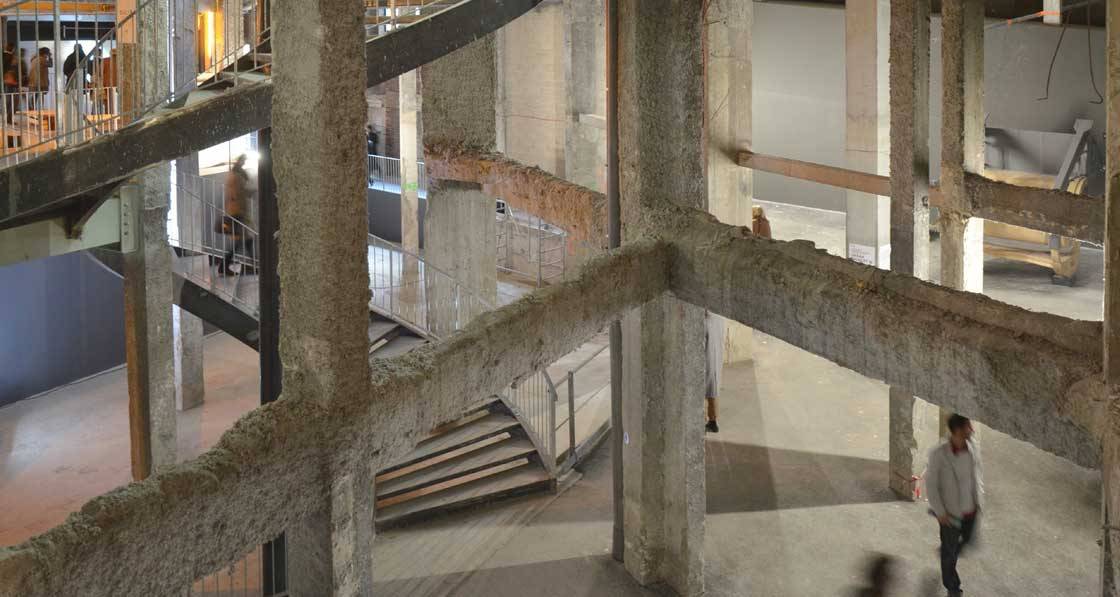
- Blogs
- Posted
Cutting embodied carbon: doing more with less
We won’t be able to reduce the embodied carbon of construction fast enough just by switching to lower carbon materials, says Pat Barry of the Irish Green Building Council, so we urgently need smart design that allows us to build with less, and to create a genuine circular economy for building materials.
This article was originally published in issue 39 of Passive House Plus magazine. Want immediate access to all back issues and exclusive extra content? Click here to subscribe for as little as €10, or click here to receive the next issue free of charge
If everyone on the planet lived like the Irish, we would need 3.1 planets, ahead of the UK who only need 2.6 planets. The recent interest in embodied carbon in construction and climate action is hence welcome. Yet, there is a danger in focusing exclusively on carbon intensity per square metre.
The Irish Green Building Council (IGBC), in its submission to the government’s consultation for its revised climate action, pointed out that Ireland will increase levels of home construction from 21,000 to 30,000 a year. Economist Ronan Lyons suggests the figure is closer to 50,000 a year. This will lead to a massive increase in carbon emissions and resource consumption from the construction sector, when the country is supposed to be cutting its emissions by 51 per cent in eight years.
In simple terms, embodied carbon equals the carbon intensity of a material multiplied by the quantity of that material. Reductions in the carbon intensity of materials won’t happen fast enough to reach our target, so we also need to focus on quantity. That means housing more people with the least quantity of resources and material use possible.
Circular thinking
In a climate emergency, provision of dedicated parking for a new home is now as daft as providing a chimney.
Circularity in construction is one key strategy. The goal is to retain value for as long as possible, through reuse, restoring, regenerating, recycling, circulating and re-manufacturing — and most importantly through co-operation. This encompasses urban planning, buildings, infrastructure and materials. It means breaking the linear make-break-waste model and replacing it with one where we can extract the maximum value from every product for as long as possible.
Car sharing schemes like GoCar and Yuko demonstrate that a product as a service can also result in major carbon savings for the built environment. According to Berkley university research carried out in North American cities, one shared car could in some cases replace the need for up to 11 other vehicles.i This could allow local authorities to relax minimum car parking rules for new developments, and thus reduce the need for carbon-intensive underground car parks. Not many incremental changes to building regulations can beat the carbon savings of both eliminating the cars and the basement! In a climate emergency, provision of dedicated parking for a new home is now as daft as providing a chimney.
