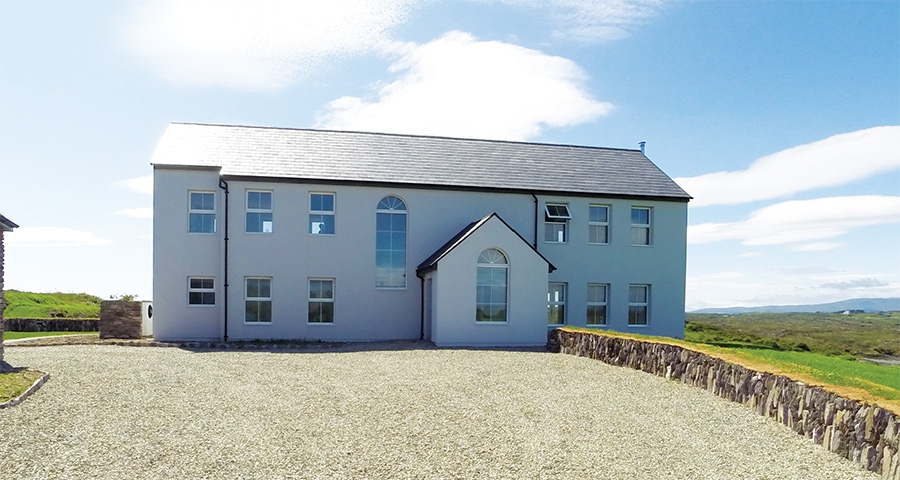
- New build
- Posted
West Cork passive farmhouse mixes build methods
This striking new-build passive house combines a traditional farmhouse form with ultra-low energy performance and a spectacular location – using two different forms of masonry construction
On a remote West Cork island not far from Baltimore sits a new tall, pale grey detached house and separate stone-clad studio that turns out to be a passive house, though it certainly doesn’t look like one. Of course, passive house standards don’t necessarily dictate what form a house should take, but most passive dwellings built in Ireland and the UK to date do seem to be modelled very much along contemporary lines.
“If you look at this building, you’d have to say no,” agrees its architect, James Murphy O’Connor of Cork-based practice Boyd Barrett Murphy O’Connor. But he adds: “Using traditional techniques but being more rigorous about how you’re applying them, you can achieve passive standards. They don’t need to be contemporary buildings.
“With a little forethought at the various stages with regard to the importance of minimising thermal bridging and maintaining airtightness, a very efficient building can be achieved in a traditional building form.”
Having said that, Murphy O’Connor is frank enough to admit that a traditional farmhouse wouldn’t have been his first choice for a design that would meet passive house standards if he had been in his client’s shoes. He believes a lower-key contemporary design would have been his more usual approach given the highly exposed location on the island of Reengaroga, which overlooks a small creek between the River Ilen and Baltimore Harbour.
The clients, however, were insistent on a traditional form, and also that it be built on roughly the same footprint of the original buildings that it replaced — at least partly because it would have been very difficult or impossible to obtain new planning permission for a different footprint. Of course, he acknowledges that, as an architect, his personal opinion will not always be in line with his clients, and that he still has to decide how best to serve their needs.
“In this case, once the decision on the traditional form of the house was taken then it was a case of taking the views, the weather and other factors of the site into account to provide an optimum layout in the form of other farmhouses visible on the island.”
The studio’s insulated foundations and underfloor heating pipework
At least one thing he and his clients agreed on at an early stage was to keep the studio close to, and at an angle to, the main house, thus “reducing the apparent scale of the main house and softening the impact of what is in fact quite a large house at an exposed location”.
The homeowner works in the UK property industry and already came equipped with a robust knowledge of low-energy building design, as well as some foreknowledge of how new EU legislation may look at passive houses in the future.
MVHR supply ductwork installed into top 100mm of floor insulation
“As this was a new build, he was fully on board from the outset with making this house as practically efficient as possible, and to do it in such a way that the result is controlled and calculated to work,” said Murphy O’Connor.
“Passive house standards offer the levels of comfort and energy efficiency to make this happen. It does not leave room for doubt as the physics of the building are calculated precisely.” This included obtaining local climate information so that the build suited its particular south-west coast environment rather than the generic data in the PHPP.
The studio’s walls are of 300mm cavity wall construction with a full-fill pumped bead insulation, so that they could support a natural stone cladding exterior
“The standard data sets in PHPP for Ireland are based on either Birr in the midlands or Dublin,” said Murphy O’Connor. “West Cork, anecdotally, has a much milder year-round climate and the localised data supports this. This in turn allows you model the building physics more precisely say, for example, reducing insulation requirements and hence costs.”
