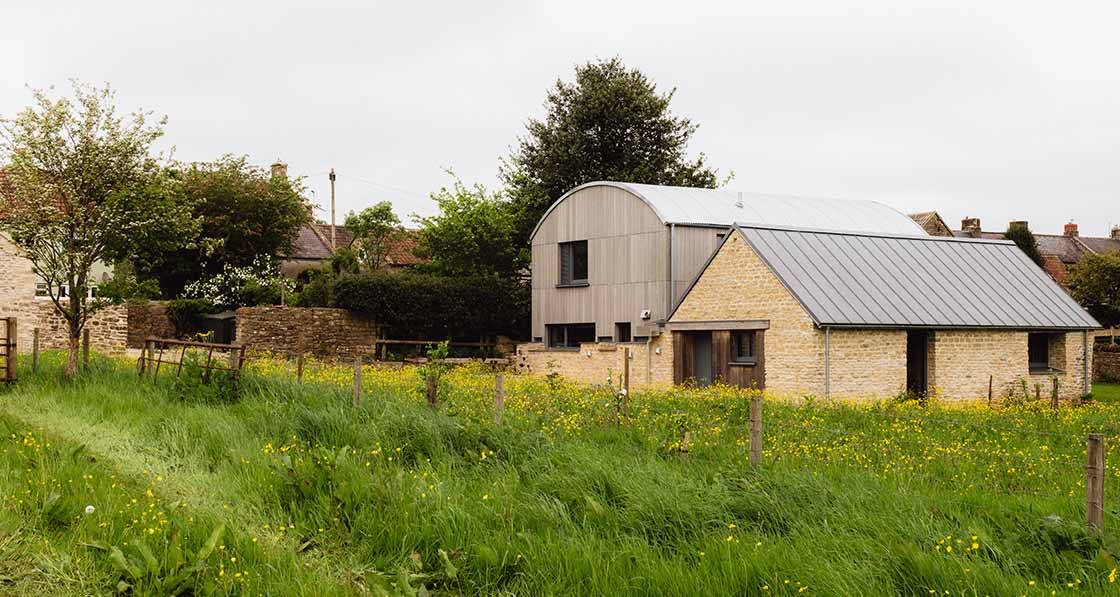
- Upgrade
- Posted
Derelict to dream home
Click here for project specs and suppliers
Development type: 132 m2 detached home plus outbuildings
Method: Derelict barns renovated into low energy home and office using cellulose-insulated timber frame, insulated foundations and heat pumps
Location: Bath
Standard: Enerphit
Space heating cost: £13 per month (estimate, for house only). See 'In detail' panel for more information
Having friends around for dinner is pleasant enough but having them come to dine where once they laboured to remove plants can only be even more special. This is what couple Richard and Chris have done having built their dream home, transforming a set of Grade II-curtilage listed derelict agricultural barns into a modern, energy efficient dwelling, while championing the use of timber and achieving certification to the Passive House Institute’s standard for retrofit, Enerphit.
Recalling the work that got them to where they are now, Chris smiles.
“All of our friends came and helped up.” she says. “We had them remove butterfly bushes and buddleia, and now they come round and have dinner, sitting where the buddleia was.”
Both having an interest in sustainability, the couple always intended to build green. Helping them along the way was the fact that the house they were living in at the time was deeply uncomfortable.
“It was 300-years old. Not listed, but it had all of the attractions of a listed building: damp, an Aga that used to burn five pound notes, and draughts. We sold that and lived in a flat while we set to work on this build,” says Richard.
Richard, an electrical engineer (“nothing remotely involved in building,” he says) and Chris, a former mechanical engineer who now works for the NHS, came to passive houses after hearing an item on BBC Radio Four. However, their investigations went a little deeper than listening to the radio, Chris says. “The Passivhaus Trust was really good. We did some remote courses with them,” she says.
The process that led up to the couple building what is now called the Tin Barn was not swift. Despite there being no shortage of land, no-one wanted to sell, and the first two prospective sites fell through.
“Round here, it is just impossible to find land. We’d write dozens of letters, but no-one wanted to sell,” says Richard.
Finally work could get started when the couple acquired a site on the edge of the village of Marshfield.
“We had a few false starts, but eventually found this plot for sale,” he says.
