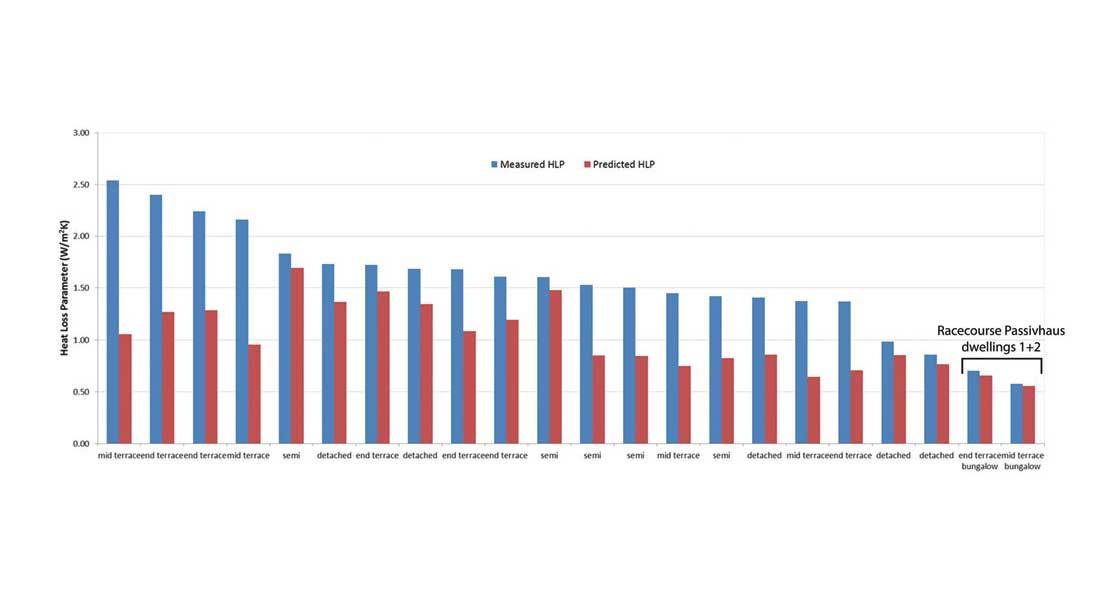
- Insight
- Posted
Bridging the building performance gap
Predicted energy usage seldom reflect actual consumption, whether in the case of typical stock or notionally low energy buildings. But how well does passive house turn theory into reality?
This article was originally published in issue 3 of Passive House Plus magazine. Want immediate access to all back issues and exclusive extra content? Click here to subscribe for as little as €10, or click here to receive the next issue free of charge
Over the last number of years research by Leeds Metropolitan University (Leeds Met) has repeatedly shown that new homes, including those built to UK building regulations and the Code for Sustainable Homes are performing much worse than expected. The researchers have consistently measured cases where the heat loss of the homes is 40 to 70% greater than predicted. They’ve observed that these performance issues arise from failures in the design, procurement and construction of buildings and that as energy performance standards become ever more demanding there is a tendency for this gap to increase. The performance gap is not restricted to the shores of the British Isles. Similar issues have been observed in Germany, Austria and Sweden.
It was concerns about the serious underperformance of supposedly low energy buildings that led Prof Wolfgang Feist to develop the Passivhaus standard (referred to later as ‘passive house’ at the editor’s request). But does the standard perform in practice?
Whilst first researching passive house I also became fascinated by research regarding thermal bypass and the impact that it can have upon the performance of the building fabric. These concerns led to two papers presented at the International Passive House Conference and UK Passivhaus Conference1. Awareness of thermal bypass has consistently underscored my approach, and that of a number of others, to the passive house standard.
As project architect and passive house designer for the Racecourse scheme by Gentoo I had the chance to test the theories that I’d learned about. Could I, along with the rest of the team, close the performance gap that has been observed elsewhere?
Leeds Met has recently performed co-heating tests on two of the twenty five passive house residences on the Racecourse Estate. I’m pleased to report that each result has demonstrated a very high level of correlation between the measured and predicted performance; within the accuracy of the test method. Figure one (below) shows results of coheating tests from Leeds Met database, with Racecourse homes on the right.
Figure one: results of coheating tests from Leeds Met database; Racecourse homes on the right
Is this a freak occurrence, or are similar results being achieved at other passive house developments? As it happens, further co-heating tests – by other organisations and institutions – have recently been conducted on three other passive house dwellings on different sites in the UK. Each has reported similar results. It was on the back of this success that I recently coauthored a paper with John Trinick of Warm and Dr David Johnston of Leeds Met that was presented at this year’s International Passive House Conference.
While I’m mindful that this is a rather limited dataset, and therefore can’t be considered statistically reliable, it’s the best evidence to date that the energy/carbon performance gap can be closed.