A major contributor towards ensuring that the house had no thermal breaks was the use of a Kingspan Aerobord Supergrund foundation system, which completely isolates the house from the ground. To allow for added loads, Foamglas Perinsul blocks were used to transfer isolated loads to the ground in particular locations, thus minimising the thermal transfer. The main walls are made with 225mm single leaf blocks that were rendered before the application of Sto external insulation and finish. The roof is of traditional construction but with airtight membranes.
The MVHR ductwork is divided between the ground floor, first floor and vaulted ceiling
A similar isolated foundation system was used for the studio building, but the studio’s walls are of wide 300mm cavity wall construction with a full-fill pumped bead insulation, so that they could support a natural stone cladding exterior. Low thermal transfer extruded basalt wall ties were used to minimise thermal transfer across the cavity.
Visually, the contrast between the smooth rendering of the main house and the stone cladding of the studio creates a nice effect, with both buildings enhancing each other. The same stone has been used in the extensive landscaping around the house.
Siga Majpell vapour control membrane protects the building against excessive moisture penetration
In both buildings, the windows are set into the insulation layer to prevent thermal bridging. Holes for services were kept to a minimum and airtight tapes employed at window and floor junctions, with the result that the house meets the exacting airtightness target for passive houses.
Other than a room-sealed Chesney Milan 4 Passive wood burning stove, the house is heated by a Nilan Compact P system. The unit, which combines an exhaust air-to-water heat pump with heat recovery ventilation, supplies underfloor heating in the farmhouse and adjacent studio – via heavily insulated pipes between the buildings – and also provides domestic hot water. The studio’s ventilation strategy uses an Aereco demand controlled mechanical extract ventilation system instead of MVHR.
The ductwork runs for the MVHR system is divided between the ground floor, first floor and vaulted ceiling.
The walls of the main house are externally insulated with 250mm StoTherm EPS with adhesive fixing
“The ductwork is set into the top 100mm layer of the 300mm floor insulation, keeping the gaps in the insulation to a minimum, and cutting it in quite tightly,” said Murphy O’Connor. “All delivery air is to floor boxes and the exhaust air is at high level.”
As well as the traditional style and form, the other notable thing about this build is that the cost was on a par with a conventional build. “The cost of this build is no more than the cost would have been if we were to have used basic but regulatory compliant construction techniques and achieved a BER A2 rating,” said Murphy O’Connor.
Two factors helped. The first was the very simple traditional form of both buildings and the use of traditional building techniques, albeit in a more rigorous manner. The second — and possibly more important – factor to keeping the cost down was the quality work of the contractor, David Evans, with whom Murphy O’Connor has worked with on builds in West Cork over 15 years. As well as being Murphy O’Connor’s first passive house build, it was also a first for Evans, who was keen to be involved.
“He was very eager, and hence getting such a good price, he priced the job well because he wanted to do it. He was also eager to learn about low-energy building,” said Murphy O’Connor.
So the challenge of the build was as much to do with the design as the fact that it was a new experience for both of them, particularly in the need to focus on the small details that are so crucial with passive house builds. “Without that prior experience, you don’t know how critical they are. So we probably over-focused on certain elements of it, particularly in relation to the airtightness.”
Much of it was simply about thinking ahead, but it helped that Evans is “such a conscientious builder”, said Murphy O’Connor, adding that he was willing to learn, get the right advice, ask the right questions about airtightness and even got reps from the various companies down to site if necessary to demonstrate the use of products like airtight tapes. The result was that he returned a successful airtightness pressure test of 0.5 air changes per hour at 50 Pascals at the first attempt.
It sounds like the pair could be even more cost-competitive with a similar build in the near future. “Because we were taking a belt and braces approach to the build, in hindsight there were probably areas where I could possibly have saved a little bit of money by using different methods of construction.”
Although this is the first house Murphy O’Connor has completed that he hopes to have certified by the Passive House Institute, others are now in the pipeline, including another in Cork, one in Co Kerry and an apartment building in Cork City. “People are becoming more aware of what real energy efficiency in construction means, and that is certainly not just applying the minimum standards to get you over the line in terms of regulatory compliance.”
However, he says it’s a constant battle to persuade others that a Building Energy Rating score of A3, as calculated by the Deap software, is not the be-all and end-all of energy efficiency. “The reality is that doesn’t guarantee the comfort levels that a passive house does, and to explain to people why that is, it boils down to the fact that [Deap] calculations are not rigorous enough, they’re too general.
“With a passive house, the calculations are really specifically for that building, for that location. All of the building’s physics are taken into account to a far greater degree than using your standard Deap calculations.”
