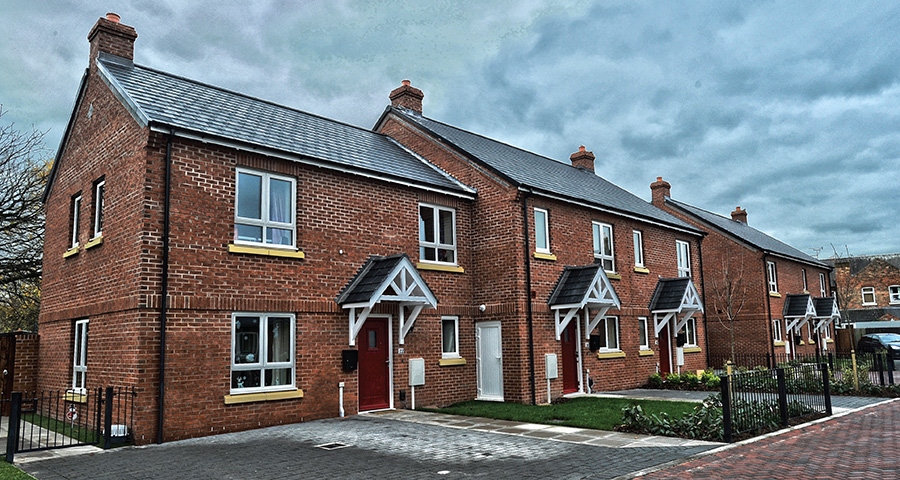

- New build
- Posted
East Midlands scheme opt for passive regeneration
One third of the units at a new social housing development in the East Midlands have met the passive house standard— but the entire project was inspired by fabric first, low energy design.
This article was originally published in issue 7 of Passive House Plus magazine. Want immediate access to all back issues and exclusive extra content? Click here to subscribe for as little as €10, or click here to receive the next issue free of charge
Three passive house dwellings in the East Midlands are part of a new multi-million pound regeneration programme by social housing provider East Midlands Housing Association (recently rebranded as emh homes). The first phase of the scheme, nine houses at Hart Lea in Sandiacre, was completed in October 2013.
Following the advice we gave at Encraft, the design team decided to adopt a passive house inspired, fabric first approach on the development of nine new houses. But it was Lindum, the main contractor, who decided to aim for full passive house certification.
The ground floors are insulated with 200mm of Celotex insulation
Lindum would have effectively met the standard anyway in delivering the fabric first approach outlined in the tender. But as it was not an explicit requirement from emh, passive house certification was only made possible through Lindum’s commitment to achieving the standard.
Early analysis carried out in PHPP showed that certification would be achievable with no further enhancements to the tender specification, at least on plots with favourable orientation. To be sure of success, Encraft worked with Lindum throughout design and construction to develop the detailed designs in line with passive house criteria.
Our initial involvement with the project came through Ridge and Partners in Leicester who were working on behalf of emh homes as project managers. At the time the scheme was being designed in the traditional way, by a design team familiar with emh’s previous schemes and standard design brief. However with additional requirements to meet level four of the Code for Sustainable Homes (CSH) and Lifetime Homes, Encraft took the lead to evaluate how the scheme could meet these targets.
Having recent experience of building to varying code levels, emh was already aware of the potential pitfalls of achieving compliance with the code's energy requirements. Poor integration of low carbon technologies, high maintenance issues, dwellings not performing as expected and homes having higher bills than predicted — these were all problems that emh is keen to avoid on their new build schemes. Based on past experience, it was clear that the favoured approach would be to adopt a fabric first build specification that would enable the scheme to achieve the required energy performance without the need for any bolt-on renewables, while also delivering the lowest predicted fuel bills for residents and the lowest whole life costs for emh.
A passive house inspired fabric first approach was pitched against more commonly adopted high-tech approaches, including ground and air source heat pumps, and bolt-on renewables such as solar PV and solar thermal. The whole life costs and benefits of each option were evaluated to estimate lifetime performance, which should always be a key factor for social housing providers who have a long term vested interest in their building stock.
