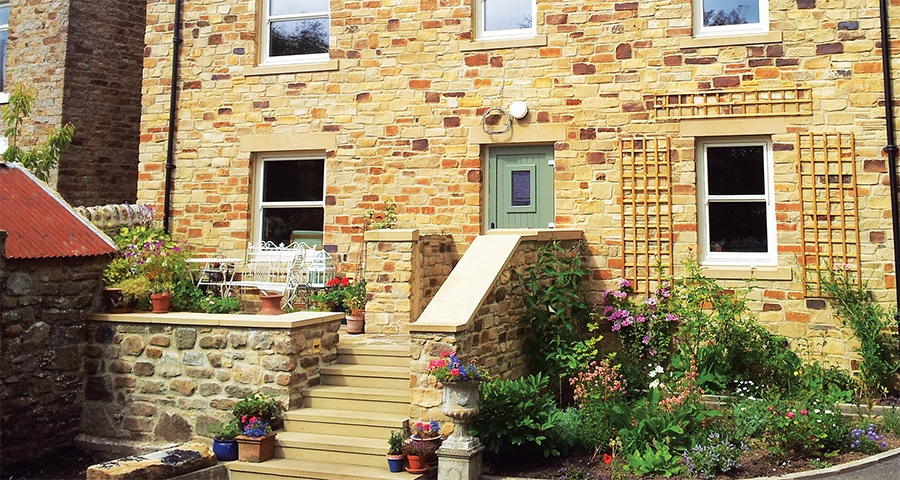
- Feature
- Posted
Rural Durham home mixes thoughtful design and passive aims
Architectural technician Phillip Newbold overcame strict planning rules and a tight budget to build his sensitively designed, super low energy home in an area of outstanding natural beauty.
Architectural technician Philip Newbold of New Bold Design describes how he overcome strict planning rules and a tight budget to build his sensitively designed, super low energy home in an area of outstanding natural beauty.
My wife Joy and I sold our leaky Victorian home in 2008 and started looking for a plot to build our own low-energy house. In 2011, shortly after I was made redundant from a senior associate’s job with a leading architecture practice in the north east, we found a plot in Upper Weardale with what we thought was detailed planning consent. In fact it turned out the planning consent had expired in 2009. The seller had to re-apply, but we finally secured ownership of the plot in January 2012 for £70,000.
The timber frame being erected
I had used some of my redundancy money to train as a passive house consultant and as we now had no significant income, we decided to use all the money we had to build a passive house, so that we would not have any major heating bills in future. We originally planned to build without a mortgage but in the end we needed £65,000 from the Ecology Building Society and £10,000 from the Bank of Mum and Dad just to make the house complete enough to live in. The total build cost so far is around £180,000.
The plot is 345 square metres and the village is in a conservation area on the river Wear. When we opened discussions with the plan- Rural Durham home mixes thoughtful design & passive aims ners on the 15 conditions, we found they were inflexible and not really interested in our aspirations to build a passive house. Thanks to draconian planning restrictions, out went any hope of being able to build a certified passive house. While I had hoped to build a more compact, cubic house, the planners insisted we conform to the Dales cottage vernacular of an L-shaped dwelling plus a lean-to extension.
Our new home is a two-storey detached house of 116 square metres (over two floors) with a non-habitable attic plant room and store. The ground floor comprises an open-plan dining hall and kitchen, lounge, WC, utility room and store. The first floor has a master bedroom, study bedroom, bathroom and WC, guest bedroom with en-suite shower and WC, and linen cupboard. The attic plant room and store houses the 250 litre hot water tank and the MVHR unit.
We started work in March 2012 and moved to a small, rented cottage next door to the plot. It didn’t stop raining (or snowing) for about 10 months, and 2012 turned out to be the wettest summer for 100 years.
Smartply OSB lines the internal face of the timber frame, with the joints sealed with Tescon airtightness tape
We cast the concrete floor slab over 450mm of EPS insulation in June. As the timber frame was erected, I inserted continuous Intello membrane with taped joints around the perimeter of the upper floors and roof in order to ensure good levels of airtightness. All the drain pipes and services penetrations through the floor slab and external walls were fitted with airtight grommets.
