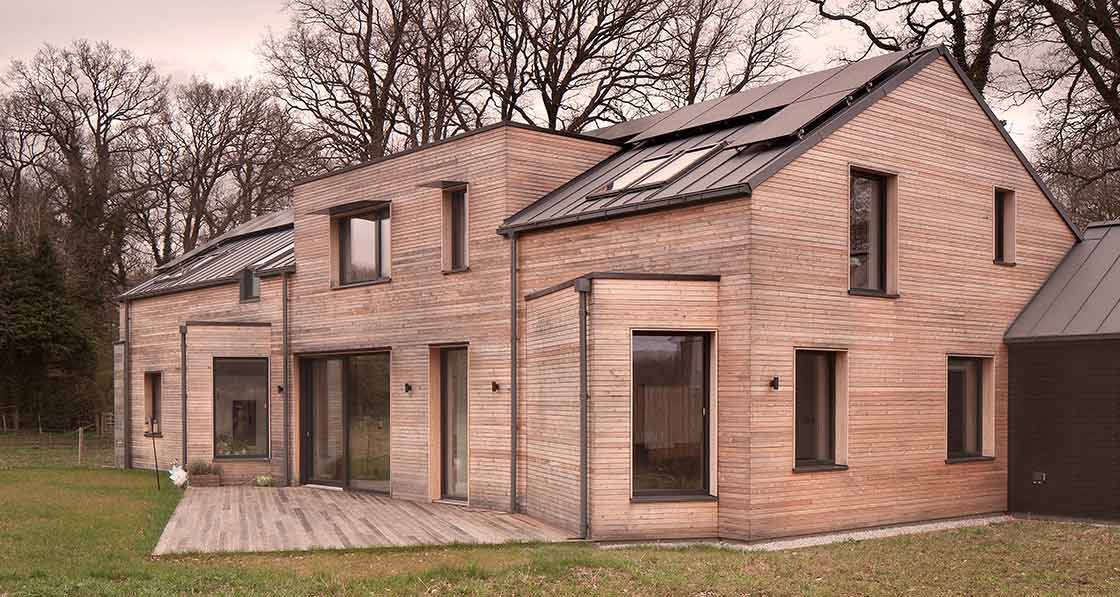
- New build
- Posted
Just what the doctor ordered
What do you get when a clinician couple decide to build their dream family home? In the skilled hands of leading Scottish architects Paper Igloo, you get a forensically detailed, highly ecological, cosy home that wraps up low embodied carbon and passive house into a beautiful design.
Click here for project specs and suppliers
Development type: 258.6 m2 detached home and home office
Method: Naturally insulated timber frame, insulated raft, infrared heating, PV
Location: Stirling
Standard: Passive house classic
Total energy costs: £147.90 per month total energy costs (all energy use – home, garage, and charging two EVs – inclusive of VAT and standing charges. EV charging using 48.5 per cent of annual energy consumption. See 'In detail' panel for more information.
What does it take to build a low energy, low carbon house?
When we first met Sarah and Marcus in late 2019 their brief was quite loose. Having outgrown their current flat with the arrival of their second child, they wanted to move somewhere in the Forth Valley region close enough to their workplaces, and either renovate or build a new home, ideally to the passive house standard. That seemed straightforward enough.
Over a period of several months, we viewed a lot of interesting properties and sites together, but it felt like nothing was quite right for one reason or another. Just as the search was starting to take its toll and dampen spirits, a plot at Blair Drummond came on the market. Set in the open landscape in an attractive semi-rural location, yet only a few miles from the City of Stirling, it seemed like the perfect fit for their environmental ambitions and family needs.
In early 2020 – during the process of searching for the plot for this house – we decided as a company to commit to only design our new build projects to the passive house standard.
Early discussions about this project were a key part of that decision.
We had designed many low-energy or passive house buildings in the past. My journey into low-energy design began with a renovation of my parents’ existing 1868 family home in the Highlands when, some 20 years ago, I created my own SAP spreadsheet to better understand the calculations. In 2013 I became a passive house designer in order to design and build our own certified home and home-office in which we currently live. Despite the potential commercial risk to our company, the commitment seemed like both a natural evolution and an environmental necessity.