A three-legged strategy
This article was originally published in issue 49 of Passive House Plus magazine. Want immediate access to all back issues and exclusive extra content? Click here to subscribe for as little as €15, or click here to receive the next issue free of charge
Comprised of three buildings – a traditional stone barn, a round-roofed Dutch barn, and an outlying building – the property is situated in the serene landscapes of Marshfield Conservation Area, and the house as such is a single dwelling constructed from the stone and Dutch barns.
Designing and building a retrofit is always a challenge. Architect Matt Hayes, a co-founder of Hereford-based, RIBA award-winning firm Arbor Architects, says that the challenge is that planning permission demands that the structures actually be used.
“It was a ruin,” he says. “The roof had fallen in [on the stone barn] 15 years previously and a lot of degradation had happened since that.”
The outlying building, which is used only as a home office, storage and guest accommodation, was not done to Enerphit standards. “It was in the best condition [of the three buildings],” says Hayes. “It pretty much just needed reroofing and a bit of stonework patching up.”
This is something of an understatement: in addition to repointing, the walls were plastered internally with Diathonite insulated lime plaster and a cellulose-insulated engineered timber roof was added. But the majority of the budget was put into renovating the new home being fashioned out of the other two buildings – combining new structural elements with the retention of a significant amount of the existing buildings.
“You've got a structure there, you've got walls there [so] you can't just come in with a digger and put up a balloon frame,” Hayes says.
As a result, instead of simply building an engineered stud wall, Arbor worked out, onsite, how to, for example, build inside the steel frame of the Dutch barn.
“We spent a lot of time working out the details of how we were going to do this. That was an effort of structural engineer Beth [Williams], the QS, the builder, everyone, just trying to work it out,” says Hayes.
The airtightness end result came in three times tighter than required for the Enerphit standard at 0.34 ACH. This is a testament to the fact that everyone on site managed to follow the details and work it out, he says.
The stone building also needed work. Aside from the removal of the tree growing inside it, one wall was badly cracked and demanding repair. Additional matching stone was sourced from a local quarry, and a timber frame structure was built inside, using the original stone walls as a rain screen, with a ventilated cavity created behind the stone and an insulated timber frame that combined airtightness and breathability – insulated with moisture-buffering cellulose behind an intelligent airtight membrane.
“On the inside face of the timber frame we used an Intello membrane so we could regulate the moisture – so it could breathe in both directions.”
Space heating for all three buildings, and hot water in the two that form the house, is provided by a Vaillant Arotherm heat pump. An accurate analysis of energy use is not available because subsequent to construction some additional finishing touches were done with a heavy-duty chop saw in the living room, not to mention an open door, but the couple have no complaints.
“We’re very satisfied. Unfortunately, we can’t see what’s using what as it's all on the same circuit [but] I suspect the office is disproportionate in terms of consumption,” Richard says.
Hayes said that while both embodied carbon and operational energy are a concern for his practice, operational energy came first in this case.
-
The ruin of the original stone barn and Dutch barn The ruin of the original stone barn and Dutch barn
-
The thermal envelope was built inside the existing structures, including the Isoquick insulated foundation system and a cellulose-insulated timber frame wall The thermal envelope was built inside the existing structures, including the Isoquick insulated foundation system and a cellulose-insulated timber frame wall
-
A Fronta Humida membrane facing a ventilated cavity to the stone wall. A Fronta Humida membrane facing a ventilated cavity to the stone wall.
-
A Fronta Humida membrane facing a ventilated cavity to the stone wall. A Fronta Humida membrane facing a ventilated cavity to the stone wall.
https://passivehouseplus.co.uk/magazine/upgrade/derelict-to-dream-home#sigProId63d4deef71
“In terms of our process, we actually did it the other way around. We did the energy model for the space heating demand so we could say, ‘yep, we know your space heat demand is going to be this’, which is the kind of passive house view on things.’”
To carry out that energy model, Arbor collaborated with Delta Q passive house consultants to push the barn conversion to the Enerphit standard. “Their input was invaluable in terms of their expertise around PHPP modelling and certification,” says Hayes.
“We talked through some of the more complex details and agreed strategies to take the build forward.”
The roof had fallen in 15 years previously and a lot of degradation had happened.
