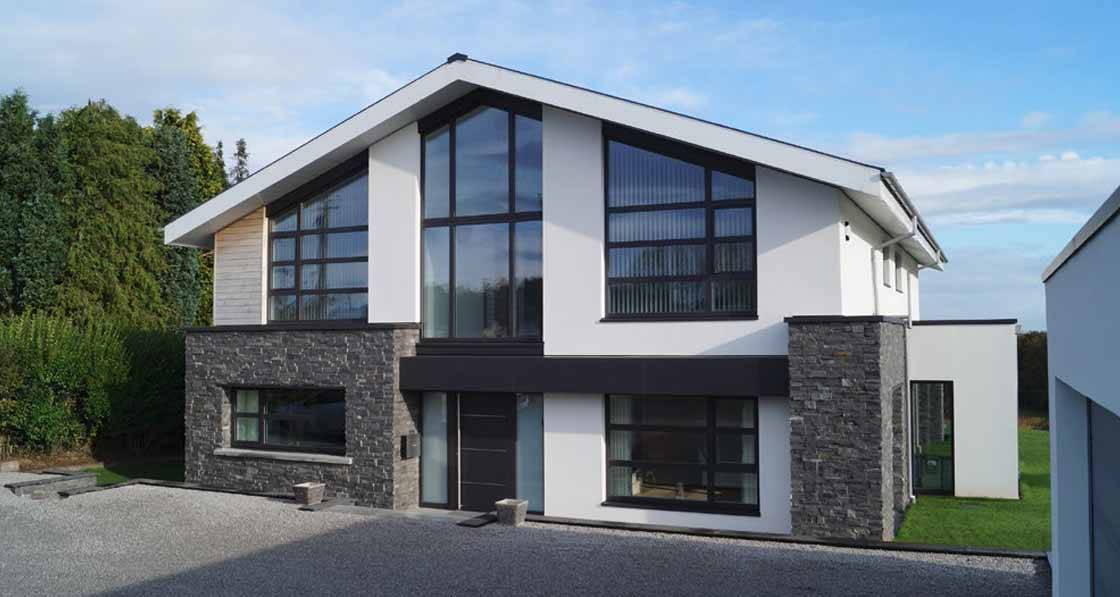
- Marketplace
- Posted
Good design integral for latest MBC passive house
For new self-builders Andrew and Lynne Webster, spending extra time and money on the design stage of their new passive grade timber frame house proved to be one of the best decisions they could have made.
This article was originally published in issue 32 of Passive House Plus magazine. Want immediate access to all back issues and exclusive extra content? Click here to subscribe for as little as €10, or click here to receive the next issue free of charge
Chartered architectural technician Tony Holt, of Tony Holt Design, worked with the couple through a concept design phase, before gradually fine-tuning it into a ‘ready for planning’ drawing.
“At this point,” Andrew commented, “many self-builders opt to head straight into the build phase, but we recognised the value that would be brought by retaining Tony Holt to bottom out the detailed design, despite the additional cost.
“Having watched endless episodes of Grand Designs, one thing screamed out at us – problems seem to happen mainly for people who hadn’t committed enough resources to planning their project fully. Detailed design work tends to force you into looking more closely at the tiniest of details.”
Andrew and Lynne considered various build systems, but ultimately opted for timber frame. “I knew I would be managing the build myself,” explained Andrew, “yet I was acutely aware that I had a full-time job and my time on site would be limited. Building with timber frame gave me two key advantages. Firstly, I could devote whatever time was needed in the weeks and months preceding the build to ensure that everything had been considered and accounted for – I knew to the millimetre what I was going to get! Secondly, I wanted to limit the ‘wet trades’ on site.”
The couple chose MBC Timber Frame Ltd in Gloucester, they say, mainly because their reputation was good both in terms of the quality of their frames and their professionalism on-site.
The couple specified MBC’s passive standard slab with underfloor heating included, as well as their twin wall passive standard frame. Detailed up front planning also helped to ensure smooth installation of the building services and window installation.
“The finished house speaks for itself – we provided a high level of detail to MBC Timber Frame and in return things went pretty smoothly when we came to the all-important erection of the timber frame phase of the project,” Andrew said.
“Even on the coldest of mornings, the triple glazing does very well to retain heat. We did account for adding small radiators in the bedrooms if we ever felt the need, however, we’re now entering our third winter in the house and we still don’t have them.”
No doubt this is due in no small part to the excellent air test results – a measured air permeability of just 0.21 air changes per hour.
A longer version of this case study is available at www.mbctimberframe.co.uk
Related items
-
Material matters - A palette for a vulnerable planet
-
Focus on better buildings, not better spreadsheets
-
MBC offers total passive house envelope solutions
-
Historic Dublin building retrofitted with cutting edge insulation
-
Proctor gains ground with Scottish passive schools
-
Full EPD Certification for Pro Clima airtightness and windtightness products