So what appears to be the secret?
It’s pretty a simple answer: dedication. It’s about ensuring that appropriate understanding and quality assurance mechanisms are in place throughout the entire supply chain for the duration of the project – from clients to architects and engineers to contractors and sub-trades. So, with my rose-tinted glasses on, it would appear that the passive house standard – when complimented by suitable attention to thermal bypass – has what it takes to deliver building fabric that performs.
This is great news, but does it mean we can relax? Let’s step back for a moment and borrow a few words from Dana Meadows, author of Thinking in Systems and co-author of the Limits to Growth:
"Ideally we would have the mental flexibility to find the appropriate boundary for thinking about each problem. We are rarely that flexible. We get attached to the boundaries our minds happen to be accustomed to.....
......It is a great art to remember that boundaries are of our own making, and that they can and should be reconsidered for each new discussion, problem, or purpose. It's a challenge to stay creative enough to drop the boundaries that worked for the last problem and to find the most appropriate set of boundaries for the next question. It's also a necessity, if problems are to be solved well."
Even if we can replicate the apparent success of projects like the Racecourse homes, we still have a long way to go before closing the performance gap. Why? Because so far I’ve left out the people who use and occupy the buildings! Buildings are what economists call experience goods; the characteristics, such as quality or price, are hard to appreciate until they’re used, experienced or “consumed.” In my view the passive house standard succeeds because it addresses qualitative issues that directly relate to the end user – the ultimate consumer. Thermal and acoustic comfort and minimised energy bills would be typical examples of value, as may be the satisfaction of knowing that the carbon emissions from the home are being minimised.
With regard to comfort, it’s worth noting that the passive house standard is resilient to “comfort take.”
The CEPHEUS study recorded indoor temperatures for more than 100 passive house homes; the lower range of average household indoor winter temperatures was 17C whilst the upper average was closer to 25C. The mean indoor temperature selected by households was 21.4C; some 1.4C higher than the assumed design temperature of 20C used by the passive house design standard. The resulting increase in energy demand doesn’t appear to destabilise the passive house standard itself.
For instance, figure two shows that the measured space heating energy demand in some homes is three times greater than the design target – the energy demand is nearer to 45 than 15 kWh/m2/yr.
Figure two: a collation of measured energy consumption for 228 certified passive house dwellings
Does this mean that the standard fails to deliver the stated energy performance? If we analyse the dataset more closely we find that the mean energy demand for space heating is 16.95 kWh/m2/yr.
It’s important to recognise that the energy demand for the homes represented in figure two was recorded primarily within the first year of use – when the buildings were still drying out.
This process has been found to increase the energy demand by about 1.5 kWh/m2/yr compared to future years. If we correct for this drying out, we find that the adjusted median energy demand for space heating can be said to be about 15 kWh/m2/yr. However even an additional 5 kWh/m2/yr equates to only £0.24/m2 (based upon natural gas at £0.048/kWh). We must also remember limits to the accuracy of measurement.
In the past Prof Feist has confirmed that it isn’t economical to deliver greater accuracy absolute than the range of +/-3 kWh/m2/yr; so it’s reasonable to expect that some latitude, one way or another, may be expected.
So how does the passive house standard deliver such resilience against the variable demands of the end user? First and foremost the Passive House Planning Package, the core design tool for passive house design, is built upon a robust set of assumptions that have been tested and verified through monitored building performance. Compared to dynamic analysis tools PHPP is relatively simple, thereby reducing design risk by requiring less data input. It’s further simplified by relying upon a number of design parameters such as the use of external dimensions. This simple change in geometric accounting procedure means that thermal bridging calculations may be avoided provided that the continuity of the insulation is suitably maintained. This saves both time and expense whilst also creating design tolerance due to the tendency for external dimensions to overestimate heat losses.
The high standards of airtightness required by the passive house standard are beneficial in several ways. Firstly, drafts are minimised to such an extent that, for the same standard of comfort, the temperature of a room may be reduced. Secondly, airtightness helps to ensure that the balanced ventilation system performs its function with near optimal effectiveness, which serves to ensure that excellent indoor air quality may be achieved. Also a tight building with controlled ventilation has a more predictable energy use than a draughty one with random window ventilation – another factor in closing the gap between theory and practice.
The use of heat recovery is a sensible addition to the provision of a balanced ventilation system. This not only serves to minimise energy demand and carbon emissions but also, and perhaps most crucially, helps to maintain draught free thermal comfort – even in the depths of the winter. The acoustic standards required by the passive house standard also act to preserve indoor air quality and energy saving as people are far less likely to turn the ventilation system down to a lower setting due to noise. This package of measures reduces the need for occupants to open windows, though they are free to do so, and consequently helps to minimise energy demand.
