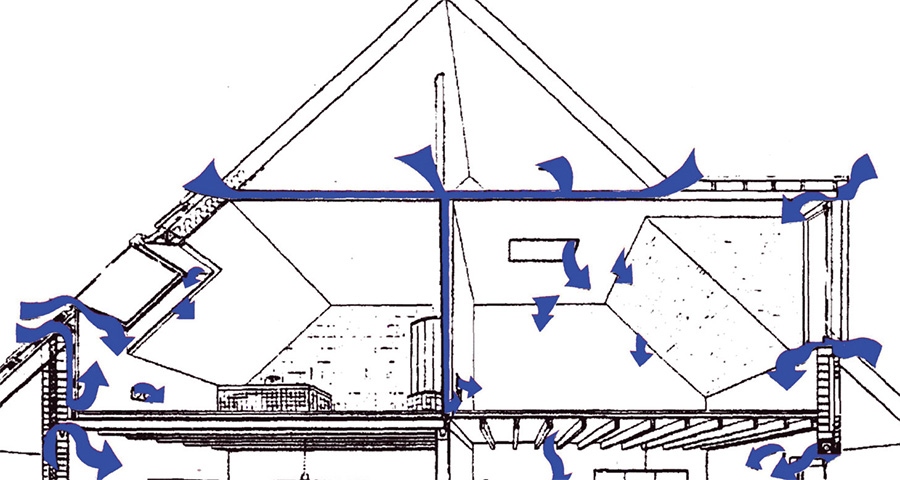
- Insight
- Posted
Airtightness - the sleeping giant of energy efficiency
A building’s airtightness test result isn’t just an indicator of its energy efficiency – it’s an unambiguous indicator of build quality. With a little care in design and on site, airtightness targets that may seem impossibly tough are anything but, argues leading architect and certified passive house designer Simon McGuinness.
This article was originally published in issue 7 of Passive House Plus magazine. Want immediate access to all back issues and exclusive extra content? Click here to subscribe for as little as €10, or click here to receive the next issue free of charge
There are 1.3 million1 two-storey houses in Ireland – and over ten times as many in the UK – which must be retrofitted in order to reduce their impact on national carbon emissions, reduce fuel imports and to mitigate the impact of rising energy costs on fuel poverty. Done well, this retrofitting will have massive positive impacts on public health, the domestic economy and on Ireland’s and the UK’s balance of payments
Many of the measures we need to undertake are expensive and disruptive. Many have short lifecycles and will need frequent maintenance throughout that short life to keep them running efficiently. But some are free, easily won and long lasting. Airtightness is one of those free gains which is not properly understood or valued. This is partly due to inexperience with building tightly, and partly due to confused responsibilities for the delivery of airtightness. The aim of this article is to cast new light on both of these areas.
Measurement
‘You can’t manage what you can’t measure’2 is the fundamental tenet of performance management. When it comes to buildings, airtightness is one of the performance indicators we can measure very accurately. We even have an international standard3 describing how to measure it and national accreditation bodies ready4 to enforce proper standards on the independent testers of airtightness. Everything we need is in place, we just choose not to measure every building. Why?
I think the answer to this lies in part within the building regulations. It is a basic presumption of the regulations in the UK and Ireland that necessary background ventilation can be provided partly through leaky construction. Why else would it be necessary to increase the area of designed background ventilation openings in the event that an airtightness test returns a leakage rate of less than 5 m3/h/m2? If you build tight in Ireland, you have to compensate by drilling more and bigger holes in the fabric to let air in. This is a fundamental contradiction and a contradiction that militates against building tightly. Furthermore, if you claim the energy advantage for building airtight in Ireland’s Building Energy Rating, then you are required to test every dwelling in a development. If, on the other hand, you build to 7 m3/h/m2 at 50 Pascals, you have to test just one in 20 dwellings. So the prejudice against airtightness is reinforced.
