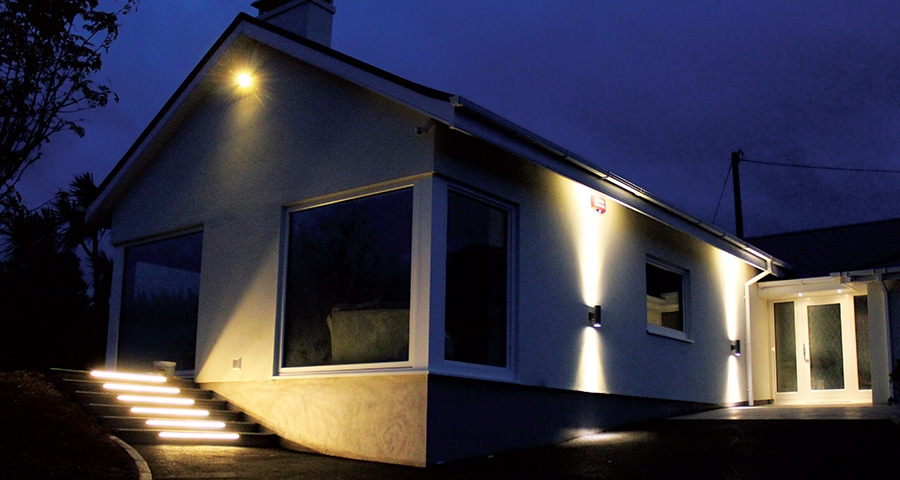
- Upgrade
- Posted
A2 rated extension and upgrade, Co Cork
This upgrade and extension to a rural home in County Cork cut its energy use by almost 90%, bringing it to the cusp of an A1 Building Energy Rating.
Two engineers brought their technical minds to this retrofit and extension in Carrigtwohill, Co Cork — and created a warm, energy efficient home in the process.
Emma and Rob had each owned separate homes, but after getting married decided to put one up for sale.
His house was on a site in the country where both of us preferred to live,” Emma says — so they decided to sell her house.
All windows and doors throughout the house are triple-glazed
Parts of Rob’s 1980s cavity wall house were cold and damp, other parts were fine. But the layout wasn’t ideal, and the couple wanted to make the space more efficient and usable. Being engineers, they were keen to get their teeth stuck into the technical details. “We weren’t going to compromise on the energy side of it,” says Emma.
The couple interviewed various architects and selected Cork-based Andrew Lane. Their main design goals were to maximise natural light and views over the east Cork countryside, and to create a modern, open plan living space in the extension — thus allowing them to re-task rooms in the old house.
But the project stalled when it took Emma a year to sell her old house. This turned out to be a blessing in disguise, as it gave the couple more time to research low energy building.
Carrigaline-based Vinro Ltd was appointed builder, while John Roche – then of Permagreen – was insulation and airtightness contractor for the retrofit of the old house.
The external walls of the extension feature 12mm Aquapanel cement fibreboard
Not wanting to lose any floor space, Emma and Rob chose to insulate the original house externally with 150mm of graphite EPS, finished with mineral render and installed by John Roche, who also pump-filled the existing 50mm cavity with Isothane Technitherm polyurethane foam.
The attic had previously been insulated with 300mm of mineral wool between the joists. But as part of the upgrade John Roche sprayed the sloping rafters with an extra 150mm of Isothane Duratherm, a rigid polyurethane spray-foam.
Getting the insulation and airtightness right in the old part of the house was the biggest challenge, says architect Andrew Lane.
“We in effect wrapped the building to create a warm structure, but the existing floor structure was a challenge as we did not want to take up the existing floor slab,” he says. The solution here was to lay 50mm of Kingspan PIR insulation on top of the existing slab.
Not wanting to lose any floor space, the clients chose to insulate the external walls of the original house with 150mm of graphite EPS
The extension was constructed with a factorybuilt timber frame from Cygnum. Emma and Rob opted for the company’s Precision 300 wall system, which delivers a wall spec pitched at the passive house market, including a U-value of 0.13.
The couple always preferred timber frame over block. “It’s warmer, it goes up a lot quicker than block. We didn’t want a long construction schedule,” Emma says.
Cygnum’s Heber McMahon calls Precision 300 the “Rolls Royce” of their timber frame systems. This was one of the first projects in which it was used, but he says demand has grown rapidly since.