For any architect, establishing the initial story with a client is a multi-faceted creative process, yet inevitably it culminates in a deceptively simple list of spaces: an open-plan kitchen dining space, a set number of bedrooms to accommodate everyone who will live there and regular visitors, spaces for the children to grow and be apart from their parents at certain times, and spaces for the whole family to come together in.
However, the joy and excitement in any architectural process goes beyond the prosaic.
When you really get to know people and understand how they live their current life, and how they want to live their future life, you become an integral part of their story: a facilitator and curator, a support and a guide, a counterpoint to thoughts, discussions and decisions. That’s when the creative process can really flourish, and the outcome can be transformative.
For a client who is committed to passive house this journey has another layer of meaning: the desire to reduce energy demand and create a warm, comfortable, and future- proofed home can be used to push every member of the design team to think beyond the usual.
Working as both the architect and passive house designer simultaneously, certain questions inevitably come to the fore in your mind whenever pen is put to paper. How can the layout be optimised, not just from a building physics perspective, but how can those often dry, analytical processes be used as a creative tool? How can we turn discussions about compact plumbing arrangements and the location of the MVHR unit on their heads so as to infuse our creative spirit with energy, and drive us to create delightful, beautiful spaces?
Coupled with matching our clients’ low-energy ambition we brought the ideas of natural materials, vapour-open construction and designing for deconstruction to the table. We also recommended that one of the higher levels of sustainability in the Scottish Technical Standards be targeted due to the additional multifold benefits; in this case together we settled on the Silver Active level which includes enhanced acoustic separation between spaces, a dedicated day-lit home office space with wired internet (which reduces their car dependency), increased spatial requirements for bikes, prams or wheelchairs, and water saving measures throughout.
Similarly to passive house, we find that these ambitions and standards can guide, direct and enliven, rather than restrict or limit, the creative process.
In December 2020 we presented our initial designs to Sarah and Marcus; by March 2021, the planning was submitted. The layout had evolved from conversations around needs arising from changes to the life / work balance the clients sought. This included the need for dedicated space for parents who live at a distance to come to stay more often, in part to assist with childcare, in part to be able to meet frequently as an extended family. The need for spaces for the clients’ hobbies and pastimes also came to the fore. This generated a layout that simultaneously responded to the site and wider context.
The client's view
We love living in our new home. We wanted to reduce our carbon footprint and aiming for the passive house standard seemed the obvious way to do that. It's obviously a huge privilege to be able to live somewhere specifically designed for our needs, and we may be biased, but our home is perfect for us. Even after a year, it continues to bring joy when we come home.
Having experienced all the seasons now, the house has been very comfortable winter and summer and performs extremely efficiently. We had 10 adults and 7 children in the house for Christmas and didn't need any heating on.
We were a bit worried that maintaining two electric cars would make it a bit more challenging, especially with work commutes. However, the setup we have with the solar panels, home battery and a favourable tariff with Octopus has made it quite straightforward. Running costs have been incredibly low, and although Mhairi did tell us that would be the case, it has still been a very pleasant surprise.
The whole process of self-building has been hugely rewarding, though we can take very little credit. The whole team have done an amazing job, and we have come out the other side with an incredible family home which will hopefully allow us to live sustainably for the future.
The design evolution was interesting: due to the clients both working varying shift patterns, one of their key dream spaces was a home gym (but a space which could take on another use in the future) so that they could fit their chosen form of exercise around their work patterns, without being out of the house and away from their children.
We initially proposed locating the gym in the garage building – a double use of an alternative space but one that did not involve using valuable thermal envelope to enclose it. After some discussion, it became clear that the gym needed to be within the passive house thermal envelope so that everyone in the house at any one time could be within shouting distance of one another!
The integration of the gym inevitably increased the house size. We looked at containing the gym in a single-storey volume at one end of the dwelling, but the form factor change and creation of additional junctions led to a further revision where the extra footprint was simply extended vertically. A secondary benefit was the addition of a new upstairs room which could form a hobby space for Sarah and her crafting activities, but also function as a guest bedroom when friends and siblings with their own families come to stay.
The overall layout of the house also responds to the wider context. The house sits above a small burn, and fronts a local loop road which connects the building cluster (of which Melamar is the final addition) to adjacent rural farmsteads. The design enhances not only the owners’ experience of the site, which is defined by long views over fields to the south and west, but has also transformed their quality of life.
