- Design Approaches
- Posted
Heaven sent
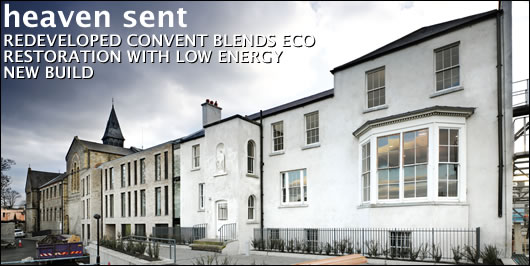
When it comes to redeveloping old buildings, green designers face two choices: replace existing structures with modern, energy efficient buildings or refurbish and avoid the embodied energy and waste of demolition and new construction. Lenny Antonelli visited a redeveloped convent in Booterstown, County Dublin that combines the best of both approaches.
Boasting the rare achievement of aesthetically marrying historic buildings with modern architecture, Saint Anne's, Booterstown is a biomass-heated convent that features five protected structures and two new, low energy extensions.
The convent has a long history. In 1760 a villa - typical of the many built around Dublin Bay at the time - was constructed on the site. The residence was extended to include a ballroom in 1820, while a church was built nearby the same year. The Sisters of Mercy bought the site in 1838 under the direction of founder Catherine McCauley. An orphanage was built, followed by a parish centre in 1860, and further extensions were added over the years.
Dublin-based sustainable architects MCO spearheaded the redevelopment. The firm had previously worked on five other Sisters of Mercy projects, including two profiled in Construct Ireland - the Mater Orchard building on the Mater Hospital campus in Dublin, and the Mount Saint Vincent convent in Limerick.
"Sustainability is a high priority for us," says Sister Anne Doyle.
Doyle previously outlined the Sisters' environmental philosophy when
Construct Ireland spoke to her about Mount St Vincent: “We would want
as Mercy Sisters to live in harmony with the earth and if we don’t
follow that principle when we can, in building new buildings or
renovating, we’re saying one thing and doing another thing. We do
believe we are an integral part of the earth and not a dominant part of
the earth.”
The sisters decided to renovate St Anne's in 2006. Architect Philip
Crowe says the old buildings were riddled with problems. "They had
every conceivable problem. A lot of the plaster internally was rotten
and a lot of the ceilings were sagging."
MCO opted to knock some buildings, including small concrete service and
office buildings dating from 1950 and changing rooms built in 1838, and
construct two new extensions. Knocking certain buildings further opened
a large north-facing space between the villa and the parish centre.
"Originally there was a big courtyard there and we suggested that it
was the best place to put a new building," says Crowe.
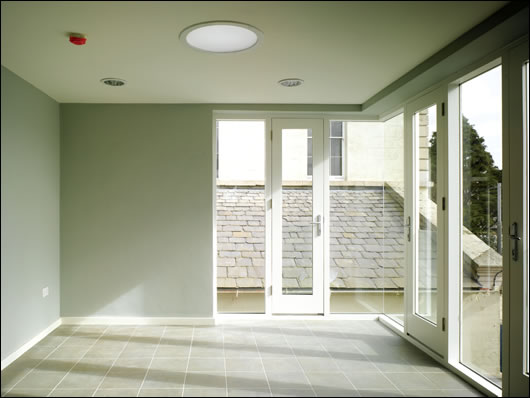
A south facing sunroom in the east extension is one of many communal space throughout the buildings
![]()
The new buildings are fitted with double-
glazed windows that boast a U-value of 1.5 W/m2K for the overall unit. Glazed sections cannot be opened, but accom- panying timber panels can |
The extension that now fills the space is home to the main educational and residential facilities at St Anne's. "It's north-facing, which is one of the challenges of the project," Crowe says. To counter the orientation, and the overshadowing of surrounding buildings, a light-well brings sunlight from the roof to the floors below, helping to naturally illuminate the interior.
The chalky brick exterior of the north extension is designed to fit seamlessly with surrounding buildings, complimenting both the granite brickwork of the parish centre and the newly lime-plastered villa. "Hopefully the new building will sit quite well and not look too intrusive, but at the same time it's a fairly modern design," says Crowe.
The shape of the building was also designed to compliment the historic buildings - the main elevation of the north extension is the same width as the original villa, while an angled wing of the building mirrors the old ballroom extension.