The walls are insulated with 300mm of factoryfitted cellulose, with an insulated thermal break in the studwork to prevent cold bridging. The service cavity is packed with high density Metac mineral wool. Emma was attracted to the efficiency of a closed panel system — one that arrives pre-insulated, rather than being pump-filled on site.
The sloping extension roof features 300mm of high-density Metac mineral wool between the rafters, while a flat-roofed section has 400mm of the same. Airtightness is provided by German- manufactured Gerband tapes and membranes, supplied by Clean Energy Ireland.
The new extension comes together, with airtight layer
The couple insisted on detailed attention to airtightness during the build, and the whole house — old and new parts combined — scored 1.6 m3/mhr/m2 air permeability on its final blower door test.
“That’s nothing to be sneezed at for a bungalow of that vintage,” says Rodney Cronin of contractor Vinro. Rodney says the house is Vinro’s most energy efficient project to date — though he’s used to building well in excess of the building regulations.
“It was very straightforward because Emma had all her homework done,” he says of the job. “They were the perfect client, they knew exactly what they wanted.”
Building a low energy extension set a high standard that the team aimed to match for the retrofit, according to Andrew Lane. “I also learned how vital it is to have good coordination between the trades if you are seeking an airtight building. In this case we were fortunate to have a first class contractor who made this process as smooth as possible,” he says.
Carey Glass Joinery installed windows and doors throughout the house. The windows are aluclad with hardwood Iroko inside. Both the doors and windows are triple-glazed and feature the company's Vista Therm Elite SE glass with black, warm edge spacer bars.
There’s also six Fakro FFT thermally broken triple-glazed roof window, helping to create a bright, airy kitchen space, and large windows in the sitting room maximise daylight.
The heating set up features four thermodynamic panels — a hybrid of solar and heat pump technology.
Insulation added to the service cavity before plasterboarding
The panels feature a liquid refrigerant that has a boiling temperature of -25C. Sited on the roof, they absorb heat from the surrounding environment. This raises the temperature of the refrigerant and converts it from liquid to gas. The refrigerant is then recompressed into a “super saturated” liquid by an electricallypowered compressor. It is then passed through a heat exchanger, warming up water in the cylinder.
There’s also a fifth thermodynamic panel for hot water production. But the 50 solar evacuated Sun Pro tubes get priority here.
“Hot water is provided by the evacuated tubes when solar gain is present and then by the thermodynamic panel when there is no solar gain,” says Eamonn Ryan of Complete Alternative Energy, who designed and supplied the system. “This heats a 300 litre domestic hot water stainless steel cylinder.”
“The space heating system is controlled by the four panel thermodynamic system and any surplus energy from the solar tubes after heating the domestic hot water first is then dumped into the 500 litre buffer tank for space heating.”
Passive House Plus had heard reports of some thermodynamic systems frosting over, and Eamonn says when they are are undersized and overworked, they can freeze up.
But he argues that properly designed systems won’t encounter these problems — in this case having four panels for space heating and a separate panel for hot water means no panel is put under excess pressure. He says the system installed at Emma and Rob’s house is a replica of the one in his own home.
For heat distribution, underfloor heating was installed in the extension. Radiators were stripped out of the old house and replaced with low temperature aluminium units.
The ground floor features Cemex’s high thermal conductivity Supaflo screed.
“It’s using the latest screed specially designed for underfloor heating,” says David Kelly of Cemex. “It can be laid far thinner than traditional screed, and it has a higher thermal conductivity than traditional cementitious screeds.”
Complete Alternative Energy also supplied and installed a solar photovoltaic system to the house, a 3kW IBV solar system that produces about 3,000 kWh per year, according to Eamonn Ryan — roughly €600 worth of electricity. Because their main heating system is based on electricity, putting in PV made sense, and Emma and Rob are thinking about putting up a wind turbine too.
Emma says the thermodynamic panel system kept the house at 19C through the winter. The house is also equipped with a standalone Fondis V90L wood burning stove, but the couple say it isn't essential for keeping the house warm and is only used for extra comfort on cold days.
There's also a heat recovery ventilation system— a ProAir Systems 600 unit manufactured in the Éasca approved company’s Galway factory.
