- Design Approaches
- Posted
Hempcrete retreat
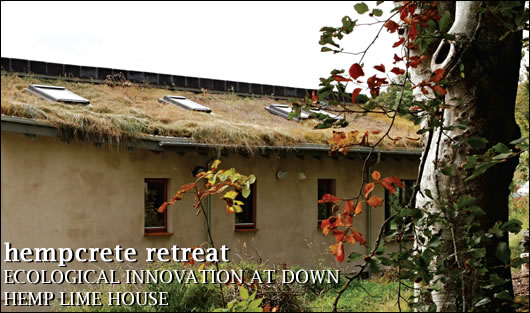
No matter how energy efficient a building method is, constructing a house from scratch will always cause some damage to the environment - but what if a building material could absorb more carbon than it causes to be released over its life cycle? Lenny Antonelli visits a hempcrete house in Co. Down that seeks to trial this innovative method of buildingIf someone said you could build a sturdy, energy efficient home with hemp and lime, you might call them mad. But as more architects and builders demand materials with both a low carbon footprint and high energy performance, hemp-lime construction – also called hempcrete – is growing. It's hardly a surprise that when it came to building a house for his father, professor of architecture Tom Woolley – one of the UK's authorities on green building – plumped for hempcrete.
"The idea was to trial it," says Woolley, who built the house with his partner Rachel Bevan, also an architect. "As architects we wouldn't specify it for clients without having done it ourselves." The couple built the bungalow beside their own home in a rural corner of Co. Down. They hope to entice Woolley's father from his coastal home in Anglsey, north Wales, to live closer to the pair.
Woolley and Bevan built the walls by mixing hemp shivs – the woody core of the plant – with a pre-formulated proprietary lime binder, then adding water to create a sticky crumble. Lime Technology supplied the radical hemp and lime system for the mix – two bags of lime for each bag of hemp. "Recently they've reckoned you could probably use about one and a half bags of lime to one bag of hemp," Woolley says.
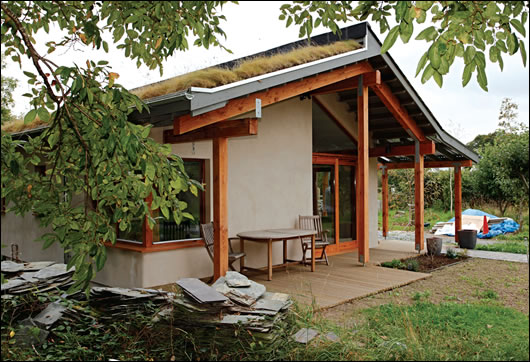
The roof features grass roofing to the rear and a sloping slate finish to the front. The slate roof is designed to be "polite" to nearby vernacular bungalows
The mix was dropped into timber shuttering that was attached to an FSC-certified softwood timber frame. The builders then pressed down the mix, taking care to avoid over-compressing it and forcing air out, which would reduce the hempcrete's ability to insulate. The shutters were removed after 24 hours and the hempcrete was left to dry – because the house was built over winter this took two to three months, but much quicker drying times are possible in summer. Lime render was then applied over the hempcrete both inside and out.
Once dry, hempcrete makes an impressive insulator – tests at the UK's National Physical Laboratory indicate a U-value of 0.23 W/m2K for Woolley and Bevan's 300mm build. While this figure isn't ground-breaking, Woolley says the thermal performance of hempcrete can't be measured by U-value alone. The thermal mass of the material - its ability to absorb, store and release heat - means it can naturally balance out temperature fluctuations and maintain a comfortable indoor temperature. A study by the BRE also found that hempcrete performs better than its calculated U-value.
"Once you start looking at these things you discover that the current method of assessing thermal insulation is so crude," says Woolley. "[When testing insulation] you shove a piece of material in a hot box, and you're testing it in a completely artificial situation."
