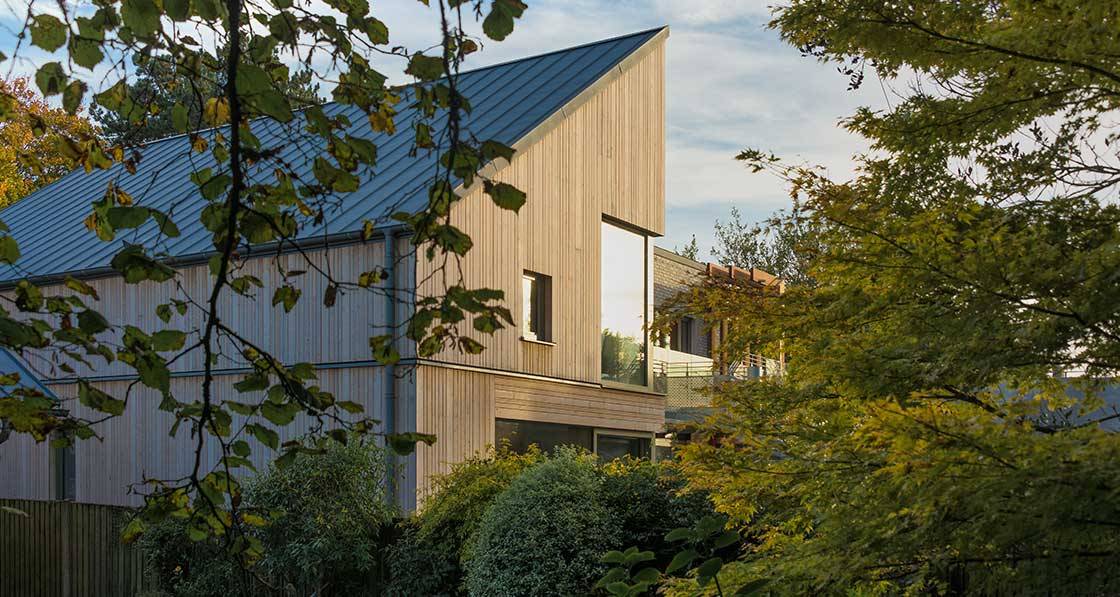
- New build
- Posted
Home from home
Few architects are tasked with knocking their old family home, but for John Morehead, once this difficult decision was made, it was a chance to create a future-proofed new passive house that embraces its stunning natural surroundings and exhibits remarkable attention to detail.
Click here for project specs and suppliers
Development type: 269 m2 detached dwelling
Method: Timber frame, insulated foundations, brick slips, low carbon materials, heat pump, PV
Location: Cork City
Standard: Passive house classic (pending)
Heating cost: €12 per month*
* Calculated space heating cost.
See ‘In detail’ panel for more information.
When passive house architect John Morehead received an email from a prospective client, enquiring about the prospect of designing a passive house on the site of Morehead’s childhood home in Cork, he assumed it was a joke.
Morehead is a well-known figure in the passive house community. The house he grew up in, a 1960s dwelling in the riverside suburb of Blackrock, had recently been sold. “I thought it was a family friend winding me up,” he says. But it was not.
The email came from Killian Hurley, a Cork native who is the chief executive at Mount Anvil, a housebuilder in central London. Killian and his wife Maeve had bought the house in 2018, with a view to building a new home for themselves on the site. They had turned up Morehead’s name when looking for a local architect with passive house expertise.
For Morehead, taking on the project was an emotional as well as a practical proposition. His parents moved from Dublin back to Cork in 1965. They bought the site along the marina, and had an architect-friend design a modest brick-clad dwelling, which they called Leeward. They lived there for almost 40 years. In 2005, Morehead’s parents divided the site in two, and Morehead designed a new low energy house for them on the newly created site next door.
Morehead’s parents moved into that house, called Svendborg, in 2007, and sold their old home. Sadly, Morehead’s father died soon after. Leeward was rented out for a few years, but was not looked after, and was empty when Killian and Maeve purchased it. The area is now highly sought after and has some of the highest house prices in the city.