This evaluation presented the fabric first approach in a complimentary light, and helped to justify extra capital expenditure. While emh was sold on the idea of a fabric first approach they feared that full passive house certification for the development could potentially overinflate build costs. Furthermore, the project had already been submitted for planning and there was a need to be onsite within a specific timeframe which meant that the scheme was already constrained in terms of site layout and building design.
Thermalite AAC blocks were also used in the ground floor details; cooker extract fans recirculate indoor air after passing it through a grease filter, thereby not piercing the airtight layer; the houses feature Airflow Developments DV72 mechanical ventilation heat recovery systems with inline battery heaters and radial duct system distribution box.
Encraft proposed a specification for the build which would enable passive house standards to be achieved for the plots with the best orientation and building form factor. Initial analysis in PHPP focussed on plots that were expected to perform best. By aligning the passive house design criteria with the best-performing plots we were able to ensure the cost-effectiveness of the scheme — especially as there were bungalows on which it would have been challenging and costly to achieve certification.
We arrived at a build specification which could be applied across the entire site, enabling certification of three plots while ensuring that the remaining six dwellings would be built to the same high standards. Using this tactic, all dwellings on the site would end up as close to the passive house standard as practically possible, while keeping within budget.
In the end all plots were modelled in PHPP with the best performing only just achieving the passive house heating load target of 10 W/m2 and the worst (a bungalow) around 3W/m2 worse than this. It would not have been possible to certify on the basis of the space heating demand target, which ranged from 19 kWh/m2/yr upwards.
The build specification, on which contractors were invited to tender, included: a contractual requirement to meet the passive house air leakage limit of 0.6ACH at 50Pa; limiting U-values to 0.1 in the walls, roof and floor; Sheerframe triple-glazed windows and doors with an installed average U-value no worse than 0.85 and prescribed G-factor of 0.6; enhanced construction detailing to achieve a Sap Y-value no worse than 0.05; Glow-worm condensing gas boilers for heating and hot water; and mechanical ventilation with heat recovery provided by the Paul Focus 200 from Green Building Store. With this specification CSH level four is attained without the need for any renewable energy.
Although contractors were given a fairly detailed performance specification for the build, they were invited to tender on the basis of a design and build contract. This gave them the freedom to propose their preferred method of construction, while ensuring the lowest risk for emh in terms of their contractual obligations and design responsibility.
The contract was awarded to Lindum Construction in November 2012, who priced competitively at just under £1,400 per sqm for the total cost of the build and proposed to use the Val-U-Therm off-site build system which promised to deliver the required thermal protection, quality control and airtightness performance standards.
Lindum MD Simon Gregory, emh homes CEO Chan Kataria, Cllr Carol Hart & Encraft’s Helen Brown launch the scheme.
The Val-U-Therm wall system exceeded the thermal protection requirements with a U-value of 0.09. This enabled some flexibility in the design for meeting the passive house criteria. Similarly, a switch from the Sheerframe windows and doors proposed in the tender to the passive house certified range from Munster Joinery added to this performance buffer because the Munster option is slightly better performing in the PHPP (as well as being cheaper).
Lindum decided not to use the complete Val- U-Therm system, which can include both ground floor and roof elements in one integrated build system. The basis of this decision was cost, as implementing a traditional suspended concrete beam floor and attic truss roof looked likely to be the more cost-effective option at the estimating stage. However, connecting the Val-U-Therm walls to the more traditional floor and roof elements proved to be quite time consuming, both in the design detailing and subsequent implementation onsite, particularly in regards to airtightness and thermal bridge details. Time and effort would certainly have been saved if the complete Val-U-Therm system had been used. It would be interesting to evaluate how much of an impact on build costs this would have had.
In general construction details were developed in a collaborative way with lead designers Geoff Carter Architects taking specialist design input from Encraft, particularly in regards to airtightness and thermal bridge details. A clear strategy for airtightness was defined to incorporate a single air barrier, primarily consisting of Glidevale vapour control membranes on the warm side of all major elements, connected with appropriate tapes at junctions and into the window reveals.