Circularity at the urban scale
Well-designed villages, towns and neighbourhoods offer the advantages of the circular economy, allowing efficient use of shared space, infrastructure, materials and energy. Densifying existing towns means reusing the same infrastructure more efficiently. A building properly designed and located should last 200 years and the infrastructure even longer. Dublin’s Phoenix Park tunnel was built in 1877 with manual labour, and is now proposed to be repurposed as part of a new metro, saving tens of millions of euros.
We lost sight of this over the past 50 years and abandoned living space in our villages and towns often in favour of remote oversized homes, usually built when a household is starting a family. These often have maximum occupancy for only 18 to 20 years and are then largely underutilised. Enabling first-time buyers to refurbish a derelict building in a local town or village instead would save substantial emissions from embodied carbon and transport, bring towns and villages back to life, and free up scarce construction material and labour. This requires a reversal of traditional financial and government policy, which prioritises the purchase or construction of new homes, to instead incentivise the renovation of underused space.
Building in flexibility
To extend the life of our buildings, they must be designed to adapt to other uses. This means thinking through floor-to-ceiling heights, location of sanitary services, stairwells, circulation, and floorplate depth, to test whether adaptation to other uses is possible. This can even mean trade-offs in increasing initial carbon emissions to extend the useful life of the building. Design of simple structural grids without obstructions allows better use of space and maximises furniture layouts.
Within the Irish Green Building Council’s Home Performance Index certification, indicators for universal design ensure that homes can continue to be used throughout a person’s lifetime even if they are subject to a temporary mobility impairment.
Innovation to integrate a range of shared social spaces or shared guest bedrooms and workspaces within housing are also needed.
This would allow families to temporarily expand their space as needed, rather than building redundant space into each home. This may mean a move away from standard models of ownership or rental toward hybrid models that guarantee tenure and security. As your family grows you occupy more space and you pay into the pot, then when your family contracts as children leave you receive an income when you give up this additional space. No space is wasted.
The flat pack build system by Irish offsite specialist Glavloc, which lends itself towards disassembly.
Designing for disassembly & product as a service
Where a building inevitably will have a short life span, it is essential that every component is designed for disassembly. The concept of buildings as material banks imagines them as temporary material warehouses, where a product should come out of the building at end of its life with at least the same value it had when it went in. But this requires knowing what is in the product, and having digital material passports for each component.
It also requires thinking through how each component is assembled and conceiving the different layers of the building as having different lifespans, from the core structure to the cladding to the internal finishes.
Making circularity measurable & regulated
To transition to circularity, we need definitive quantitative and qualitive indicators. Level(s), the EU frameworks for sustainable construction, sets out several indicators including design for adaptability, design for deconstruction and disassembly, and measurement of waste and overall resource efficiency. Simple indicators such as the ratio of usable area to gross area tell us how efficiently a building is designed, but more complex evidence may require demonstrating alternative plans of the building converted to other uses, eg, an office block to say a hotel or school.
London is the first city to require circularity statements for developments over 5,000 square metres at planning stage. This requires the design team to think through the implication of their design to minimise resource use looking at all the indicators outlined above, including design optimisations, adaptability, and disassembly. The city has developed a series of useful primers on circularity, which are available at tinyurl. com/CircularLondon.
Practical implementation of circularity
As part of the CircularLife EPA-funded project, IGBC will be testing the use of circularity indicators and is inviting design teams to participate in workshops, including one with Dutch architects and “urban miners” Superuse Studios, to develop circularity strategies for their live projects. Regenerate is one cloud-based tool developed by the University of Sheffield’s Urban Flows Observatory that the IGBC intends to trial. It takes a design team through a series of steps from early strategic design onwards through a series of questions and prompts, covering every concept outlined above, scoring the circularity of the building, and measuring the degree to which strategies have been integrated.
IGBC’s review of circularity indicators is intended to feed back into guidance on the integration of circularity in development plans and public procurement. IGBC will also pilot an online materials exchange platform with a Dutch partner, creating material passports for materials coming out of demolition, and finding potential users using blockchain. We are also rolling out a series of webinars on circularity across the autumn. These are available on our online learning hub at www.igbc.ie.
None of this is easy! The solutions are not quite there yet but by switching to ‘think circular’ mode in our construction brains, hopefully rapid innovation will follow. This may yield faster results than just incremental reductions in per-square-metre embodied carbon.