MCO specified an unusual spin on cavity wall construction for the building, with brick externally and 240mm poroton block - a type of fired clay with lower embodied energy than concrete - internally. The 120mm cavity is full-filled with Rockshield, a form of rigid rockwool insulation, and has a U-value of 0.2 W/m2K.
St Anne's is MCO's first poroton project. "The builder was cautious about using it at first I think," Crowe says, "but they loved it once they started. They suddenly realised this is something they could do, and it actually cuts out labour, and it's quite a nice material. And then they love the fact that they can break into it to get their conduits in to make adjustments."
MCO specified a different wall build-up for the east extension - 240mm
poroton block finished with 120mm of StoTherm Classic, an expanded
polystyrene (EPS) insulation and render system. The walls have a
U-value of 0.19 W/m2K .The east extension houses kitchens, bathrooms
and a sunroom, one of many communal spaces in the complex.
But why use two different wall systems? "The conservation planner was
very insistent that the east extension wasn't a brick building," says
Crowe. "The buildings around it are rendered. The church is rendered,
the villa is rendered, the east wing is rendered, so this should be
rendered too. We decided to do it in a very dark colour so that it
receded."
"We spent a lot of time choosing the external render system," Crowe
continues. "The Sto render system costs slightly more but has the major
advantage of being quite flexible, it will move itself and doesn't have
any expansion joints. It would have been a shame to have expansion
joints and a number of the systems we looked at did."
Preventing cold bridging was key in the new buildings. "External
insulation [on the east extension] is the most brilliant way of
preventing cold bridging. The cold bridging details in the cavity of
the north extension are more complicated, but it's just a matter of
rethinking certain details. Sometimes you may have to make a compromise
in terms of how it looks, but ultimately it's about making sure you
have thermal breaks."
The east extension provides disabled access to the convent. "The
problem with Georgian buildings like the villa is that they tend to
have steps going up to them," Crowe says, "and it's quite difficult to
get wheelchairs in. So we've used this space [the east extension] which
is slightly hidden away. It doesn't compromise the protected structure
at all."
Both extensions boast 100mm deep green roofs planted with sedum, a
small herbacious plant. The roofs are insulated with 140mm of
Paratorch, a rigid urethane insulation. "Sedum is ideally suited to
rooftops because it's very drought tolerant, and sedum roofs are
generally low maintenance," says Brian Conroy of Moy Materials, who
supplied the roofing system. "You feed it in spring and in autumn after
flowering has died back a little you have a second visit to remove any
unwanted plants."
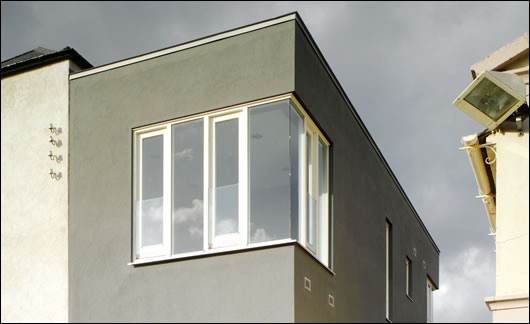
The new east extension was painted black in order to visually recede and draw attention to the surrounding historic buildings
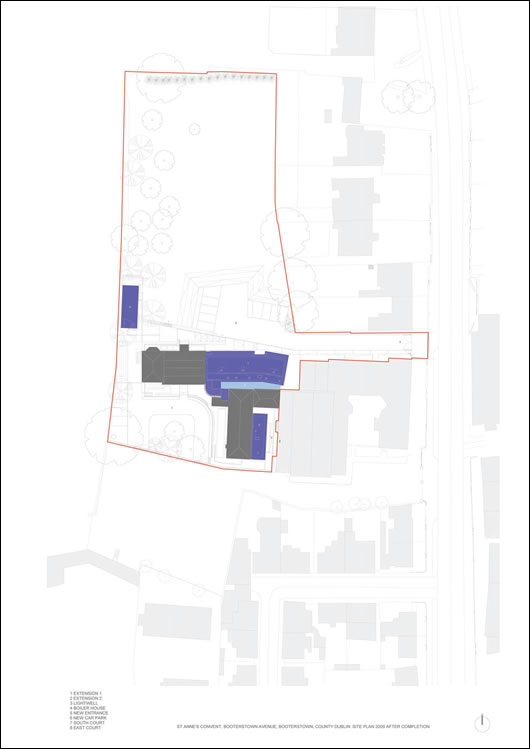
An architect's drawing of the site, showing new (blue) and historic (grey) buildings
Conroy points out the various advantages of green roof. "If you have a
green roof it can attenuate a large volume of water. At Dublin Airport
the rainfall recorded on 9 August, 2008 was 36mm per hour, which was
quite an event. A sedum blanket roof, if it were dry beforehand, could
have absorbed that rainfall for an hour and 20 minutes before water
started to fall off the roof. Green roofs can act as hydraulic brakes
for a city."