Whilst there’s evidence from the continent that suggests that passive buildings do deliver the expected energy efficiency when occupied, and that occupants are generally satisfied, there are still many lessons that we need to learn before we can say that we’ve closed the performance gap. The reason for this is that building performance evaluations – on a range of building types and to a range of standards– have, time and again, highlighted chronic low level failures that can have an impact upon health and wellbeing, energy use and carbon emissions.
Current performance gaps for new buildings that regularly arise during design and construction processes may be regularly found in areas such as:
- Domestic hot water (design, specification and energy accountancy); the AECB water standards are a good start;
- lighting; visual quality, views, illuminance, luminance ratios, reflection, spatial geometry, finishes, glare, lighting quality, natural daylight, luminaires, controls, maintenance;
- fan power; usage and energy demand;
- equipment and appliances; usage, energy demand and impact upon cooling loads;
- overheating (risks and mitigation); comfort thresholds, complex interactions between comfort thresholds and other conditions (such as the impact of external noise upon window opening), suitable and practical cooling load reduction strategies, etc.;
- the functionality and usability of controls, equipment and interfaces; simple and intelligible equipment that offers appropriate feedback/response to the user;
- duct cleanliness; there are no protocols readily available for use by the building contractor, the client’s agent or building control to determine appropriate cleanliness (how clean is clean enough?) Without such guidance health and wellbeing can be compromised;
- acoustics: Noise arising from natural or mechanical ventilation strategies (the Passive House standard does impose requirements for mechanical systems);
- hand over, user guides and training; intelligibility, practicality, suitability, relevance; purchase by a new owner perhaps years after the building was built – how will they be trained and informed?
- maintenance of ventilation systems; suitability of education, training, warning and notification.
These performance gaps are not “passive house problems” but issues that the whole industry must engage with. On the basis of people’s willingness to engage with knowledge sharing events, such as open days and conferences, and to undertake energy audits and post occupancy evaluation, I believe the passive house community is well positioned to engage with addressing many ailments affecting building performance and the building industry at large. Feedback – and feedforward – processes really need to become routine and instituted within all working practice.
References
Ebel W., Großklos M., Knissel J., Loga T., Müller K. (2003) Wohnen in Passiv- und Niedrigenergiehäusern – Eine vergleichende Analyse der Nutzungsfaktoren am Beispiel der „Gartenhofsiedlung Lummerlund“ in Wiesbaden-Dotzheim, Endbericht / Energie; Institut Wohnen und Umwelt; Darmstadt. http://www.iwu.de/fileadmin/user_upload/dateien/energie/neh_ph/endbericht_ph-wiesbaden.pdf (last accessed on 18/05/2013)
Wolfgang Feist (1997) “Passivhaus Darmstadt-Kranichstein - Planung, Bau, Ergebnisse”, Fachinformation PHI 1997/4, 1. Auflage, 16 Seiten
Feist W., Peper S., Kah O., von Oesen M. (2005) Climate Neutral Passive House Estate in HannoverKronsberg: Construction and Measurement Results, PEP Project Information No. 1. http://www.passiv.de/old/07_eng/PEP/PEP-Info1_Kronsberg_150dpi.pdf (last accessed on 18/05/2013)
Peper S., Feist W., Pfluger R. (2004) Ein nordorientiertes Passivhaus Messtechnische Untersuchung und Auswertung von 19 Wohnungen im Passivhaus-Standard in Frankfurt-Bockenheim, Grempstraße Passivhaus "Wohnen bei St. Jakob", Darmstadt. http://www.passivhaustagung.de/Passivhaus_D/pdf/PH_St.Jakob_www.pdf (last accessed on 18/05/2013)
Peper S., Schnieders J., Feist W. (2005) Mehrgeschoss-Passivhaus Hamburg Pinnasberg, Darmstadt. http://passiv.de/downloads/05_mehrfamilienhaus_hamburg.pdf (last accessed on 18/05/2013)
Reiss J. and Erhorn H. (2003) Messtechnische Validierung des Energiekonzeptes einer großtechnisch umgesetzten Passivhausentwicklung in Stuttgart-Feuerbach, IBP-Bericht WB 117/2003, Fraunhofer Institut for Building Physics, Stuttgart. http://www.passiv.de/old/04_pub/Literatur/IEA/IEA_04/041012_07_IEAT28_IBP_JReiss_Passivhaeuser_Stgt-Feuerbach.pdf (last accessed on 18/05/2013)
Schnieders J. (2003) CEPHEUS – measurement results from more than 100 dwelling units in passive houses, ECEEE 2003 Summer Study – Time To Turn Down Energy Demand http://www.eceee.org/conference_proceedings/eceee/2003c/Panel_2/2047schnieders/paper (last viewed on 18/05/2013)