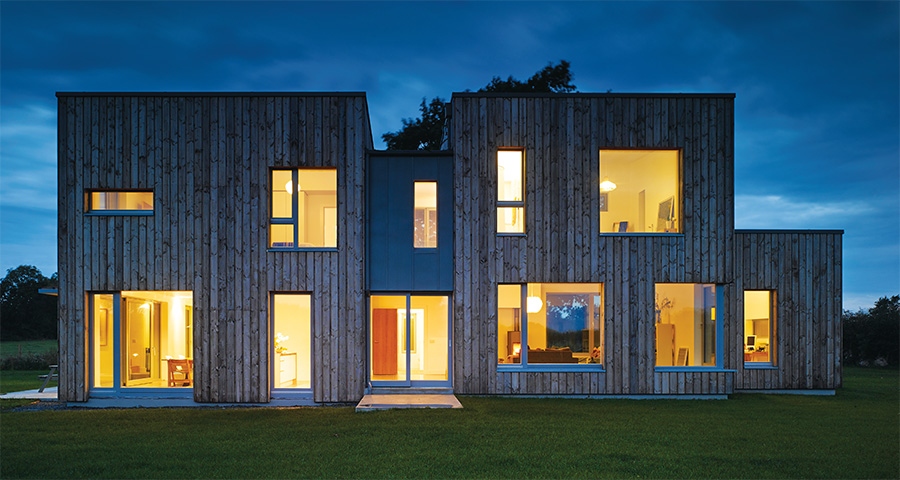
- New build
- Posted
Passive architect walks walk with Carlow home
None of the team behind Passive House Plus has the good fortune to live in a passive house – at least not yet – meaning our promotion of passive house comes with more than a hint of “Do as I say, not as I do”. That’s emphatically not the case with certified passive house designer Helena Fitzgerald, who chose to practice what she preaches with her own home, to stunning effect.
The window company who came to fit out architect Helena Fitzgerald’s passive house in Carlow had allowed five days for the job. Such was the precision with which the frame had been planned however that they only needed a day and a half.
Donal Mullins of Shoalwater Timberframe says that the levels of accuracy in the frame were unbelievable. “Helena had worked everything out to the millimetre,” he says. “All that accuracy in design spills through for everyone so that the build goes really smoothly. Everything was done on paper beforehand and that’s the way it should be done. There were no meetings on site with the usual head scratching; ‘how are we going to get around this one? Whose fault is this?’ She was a pleasure to work with.”
Helena cut her teeth working with Building Design Partnership (BDP) in Scotland, before returning home to Carlow in 2005. Four years later, she set out to build a passive house for herself and her young family.
“My husband and I understood that this was the biggest project we were ever going to get involved in and that it had to reflect our values,” says Helena. “My husband was really supportive about trying to develop our own project as a passive house.”
Built on her family’s farmland, the site on which Helena planned her house provided spectacular views of Mount Leinster and the Blackstairs mountains, and featured a mature oak tree. The problem however was that these were found to the east and west of the site respectively. Passive design seeks to make the most of solar gains by maximising glazing on the southern elevation.
Making the most of the site’s natural features while maintaining the passive approach was a challenge which Helena relished. “Many of the passive houses I had seen appeared quite scientific in their approach,” she says. “They weren’t very expressive forms, their architectural quality wouldn’t appear to have been a priority. If passive house is to be applied more generally, you need to be able to use it on all sites, not just the ones which have the south facing aspect to the rear. I was really interested to see how flexible it could be.”
Acutely aware of the ‘privilege’ of building on a green field site, she wasn’t solely concerned with the energy profile of the house. In addition to the mountain view and the mature oak, the site also featured an old granite dry stone wall and a slight dip in the ground to the south east corner. Helena was keen that the design should respond to these features. “The other preoccupation was land use. We live in the countryside and we have a relatively large site; it’s in excess of half an acre and we didn’t want to be mowing the lawn all the time. We wanted to think about how we were going to be using this piece of land.”
In coming up with a design, Helena divided into four distinct areas: a public/arrival area to the north east and a functional/working garden for wood storage and clothes drying to the south west, with a raised bed percolation area providing shelter for the kitchen garden. The kitchen/dining area opens onto a leisure garden to the south east, which includes the only area of conventional lawn. In the final quarter to the north east, she had planned a wilderness garden, though this is now under review because the soil type doesn’t appear appropriate.
To make the most of the key features to the east and west, the living areas were given an east/west orientation with informal kitchen, dining and family room to the south. Services went into the northwest corner, with utility and entrance, neatly facilitating a division between the public arrival space from the more intimate kitchen garden. “We decided not to have a garage because people don’t use garages, they just need a space to store bikes and stuff,” says Helena. “This meant that we ended up with an L shaped plan...Having this L shape meant we could have the longer elevation to the south, which was critical in terms of getting enough southern light into the building.”