Sub-contractors and suppliers can hold the key to lowering or raising embodied carbon without even realising it.
This connection to nature, both visual and physical, has given the clients some much needed relief from the stress of their day (and night) jobs. Working as doctors in an enclosed hospital environment, providing critical care for people often at their most vulnerable takes a toll on the human psyche – having a calm and peaceful space to retreat to at the end of a difficult and emotionally draining shift has had a significant impact on their well-being, with Sarah expressing to me recently the joy she now feels upon returning home every day.
These feelings are subtly articulated in the architecture: the striated Scottish Caithness stone walling with the recessed pale lime mortar on the east elevation defines the more ‘formal’ public realm by creating a robust and solid, yet highly textural mass when the house is viewed on approach or by passersby.
This is complemented by the softer, naturally weathered, hand-nailed Siberian larch rainscreen cladding enveloping the remainder of the building, facing the private garden spaces, referencing the informality of the wider agricultural context, and echoing qualities of the nearby rows of mature deciduous trees that define the boundaries between adjacent fields.
-
The thermal bridge-free Isoquick insulated raft foundation system The thermal bridge-free Isoquick insulated raft foundation system
-
The building was finished in Caithness stone The building was finished in Caithness stone
-
A suspended ceiling was created to house the ductwork and other building services A suspended ceiling was created to house the ductwork and other building services
-
MVHR ducts were insulated and sealed –and capped during construction, to prevent debris and dust entering the ductwork and MVHR unit during construction MVHR ducts were insulated and sealed –and capped during construction, to prevent debris and dust entering the ductwork and MVHR unit during construction
-
The thermal bridge-free Isoquick insulated raft foundation system The thermal bridge-free Isoquick insulated raft foundation system
-
Erection of the timber frame Erection of the timber frame
-
Erection of the timber frame Erection of the timber frame
-
An immaculate airtight layer in the roof, including the Finsa SuperPan VapourStop airtight board and ProClima Vana tapes An immaculate airtight layer in the roof, including the Finsa SuperPan VapourStop airtight board and ProClima Vana tapes
-
Battens were then added to create a 45 mm service cavity, insulated with 40 mm Steicoflex 036 flexible wood fibre insulation Battens were then added to create a 45 mm service cavity, insulated with 40 mm Steicoflex 036 flexible wood fibre insulation
-
Airtightness detailing at window reveals Airtightness detailing at window reveals
-
Insulation to reduce thermal bridging at window reveals; Insulation to reduce thermal bridging at window reveals;
-
Airtight grommets were used to prevenet infiltration via penetrations for wires Airtight grommets were used to prevenet infiltration via penetrations for wires
https://passivehouseplus.co.uk/magazine/new-build/just-what-the-doctor-ordered#sigProIda43905c8bf
Windows: views, light, seats and storage in one
Two unconventional bay windows to the rear serve to combat the less optimal but necessary north-south long axis of the building. Located in the primary, family-orientated spaces, the cladding on the west is peeled back to reveal two optimally orientated windows with integrated seats and storage below, which not only allow sunlight deep into the plan, but also direct longer views to the hills beyond, while giving privacy to both the occupants of this house and the immediate neighbours.
The stairs are also carefully positioned. Separating the grandparents’ room from the remainder of the accommodation on the ground floor and coordinated with a roof-to-wall window over an amply lit void to the kitchen below, the landings become natural stopping points at which one can pause, absorb the view, and feel peace and calm through a visual connection with the natural world beyond.
The technical design phase had, inevitably, focussed primarily on marrying these architectural, spatial and perhaps slightly more esoteric aims with compliance. By August of 2021, the building warrant was submitted. There were no major bumps in the road during this phase, but it wasn’t until May 2022 that the warrant was granted.
A contract was then signed, with a main contractor mobilised but on stand-by, and a timber frame manufacturer ready to deliver the kit only a few weeks later. The warrant approval was the last link in the chain to allow the works to formally commence on site.
With all of the key design decisions locked in place to ensure the road to both passive house certification (being undertaken with the team at Etude) and low-embodied carbon (although with no formal metrics being sought), at this stage the road ahead looked clear and straight.