Conroy continues: "Also, if you install a green roof you're protecting
the waterproofing from UV radiation. If you protect it from UV and
extreme temperatures you prevent drying and cracking. And not only do
you get a thermal resistance from it, but it cuts down massively on
solar gain, and if you can get that down you cut down on the need for
air conditioning."
The new buildings at St Anne's are fitted with double-glazed,
argon-filled windows with low e-coatings and an overall U-value of 1.5
W/m2K, supplied by McNally Joinery. Glazed sections in the north
extension cannot be opened, but accompanying timber panels can. Crowe
explains: "The opening sections are timber panels so you reduce the
amount of frame in the glazed part. And that's partly aesthetics
because you're sitting next to a building that has very fine timber in
the joinery, so if you're going to have a modern opening section with
glazing it's going to be very clunky and chunky. Also, you lose most of
your heat in a window through the frame, so if you can reduce the frame
you're doing well."
"The proportion of the windows is obviously to try to sit well with the
tall large windows we have throughout [the historic buildings]. The
proportions are quite important. And with tall thin windows you get a
much better spectrum of light."
Heat recovery ventilation units service most of the complex, with the
exception of certain rooms in the villa. "We couldn't get into the
ceilings there [to install ventilation ducts] as they were all original
ceilings that were sagging, but we did screw the ceilings back up to
the joists."
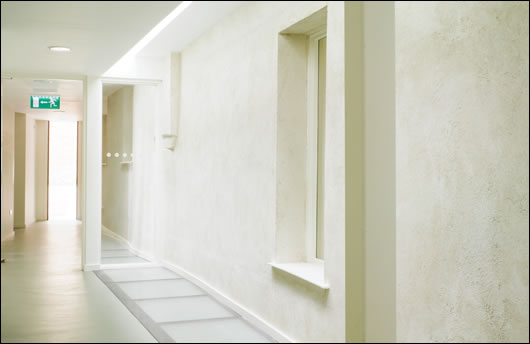
A light-well in the north extension brings sunlight to the floors below, helping to illuminate the interior of the building
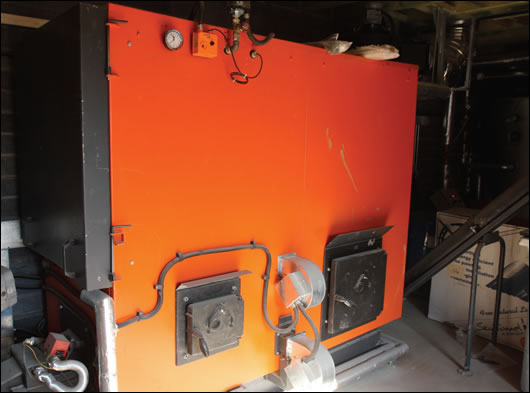
A 92 per cent efficient Heizomat wood pellet boiler heats both new and old buildings
Lindab Ireland supplied five Vent-Axia HR800 HRV units, which are 70 per cent efficient at recovering heat. Crowe considered using Dwell Vent, an innovative passive ventilation system previously featured in Construct Ireland, but ultimately opted for mechanical ventilation. "We've used the Dwell Vent system a number of times and found it very good, and it works well and it's passive, but because the bulk of the windows here are north facing you're not getting any solar gain, and that system works best when you get a bit of solar gain. We did a Dwell Vent simulation, and it just wasn't working particularly well for this building, so that's where the decision came from to go for mechanical ventilation with heat recovery."