The blanker the canvas, the easier it is to achieve truly low energy buildings. One key aspect is the form factor – the ratio between the surface area of the external envelope, and the volume of the building. The higher that ratio is, the more surface area in terms of walls, windows, floors and roofs through which heat can escape. It’s therefore simpler and cheaper to meet the passive house standard in buildings with a low form factor, meaning a cube-shaped building. But as Delta Q’s Dave Bryan explains, in this case the planning constraints on retaining the existing structure had a knock-on effect in terms of thermal performance aspirations.
“This effectively removed the ability to optimise the efficiency and form factor to assist with passive house compliance, resulting in a form factor of 3.86. This meant that achieving passive house classic was virtually impossible and in agreement with the certifier, Mead Consulting, the Enerphit standard was pursued.”
According to Bryan, careful consideration had to be given during the design phases to any material change on the envelope areas and treated floor area “as changes are amplified because of the high form factor.”
Another key issue to address was the impact of retaining the existing structures. “This demonstrates not only the importance of a well thought out and conceived building at the earliest possible stage,” says Bryan, “but the even greater importance of effective collaboration when there are external influences that necessitate change".
As embodied carbon remains very much a new frontier in construction, the onus is on designers engaging with calculation at early design stage, so that the impacts of different design decisions can be considered before high carbon impacts get locked in. With no brief from the client to set embodied carbon targets, Arbor took a different approach.
“In terms of embodied carbon, we had a hunch that because we were working with natural materials, you know, it's all timber, the insulation is all recycled [paper].” said Hayes. “We knew there was some concrete in the ground and there's a bit of corrugated metal and steel on the roof, but we had a feeling that actually embodied carbon was going to be quite good on it.
“Towards the end of the project, we did the embodied carbon calculations so we could evidence the hunch and learn from the detailing when comparing to other projects in the office”.
The calculations, which were generated by Peter Morgan of Building Efficiency using PHribbon, are impressive – hitting a cradleto- grave total of 363 kg CO2e/m2 of gross internal area, although in some instances embodied carbon was provided from similar products. For context, the 2030 target for dwellings under the RIBA 2030 Climate Challenge is 625 kg CO2e/m2 GIA. While the house benefits from the retention of existing stone and steel structure and partial foundations, the benefit is arguably relatively minimal in embodied carbon terms.
Essentially a new thermal envelope was built, complete with insulated foundation system, concrete slab, insulated timber frame superstructure, corrugated steel roof and cladding, larch cladding, and new building services and finishes.
-
The same airtight strategy was used for the cathedral ceilings The same airtight strategy was used for the cathedral ceilings
-
Care was taken to ensure airtightness where the roof timbers connected with the walls, such as an Intello airtight sock on the ridge beam Care was taken to ensure airtightness where the roof timbers connected with the walls, such as an Intello airtight sock on the ridge beam
-
Care was taken to ensure airtightness where the roof timbers connected with the walls, such as an Intello airtight sock on the ridge beam Care was taken to ensure airtightness where the roof timbers connected with the walls, such as an Intello airtight sock on the ridge beam
-
The shape of the barrel-vaulted Dutch barn roof was reflected in the airtight layer, built with Smartply airtight boards The shape of the barrel-vaulted Dutch barn roof was reflected in the airtight layer, built with Smartply airtight boards
-
Smartply airtight boards were taped together before the stud walls were added Smartply airtight boards were taped together before the stud walls were added
-
The same airtight strategy was used for the cathedral ceilings The same airtight strategy was used for the cathedral ceilings
https://passivehouseplus.co.uk/magazine/upgrade/derelict-to-dream-home#sigProId907f83ab2b
Beyond embodied energy and energy, Arbor has additional concerns, Hayes says.
“In terms of our thinking, we're aiming at (reducing] both at the same time – the embodied carbon and the carbon in energy – but then also, there is a third one that we put into the mix: internal air quality and from an architectural perspective that's all around trying to specify materials which have low VOC [volatile organic compounds] and low off-gassing. This is always in combination with an efficient MVHR bringing in a constant supply of tempered fresh air. In this scenario it helps that the external environment around the barn has good air quality,” he says.
If construction was stressful it was simply because it occurred during the Covid-19 pandemic, but activity on-site went as smoothly as could be hoped.
“There were lots of unforeseen events, but that's normal for building. We have a slightly weird dogleg in our living room, and that's because the old foundation stuck out that way,” says Chris.