Killian knew about the passive house standard from his work as a developer and says that if he was going to knock a dwelling, with the inherent environmental impact of doing so, he was keen to make the replacement as sustainable as possible. The couple were also keen on the promise of good indoor air quality.
A difficult decision
This article was originally published in issue 46 of Passive House Plus magazine. Want immediate access to all back issues and exclusive extra content? Click here to subscribe for as little as €15, or click here to receive the next issue free of charge
Morehead and his team at Wain Morehead Architects examined the possibility of renovating Leeward, but the ground floor was quite low-lying, and the house sits less than 20 metres from the tidal estuary of the Lee.
The site is on reclaimed slob-land along the river, created during the construction of a towpath in the 19th century, and will face an increased flood risk in the coming decades.
Extending the lifespan of the site meant knocking Leeward and building a new house with a raised floor level. “It was a difficult decision as you can imagine, to demolish the house,” Morehead says. “It was a very strange time for me, emotionally.”
But there were good reference points to guide the design of a new home. The waterfront location was one, even though the estuary views are north-facing. The sunny, sheltered, south-facing garden was another.
The neighbouring architecture was a third. The house is located in an Architectural Conservation Area, in a row of a dozen oneoff homes. “There’s a lovely eclectic mix of architecture along there,” says Morehead.
“They’re very much of their time. There’s Victorian, Edwardian, early Arts and Crafts.” He wanted to reference these styles and embrace their attention to detail while creating something thoroughly modern.
With its north-facing façade, a back garden that rises steeply at the rear, and lots of mature vegetation, getting more light into the house was a priority. For the northern rooms and terracing, this was achieved by introducing a glazed courtyard into the core of the dwelling, with vertical features to draw light down. Maeve Hurley took on the role of finishing the design of the courtyard and selecting a tree to plant at its centre.
Doughnut design
Passive house is really important, but it comes second to the architecture sometimes for us
The small, partly-glazed courtyard is a work of art, with vertical larch cladding, a bench for seating, and pedestals referencing old greenheart fenders on the quay wall. It sits in a direct line between the front door and the rear sliding door, creating an axis of light and vegetation running right through the house. “The courtyard has been a great success, it’s just gorgeous, it keeps drawing you into it,” Morehead says.
But it was “a nightmare from a passive house perspective,” he says. It essentially turns the house into a doughnut, with one external envelope on the outside, and another on the inside. This meant more surface area from which heat could escape, and more junctions to be made airtight.
“Passive house is really important,” Morehead says. “But it comes second to the architecture sometimes for us.”
The courtyard features triple glazed sliding glass doors from Schüco, and on hot days, these can be opened, along with the rear sliding doors, to create a stack effect and cool the building.
Morehead was keen to make sure the building was fit for a warming climate (it is interesting to note that, by using site specific climate data rather than generic data from Cork Airport, it was easier to meet the passive house standard. See figures for energy demand from ‘In detail’).
But he did not want to install active cooling. He was wary that, in our damp climate, mechanical cooling creates a risk of interstitial condensation, lowering the temperature of surfaces and triggering the dew point at which water vapour condenses.
At Leeward, the project team learned the hard way just how sneaky condensation can be. When the intermediate floor slab was slow to dry, the team inserted moisture probes to find out why. They found the temperature of the slab was lower than the surrounding air — water vapour was condensing on its underside, soaking into the Gutex wood fibre insulation beneath. It was a problem easily solved by cranking up the underfloor heating, but one that could have been much more serious.
-
The original 1960s house The original 1960s house
-
Gutex wood fibre insulation Gutex wood fibre insulation
-
Siga Majpell airtightness membrane and taping Siga Majpell airtightness membrane and taping
-
Brick slip installation in progress Brick slip installation in progress
-
MVHR ducting MVHR ducting
-
The south terrace The south terrace
-
Flat roof and solar PV array Flat roof and solar PV array
-
Arrival of the silver birch tree for the courtyard at the centre of the house. Arrival of the silver birch tree for the courtyard at the centre of the house.