As a company, our journey into low embodied carbon design began with our own house Ostro, where we learnt that our key decisions around choosing a vapour-open timber frame, insulated with bio-based materials, minimising layers, and simplifying the form factor, had naturally led to a low embodied carbon design, even despite the use of an EPS insulated raft with a concrete slab foundation system.
In both that building and Melamar, post-completion embodied carbon analysis has shown that these critical decisions for the super-structure can create buildings with around 400kg/ CO2e/m2.a with no great difficulty.
In this design as with others, the insulated raft foundation became the ground floor finish, eliminating the need for additional material and using the carbon-heavy slab for dual purpose.
This type of foundation also typically requires less excavations than strip foundations, and in this case, as on all our projects of this type, there was no soil removed from site. No foundation solution is perfect from a holistic environmental perspective, but this one does also have the value of adding a small, manageable amount of thermal mass to the building, which when coupled with the ceiling-mounted, thermostatically controlled, infra-red heating panels as the primary space heating source, offers a third comfort benefit.
When embodied carbon and supply chain collide
This article was originally published in issue 48 of Passive House Plus magazine. Want immediate access to all back issues and exclusive extra content? Click here to subscribe for as little as €15, or click here to receive the next issue free of charge
The concrete slab procurement brought about an interesting realisation on embodied carbon: sub-contractors and suppliers can hold the keys to lowering, or raising, the overall embodied carbon of a given design without even realising it. We had worked hard with the structural engineers, Narro Associates, to specify 70 per cent GGBS replacement to the slab. However, when the main contractor came to place the order the message coming back down the chain from the supplier to concrete sub-contractor to main contractor was loud and clear: “there is none available”.
Unfortunately, in construction as elsewhere in life, the aphorism ‘time is money’ rings true, and, with a timber frame already prefabricated and ready to be delivered just over the horizon, we had no financial choice but to sanction the main contractor to use a standard concrete mix.
Interestingly when we came to undertake the retrospective embodied carbon analysis, the supplier was contacted and either couldn’t or wouldn’t confirm one way or another the mix they had provided, so in the whole life carbon calculations CEM I was assumed as a worst case.
It is easy to imagine that the only thing necessary to combat this effective control over outcomes is to include (as we did here) specification of a lower embodied carbon alternative in the tender documentation.
However, when faced with the reality of cost increases for delays on site caused by the supply chain, many architects, clients and contractors feel the pressure to compromise to keep a project on track and delivered. There is an opportunity here for empowerment within the industry; with wider-spread education, knowledge and improved regulation perhaps there could come a more streamlined realisation of our collective environmental goals.
We chose the I-Joist kit manufactured and erected by Eden Insulation as it utilizes mechanical fixings and non-adhered layers, and in this case was insulated using blown cellulose, with an external wood fibre wrap factory fitted behind the breather membrane, which together with the vapour-open racking board, manages interstitial moisture movement. The selection of these non-toxic materials will allow many of these elements to be safely composted at end of life if they cannot be reused or recycled.
As on all of our projects of this type, there was no soil removed from site.
To address excess waste from renewal and replacement cycles, and to avoid potential damage to the air and vapour control layer (AVCL) board, a service void is included throughout all external walls and pitched ceilings.
To improve the wall U-values slightly (to compensate for heat loss from some view-oriented window orientation compromises) we filled these service cavities with friction-fitted wood fibre batt insulation, which can also easily be removed for recycling or composting at end of life.
We created an additional deep horizontal service void above many of the ‘wet’ rooms to contain MVHR ductwork, pipes and electrical cabling, all below the fire-rated intermediate ceiling. This design move permits easier access to service installations over time, reducing disruption and consequential waste following any internal upgrades or services replacement cycles. It also preserves the acoustic and fire performance of the intermediate floor, and so represents a low-risk solution.
The wall and roof construction were erected in just a week, allowing the main contractor to progress with the other elements of the build immediately. However, there was a significant delay to the programme thereafter due to the delivery of the windows – a hangover from the production and delivery delays caused by Covid the preceding year. Once these were installed in early 2023 the building was finally weather-tight.