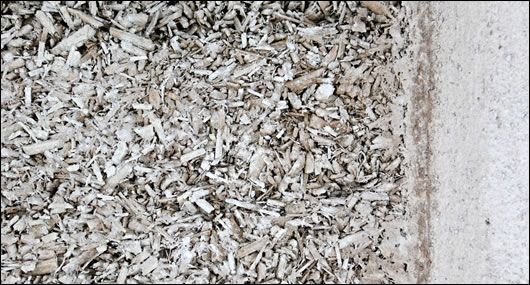
A small section at front of the house was not rendered with lime, leaving the set hempcrete mix exposed to show to those interested in learning about the method
Research suggests using less lime binder to reduce the density of a 300mm wall could boost its U-value to 0.21 W/m2K or better. Lime Technology say 0.14 W/m2K or lower is possible with a 500mm wall. Keen to test a thinner build, Woolley and Bevan opted for a 300mm build.
The house had yet to be tested for air-tightness when Construct Ireland went to print, but in their book Hemp Lime Construction, Woolley and Bevan say the simple, monolithic nature of a hempcrete wall - it's one solid material all the way through – lends itself to excellent air-tightness. With no need for taped membranes in the walls themselves effort can be focused around windows, doors and other junctions. There is also little risk of thermal bridging, because the timber frame is buried in the hempcrete mass.
Hempcrete performs superbly in Ireland's damp conditions, Woolley says. "The walls are capable of regulating the humidity from inside the building or outside, but that doesn't disadvantage the material."
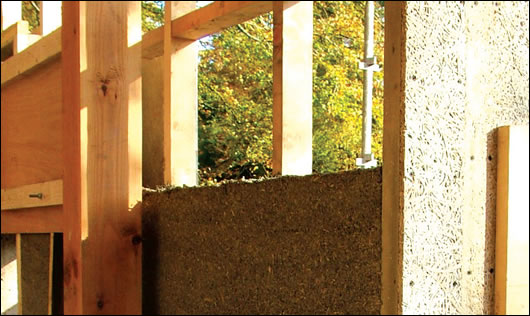
Hempcrete walls during construction
Despite using traditional materials, hempcrete is a fairly new technology. It developed in France during the 1990s, initially as a substitute for wattle and daub in the restoration of old buildings. Some innovative architects and builders then started to use it for new buildings, and it spread from there.
The Suffolk Housing Society built two hemp-lime houses as part of a social housing project in Haverhill in 2001. A study by the Building Research Establishment found the two houses – despite being just 200mm thick – had similar structural and thermal performance to conventional cavity-wall houses on the site with 100mm rockwool filled cavities.
Lime Technology upgraded their Oxfordshire office using their own Tradical hemp-lime formula. The firm removed the original cavity walling, installed a secondary timber frame to the steel-framed building and spray-applied hempcrete to permanent shuttering that was fixed to the timber frame. After four days they had created a 500mm wall with a calculated U-value of 0.14 W/m2K.
Last year, the Orwell Housing Association completed a scheme of 22 hempcrete social houses and four flats in Suffolk, again spraying a hempcrete mix on to a timber frame. Lime Technology have over 300 houses on the cards for next year - most in social housing projects - while two hempcrete homes are under construction at the eco-village in Cloughjordan, Tipperary.
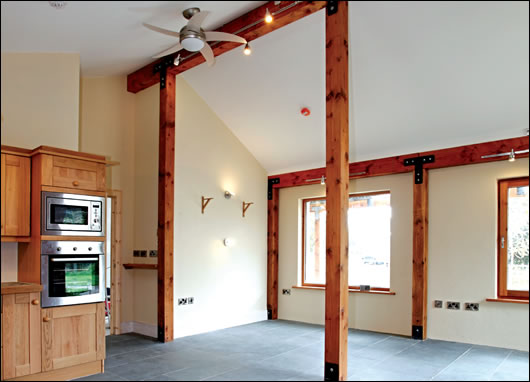
The main post and beam structure, seen here in the kitchen-cum-living room, is locally sourced douglas fir
So what can hempcrete offer that conventional methods can't? In an analysis published in Construct Ireland last year (Vol 4, Issue 2), architect Joseph Little found that hempcrete timber frame walls have a negative carbon footprint - the hemp absorbs more carbon dioxide while it grows than is embodied in the wall materials. Choosing hempcrete saves five tons of carbon compared to timber frame and eight tons compared to cavity block, Little found. Tradical's lime binder does contain some cement – which has a high carbon footprint – but it's a minority ingredient. Calculating hempcrete's exact carbon footprint exactly would require a painfully detailed analysis, but it's clear hempcrete is as low carbon as building materials come.