-
Site cleared in preparation for the new build Site cleared in preparation for the new build
-
Insulated foundation system prior to concrete pour Insulated foundation system prior to concrete pour
-
Foundation complete Foundation complete
-
Timber frame walls with Smartply Propassiv OSB airtight layer Timber frame walls with Smartply Propassiv OSB airtight layer
-
Underfloor heating Underfloor heating
-
Smet Sudanit 280 hemihydrate screed Smet Sudanit 280 hemihydrate screed
-
Taping around windows Taping around windows
-
Sill to timber cladding Sill to timber cladding
https://passivehouseplus.co.uk/magazine/new-build/home-from-home#sigProId37b2c5202e
Attention to detail
Good quality daylighting, light dancing off things, good shading, is very important for the wellbeing of the person living there
The build suffered from other slowdowns — Brexit, Covid, and a difficulty in finding skilled subcontractors — but the finished house scored a blower door test result of 0.45 air changes per hour, an exceptional result given the number of junctions. “The detailing had to be very robust everywhere,” Morehead says. He praises his builder, Lough Contractors, for their “top class attention to detail”.
The timber frame was built by Eco Timber Systems, whose factory is just 15 kilometres away. And the twin-stud walls feature 300 mm of cellulose, manufactured by Ecocel less than three kilometres from the site.
The twin stud was key to ensuring there was enough insulation to meet the passive house standard. Airtightness is provided by Smartply Propassiv OSB, rather than membranes.
“We’ve always had a preference to use OSB as an airtight layer,” says Stephen Spillane of Eco Timber Systems. “It’s easy to apply tapes to. It’s very robust, you can even fix electrical socket boxes, etc directly to it without any compromise in the airtightness. A membrane can be damaged much easier and sometimes goes by unnoticed.” Spillane says that some of the architectural features, such as cantilevered corner windows and doors, required especially careful detailing.
The ground floor, meanwhile, was raised 310 mm above its previous level. It has an EPS insulated foundation system from Cavan manufacturer KORE. Space heating is provided by a Hitachi air-to-water heat pump, ventilation from a Zehnder mechanical ventilation with heat recovery system. There’s also a Showersave wastewater heat recovery unit — essentially a heat exchanger that recovers heat from wastewater going down the shower drain, and uses it to warm incoming mains water, and the cold supply to the shower mixer. There’s also an Amerisolar solar PV array with an average annual output of 1,979 kWh — which can be extended further on the western monopitch roof — and two electric car chargers.
Biophilia
With the principles of biophilia, we still have the same attention to the detail that the Edwardians did
Killian Hurley praises his architect’s “attention to minute detail”, and this is perhaps best expressed in the way the house interacts with its environment — its appreciation for nature, or biophilia, as Morehead likes to say.
“[Killian and Maeve] were very taken by the Edwardian houses down the road,” Morehead says. “We were designing a modern house, knowing they love the intricacies of those properties. With the principles of biophilia that we apply, we still have the same attention to the detail that the Edwardians did.”
This meant embracing views of the water and the garden, and retaining the mature vegetation on site (the build team were careful to retain the large Scots pines in the front garden).
Maeve Hurley selected a silver birch tree for the courtyard at the centre of the house, and when landscaping is complete, the view from the front door through the courtyard will extend out back to a timber-framed pathway, covered with climbing plants. A winding path will lead through thick vegetation to the escarpment at the back of the garden.
The new Leeward sits on a similar footprint as the original dwelling, but is larger at 269 m2. It embraces the estuary views while keeping the glazing ratio sensible on this north facade. But there is a new outdoor terrace here at first floor level, with views over the river. And there are clever nods to neighbouring properties. The western element of Leeward is aligned with its neighbour to the west, Svendborg, while the eastern element is aligned with Carriglee, to the east. This creates a slight ‘crank’ in the plan. The house’s timber and zinc cladding doff their cap to Svendborg, the brick cladding to the Edwardian dwellings nearby. The steep roof of the western element also references the gables of neighbouring homes.
For energy & humanity
Morehead and his team thought hard about how natural lighting would work in the space. “Good quality daylighting, light dancing off things, good shading — all of that stuff is very important for the wellbeing of the person that’s living there,” he says. “How the light works around the house — it’s not just for energy, it’s for humanity as well.”