IEQ: from shading to low VOC paints
Much of the necessary or desirable shading in this home comes from the deep reveals afforded by the selection of a naturally insulated frame. Bucking the thermally poor trend of placing the fenestration flush on the outer plane of the wall, here we followed the more optimal passive house approach: with the windows placed centrally in the thicker walls the lateral and reveal shading provided the right degree of protection from excessive solar gain. This strategy was complemented by the visually light and delicate brise soleil above the west facing windows.
Their perforations track the sun’s path through the day, while still allowing a curated percentage of light to filter through, creating moving patterns on the internal walls and floor, which delight and add a little whimsy (which every home needs!).
Dedicated indoor air quality monitoring has not been undertaken in this dwelling, other than a CO2 monitor in the master bedroom, as required under Scotland’s building regulations, which has shown average CO2 levels of 533 PPM, and a maximum peak of 762.5 PPM, both well below the safe limit, thanks to the constantly running MVHR system and absence of any fuel-burning appliances for heating or cooking.
Meanwhile, all internal decorated surfaces are finished with low VOC water-based paints, or Osmo natural oil-based products, which not only creates less internal air pollution, but lows painted or finished timber-based materials to be safely re-purposed, or recycled, at end of life. Additionally, the fire-retardant treatment required for the timber cladding to the north gable wall due to distance to boundary was also water-based and so is less deleterious to the environment than alternatives.
Although passive house certified in August 2023, Spring 2024 saw the culmination of this journey with completion finally reached after the standard defects period; a journey which had started back in 2019 with Sarah and Marcus’s desire to change their lives for the better and a short email to an architect’s office.
In tandem with our clients (who are also self-confessed lovers of spreadsheets) we have been monitoring the environmental performance of the house in a few different ways. Temperature and humidity sensors in the west-facing home office room and the open-plan dining area below have shown the usual patterns for low-energy dwellings emerge. When all windows and doors are closed while the occupants are out during the day the indoor temperature rises slightly due to solar gains, particularly as the long elevation faces west. The house is then cooled overnight by following a routine of purge ventilation via the rooflights on the western roof slope coupled with some ground floor windows on tilt.
Overheating frequency has been assessed in these spaces during the first 9 months of occupation at circa 2.86 per cent and 5.36 per cent respectively, which is largely in line with the averaged PHPP estimation of 3 per cent. This should improve over time as the owners become more familiar with a routine of window opening overnight.
Additionally, the renewables systems installed in this direct electric building, which comprise a 6.84kWp PV array fixed over the west facing Greencoat roof covering, connected to a 13.5kW Tesla Powerwall battery, a well-insulated HWC with a divertor from the PV system, and the two EV charging points, all provide detailed .csv export files from which the graphs of energy consumption shown here are derived.
Moreover, the building uses a notable 65 per cent less energy for space heating than a baseline equivalent home of the same design when benchmarked against the 2021 Scottish Technical Standards, which was the year it was consented.
Since the project has concluded the clients have been busy not only assisting me in my favourite pastime of creating graphs of their energy consumption, but also embedding their new home into their first garden. They have planted a mixed species hedge along the eastern boundary to improve the habitat for wildlife, sown a wildflower area including spring bulbs to the front garden, and are gradually implementing their plans for additional permeable landscaping and pollinator-friendly planting in the rear garden.
The flexibility of the spaces, the accessibility and potential for future changes have created a home that not only suits our clients now but will allow for adaptability to suit both them and future occupants without the need for invasive retrofitting works: a home for life. Our clients chose the house name Melamar as an ode to their feelings about the culmination of this once in a lifetime adventure – loosely meaning one’s true or emotional home, this is a place in which they feel rooted and content.
If I had to distil the answer to the question I first asked myself when starting to write this article - what does it take to build a low energy, low carbon house? – I would say above all else it takes tenacity.