The deployment of glazing has of course a significant impact on the performance of the house. Helena here was guided by how each room was used. In the kitchen/dining area, which opens onto the recreational garden and faces south, the windows go right down to floor level. In the more formal areas east and west, smaller ‘picture’ windows capture specific views. “If we put smaller windows in east and west, we would have had a better thermal performance for sure, but the amenity value of the views would not have been the same. There was a trade-off there.”
Here again is a reaction against the notion that passive must be hamstrung by the science. Strict interpretation of the guidelines would leave northern elevations almost blank, with extensive glazing to the south. A more liberal interpretation allowed Helena a more expressive building, though this meant that she had to find ways of compensating for any resulting heat losses in other ways. She points out too that that you can increase glazing while minimising heat loss. It’s the frame that tends to let the window’s energy performance down. “If you have lots of divisions, your window is going to perform less well than if you have larger panes of glass. That’s taken to the ultimate in the master bedroom window, which is just a huge fixed pane of glass with no openings.”
While the budget did not stretch to passive certified windows – the options Helena looked at commanded a considerable premium over non-certified ones available at the time – she says the Kneer-Sued-fenster triple-glazed units still achieve close to passive standards.
When it came to choosing materials and a building method, Helena was keen to maintain the sustainable philosophy she brought to the rest of the project. She learned about Siberian larch cladding from BDP colleagues who had used this material on the Isle of Skye, off the northwest coast of Scotland. The timber is untreated, and has a rough, organic appearance. Not only does it respond well to the existing tree on the site, it also weathers to a pinky grey colour, very similar to the existing granite wall. “In five years time, I think this building will be almost invisible from the road,” says Helena. “It will disappear.”
The combination of Supergrund foundation and cellulose-filled timber frame construction delivers an envelope befitting of a passive house. Thermal bridge free construction – an essential part of passive house design – was achieved through the use of a continuous insulation layer which wraps the entire building. Helena trained in thermal modelling and produced all the construction details herself. Shortly after she had completed the work however, the National Standards Authority of Ireland introduced a registration scheme for thermal modelling. Helena found registration an expensive process, and decided that commissioning new thermal bridge details from a registered modeller was both unnecessary and beyond the reach of the budget. The result is that for Deap purposes, Helena has had to use a set of default details which drastically misrepresent how thermal bridges are circumvented in the house, leaving her with a poorer BER certificate.
Airtightness was achieved primarily through the use of OSB board, taped using Intello products. Donal Mullins of Shoalwater, who took responsibility for this element of the build, says that he was initially nervous about using OSB as an airtight layer.
“This was a challenge because OSB isn’t a certified board for airtightness,” he says, “but I knew that detailing the project properly and dealing with all the crucial areas would limit that risk. We had to think outside the box with the airtightness, but it did pay dividends in the end with the final reading we got.”
Gavin O’Sé, who conducted the airtightness tests and carried out the BER assessment, reports a final test air change rate of 0.38, an excellent result, well inside the passive house threshold of 0.6 ACH.
Solar thermal panels provide the bulk of domestic hot water needs. Helena considered two options for space heating and domestic hot water backup. “We couldn’t imagine a living area without a flame so a room-sealed stove was included in both options. The first was an air to water heat pump with a room heating stove, the second was a stove with back boiler.” Because of budget restrictions and the fact that the heat demand was so low, Helena didn’t want to duplicate the systems, so she opted for the latter. This option, while it did suit the family’s lifestyle, did however have an impact on the final BER, owing to the lack of heating regions or thermostatic control. “Stoves are inherently manually operated,” she says. “We were penalised for this in the BER process due to the lack of thermostatic control.”
As for fuel usage, Helena has an abundant biomass supply that comes from maintaining hedgerows on the family farm – a supply that far ourstrips demand. “We stopped lighting the stove in April,” she says. “We’ve lit it twice so far this winter, but mostly because we had people staying who wanted to see it in action.”
Electricity costs are working out at approximately €95 per month – the only actual energy cost at the moment.
Helena also decided not to go for passive house certification – which would have added a cost of circa €1500 – due again to budget considerations. “I have another project pending certification, so I didn’t really need to do it for my work. I would have liked to do it on this project but we needed to put a kitchen in.”
The family moved in March 2012, during the cold snap, when temperatures outside rarely got above freezing during the day. “It was very comfortable,” says Helena. “If there’s any sun at all when it’s cold, you’re toasty.