The more extensively glazed south-façade looks out into the sunny, sheltered and lushly vegetated garden, with its outdoor dining terrace. Downstairs, the main living and dining areas face south too. A basket weave oak floor that was salvaged from the demolished house has been reused here.
Upstairs, the emphasis was on creating useful, adaptable rooms. There’s a study with a pull-out sofa for guests, and a family room with bunkbeds hiding behind a sliding door.
A south-facing, first floor terrace overlooking the garden is accessible from two of the upstairs bedrooms, with an external spiral stair connecting to the gardens below.
Killian and Maeve had just moved in as Passive House Plus went to press, and according to Killian they are loving the house, and especially the courtyard.
“To have a tree in your kitchen or living room is a nice one,” Killian says. “We’re in there a couple of weeks. We’re just loving the space. The light is particularly good. There are full height windows in a lot of the rooms, and that combined with the atrium gives a lovely feel to the house.”
Selected project details
Client: Killian & Maeve Hurley
Architect: Wain Morehead Architects
Civil/structural engineer: Horgan Lynch
Consulting Engineers Main contractor: Lough Contractors
Quantity surveyors: Richard Leonard & Associates
Mechanical contractor: Robert McGarry Plumbing
Electrical contractor: Gar Callanan Electrical
Airtightness tester/consultant: Building Environmental Resources
Build system supplier: EcoHomes
Thermal breaks: Bosig, via Ecological Building Systems
Roof insulation: Unilin Insulation / Xtratherm
Additional roof insulation: Ecocel
Insulated foundation system: Kore
Airtight board: Medite Smartply
Airtightness membranes and tapes: Ecological Building Systems / Siga
Heat pump and underfloor heating system: Pipelife Ireland
Heat recovery ventilation: Zehnder, via Clean Energy Ireland
Screeds: Smet
Windows: Zylefenster, via Walter Power
Embodied carbon
Shane Fenton of Wain Morehead Architects calculated the building’s embodied carbon using an early iteration of the new Irish national methodology for whole life carbon assessment, which is being developed by the IGBC under the Indicate project.
The scope was as per the EU’s Level(s) framework, and the cradle-to-grave total came in at 155 tonnes of CO2e, or 594kg/m2. As per the RIAI 2030 Climate Challenge requirements the results excluded emissions from operational energy and water use (modules B6 and B7).
As product level embodied carbon data is currently harder to come by for mechanical, electrical and plumbing services, at present the tool uses generic estimates for these elements, based on weight of each material type.
In detail
Project name: Leeward
Building type: 269 m2 detached dwelling, off site timber frame construction
Site type & location: Urban site, Cork
Completion date: 01/08/2023
Budget: Not disclosed.
Passive house certification: Passive House classic certification pending
Space heating demand: 11.01 Wh/m2/yr (site specific climate data), or 12.92 kWh/m2/yr (Cork Data) calculated using PHPP Heating load: 8.69 W/m2 (site specific climate data), or 10.11 W/m2 (Cork data) calculated using PHPP
Primary energy non-renewable: 37.82 kWh/m2/ yr (site specific climate data), or 38.45 kWh/m2/yr (Cork Data) calculated using PHPP
Primary energy renewable: 20.33 kWh/m2/yr (site specific climate data), or 20.70 kWh/m2/yr (Cork Data) calculated using PHPP
Heat loss form factor: 4.05 calculated using PHPP
Overheating: 0 per cent of year above 25 C (site specific climate data), or 3 per cent of year above 25 C (Cork data) calculated using PHPP
Number of occupants: Two adults
Energy performance coefficient (EPC): 0.031 (0.30 threshold)
Carbon performance coefficient (CPC): 0.019 (0.35 threshold)
BER: A1 (4.75 kWh/m2/yr)
Environmental assessment method: N/A
Embodied carbon: 492 kgCO2e/m2, calculated using PHribbon.
Measured energy consumption: Data not yet available
Space heating costs: Calculated at €148.91/yr, based on the calculated space heating demand of 11.01 kWh/m2/yr and stated heat pump seasonal performance factor of 569 per cent. Based on a 24-hour rate of 31.54c per kWh from Yuno Energy, this figure ignores the contribution to running heat pump from the solar PV array.