The house features a Chesney Milan 4 Passive room-sealed wood burning stove
Which leads us to what some might rigidly interpret as the building’s one failing: the fact that the renewable energy supplied by the heat pump and biomass stove in the building doesn’t satisfy the renewables target in the technical guidance document to Part L of the Building Regulations. The Deap calculations came out well short of the target of 10 kWh/m2/yr.
However Murphy O’Connor is philosophical. He argues that even though it doesn’t meet the advised target in the TGD, it meets the requirements of the statutory regulation, which says that a “reasonable proportion” of a building’s energy demand must come from renewables, given that renewable energy systems meet the entire heating and hot water demand, albeit with the heat pump using grid electricity to generate renewable heat. Oddly, part of the problem is that the building was too efficient – Deap credits it with a 70.6% energy reduction compared to 2005 regs, when a 60% reduction is demanded by TGD L. Had it been less energy efficient, the renewable energy systems would have had a higher demand to meet, and would have scored higher.
“If you have a low-performing building you need a higher level of renewables to show a relative energy performance, but if you have a building that doesn’t need much energy input, then you don’t need the renewables — so you don’t meet your target. So you’re actually complying with the legislation but you’re not conforming with the Deap calculator.”
Achieving the more rigorous passive house standard, he says, “is more onerous on the designer and the contractor but results in a better building”.
Selected project details
Client: Gregory & Amanda Besterman
Architect & passive house designer:
Boyd Barrett Murphy O’Connor
Contractor: David Evans Construction & Joinery Ltd
Mechanical contractor, heat pump & MVHR
system: Nilan Ireland
Electrical contractor: Don MacCarthy Electrical
Energy assessor: National Energy Assessors
External insulation: Sto
Airtightness tapes and membranes: Siga
Insulated foundation system & rigid insulation: Kingspan
Mineral wool insulation: Isover Ireland
Thermal blocks: Foamglas, via TIDL
Windows: Munster Joinery
Wood burning stove:
Chesney’s, via The Woodburning Centre
Twin wall flue: Oriel Flues Ltd
DCMEV: Aereco
Additional info
Building type: 266 sqm block-built detached house with external insulation, plus 82 sqm detached studio, block-built with wide cavity construction
Location: Reengaroga, West Cork
Completion date: June 2015
Budget: €440,000
Passive house certification: main house pre-submission; studio fabric built to passive standards but not seeking certification
Space heating demand (PHPP): 12 kWh/m2/yr
Heat load (PHPP): 9 W/m2
Primary energy demand (PHPP): Not yet available
Airtightness (at 50 pascals): 0.5 ACH at first fix, awaiting re-testing.
Energy performance coefficient (EPC): 0.294
Carbon performance coefficient (CPC): 0.296
BER: A2 (43.42 kWh/m2/yr)
Thermal bridging: Fully isolated Supergrund slab system (Foamglas Perinsul blocks used in isolated locations for load bearing), external insulation meeting roof insulation to create a continuous thermal wrap, passive-certified windows in insulation layer.
Ground floor: Supergrund insulation foundation system with 300mm of extruded polystyrene. Nilair MVHR supply ductwork cut in tight runs into top 100mm of insulation. DPM stepping over the ring beam, then mesh and 100mm structural screed containing underfloor heating pipework. U-value: 0.114 W/m2K (same as for studio building)
Walls (main house): Internal plaster, 215mm block, cementitious render and StoTherm Classic K, including adhesive fixing, 250mm StoTherm EPS, cement-free reinforcing render with glass fibre mesh embedded into reinforcing coat & acrylic render finish. U-Value 0.132 W/m2K
Walls (studio building): internal plaster, 100mm blockwork, 300mm blown bead insulation, 100mm blockwork followed outside by 200mm natural stone externally. U-Value 0.113 W/m2k
Roof: 300mm Isover Comfort 32 quilt insulation over and between rafters, Siga Majpell vapour control membrane & airtightness membrane with Kingspan K18 insulated plasterboard underneath. (same as for studio building)
Windows: Munster Joinery passive-certified Passiv uPVC triple-glazed windows. Overall U-value: 0.78 W/m2K Triple-glazed Munster Joinery uPVC oculus and fan light windows. U-value 0.99 W/m2K.
Heating system: Nilan Compact P exhaust air-to-water heat pump with heat recovery ventilation, and supplying underfloor heating in hall, kitchen and bathrooms. Passive House Institute certified heat recovery efficiency of 77%. Plus Chesney Milan 4 Passive airtight wood burning stove with external air supply, and twin wall flue.
Ventilation: Nilan Compact P for the farm house, as per above, and an Aereco DCMEV system for the studio, with BXV extract units in the kitchenette and bathroom.
Image gallery
Passive House Plus digital subscribers can view an exclusive image gallery for this article. Click here to view