Storm Darragh is raging as we speak, and you don’t notice it unless you go outside”.
Richard says that this resulted in some hasty recalculations.
“It’s really interesting how much analysis can be done during construction. They had to add extra installation,” he says. Contractor CRD, which had never worked on a passive house project before, was keen to learn.
“We talked about them going to do the passive house contractor course, which they did. It was really good that they had an awareness on their side. They absolutely nailed that,” Hayes says. Delta Q director Piers Sadler agrees.
‘We were fortunate enough to have a main contractor in CRD Bath”, says Sadler, “who despite this being their first passive house project, embraced the site training provided by Delta Q and in particular rose to the challenge of constructing some of the more complex airtightness detailing.”
Internally, a modern open plan layout on the ground floor gives way to spectacular views, while bio-based materials were used to create soft and refined interiors, spilling light across varied and textured spaces.
“Elly [Deacon, also a director at Arbor Architects] and Matt listened, the thing we said was ‘chunky stuff’, materials that felt natural and they look lovely,” says Chris.
Now, a year after moving in, how has the build worked out for the couple? Very well, it seems.
“It’s all the things people who live in passive houses tell you and you never quite believe. There aren't any draughts anywhere,” says Richard.
“We’ve gone from somewhere where doors didn’t close to a place where you can have a storm – one is raging as we speak – and you don’t notice it unless you go outside”.
Indeed, Storm Darragh was battering the Cotswolds as the couple spoke to Passive House Plus magazine, but it was entirely inaudible during the video call, a testament to the standard achieved with the building.
For Chris, this says everything: “It’s a revolution. We can't quite believe it. It feels like, at some point the adults will come and take it back”.
Selected project details
Architect: Arbor Architects
Main contractor: CRD
M & E engineer: Hydrock
Civil / structural engineer: Build Collective
Cellulose insulation: PYC Warmcel, via Smart Construction
Floor insulation: Isoquick
Airtightness products: Ecological Building Systems / Medite SmartPly
Windows and doors / MVHR: 21° (formerly Green Building Store)
Primary space heating system: WDS Green Energy Ltd
Energy consultant: Delta Q
Passive house certifier: MEAD Consulting
Quantity surveyor: Adams Fletcher Consultants
Life cycle assessment consultant: Peter Morgan Building Efficiency
Cladding supplier: Russwood Timber
Fit out: Parnosa
Furniture: Made In Ply
Build specs
Building type: Conversion of curtilage listed barns dating to early 19th century. Build method was timber frame to Passivhaus Enerphit certified standard. TFA 118 m2
Site type & location: Rural site, outskirts of Bath. On edge of conservation area of a typical Cotswolds village
Budget: Private
Completion date: October 2022
Passive house certification: Enerphit certified
Space heating demand: 22.65 kWh/m2/yr (PHPP)
Heat load: 11.74 W/m2 (PHPP)
Primary energy non-renewable: 61.58 kWh/m2/yr (PHPP)
Primary energy renewable: 51 kWh/m2/yr (PHPP)
Heat loss form factor: 3.86 (PHPP)
Overheating: 2.08% (PHPP)
Number of occupants: 2 adults
Embodied carbon: 363 kg Co2e/m2 GIA for life cycle stages A1-5, B1-5, C1-4 Calculated to RICS standard using PHribbon
Energy performance certificate (EPC): B88
Energy costs: Monitored usage is not yet available, and analysis is complicated by the fact the heat pump serves the main home and separate outbuilding too. Estimated space heating costs for the home are £155.34/year based on PHPP calculated space heating demand, and the tariff the home is on, the Octopus Flexible tariff, of 23.83p. To estimate the seasonal COP of the heat pump, the average SCOP for the heat pump model used (Vaillant Arotherm) was taken from www.heatpumpmonitor.org – showing an average of 4.1 for space heating and hot water. While the low space heating demand of a passive house may mean slightly lower efficiency, given the heat pump would be required only to generate small amount of heat, rather than run for longer periods at low temperatures, in this case the heat pump also provide heating for the adjacent outbuilding with office and guest rooms, meaning longer running hours being required, and a better SCOP being attainable.