The planners had initially insisted on double-glazed, sliding sash windows, but I was able to persuade them to accept triple-glazed, mock-sash, tiltand- turn casements with a U-value of 0.9. By September 2012 the roof structure was watertight, but just as the rain turned to snow, the windows and doors arrived from Lithuania, some weighing up to 70kg each. I applied special airtightness tapes internally and externally to all the frames before getting a local joiner to help install them. The same joiner helped me to line the internal face of the timber frame with Medite Smartply 18mm OSB 3. We then primed and taped the OSB joints with Tescon tape using a heat-gun to dry the joints.
I also taped the joint between the OSB and the ground floor slab. When all the airtightness measures were complete, the blower door test gave a result of 0.59 air changes per hour. Using local stone, the stonemason managed to get the external stonework up to the ground floor window cills before the first serious snow arrived in November. As the coldest and longest winter for 50 years followed the wettest summer, progress on the stonework almost ground to a halt.
The internal OSB was lined with battens to create a 50mm services zone for pipes and wiring. After all the services had been installed, the void was filled with 50mm PUR insulation board before a final lining of 12.5mm plasterboard and skim was added. In spite of incomplete stonework, no stove and no slates on the roof, we moved into the house in February 2013. We then installed a room-sealed wood-burning stove in the lounge with a back boiler that provides up to 8.5kW to hot water in the winter and also heats towel rails in the bathrooms and a heat-leak radiator in the linen cupboard.
After all services had been installed, the void was filled with 50mm PUR insulation board
We have no central heating system beyond the wood burning boiler stove and the house is maintained at a minimum of 20C. Solar thermal panels provide most of the hot water in the summer, topped up with the immersion heater, assisted by the output from our 1.5kW solar PV array.
We discovered that we could not get the feed in tariff for the solar PV until we had an energy performance certificate. But we could not get an EPC until we had a completion certificate from the building control officer. And we could not get the completion certificate until the stove flue, stonework, roof slates, electrics and rainwater goods were finished. This was finally achieved in October 2013, with the EPC giving the house an A rating.
As the house nears completion and we have occupied our new home for over a year, we are beginning to appreciate what all our hard work has achieved. We only need the stove burning on winter evenings and have no other fuel bills apart from electricity which is currently running at £35 a month, excluding the feed in tariff. The silent MVHR system recycles the heat generated inside the house while providing filtered, fresh air. There have been no overheating problems so far.
Despite costing around £250,000, the house is only worth £225,000 according to the Royal Institute of Chartered Surveyors, so building a one-off house like this in the UK is still too expensive. The clever components have to be imported and our workforce is just not good enough. The hybrid heating and hot water system is difficult to control and both solar systems have had technical failures.
A continuous Intello membrane with taped joints around the perimeter of the roof ensures good levels of airtightness
But we have managed to self-build a Band A home to the cusp of passive house and have a warm, comfortable home in which to live and work without any significant heating bills. More importantly, we have proved that it is possible to build a real low-energy home in a conservation area, and an area of outstanding natural beauty (AONB), which fits in with the local architecture while addressing fuel poverty issues head-on. One day, all houses will have to be built like this.
Greendale Cottage was recently awarded the price for best individual new home at the 2014 Northern LABC Building Excellence Awards, and will go forward to November’s national awards in London.
Selected project details
Design & project management: New Bold Design
Client: Philip & Joy Newbold
Timber frame: Swift Timber Homes
Windows & doors/MVHR: Green Building Store
Airtightness products: Pro Clima
Solar thermal: Baxi
Solar PV: Panasonic
Mechanical contractor: Pure Energy Systems
Airtightness tester: Apex Acoustics
Cellulose Insulation: PYC Insulations
PUR insulation: Quinn-therm
Floor insulation: Springvale
Basalt wall ties: Ancon
Stone cladding: Dunhouse Quarry Co
Wood burning stove: Stoves Online
Towel radiators: Best Bathrooms
Reclaimed roof slates: Reclamation Supplies
Finance: Ecology Building Society
Additional info
Building type: detached 116 sqm three-bedroom, two-storey house with additional 48 sqm attic plant room and store.