Don’t get me wrong – there is a need to provide adequate ventilation in all buildings, depending on occupancy levels and the use of the building. However, the presumption that a building with a q50 permeability of 5m3/h/m2 is a healthy building but a more airtight one poses a danger to human health is false. Quite the opposite in fact, as the migration of humid air through the fabric that is measured in an airtightness test, may actually indicate a risk of interstitial condensation and its potential consequence: hidden mould growth. Leaving aside hygrothermal concerns and dealing only with ventilation, we need to move towards a regime where indoor air quality is measured, not presumed; where carbon dioxide and humidity are routinely monitored and fresh air introduced as and when required, and in the precise quantity required.
Airtight ceiling membrane with cable services cavity beneath & plastered partition junctions. Standard polyester scrim was applied to the new ceiling/wall junction and skimmed over, covering the Tescon tape joining the Intello membrane to the plaster face of the wall
Fortunately, the technology to achieve this is simple, robust, reliable and relatively inexpensive (in fact, it will pay for itself many times over in energy savings). It requires no human intervention to activate and no electrical power to open or close the vent. Known as demand controlled ventilation, this technology is not even mentioned in Part F of the Irish building regulations technical guidance documents (TGDs), last updated only five years ago. This is a startling omission.
So, we have a cultural problem. We can perhaps fix the TGDs in time. Meanwhile the DCV deficiency can be bypassed by employing a suitably qualified mechanical services engineer to design a whole building mechanical ventilation solution to international engineering standards using DCV and certifying it as compliant with building regulations — if you can find such an engineer with residential experience. However, no case law exists as yet to confirm an Irish court’s view of this approach. In that context, the new Building Control (Amendment) Regulations5, introducing self-certification and very strict compliance requirements in Ireland (and as yet unknowable penalties for transgressions), is likely to result in even less willingness on the part of professionals to find such creative solutions to obvious gaps in the official guidance.
Inexperience
Having established that regulatory context, let me now address the issue of inexperience. Because we tend to build leaky buildings, we have few professionals able to design and specify airtight construction. Nor, without a demand for such airtight forms of construction, is there much opportunity to develop the trade skills required to deliver them on site. The Irish construction industry is trapped in a morass of low standards and a sheriff-and-cowboys attitude to compliance, some of it attributable to disjointed regulation, more of it to the effects of endless and catastrophic boom-bust cycles. A 2008 study suggests that Irish standards of airtightness are actually getting worse6.
Plastered up intermediate floor joists, taped to new plaster. One floorboard and upper skirting board removed to allow for plaster continuity between floors. The preservative treatment applied to joist ends is historic and is unnecessary given that the junction is now airtight and, as a result of external insulation, the entire inner leaf of the wall is retained at above 17C all year round. All risk of interstitial condensation around the joist ends is therefore eliminated.
One of the factors not adequately addressed in Irish regulations is the influence of our exposed geography. We live on a low-lying outcrop on the edge of the fierce north Atlantic weather system. We have the fourth best wind energy potential on the planet7. A windless day is something we only read about. Here, a small leak produces a big effect, significantly over-ventilating our buildings at certain times of the year, usually when least required – Ireland is about the last place in the world where passive ventilation (hole-in-the wall) is appropriate, particularly in the context of rapidly rising energy costs. Yet, we cling to this so-called natural ventilation as if to a long handed-down tradition.
In fact, it’s a relatively modern addition to our building codes, and largely a response to an epidemic of TB which swept Ireland in the 1950s. Excessive ventilation remains a key component of TB infection control to this day8. However, in the absence of a TB epidemic, the threat of icy draughts caused by over-ventilation of Irish houses may now be a bigger factor in excess winter death statistics, due to its impact on people with heart conditions9. The predictable response of householders to excessive designed-in draughts is to block vents, thereby endangering indoor air quality. This trend is exacerbated by rising heating bills. There is a need for a systematic study of the impacts on human health of the various forms of ventilation found in Irish homes. The current “natural” ventilation provision may actually be killing more of us than it is saving.