The system appears to be working well: "We had a meeting with all the nuns recently, and the room felt fresh the whole time. I was quite conscious of it. Whatever speed it's working at - and it's at quite a low setting at the moment - it's working very well. It's probably fairly unusual to have controlled ventilation in a protected structure in Ireland. You can only put it in if you have a building that has a fairly robust fabric and that you can get the ducting in the floors or up the walls."
Despite the age of the original buildings - and the fact that conservation rules prohibited their walls from being insulated - lime rendering and window sealing ensures they are reasonably air-tight. "Lime render is excellent for air-tightness, and masonry is good for air-tightness generally. As you walk from the new buildings which are completely warm and comfortable to the old buildings there's a slight change in temperature, but it's only very slight," Crowe says.
Colm McCabe of John O'Connell architects, the project's conservation architects, says re-rendering the old buildings was crucial. "The cement-based render was cracking and causing damp. That was removed by hand, literally with a hammer and chisel, and all re-rendered with a lime-based render."
PVC windows in the villa were replaced with timber-framed sash windows, supplied by Thomas Mellot Windows. Double or triple glazing wasn't allowed in the protected buildings. "I personally don't see it as a massive problem as long as we get the frames absolutely air-tight," Crowe says. "Most sash windows lose their heat by the fact they have have huge holes in them. The other thing to do is secondary glazing, but conservation officers are reluctant to allow it."
The ground floor throughout the old buildings was gutted. "The whole of the ground floor is new. It had concrete slab when we came, like a modern concrete slab, but that just wasn't sufficient, and water was coming up through it, so we had to dig it all up and dig down. The damp proofing is actually not by render, it's by electro-osmosis. There's a little electrical current going around which basically repels the water to prevent it from rising up." The refurbished floors were insulated with 80mm of Kingspan's Styrozone expanded polystyrene (EPS) insulation. "We would have liked to use more but excavation costs are very high for old buildings," Crowe says.
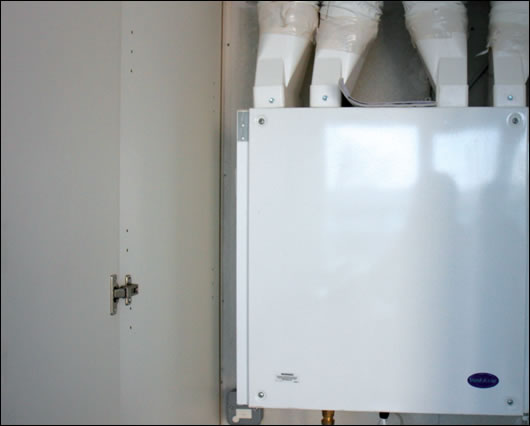
Five Vent-Axia HR800 HRV units service the buildings
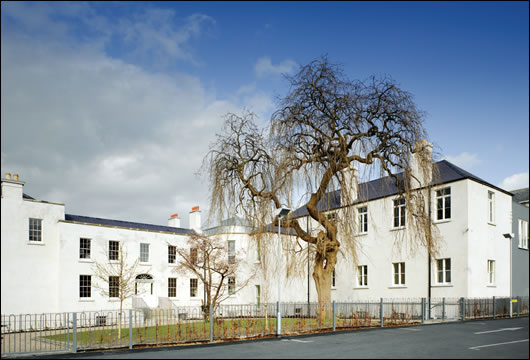
Historic buildings at St Anne's were re-rendered using a lime-based render
MCO insulated the roofs of the buildings with Rockwool - between 150mm and 300mm depending on the exact location - though sections where internal rooms go right up into the roof pitch couldn't be insulated. A boiler house was also built, housing a 92 per cent efficient Heizomat 200kW wood pellet boiler to heat both new and old buildings. Low surface temperature radiators distribute heat throughout the buildings. "Underfloor heating sometimes isn't great for older people,” says Crowe. “And we were able to put low surface temperature radiators everywhere. The response time is also quite important, and underfloor heating isn't always brilliant when it comes to response time. The other thing about underfloor heating is that older people really like it when they know where the heat is coming from."
