaining floor joists and slinging insulation between them using a breather membrane. But with a passive approach, the timber becomes a weak thermal link, and the design team found that the only way of effectively dealing with the thermal bridge was to completely remove the floor and install EPS insulation beneath a new slab. While this approach involved increased waste, Little explains, it did save on labour.
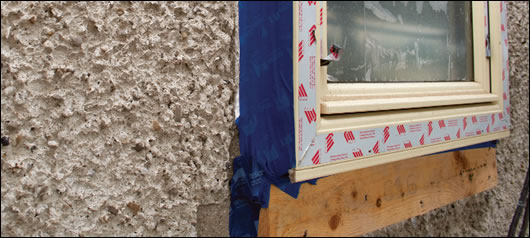
Munster Joinery Future Proof PassiV windows sit proud of the wall to maintain a complete insulation layer
Selected project details
Client: Pauline Conway
Architects: Joseph Little Architects
Civil / structural engineers: Malone O'Regan
Energy consultant: Ann-Marie Fallon
Main contractor: Bourke Builders
Quantity surveyors: Walsh Associates
Mechanical contractor: Ollie McPhillips
Airtightness tester: Greenbuild
External insulation: Diffutherm /Parex Lahabra
Roof insulation: Warmcel
Floor insulation: Kingspan Aerobord
Windows and doors: Munster Joinery
Airtightness products: Ecological Building Systems
Solar thermal supplier: Kingspan Renewables
Radiator supplier: Solo
Heat recovery ventilation: Pure Renewable Energy
Rainwater harvesting: Reedbeds Ireland
Water conserving fittings: Sandringham Fittings
GGBS: Ecocem
Project overview:
Building type : 145.6m2 semi-detached house from 1960. Enerphit refurbishment with two-storey side and single-storey rear extension
Location: Monkstown, Co Dublin
Completion date: November 2011
Enerphit certification: pre-submission
Space heating demand (PHPP):
22 kWh/m2/yr
Heat load (PHPP): 10 W/m2
Airtightness: test pending – target of 0.6-1.0 ACH
BER: pending, estimated jump from F to A3 rating
Ground floor: 300mm Aerobord EPS foundation. U-value: 0.11 W/m2K in extension and existing floor. A unique point thermal load issue at a column was successfully thermally broken with Foamglas blocks
Existing walls: 50mm insulated tissue backed PIR board, inside 300 mm cavity wall filled at junctions of joists etc for airtightness, with existing render removed and 150mm EPS Parex Lanko insulation and mineral render finish, with brick slip on front elevation.
U-value: 0.12 W/m2K
New timber frame: open panel construction - 50mm insulated service cavity on taped T3 standard 18mm OSB board, with a 220mm timber frame filled with cellulose with 80mm diffutherm insulation system externally
U-value: 0.13 W/m2K
Main roof: insulated on joists 350mm blown cellulose
U-value: 0.12 W/m2K
Flat roof: open panel roof; 50mm insulated service cavity on vapour membrane with 18mm OSB with 250mm joist and cellulose insulation on 25mm woodfibre sheathing board, with 50 mm ventilated air gap on furring pieces for fall with Solitex membrane on double layer of marine plywood and double butyl layer finish. U-value: 0.13 W/m2K
Windows: Munster Joinery Future Proof PassiV certified windows. U-value: 0.85 W/m2K
Heating system: the primary heating involves post-heating the supply air on MVHR, with a modulating gas boiler and three rads (and two towel rads) as back-up heating if required. Domestic hot water met with 250L 100mm factory insulated cylinder, triple coil (for future heat source if needed) and Kingspan Thermomax solar vacuum tubes supplying separate 300L domestic hot water tank
Ventilation: Paul Santos 370DC heat recovery ventilation system — Passive House Institute certified to have heat recovery rate of 84% / EN 308 certified efficiency of 92.7%
Green materials: recycled slate to match existing context, cellulose insulation in walls and attic, FSC certified timber frame extension, all timber furniture, kitchen and fit outs from PEFC certified sources, 60-70% GGBS cement
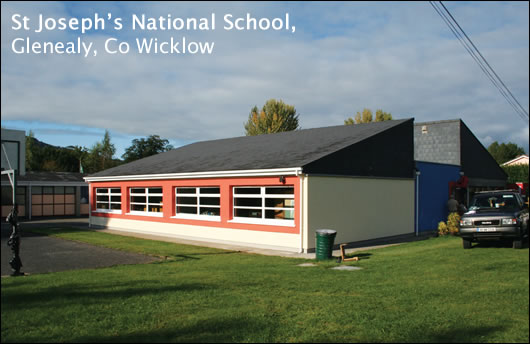
Acknowledging the particular challenges presented by retrofitting, there’s a lot more flexibility built into Enerphit certification. Hitting the space heating target of 25 kWh/m2/yr won’t be possible in all circumstances. But a form of certification is possible through the use of ‘passive house suitable components’. The thinking behind this is to encourage retrofitters to use the best possible materials when the budget simply won’t make the thresholds achievable. St Josephs National School in Glenealy, retrofitted by MosArt, falls into this category. Part funded by the Ballynagran Community Group and supplier donations from Isover, Kingspan Renewables and Munster Joinery, the design team had a budget just shy of €60,000. The key question therefore was how to deploy this money effectively.