Although the Val-U-Therm wall panel has an OSB layer there was some nervousness around relying on this as the main air barrier. A service void was incorporated into the design to ensure that the air barrier would be fully protected, both during construction and beyond. And the air barrier wraps around adjoining plots, such that the party walls between dwellings are not airtight. This approach saved on time and materials and negated the need for a service void in the party wall.
Airtightness details were generally much easier to draw on paper than they were to realise on site. Sequencing notes were written to complement the critical construction details. These were found to be a useful aid to improving buildability. Lindum’s site manager acted very successfully as the scheme’s airtightness champion, whose role was to make sure that airtightness details were understood and adhered to, take ownership of quality control, check that the correct materials were being used (such as refusing to use duct tape in place of the specified air barrier tape) and communicate the importance of airtightness to everyone on site.
All airtightness details were implemented by the Lindum site team so that they could take full ownership of this aspect of the build rather than having to rely on subcontractors. Regular site visits from Encraft ensured quality standards were met. We provided feedback on areas that could be improved and reassurance when things were done well. The window detail posed a particular challenge and it then took a considerable amount of time to seal the frame into the reveal for airtightness following Munster’s installation, which only fixed the windows into position.
Airtightness testing was carried out at interim stages, when the air barrier was still exposed, so that we could look for leaks and make improvements as necessary. Observed weak points were mainly around the window and door reveals. The windows – which are passive house certified – were airtight as a window unit, but there was leakage from the uncertified doors, the weak point being where the doors seal to the door frame.
Final air testing was carried out by UK Air Testing and all plots managed to achieve passive house standards with results across the site ranging from 0.46 to 0.58ACH at 50Pa and the passive house certified plots tested at 0.54ACH at 50Pa.
Heating and ventilation system designs were developed by the installers, RJ Wilson with design input from Encraft to ensure passive house compliance. One area that Lindum and emh were able to save money, against the original tender price was in the MVHR system. Airflow’s Duplexvent DV72 was installed in preference to the Paul Focus 200. The DV72 has efficiency in the heat exchanger of 91% according to SAP Appendix Q, which is equivalent to that of the Paul unit. But because this particular Airflow unit is not passive house certified there was a 12% penalty applied to the efficiency in the PHPP calculation. Even with this hindrance it was possible to meet the passive house criteria for building certification, if only on the south facing plots.
Furthermore, high system efficiency was ensured by positioning the central heat exchange unit on an external wall, thus allowing for the shortest possible intake and exhaust duct routes. The length of these ducts, which transport cold air through the thermal envelope, must be kept to a minimum to prevent unwanted heat exchange between the duct and the internal environment.
The MVHR units were installed in a plant cupboard which also housed the Glow-worm gas boiler, located on the ground floor; usually next to the kitchen and accessed via an external door (no internal access was provided). In this way emh will be able to easily access the plant for servicing and maintenance. Ease of access to the plant cupboard was a critical consideration because emh will need to visit at least twice per year to change filters on the MVHR units, on top of the annual boiler service and gas safety checks.
The plant cupboard also housed the electric PCT frost protection, as well as an in-line supply- air electric duct heater and Airflow’s radial duct system (Airflex Pro) distribution box. The main controls for the MVHR system are also inside the plant cupboard, out of sight and out of reach from the building occupants. The MVHR system has been set to run continuously at a standard ventilation rate and no boost control has been provided, so residents do not really interact with the ventilation system at all.
The only controls which residents were provided with in the home were for space heating and hot water. This included a standard programmable time-clock as well as two room thermostats, one to control the space heating delivered by the gas boiler (provided by two towel heaters in the bathroom and downstairs WC) and one to control the electric duct heater.
Encraft took great care to write an easy-to-read home user guide which focussed specifically on the passive house aspects of the scheme, introducing the concepts of passive design to residents and helping them to understand how best to use the home and the technologies installed.
Great importance was placed on the functional aspects of the MVHR system, so that even while direct control of this system was not put in the hands of residents, they should still be able to understand how it works, why it is important, and be able to troubleshoot air quality problems and seek further advice or remedial work if it's needed. Further guidance was given on the operation of the heating controls and also what to do during summer to mitigate the risk of overheating.