Two gas-fired boilers act as a back-up heat source. Solar thermal and PV were ruled out for the moment, but will be considered in future. "We absolutely thought about it, and it could be something they could add at a later date. I suppose whenever you're investing so much money in a wood pellet boiler, you need to get the best value you can out of that. And actually that roof is overshadowed at certain times of the day, so it wouldn't be perfect for solar, though it's still pretty good."
While St Anne's has few green bells and whistles, certain features make it stand out from an environmental perspective: the care taken to restore and reuse old buildings, the clustering of the buildings, the energy efficiency of the new ones, and the use of natural, low embodied energy materials - from wood pellets for heating to the poroton, lime and the green roof itself.
Items including floorboards, granite rubber, cills, windows and doors were also recycled and reused on site. All lighting is low energy CFLs or LEDs, and energy efficient appliances were specified throughout. Ecoblock - a permeable paving system that allows grass to grow while providing support for vehicles - was also used on the grounds. Easyscreed, a self-levelling liquid screed manufactured from pulverised fly ash was used on the the basement floor. A by product from pulverised fuel power stations, PFA displaces the use of Portland cement in the screed. Similarly, Ecocem’s ground granulated blast furnace slag – a by product from the steel smelting process – made up circa 50 per cent of the mix in all concrete pours including the entire basement ground floor slab of all buildings, the lift shaft and capping to retaining walls.
Conservation was clearly a key part of the re-development. As well as paying attention to the appearance of the historic buildings, MCO aimed to maintain as much of the original fabric (both visible and hidden) and to retain the internal pattern of rooms. Ceilings in the villa have been retained and repaired, while structural timbers, floorboards, joinery, chimney and leadwork all underwent major conservation works.
"[The old buildings] were totally overhauled, they hopefully don't look it but they've had a huge amount of detailed work done on them," says Crowe. "We had a very good foreman on the project, PJ Smith, who has a lot of experience dealing with old buildings, and we had a conservation architect as well...The chimneys had to be reconstructed because they were falling, but they're all blocked off so there's no heat loss."
Crowe mentions ‘Energy efficiency in historic buildings’, a recent conference organised by the Irish Georgian Society that he attended. "One of the speakers [Dr Gary White, Crichton Carbon Centre] reckoned his research showed that we're all totally underestimating the embodied energy of building. For example, the energy involved in getting rid of buildings is vast. So I suppose one major plus point of this is that we have kept these buildings."
The clustered form of the complex has environmental pros and cons. "You're inevitably going to get a dark building in the middle of the plan. But you leave more land for other uses and you're reducing heat losses and sharing heat a lot more," says Crowe, who points out that the Sisters’ way of life is inherently green. "They share everything. It's a very sustainable way to live."
Though the Sisters had only just moved back in as Construct Ireland went to print, Sister Anne Doyle says they are quite impressed with their redeveloped home. "It's much more comfortable, and it's more spacious, and it's sustainable, which is something we're very anxious to promote - to cut down on energy loss. It's a comfortable, healthy space."
Selected project details
Client: Sisters of Mercy
Architects: MCO Projects
Contractor: Allen & Smyth Constructions
Conservation architects: John O'Connell Architects
Archaeologist: Irish Archaeological Consultancy
Biomass boiler: Clearpower
New windows & doors: McNally Joinery
Floor insulation: Energy Savers
Poroton block: Formula Building Technologies
Basement floor screed: Jerry Beades Concrete
GGBS: Ecocem
New sash windows: Thomas Mellot Windows
Heat recovery ventilation: Lindab Ireland
- Articles
- Design Approaches
- Heaven sent
- low energy new build
- green design
- embodied energy
- biomass
- poroton block
- sto therm
- Vent-Axia HR800 HRV
Related items
-
New embodied carbon rules for large London projects
-
Coasting home - Beautifully designed Hampshire home breezes past passive standard
-
Steeply sustainable - Low carbon passive design wonder on impossible Cork site
-
Focus on whole build systems, not products - NBT
-
Achieving NZEB event in Cork hears of embodied carbon plans
-
International - Issue 29
-
Passive Wexford bungalow with a hint of the exotic
-
The House of Tomorrow, 1933
-
1948: The Dover Sun House
-
The dazzling Dalkey home with a hidden agenda
-
The stunning low energy seaside home that's built from clay
-
Mayo passive house makes you forget the weather