Some environmentalists worry whether too much land will be needed for hempcrete to take off – about one hectare is needed to build a typical hempcrete house. Surging demand for biofuels last year reduced the amount of land devoted to growing food and pushed food prices up by 75 per cent, causing a crisis in many developing nations. Hemp can mount a strong defence here though: it can be grown in rotation with food crops, and as a breaker between cereals and potatoes. It also surprises weeds, nourishes the soil and produces high yields. Woolley and Bevan estimate building all new houses in the UK with hemp-lime would require one per cent of the country's agricultural land.
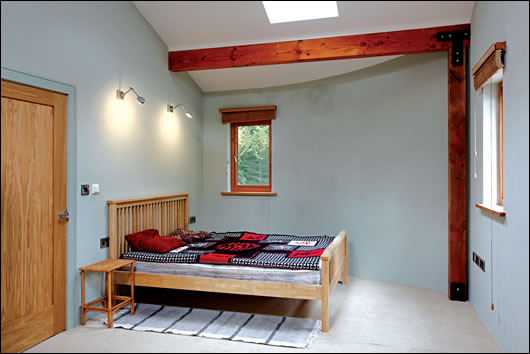
The hempcrete walls were finished with a lime render inside and out
While hempcrete is typically applied as an on-site mix, blocks are available too. These may be denser than a typical mix though, so while they don't perform as well thermally they can provide more thermal mass. Hemp-lime can also be used to insulate floors and roofs, with a lighter mix (using less lime) typically used for roofing and a denser mix for floors.
Woolley and Bevan didn't use it for either though. They installed 250mm of recycled polystyrene in the floor, sourced mostly from a demolished cold store in Belfast. Polystyrene surrounds the perimeter of the ground slab too, helping to prevent cold bridging, and 300mm of sheep wool insulation was installed in the roof. "We could have done the roof in hemp and lime but so far the only Local Authority Building Control approval is for walling," Woolley says.
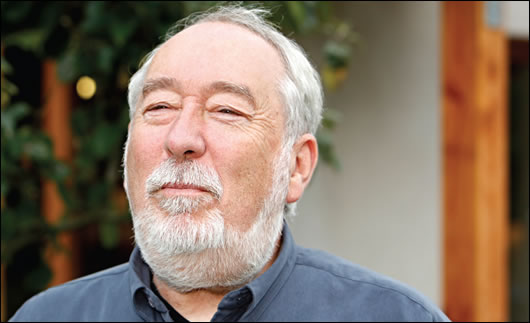
Professor of architecture Tom Woolley warns against taking an amateur approach to building with hempcrete
The couple opted for a sloping roof with a slate finish to the front and grass roof to the rear. The slate is designed to be "polite" to other vernacular cottages in the area, and the grass – installed over secondhand carpet, an EPDM membrane and plywood decking – to merge the house with the landscape. "In fact it just attracts attention rather than anything else," Woolley says.
The depth of soil in the grass roof should have been greater, he says – the climate is getting drier in the north east and shallow roofs are no longer sufficient to hold enough water. "We could have done with a shallower pitch [too], I think the water's running off too fast. But it's not really a problem because we know sooner or later it'll rain for weeks."
The couple chose to heat the house using a 28kW LPG high efficiency Vaillant condensing combi boiler, with hot water distributed via underfloor heating. They installed three separate heating zones – the bedroom, sitting room-cum-kitchen, and bathroom and hallway – and Woolley's father will control the temperature in each with a simple thermostat. The house was designed to accommodate a solar thermal system in future – a duct for pipework through the roof was left, as was space for a large buffer tank.