This passive house specific home user guide was incorporated into the larger home user pack provided by Lindum in order to comply with CSH requirements. But it was the passive house specific guide which emh used predominantly in their initial discussions with residents and their intention is to use the guide repeatedly as a reference in future to deal with user problems or concerns when they arise.
Overall, Encraft was pleased to use our passive house expertise to enable certification of this landmark residential project for emh homes. Going forward, it would be great if this project could provide a stimulus for the wider uptake of the passive house standard in the East Midlands region.
Selected project details
Client: emh homes
Architect: Geoff Carter Architects
Developer: Lindum Construction
Passive house consultant: Encraft Ltd
Structural consultant: BSP Consulting
Quantity surveyor & project manager:
Ridge and Partners
M & E contractor: RJ Wilson
Airtightness tester/consultant: UK Air Testing
Build system supplier: Val-U-Therm
Phenolic insulation: Kingspan Insulation UK
Mineral wool insulation:
Superglass, via Total Insulation Solutions
Floor insulation: Celotex
Airtightness products: Glidevale
AAC Blocks: Thermalite
Windows and doors: Munster Joinery
Mechanical ventilation supplier: Airflow
Condensing boilers: Glow-worm
Additional info
Building type: A 236 sq m terraced passive house new build. The certified building consists of three domestic dwellings and was built using a timber frame construction. Six other dwellings were built on the site – four semi detached houses and two bungalows. All were built to the same specification but only the terraced row of three were certified due to its favourable orientation and form factor.
Location: Sandiacre, Leicestershire, UK
Completion date: November, 2013
Budget: £1m or £1,400 per square metre approx
Passive house certification: Three-dwelling terrace certified by the BRE
Space heating demand (PHPP): 19 kWh/m2yr
Heat load (PHPP): 10 W/m2
Primary energy demand (PHPP): 111 kWh/m2yr
Environmental assessment method: Code for Sustainable Homes – level 4
Airtightness (at 50 Pascals): 0.54 ACH
Energy performance certificate (EPC): B (85)
Thermal bridging: Heat Loss from thermal bridges reduced using a mixture of Advanced Construction Details and EST Enhanced Construction Details. Extra Kingspan TW55 low-e coated insulation added around the perimeter of the roof to reduce thermal bridges. Thermalite low density concrete blocks used in ground floor details with phenolic foam insulation in window reveals. Calculated Yvalue using ACDs and ECDs of 0.045 W/m2K.
Ground floor: suspended concrete beam floor. 150mm concrete slab, 200mm PIR/PUR insulation, 75mm screed. U-Value: 0.106 W/m2K
Walls: ValUTherm timber frame wall. 15mm Knauf Wallboard fitted to Val-U-Therm panel system including 35mm unventilated battened cavity facing 25mm Kingspan TW55 low-e coated insulation, Glidevale Protect VC foil vapour control layer & either Protect VC foil tapes at window reveals or Glidevale Butyl tapes where nails penetrated the membrane, including 9mm OSB sheathing, 235mm injected insulated polymer derived from renewable vegetable oil with timber frame fraction 0.1,
9mm OSB sheathing, Protect TF200 Thermo, 60mm ventilated cavity, 103mm brick outer leaf. U-Value 0.090 W/m2K
Roof: timber truss roof. 150mm mineral wool with timber fraction .063, covered with 350mm Superglass mineral wool. The air barrier was a polythene membrane installed on the warm side of the insulation (at ceiling level) with a 25mm service void below to accommodate all electrical wiring etc. U-Value 0.098 W/m2K
Windows: Munster Joinery Passiv Future uPVC frames with Saint Gobain triple-glazing. 4-20-4-20-4 mm with 90% argon cavity fill and low-e coating internal and central panes. Uvalue: 0.78
Heating system: Glow Worm Ultracom 12sxi 89.5% efficient condensing gas boiler, supplying two towel radiators and domestic hot water cylinder.
Ventilation: Airflow DV72 MVHR system (certified heat exchange efficiency of 91% according to SAP Appendix Q) with inline battery heater and Airflex Pro distribution box.