Location: Ireshopeburn, County Durham
Completion date: June 2013
Budget: £250,000 (£70,000 for the site and £180,000 for construction)
Passive house certification: not certified
Space heating demand (SAP)*: 1014 kWh/year
Water heating demand (SAP): 2394 kWh/year
Primary energy demand (SAP): 16 kWh/m2/year
Airtightness (at 50 Pascals): 0.59 ACH
Energy performance certificate (EPC): A 97
Thermal bridging: Inner leaf of substructure walls in Durox Supabloc Aircrete blocks to minimise thermal bridging from the ground-bearing foundations into self-supporting concrete floor slab. Doublestud timber frame has a minimum number of small connecting strips of OSB between the inner and outer studs. Internal service zone battens are at right-angles to the frame studs to minimise thermal bridging. 150mm wide x 50mm thick PUR insulation around all openings between outer skin of stone and timber frame. All details are bespoke designs developed by New Bold Design in consultation with Swift Timber Homes.
Ground floor: 200mm thick self-supporting, reinforced concrete floor slab on 450mm Springvale EPS. Slab supported at the perimeter on 140mm inner leaf of Durox Supabloc aircrete blocks on reinforced concrete strip foundations. 200mm Springvale Platinum EPS insulation in a fully-filled cavity with Teplo-Tie basalt wall ties and outer leaf (to support stonework) of substructure perimeter walls in 100mm 7N solid concrete blocks. Radon barrier under insulation with lapped and taped joints. U-value: 0.08
Walls: 100mm thick, random, natural, local stone externally, followed inside by 50mm ventilated cavity, Tyvek membrane on 9mm OSB, 90mm outer studs, 50mm space, 140mm inner studs (studs at 600mm centres), 18mm Smartply OSB (airtightness layer) with joints sealed and taped with Tescon primer and tape. 280mm void filled after erection with Warmcel cellulose fibre insulation. Inner and outer studs connected top, centre and bottom on each storey with small 9mm OSB bridging pieces. 50mm internal service void for pipes & cables created using 50 x 38mm horizontal battens, filled with 50mm Quinn-therm PUR insulation between battens and finished inside with 12.5mm Gyproc Duplex plasterboard, skim coat and emulsion paint finish. U-value 0.12
Roof: Reclaimed natural grey slates externally on 50 x 25mm battens/counter battens, on Tyvek breathable roofing underlay, on 9mm OSB, on 300mm I-beams at 600mm centres, on 18mm Smartply OSB (airtightness layer) with joints sealed and taped with Tescon primer and tape. 300mm void filled after erection with Warmcel cellulose fibre insulation. 50mm internal service void for pipes & cables created using 50 x 38mm horizontal battens, filled with 50mm Quinn-therm PUR insulation between battens
and finished with 12.5mm Duplex plasterboard inside, skim coat and emulsion paint finish. U-value 0.12
Windows: Green Building Store Ecocontract mock sliding sash, triple-glazed, factory-finished, timber windows and external doors. Large, mock-sash windows on the south elevation and small, casement windows on the north, east and west elevations. Windows U-value: 0.9, external doors: 1.1
Heating system: Woodfire F12 room-sealed, wood burning boiler stove in the lounge providing a maximum of 8.5kW to hot water and 1.5kW to the room in the winter. Stove provides heat to towel rails in two bathrooms, a heat-leak radiator in the linen cupboard and a 250 litre dual-coil hot water tank in the attic. 4 sqm Baxi Solarflo solar thermal panel system on south-facing roof for water heating.
Ventilation: Paul Novus 300 MVHR system, PHI certified to have a heat recovery rate of 94%
Electricity: 9 sqm Panasonic solar photovoltaic array (six panels) with average annual output of 1.5kW
Green materials: Locally sourced stone cladding, outbuildings and boundary walls rebuilt using stone recycled from the site, roof slates sourced from a demolition in Newcastle. Scrap timber from the build used to heat the house for a full winter.
*Phil Newbold initially calculated the space heating demand to be 18/kW/m2/yr using PHPP, but soon after his computer
crashed and his PHPP file was lost. He was not aiming for passive house certification so decided not to start PHPP
calculations again. 50mm of PUR insulation was installed in the services zone of the roof and walls in lieu of 50mm
fibreglass on which his initial calculations were based.
Image gallery
Passive House Plus digital subscribers can view an exclusive image gallery for this article. Click here to view