Airtightness: n50: 0.45 ACH at 50 Pa
AP50: 0.47 m3/hr/m2 at 50 Pa
Thermal bridging: All Psi values calculated. Insulated foundation system with timber frame construction superstructure. Thermal bridging reduced by optimising window junction details, installation of wood fibre board externally and Bosig Phonotherm at window sills/thresholds. Y-value (based on ACDs and numerical simulations): 0.020 W/m2K
Ground floor: 50 mm Smet Sudanit 280 hemihydrate screed, over Visqueen vapour barrier, over 90 mm Xtratherm Thin-R XT-UF (thermal conductivity 0.022 W/mK), over 70 per cent GGBS RC concrete slab, over 350 mm KORE Airfloor EPS100 insulated foundation system over, Necoflex RMB400 radon barrier. U-Value: 0.071 W/m2K
Walls: Factory-built timber frame with 22 mm larch cladding externally / Likestone Capri brick slips on Cemrock Extreme carrier boards, followed inside by 44 x 50 mm treated battens and counter-batten, Proctor Facadeshield UV breather membrane, 22 mm Steico Universal wood fibre board (thermal conductivity 0.040 W/ mK), 2no. 90 x 44 mm twin stud timber frame with full fill Ecocel cellulose (300 mm overall) (thermal conductivity 0.032 W/mK), 12.5 mm Smartply Propassiv OSB taped and sealed (airtight layer), 45 mm service cavity, 15 mm Gyproc Wallboard internally. U-value: 0.102 W/m2K
Pitched roof: Standing seam VMZinc, 125 x 25 mm rough sawn boards over, 50 x 50 mm battens, over Icopal All Zone breather membrane, 354 mm open web joists with full fill Ecocel cellulose insulation (thermal conductivity 0.032 W/mK), 12.5 mm Smartply Propassiv OSB taped and sealed (airtight layer), 35 x 50 mm battens, 15 mm Gyproc Wallboard internally. U-value: 0.15 W/m2K
Flat roof: Sarnafil G410 PVC membrane over, 190 mm Xtratherm Thin-R TR/MG tapered flat roof insulation (thermal conductivity = 0.024W/ mK), Sarnavap 5000e AVCL adhered to 18 mm plywood, 219 mm open web joists full filled with Knauf Loft Roll 44 insulation (thermal conductivity = 0.032W/mK), Siga Majpell (airtight layer) with 15 mm Gyproc Wallboard internally. U-value: 0.081 W/m2K
Windows and external doors: Zylefenster Europa 92 triple glazed alu-clad timber windows, Zylefenster Sky triple glazed alu-clad lift and slide units & Schüco ASE 80.HI aluminium lift and slide units. Overall Uw: 0.92 W/m2K
Roof windows: Two EOS Rooflights. Uw: 1.28 W/m2K
Heating system: Hitachi RWD air-to-water heat pump with SPF of 569 per cent supplying underfloor heating. Electric towel radiators to bathrooms.
Ventilation: Zehnder ComfoAir Q600 heat recovery ventilation system - Passive House Institute certified to have an effective heat recovery efficiency of 84.4 per cent Water: Domestic hot water provided by Hitachi air-to-water heat pump, Showersave waste water heat recovery system installed. 3,000 litre rainwater harvesting tank for use in toilets and external irrigation.
Electricity: Seven Amerisolar 410W PV Panels with average annual output of 1,979 kWh. No storage, electric car charging, and excess electricity exported.
Sustainable materials: Timber frame using FSC certified timber, wood fibre board, cellulose insulation, 70 per cent GGBS cement.
Image gallery
-
Ground floor furniture layout Ground floor furniture layout
-
First floor furniture layout First floor furniture layout
-
Leeward FF plan presentation Leeward FF plan presentation
-
Leeward GF plan presentation Leeward GF plan presentation
-
Leeward site plan presentation Leeward site plan presentation
-
Section courtyard 2020 Section courtyard 2020
-
3d views page 1 3d views page 1
-
3d views page 2 3d views page 2
https://passivehouseplus.co.uk/magazine/new-build/home-from-home#sigProId24d3fa0cdf