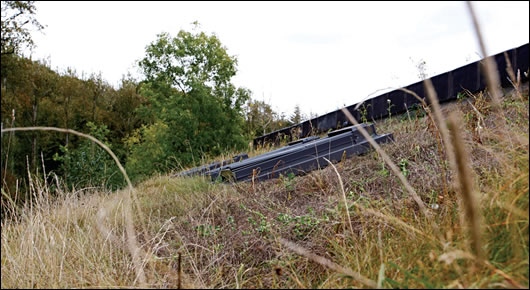
The grass roof
The main post and beam structure is locally sourced douglas fir. The porch is protected by a galvanized steel roof, which Woolley says has a lower environmental impact than powder-coated steel. The zinc that coats the galvanized steel is sourced from an Irish mine, and 99 per cent of galvanized steel is recyclable. The steel roof shades the south-facing facade in summer while letting the low winter sun in to illuminate the compact interior. Triple-glazing was deemed too expensive, so Woolley and Bevan opted instead for double-glazing with a recycled pitch pine frame and low-e coating, sourced from a local joinery.
Work on the house was coming to an end on the bright Autumn day that Construct Ireland visited. Experimenting with hempcrete was one of the main reasons for the project – so what are the conclusions?
Some lessons have been learned: keeping the form of a hempcrete house simple is crucial to keep the shuttering simple. And using a standard plastic shuttering system rather than a custom timber one would have made the job quicker. The amount of timber needed could potentially be reduced too – Woolley reckons that with further innovation, hempcrete could even be self-supporting in future. "We reckon we could reduce the timber even more – the timber frame here is doing little more than providing a ground for the windows to fix to.”
Woolley warns against taking an amateur approach to hempcrete. He's received phone calls from self-builders who have "mixed up any old lime and chucked it in with a bit of hemp," only for disaster to follow. Those who are careless with their mixes often find that if they open a section of wall, the lime is still a dry power inside. "You've got to know what you're doing and do it carefully, taking advantage of the extensive R&D carried out by Lime Technology," he says.
The message is clear: built right, hempcrete is an energy efficient, low carbon, structurally sound method of construction. But what about the cost? The hempcrete houses built at Haverhill in 2001 cost £526 per square metre, compared to £478 for the cavity wall homes. In June, the BRE unveiled their Renewable House, a standard three bed hempcrete house built at the National Non Food Crop Centre for just £75,000. Here was proof that hempcrete could be used to build affordable homes on a large scale. "It's absolutely replicable if builders weren't so stuck in their ways of thinking . All it takes is somebody to realize this can actually work," Woolley says.
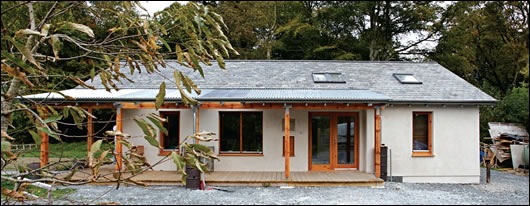
The porch is protected by a galvanised steel roof, which provides shading for the south-facing façade in summer. Woolley says galvanised steel is more environmentally friendly than powder-coated steel
Lime Technology's Mike Eberlins says hempcrete is particularly cost-effective against concrete and timber frame when builders are trying to meet high environmental standards. As building standards get stricter, the financial appeal of hemp lime can only grow. Shuttering is a more cost-effective method of application than spraying, Eberlins says.
One way for enthusiastic self-builders to keep costs down is to do some building work themselves – hempcrete is ideal for this. "One of the things I realized doing this project is how easy it is, provided people are sensible and do it properly using proper professional advice from architects who are familiar with the method," Woolley says.
For green minded self-builders, architects and developers, choosing construction methods that are cost-effective, durable, energy efficient and ecological is a balancing act. Hempcrete may go furthest in meeting these demands. "We've been trying to find a method of building that's low carbon and energy efficient, simple and affordable, that uses natural materials," Woolley says in a video interview with SustainAndBuild.co.uk (Video available at tinyurl.com/hemplime), a cross-border green building education initiative. "Hemp and lime mixed together seems to answer all of those needs."
Related items
-
Towards greener homes — the role of green finance
-
Steeply sustainable - Low carbon passive design wonder on impossible Cork site
-
Ecological brings Lime Green plasters to Ireland
-
Focus on whole build systems, not products - NBT
-
International - Issue 29
-
Passive Wexford bungalow with a hint of the exotic
-
New research finds air pollution particles in human placentas
-
The House of Tomorrow, 1933
-
Diasen thermal lime plaster features on RTE renovation
-
1948: The Dover Sun House
-
The dazzling Dalkey home with a hidden agenda
-
Mayo passive house makes you forget the weather