Selected project details
Client: Sarah Barr & Marcus McMillan
Architect: Paper Igloo Ltd
Civil / structural engineer: Narro Associates
Energy consultant: Paper Igloo Ltd
Main contractor: SK Joiners Ltd
Electrical contractor: Knowire Installations Ltd
Airtightness tester / consultant: Thermal Image UK Scotland
Passive house certifier: Etude
Life cycle assessment consultant: Paper Igloo Ltd
Build system supplier: Eden Insulation
Wall & roof insulation: Eden Insulation
Additional wall & roof insulation: Ultimate Insulation
Floor insulation: Build Homes Better
Mechanical ventilation supplier: Paul Heat Recovery Scotland
Airtightness products: Eden Insulation / Ecological Building Systems
Additional airtightness products: Ultimate Insulation
Windows and doors: ENERsign GmbH
Roof lights: Jewsons
Photovoltaic supplier: Ceiba Renewables
Shading devices / brise soleil: Clydeside Sheet Metal Ltd
Cladding supplier: Thornbridge Sawmills / Norse Stone Ltd
Finance: Ecology Building Society
Structural concrete slab: Tillicoultry Quarries / Central Rebar Ltd
Flooring: The Rubber Floor Company / The Wooden Floor Store
Roofing: Vertex Roofing & Cladding Ltd
In detail
Building type: Detached 1.5 storey timber frame house with thermally separate but conjoined double garage.
Size: 258.6 m2 treated floor area (305.5 m2 gross internal area) for the house only. 334.9 m2 used in the embodied carbon analysis, to include the garage and the ‘footprint’ of the pergola structure.
Site type & location: Semi-rural site adjacent to small building group in Countryside Policy area, Blair Drummond, Stirling.
Completion date: Building Standards Completion 11 December 2023
Budget: c. £785,200 excluding site purchase, all professional and statutory fees and client supplied items, but including some landscaping (hard surfaces, decking & fencing).
Number of occupants: 2 adults & 2 children, with extended family staying often.
Environmental assessment method: Section 7 in Scottish Technical Standard - Silver Active achieved. Passive house certification: Passive house classic. Certified August 2023.
Energy performance calculation tool: PHPP. (SAP was also undertaken for building regulation compliance but all figures relate to PHPP)
Space heating demand (PHPP): 13 kWh/m2/yr
Heat load (PHPP): 9 W/m2
Primary energy non-renewable: 93 kWh/m2/yr
Primary energy renewable: 39 kWh/m2/yr
Airtightness rating: 0.1 ACH AT 50 pa
Heat loss form factor: 2.79
Calculated overheating risk: 3 per cent of year above 25C (calculated using PHPP)
Air quality index: Fair (an annual average score of 23, based on Blair Drummond Safari Park, using the Plume Air Quality Index)
Air quality context: Site is next to agricultural fields to the west, so some degree of protection may be required when farmers are spreading fertilisers on fields.
Image gallery
-
Axo Melamar Axo Melamar
-
Graph 1 Melamar Graph 1 Melamar
-
Graph 2 Melamar Graph 2 Melamar
-
Tech Sec1 RevA Melamar Tech Sec1 RevA Melamar
-
Tech sec 2 Tech sec 2
https://passivehouseplus.co.uk/magazine/new-build/just-what-the-doctor-ordered#sigProId5f569e9c30
Monitoring results
Indoor environmental quality monitoring overview: 2 Tempo Disc Bluetooth sensors placed in the dwelling since 2023 to monitor temperature and humidity. One was placed in the home office, one in the open-plan kitchen/ dining space (which has only recorded since 7 May 2024 due to a set up issue). Data is gathered hourly and recorded in a .csv file.
Open-plan kitchen/dining room: Context: Typically open to living space (west & south facing) Monitoring period: 7 May – 5 August 2024 (initial results. Average temperature: 23/24C. Percent of period above 25C: 5.16 per cent Note that this is 5.16 per cent of a three-month summer period, indicating that the whole year figure is likely to be substantially lower. Monitoring shows a consistent pattern of temperatures rising when occupants are out at work all day and have left all windows closed for security. Relative humidity: Average of 53.77 per cent (minimum 37.9 per cent, maximum 64.7 per cent).
Home office: Context: Typically door closed for privacy, single-aspect (west facing). Monitoring period: 13 Dec-21 May 2024. Average temperature: 18.8C. Percent of period above 25C: 2.86 per cent. Relative humidity: Average of 46.0 per cent (minimum 27.5 per cent, maximum 65 per cent).