Airtightness (at 50 Pascals): 0.35 ACH Thermal bridging: The thermal bridging strategy was to design out and if not possible minimise thermal bridging from the outset. The timber frame for all the walls and roofs utilises a timber I-joist which minimises thermal bridging. In terms of the main structure the timber roof beams were kept to the inside face of the insulating structure. The opposite is true of the existing steel structure positioned in the external cladding ventilation zone, which keeps the existing structure on the outside of a new insulated timber frame for the ’tin barn’ element. A ‘duvet’ layer of insulation starts below the raft slab and continues through the walls and roof, wrapping the building in insulation. The stone walls are thermally separate from the timber frame built within. The door thresholds sit on an insulating Compacfoam detail tying them back to the structure and allowing them to sit in the insulation zone.
Ground floor: Before: Earth floor. After: 150 mm hardcore, 50 mm blinding, 250 mm Isoquick Peripor, RIW Red DPM, 250 mm RC Slab and 250 mm Isoquick Peripor. U-value: 0.127 W/(m²K) Stone walls:
Before: 400 mm stone.
After: 400 mm stone, ventilation zone, Proclima Fronta Humida Membrane, 12 mm panelvent board, 200 mm TJI fully filled with Cellulose insulation, Proclima Intello membrane, service zone, plasterboard & skim. U-value: 0.195 W/m²K
Corrugated tin walls: Before: Corrugated steel sheet on steel portal structure. After: 20 mm larch cladding, black vent membrane, 50 mm batten, 50 mm counter batten, Proclima Solitex Fronta WA, 12 mm Medite board, 360 mm TJI fully filled with cellulose insulation, 12 mm Smartply board, service zone, plasterboard & skim. U-value: 0.110W/m²K
Roof: Before: Corrugated steel sheet on steel portal structure. After: Pre-curved Galvanised corrugated sheet, 50 mm batten, 25 mm counter batten, Proclima Solitex Plus, 18 mm external ply board, 360 mm TJI fully filled with cellulose insulation,12 mm Smartply board service zone, plasterboard & skim. U-value: 0.110W/m²K
Windows & doors: Windows: GBS Ultra. U-value: 0.80 W/ m²K.
Doors: GBS Ultra. U-value: 0.79 W/m²K Roof windows: Fakro DMF U8 Rooflight. U-value: 0.80 W/m²K
Heating system: Mitsubishi PUHZ-W50VHA2(-BS) 4.5kw air-to-water heat pump heating the main home and outlying building
Ventilation: Ubbink NV - Ubiflux Vigor W325 MVHR (Passive House Institute certified). House designed to allow for natural night purge ventilation in addition to summer bypass on MVHR
Water: Low flow fixtures
Electricity: PV not permitted under planning permission
Sustainable materials: Sandstone from local quarry within 5 miles of site (in addition to reclaimed stone from site), Warmcel cellulose insulation, timber Terrazzo Foresso internal finishes, Smartply airtight board, European spruce glulam structure, oak and larch cladding.
Image gallery
-
Barn 2 3 Barn 2 3
-
Barn 23 Barn 23
-
IMG_2508 IMG_2508
-
IMG_6065 IMG_6065
-
IMG_6072 IMG_6072
-
IMG_6682 IMG_6682
-
B2 north wall showing ext. steel boxed outs B2 north wall showing ext. steel boxed outs
-
B2 east elevation framing studs and Glulam B2 east elevation framing studs and Glulam
-
B2 propassiv installed above floor junction B2 propassiv installed above floor junction
-
Taping of Glulam trimmer in b2 Taping of Glulam trimmer in b2
-
B2 north wall exposed studs at 600 centres B2 north wall exposed studs at 600 centres
-
B3 ridge intello socks wide shot B3 ridge intello socks wide shot
-
B2 north propassiv boards B2 north propassiv boards
-
Pre fabbed B2 elevations w_ply sheets Pre fabbed B2 elevations w_ply sheets
-
B3 Isoquick with foam joints B3 Isoquick with foam joints
-
B3 roof construction Pre boarding B3 roof construction Pre boarding
-
IMG_1732 IMG_1732
-
IMG_2487 IMG_2487
-
IMG_4898 IMG_4898
-
IMG_6072 IMG_6072
-
IMG_6682 IMG_6682
https://passivehouseplus.co.uk/magazine/upgrade/derelict-to-dream-home#sigProId8466495f18