The passive house movement was the first to identify air leakage as an unnecessary component of buildings designed for human health and comfort. Adequate continuous ventilation is provided to meet the needs of occupants, but nothing more. In this way, ventilation heat losses can be restricted to what is required for good health of both the human occupants and the building fabric surrounding them. Unsurprisingly, hole-in-the wall vents are not part of passive house design. Ventilation is provided by a system of whole-house, balanced, mechanical ventilation with heat recovery. In order to meet the energy and comfort targets, the Passive House Institute set 0.6 air changes per hour as the maximum air leakage allowed in the building fabric. For most houses this equates to an aggregated leakage area about the size of a smartphone. There is also a requirement for opening windows to allow for purge ventilation, as required. This results in an intelligent balance of comfort, health and energy conservation.
Building to that standard is not easy, especially if you are an Irish or British builder steeped in the practice of constructing leaky buildings. It is therefore of interest that one such builder, Michael Nally & Sons of Galway, has produced a building with a leakage rate of just 0.37 ACH. That it was their first serious attempt at building tightly speaks volumes for the potential of the sector to deliver unimagined standards of construction quality, if the regulatory and contractual environment were supportive. What’s more, this result was achieved in a retrofit project. I think it’s time to reconsider our assumed horizons on airtightness. If that test result is possible with an inexperienced but diligent contractor, who knows what they could deliver with more experience?
In an effort to promote building tightly10, I’d like to share with you the methods employed to achieve that airtightness result. For most projects, building to such standards will not be economic or necessary. But every project will benefit from tighter construction where the wins are free, or low cost. My hope is that capturing those free wins becomes the norm, and that they will result in improved building energy ratings, for little or no additional cost.
Airtight tape applied to back of window frame lapped around four corners; Fixing bracket attached over airtight tape. The stainless steel brackets are fixed to the masonry reveals and plastered over; Window installation awaiting completion of external wall insulation. Rain infiltration at this stage would weaken the bond between reveal plaster and the airtight tape so internal plastering is delayed.
Case study — allocation of responsibilities
The house is a four bedroom semi-detached 1960s home built in a small suburban estate in Salthill, Galway. It was constructed with 300mm cavity walls containing a 100mm uninsulated air cavity. The intermediate floor is timber-joisted and the roof is a timber-trussed with concrete tiles. Windows throughout were single-glazed and aluminium framed. The ground floor was concrete slab on grade with no insulation. There are hundreds of thousands of similar houses all across Ireland. If we can’t make these and the rest of Ireland’s 1.3million two-storey houses nearly zero energy by 2050, we’ll have to demolish and rebuild them from scratch. That would destroy the embodied carbon in the materials already present, produce additional carbon emissions for its removal to landfill and add the further emissions penalty of building a new replacement dwelling. A veritable carbon triple whammy.
The client’s desire was to retrofit the house to passive house standards. I designed the layout and specified the fabric upgrade using the PHPP software. External walls were pumped and externally insulated, the ground floor slab was removed and replaced, and the roof was insulated. The airtightness strategy adopted involved five key principals:
• Completely intact plaster layer on the external walls from floor slab to first floor ceiling
• No chased services of any kind on the external walls
• Airtight membrane under the first floor ceiling with a battened services cavity below
• Passive house certified windows and doors taped to walls/floor under plaster layer
• All unavoidable service penetrations of the airtight layer sealed with grommets
• Complete removal of the chimney down to foundation level
The airtight layer was drawn in blue on all plans, sections and details and called up in detail in the various specification notes issued for tender. Photographs were included to show the sequence of operations of installing critical components of the airtight layer. If it’s not drawn or described in the tender, it can’t be insisted on during construction.