Master bedroom: Context: CO2 monitor required under Scottish Technical Standards. Data has been gathered on two occasions (30.04.24 & 21.05.24) and averaged. Average CO2 levels: 533 PPM. Prior 8-hour average CO2 levels (at time of data collection): 647 PPM. Prior 24-hour average CO2 levels (at time of data collection): 552.5 PPM. Prior 24-hour peak CO2 levels (at time of data collection): 762.5 PPM. Percent of period above 1500 PPM: 0 per cent
Radon: Not monitored, however according to the UK Radon Risk Map the site is not within any radon potential area (less than 1 per cent maximum radon potential).
Acoustic test results: Under Section 7 Silver requirements all internal partitions and intermediate floor have been constructed in accordance with lab tested systems by British Gypsum (partitions) and Knauf Brio (floor) which achieve the following: Airborne sound: 44dB.
Measured energy consumption: From Octopus energy bills between 12.08.23 - 11.08.24: 12,139.5kWh. Note: this differs to the total consumption from the MyEnergi devices of 14,856kWh because the bills only include export from 17.02.24 – 11.08.24. Based on larger GIA (due to lighting / power in garage and lighting to pergola) and total measured consumption excluding exported energy and EV charging, this would equate to: 29.63 kWh/m2 GIA for 25.08.23 - 25.08.24
Energy bills (measured or estimated): Energy bills between 12.08.23 - 11.08.24: Octopus bills with 3 different tariffs over time accounted for. Most recent tariff is Octopus Intelligent Go, with current rates of 7.14 p/kWh for 11:30pm - 5:30am & 26.29 p/kWh for remainder of day/night. Current Standing Charge = 56.22 p/day. All figures excl. 5 per cent VAT. Total bill for this time period (12 months): £1,690.33 excl. VAT or £1,774.85 incl. 5 per cent VAT. This includes total energy usage for house and garage plus standing charges – space heating, hot water, regulated & unregulated energy use and the charging of 2 EVs. It does not account for exported energy back to the grid. Cost for total energy usage as noted above but excluding standing charges was £1,483.48. Note: The total energy costs above include the EV charging: it was not until the new Intelligent Octopus Go tariff was utilised on 02.11.23 that the EV charging times were optimised to either be overnight with battery charging taking place on a sunny day, or more often in winter, to charge the battery over-night at the lower rate and then top-up charge the car(s) from the battery during the day.
Embodied carbon
Upfront total (A1-A5, excluding sequestered CO2): 284.8 kgCO2 e/m2 GIA, (LETI band A rated).
Upfront sequestered CO2 (A1-A5): -149.7 kgCO2 e/ m2 GIA.
Cradle to grave total (A-C): 393 kgCO2 e/m2 GIA (meets RIBA 2030 Climate Challenge target). Calculated using PHribbon v5.23, which follows the RICS 1st edition methodology very closely. Instead of the ‘uncertainty matrix’ in the methodology of the RICS 2nd edition, as much as detail as possible was included in the calculation, including all built elements on the site (garage and pergola) even though these are out-with the thermal envelope.
Building elements included: Substructure; superstructure (structural elements, building envelope, internal elements; finishes (excluding paint / decorations, however all wall / ceiling paint was low / zero VOC by Tikkurila, and all exposed wood was finished with OSMO); fittings (all sanitary fittings included; all built in joinery included except for kitchen units by IKEA & worktops which were Corian on the back wall and porcelain on the island; services (Exclusions: electrical / wiring works & plumbing waste pipework & Tesla Powerwall battery. Inclusions: copper feed DHW pipe work, MVHR unit, PV panels and all heating emitters.). EPDs used included actual products from suppliers including Gyproc, Knauf, Steico, Gutex, Greencoat, Firestone, Aquapanel, Fakro, Sunpower, and Zehnder, with industry association EPDs, EPDs for similar products and default data used in other cases. A full list is available at www. passivehouseplus.co.uk/Melamar.
Build specs
Thermal bridging: Measures taken included thermal bridge-free insulated raft foundation system in combination with thermal bridge-free timber frame, thermally broken window frames and insulated reveals, including modelling of key junctions including ground floor perimeter, thresholds, dormer header meeting pitched roof, ridge, rooflights cill details, to verify performance. See online panel for more detail. Ground floor: 250 mm reinforced C35 concrete slab (CEM I) with power-floated finish (final floor finish), Visqueen Ecomembrane recycled polyethylene DPM, Isoquick insulated raft foundation system, 50 mm grit layer, min. 150 mm compacted Type 1 sub-base. U-value: 0.122 W/m2K.