“You could be very critical of the house, you could say that it is not the most economic way of achieving passive house but it is a very particular site and I had to respond to that. If I had just put a rectangular block here, it would have been a missed opportunity. I wanted to ask, can you achieve this energy performance with a more expressive and architectural form? If passive buildings don’t respond well to their setting, will people want them? Or is it going to be something that’s just peripheral fascination of a few, motivated individuals?”
Selected project details
Architects: Helena Fitzgerald Architects
Executive architect: Kelliher Miller Architects
Structural engineer: ONCE Civil & Structural Ltd
BER assessor and airtightness tester: Greenbuild
Mechanical contractor: Michael Wall
Electrical contractor: Doyle Bros Electrical
Timber frame: Shoalwater
Timberframe Cellulose insulation: Isocell Ltd
Mineral wool insulation: Isover Ireland
Wood fibre insulation & airtightness systems: Ecological Building Systems Limited
OSB: Medite Smartply
PIR insulation: Xtratherm
Floor insulation: Kingspan Aerobord
Additional airtightness tapes: Tremco Illbruck Ltd
Windows and doors: Kneer-Südfenster
Steel frame for brise soleil: Murtech Engineering Ltd
Screeds: Dan Morrissey IRL Lrd
GGBS for screeds: Ecocem
Stove: Olsberg
Solar thermal: Kingspan Solar via Polytherm
Underfloor heating: Polytherm
Heat recovery ventilation: Pure Renewable Energy Ltd
Lighting: Mid West Lighting/Habitat/Mawa Design
Water conserving fittings: Hansgrohe
Sanitaryware: Duravit/Bette
Fit-out joinery: James Hanrahan Carpentry
Engineered oak flooring: Wogan Distributors via Heiton Buckley
Coir mat entrance carpet: Footfall
Roofing membrane: Laydex Ltd.
Additional info
Project overview:
Building type: 233 square metre detached two-storey timber frame house with a 14 sqm shed
Location: Borris, Co Carlow, Ireland
Completion date: March 2013
Budget: not disclosed
Passive house certification: not certified
Space heating demand (PHPP): 14.9 kWh/m2/yr
Heat load (PHPP): 11 W/m2
Primary energy demand (PHPP): 92kWh/m2/yr
Airtightness: 0.3875 ACH / 0.418 m3/hr/m2. (An50 result of 0.6 would have made the building fail to reach the passive house standard as the space heat demand would have risen to 15.8 kWh/m2yr)
BER: B1 (78.47 kWh/m2/yr)
Thermal bridging: The structure was designed to be thermal bridge free, as required for a passive house, with a continuous layer of insulation around the perimeter of the building envelope. Specifically, an insulated raft foundation was used, 50mm wood fibre board was fixed to the external face of timber frame walls and PIR insulation used on top of the roof deck. Care was taken to ensure continuity of these layers at the substructure/superstructure junction and where the wall meets the roof. At window openings, timber framed windows were used; externally, wood fibre board insulation overlapped the windows by a minimum of 50mm and internally the reveals were insulated. In Deap The Y factor value used for thermal bridging was set to a default level as full calculations were deemed too costly.
Ground floor: Supergrund insulated raft foundation system with 300mm EPS. U-value 0.113
Walls: Factory-built timber frame with 25mm untreated Douglas Fir cladding externally in board on board format, followed inside by treated softwood battens and counter-battens, Pro Clima Soltex WA breather membrane, 50mm Gutex Ultratherm woodfibre board, 222 x 44mm Isocell cellulose-filled timber stud, 18mm taped and sealed OSB3, 50mm service cavity insulated with Isover Metac insulation, and 12.5mm Fermacell board internally. U-value: 0.129
Roof: 60mm pebbles on Alkorplan membrane build-up on 100mm Xtratherm FR MG insulation on Alkorplus vapour control layer on 18mm OSB3 structural deck (part of timberframe) on 225 x 44mm rafters filled with 220mm Metac insulation, Pro Clima Intello vapour control layer, 35 mm uninsulated service cavity, 12.5mm plasterboard ceiling. U-value: 0.104
Windows: Kneer-Süd-fenster HF90 1000 triple-glazed spruce windows, with argon filling. Overall U-value: 0.83
Heating system: 80.5% efficient Olsberg Tolima Aqua Compact stove with back boiler, plus 40 Kingspan Thermomax Varisol DF100 tubes, supplying 200L DHW cylinder, and 400L buffer tank supplying underfloor heating and towel radiators in upstairs bathrooms.
Ventilation: Paul Novus 300 heat recovery ventilation system — Passive House Institute certified to have heat recovery rate of 93% and electric efficiency 0.24 Wh/m3.
Green materials: Fermacell, cellulose insulation, untreated douglas fir cladding.
Image gallery
Passive House Plus digital subscribers can view an exclusive image gallery for this article. Click here to view