Extra thick slab-edge insulation creates airtight taping difficulties at floor/wall junction, particularly under depressurisation when tapes can detach from the concrete substrate
The entire ground floor ceiling was removed on my advice before the tender drawings were commenced, and the locations of all joists to the intermediate floor were surveyed and drawn. This proved invaluable in designing the layout of piped and ducted services within the intermediate floor zone and in avoiding clashes or cross-overs within the limited floor depth available. It also allowed the engineer to design the structural interventions required to allow the extensive modification required to the room layouts. Steel beams inserted into the intermediate floor zone were pre-drilled to allow pipework to pass through at a later stage of the construction. All internal block or partition walls abutting the external walls were cut back by 300mm min, the plaster layer made good and the abutment reformed.
The first floor partition heads were identified as a significant air leakage risk location, the ceiling having been installed within each room after the partitions were erected. Many were drilled for cables. All cables were removed and the head frames were specified to be taped over from above in order to join the upper surface of each ceiling to its neighbouring area of ceiling over the head of the partition. In the event, the contractor decided to remove all the first floor partitions in order to get a single continuous Intello Plus airtight membrane throughout the space. The studs and noggins were then reused to rebuild the partition walls. The client took that opportunity to improve the layout.
The existing Stira folding attic access stairs was relocated and a new frame and insulated lid added above it to produce an airtight seal. The insulated lid is tight fitting, the attic hatch and ladder unit is not, nor can it be made tight fitting. There is a market for someone to design a standard attic hatch with a U-value of at least 0.1 W/m2K, probably with upper and lower hatches, and containing a small landing area in between. The version specified, and faithfully produced on site, is functional but so tight fitting that it would not encourage anything other than periodic necessary maintenance access to the roof space. The attic is now a cold windswept desert with restricted headroom thanks to 400mm of mineral wool quilt: it is time to find somewhere else for the Christmas tree!
The skirtings were removed and the plasterwork extended to ground floor level. The intermediate floor abutment with joist end buried in the external walls was wet plastered. Once dry, the joints between the new plaster and the existing joists were taped up with Tescon No1 tape.
The sequence of window installation is instructive and relatively simple.
• The window was laid flat on a trestle
• Airtight Contega tape was applied to back of the two sides and head frames
• Flat stainless steel brackets were attached to the window frames through the airtight tapes
• The window was installed and adjusted. • The external insulation system was completed
• The reveals were plastered up with gypsum bonding
• 18mm OSB sub-cills were fitted and taped to window frame and to the plaster face
• The first blower door test was carried out (Result: 0.67 ACH)
• The cill boards were bonded to the sub-cills
• The reveals and head were then skimmed.
The ground floor slab-to-wall junction proved to be the most difficult place to achieve airtightness. The width of the edge insulation (50 to 100mm) required the use of extra wide Tescon No 1 tape, but the cut edge of the Kingspan Kooltherm board was not sufficiently smooth to adhere the tapes to, and under depressurisation these tapes lifted. (In future I’ll specify that these board edges are to be wrapped in foil tape before being fitted to provide a good surface for the airtight tapes to adhere to.) The edge of the concrete slab also proved difficult to achieve good adhesion on, in spite of using the recommended concrete sealer and bead of mastic. (In future I’ll specify a two-pack epoxy levelling compound to the floor edge to produce a smoother surface for taping to. I’ll also consider reducing the thickness of edge insulation in this area, given the fact that the external wall insulation extends to foundation level). The second blower door test produced a result of 0.37 air changes per hour.
Airtight ductwork penetrating airtight first floor ceiling to serve upper floor bedrooms
The MVHR system proved to be an unexpected challenge in achieving the airtightness rating. These systems are really designed to be contained entirely within the airtight envelope: they do not have the airtightness required to allow for ductwork terminations and air valves to protrude through the airtight enclosure, even if taped around. While it doesn’t need to be included in the airtight test (Gavin O Sé’s free on-line guide at greenbuild.ie was invaluable in teasing this out11), excluding the MVHR system required partial disassembly and extensive temporary taping of junctions, tube ends and terminal boxes. Another lesson learned expensively was that the final intake and exhaust terminals should only be fitted after the final pressure test is complete, as it is much easier to seal a protruding duct rather than a plasteredover wall vent terminal pushed through a mineral wool EWI system.