Walls: 20 mm thick x 80 mm wide untreated Siberian larch rainscreen cladding OR 100-125 mm Caithness stone wall finish with lime mortar and raked joints, 50x45 mm treated timber cladding battens, Pro Clima Fronta Quattro UV stable breather membrane (behind timber rainscreen finish) OR Fronta WA (behind stone wall finish), 22 mm Gutex Multiplex Top rigid wood fibre board, 300 x 45 mm blown cellulose filled timber I-Joist frame, 12 mm Finsa SuperPan VapourStop AVCL board with joints taped with Pro Clima Tescon Vans airtight tape, 45 mm service cavity insulated with 40 mm Steicoflex 036 flexible wood fibre insulation, 12.5 or 15 mm plasterboard or Fireline board (depending on location). U-value: 0.13 W/m2K.
Roof: Standing seam Greencoat (zinc coated steel) roof finish, 18 mm external grade plywood, 45 x 50 mm treated timber battens, Pro Clima Solitex Plus vapour open roofing membrane, 22 mm Gutex Multiplex Top rigid wood fibre board, 300 x 45 mm blown cellulose filled timber I-Joist frame, 12 mm Finsa SuperPan VapourStop AVCL board with joints taped with Pro Clima Tescon Vans airtight tape, 45 mm service cavity insulated with 40 mm Steicoflex 036 flexible wood fibre insulation, 12.5 mm plasterboard. U-value: 0.11 W/m2K
Windows & external doors: Passivhaus Institute certified Enersign triple glazed alu-clad timber frame windows (with thermal break), with argon fill. Averaged installed U-value = 0.72 W/m2K (from PHPP).
Roof windows: Passivhaus Institute certified Fakro FTT U8 quadruple glazed roof windows with thermal flashing kit. 8 x Alu-clad timber frame rooflights with argon fill. Averaged installed U-value = 0.95 W/m2K (from PHPP).
Energy bills (measured or estimated): Direct electric with PV array, divertor, battery storage and EV charging points. PV panels: 37.1m2 array of 18 x Sunpower 380 panels, with 13.5 kW Tesla Powerwall battery, Myenergi Eddie divertor from PV to unvented. 300L Heatrae Sadia Megaflop Eco Plus hot water cylinder with back up 3kW immersion. Space heating emitters: 3 x electric towel rails (1 per wet room) plus 7kW of infrared panels distributed throughout the ground floor, all individually thermostatically controlled. 2 x Myenergi Zappi EV charging points on the garage. Excess electricity exported to the grid. Electricity import rates: 7.14p/kWh for 11:30pm - 05:30am & 26.29p/kWh for remainder of day/night. Electricity export rate: 15p/kWh (fixed rate). Estimated annual electricity yield from PV after the inverter (absolute) from PHPP: 4,164 kWh. Ventilation: Zehnder ComfoAir Q350 MVHR system; PHI certified to have heat recovery of 86 per cent; efficiency in PHPP Ventilation worksheet = 88.5 per cent. No additional cooking fumes extract ventilation, only MVHR extract in kitchen.
Water conservation measures: Recoup ‘PIPE+HEX’ wastewater heat recovery unit installed below master en-suite shower. Dual flush toilets, aerated shower heads & taps. To comply with Scotland’s sustainability target Silver Active, flow rates are 4.5L (WC average flush volume); <6L per min taps serving wash hand basins & sinks, and <8L per min shower heads. 255L water butt in garden collecting rainwater for garden use. Calculated water usage: 94.3 litres per person per day, calculated using the ‘Water Efficiency Calculator for new dwellings’ online tool. Meets 2025 target in RIBA 2030 Climate Challenge.
Sustainable materials: Timber frame using FSC certified timber. Cellulose & wood fibre insulation throughout walls and pitched roof. All timber from FSC sources. Scottish stone. Untreated timber cladding. No adhered layers within substructure of superstructure to permit deconstruction at end of life. (SEDA Guide for Deconstruction followed for main aspects of superstructure.).