“When we ran it through the PHPP software,” says Jill Noctor of MosArt, “doing different elements throughout the school didn’t have much of an impact on the overall energy performance, whereas if you concentrate on one block, you could make savings in that area.”
The design team chose two classrooms at the back of the school and concentrated their efforts there. The building fabric upgrades include replacing the existing single-glazed windows with triple-glazed passive standard windows from Munster Joinery. The cavity walls were pumped with blown bead insulation, while 70mm of insulation was fixed to the external face of the building. The result was not alone greatly reduced U-values, but it also gave the façade a fresher and more interesting appearance. The two classrooms were taken off the school heating system and are now heated by an air to water heat-pump. The heating load for this space has fallen by 50%. It’s hoped that as funds become available, the same approach will inform similar energy upgrades throughout the school.
Selected project details
Architect: MosArt
Main contractor: James Doran & Son
External insulation system: Saint Gobain Weber
Additional wall insulation: Isover Saint Gobain
Windows & doors: Munster Joinery
Heat pump supplier: Kingspan Renewables
Radiator supplier: Geostar Engineering
Project overview:
Building type : primary school
Location: Glenealy, County Wicklow.
Completion date: August 2011
Budget: €60,000 (including supplier contributions and fees)
Space heat demand of entire existing building (PHPP): 252 kWh/m2/yr
Space heat demand of retrofit area (back two classrooms & courtyard) as existing (PHPP): 159 kWh/ m2/yr
Space heat demand of retrofit area after retrofit works (PHPP): 81 kWh/ m2/yr
Heat load of entire existing building (PHPP): 127 W/m2
Heat load of retrofit area as existing (PHPP): 92 W/m2
Heat load of retrofit area after retrofit works (PHPP): 55 W/m2
Enerphit certification: will not be certified
BER: pending
Ground floor: existing concrete floor
Existing walls: 100mm Forticrete blockwork externally, 50mm ventilated cavity, 50mm Aerobord insulation, 100mm concrete blockwork, plaster and skim finish to internal.
U-value: 0.60 W/m2K
Upgraded walls: 70mm Kingspan phenolic insulation and render finish externally, 100mm Forticrete blockwork, 50mm blown bead insulation into existing cavity, 50mm existing Aeroboard insulation, 100mm concrete blockwork, plaster and skim finish to internal.
U-value: 0.171 W/m2K
Existing roof: Roof slates to sloped areas and torch on felt to flat roof areas externally. 150mm mineral wool insulation on the flat between roof joists and a combination of suspended ceiling tiles or plasterboard ceiling internally.
U-value: 0.333 W/m2K
Existing windows: single-glazed, timber windows and doors. Overall approximate U-value: 3.50 W/m2K
Upgraded replacement windows: Munster Joinery triple-glazed Future Proof PassiV windows and doors
Overall U-value of 0.80 W/m2K
Existing heating system: oil condenser boiler and radiators throughout entire school
Upgraded heating system to retrofit area only: Kingspan Aeromax Plus air source heat pump fitted with Thermofon low temperature radiators to retrofit area, existing system as a backup if required
Ventilation: natural ventilation retained throughout