In future, I would contain all the ductwork within the airtight envelope, even restricting it entirely to the intermediate floor zone, if at all possible. A 3D BIM model of the services and the structures in this intermediate floor will be invaluable for getting it all to fit and communicating the requirements to the contractor, the structural engineer and the client. Fitting it is the easy bit.
In hindsight, we had the space to drop the first floor ceiling by 100mm (we had 2500mm floor to ceiling height) and this would have been a better option than penetrating the airtight layer, running ducts in the attic and penetrating the airtight layer again at each terminal box. We used the prefabricated jointless flexible duct system produced by Zehnder to match our Comfortair 350 MVHR unit, assuming it would be airtight to passive house standards. While it was much more airtight than fabricated metal ductwork, which can leak at every intermediate joint along the route, the blower door test revealed joints within each metal vent terminal box which leaked air.
I had not expected wet plaster bonding to be such a simple, adaptable and effective airtightness component. The plastering trade should embrace their emerging leadership role in delivering airtightness on site. Indeed, the decline of airtightness in masonry construction is directly attributable to the decline in the application of wet plaster: drylining, insulated or otherwise, is not airtight.
I expect that builders will find it convenient to purchase simple pressurisation equipment such as the Zephair Pre Pro, glaze it into a window frame and run it frequently during the course of construction to assess progress towards the performance target defined in the building contract. The independent tester’s role will then simply be to confirm what has been achieved. This also allows each subcontractSadly, Irish construction will not improve under the current regulatory regime which is — on the basis of this result12 — severely lacking in ambition. The cost of additional renewables, or additional insulation, to compensate for excessive air leakage is an unnecessary expense and contributes to global resource depletion. It’s time for a rethink.
1 Sustainable Energy Ireland, Five Year Strategy, http://www.seai.ie/Publications/SEAI_Corporate_Publications_/Strategy_Documents/launchdoc.pdf
2 Peter Drucker: You can’t manage what you can’t measure’ http://www.ncc.co.uk/article/?articleid=15472
3 I.S. EN 13829:2000 - Thermal Performance of Buildings – Determination of Air Permeability of Domestic Buildings – Fan Pressurization Method.
4 In Ireland, the NSAI runs a certified airtightness tester scheme and in the UK ATTMA and BINDT run a competent assessors scheme on behalf of DCLG.
5 S.I. 9 of 2014, http://www.irishstatutebook.ie/2014/en/si/0009.html
6 ARA, Sinnott D., Dyer M., Air-tightness field data for dwellings in Ireland. http://hdl.handle.net/2262/61487 Sinnott and Dyer found that the results of pressurisation tests on 28 Irish houses built between 1944 and 2008 “challenge the perception that newer dwellings are more airtight than older dwellings”.
7 Extracted from map included in Lu, Xi and McElroy, Michael B and Kiviluoma, Juha, Global potential for wind-generated electricity, PNAS 2009;106:10933-10938
8 WHO, Guidelines for the Prevention of Tuberculosis in Health Care Facilities in Resource-Limited Settings, 1999
9 See, for example, Prof Bill Keating’s work on the links between excess winter morbidity and poor housing: http://news.bbc.co.uk/2/hi/health/5372296.stm
10 There is no conflict between building airtight but to high levels of moisture vapour diffusion openness (often mis-named “breathability”). The two concepts are often confused. For a recent discussion n the differences, refer to Joseph Little’s Retrofit in Ireland linkedin group: http://linkd.in/1s6WTo7
11 http://www.greenbuild.ie/PassiveHouseBlowerDoorTesting.pdf
12 The measured air change rate is 0.372 ACH (or 0.6 m3/hr/m2), significantly better than the Enerphit retrofit standard of 1.0 ACH and better than the full passive house standard of 0.6 ACH. It is an order of magnitude better than the backstop value under Irish building regulations for dwellings of 7.0 m3/hr/m2.