Emma and Rob are happy with the upgrade: “It’s performing very well at the minute, we wouldn’t have any complaints whatsoever.”
They add: “It took us I’d say six months to get used to how the controls worked and how everything worked properly, but this year now it’s worked a dream.”
Selected project details
Architect: Andrew Lane Architects
Contractor: Vinro
BER: GeoData Surveying Ltd
Timber frame system: Cygnum
Insulation & airtightness contractor: John Roche
Slab insulations: Kingspan/Xtratherm
External insulation system: Alsecco
Windows & doors: CareyGlass
Roof windows: Tradecraft
Airtightness products: Siga/Clean Energy Ireland
Flooring: Quick-Step
OSB: Medite Smartply
Floor screed: Supaflo
Floor screed contractor: Apollo Screed
Cement fibreboard: Greenspan
Renewable energy systems:
Complete Alternative Energy
Heat recovery ventilation: ProAir Munster Ltd
Additional info
Building type: Existing 133 square metre 1981 bungalow of block construction, plus 70.5 square metre timber-framed extension
Location: Carrigtwohill, Co Cork
Completion date: August 2012
Enerphit certification: not applicable
BER
Before: D2 (267.58 kWh/m2/yr) After: A2 BER (31.86 kWh/m2/yr)
Space heating demand, heat load and primary energy demand (PHPP): not calculated
Energy bills
Before: €1,600 on home heating oil & €460 on electricity
After: Estimate €1,050 per annum total (inclusive of rebate for electricity exported to the grid)
Airtightness (at 50 Pascals): 1.61 m3/hr/m2 / 2.433 ACH
Existing walls
Before: external render, 100mm brick outer leaf, 50mm cavity (cavity partially filled with unknown white substance), 100mm block inner leaf, Internal skim finish on sand-cement scratch coat. U-value: 0.5
After: 150mm graphite EPS external insulation and acrylic render finish externally, cavity filled with Technitherm foam insulation. U-value: 0.16
Extension walls: 12mm Aquapanel cement fibreboard externally, followed inside by 50mm ventilated cavity, breather membrane, 9mm OSB, 150mm structural stud (with cellulose insulation), 53mm celluloseinsulated
cavity/thermal-break, 89mm structural stud (with cellulose insulation), 9mm OSB, airtight membrane, 50mm service cavity insulated with Metac mineral wool, 12.5mm plasterboard. U-value: 0.13
Existing roof
Before: Roof slates to sloped areas externally. 300mm mineral wool insulation on the flat between roof joists and plasterboard ceiling internally. U-value: 2.3 After: Roof slates to sloped areas 300mm mineral wool insulation on the flat between roof joists and 150mm of Duratherm spray foam insulation between the rafters. U-value: 0.16
Existing floor
Before: 25mm Aerobord insulation under existing concrete floor.
After: Upgraded with 50mm Kingspan PIR insulation over the slab, plus two layers of 11mm OSB above this. U-value: 0.24 Plus, 100mm Kingspan PIR under the bathroom, en suite and plantroom in the old house.
Extension floor: Insulated with 230mm PIR insulation. Underfloor heating and Cemex Supaflo screed. U-value: 0.10
Extension roof: Raised tie roof trusses and infill rafters. Tegral fibre cement slates externally on 50x35 battens/counter battens, followed underneath by breathable roofing underlay.
Slope ceiling: 300mm timber rafter filled with 250 high density quilt insulation, airtight membrane taped & sealed, 50 mm uninsulated service cavity, 12.5mm plasterboard ceiling. U-value: 0.14
Flat ceiling: 400mm thermal insulation, airtight membrane taped & sealed, 50 mm uninsulated service cavity, 12.5mm plasterboard ceiling. U-value: 0.11
Windows & doors
Before: Double-glazed PVC windows and doors. Overall approximate U-value: 1.9.
After: New tripleglazed windows: CareyGlass triple-glazed Aluclad Iroko windows and doors. Aluclad french doors & single doors U-value: 1.3. Aluclad sliding doors: U-value: 1.1. aluclad triple-glazed windows U-value: 0.9.
Roof windows: Fakro FFT 12 U5 thermally broken triple-glaze roof window with thermally broken timber frames complete with XDP external overfelt kit. Overall U-value: 0.94 W/m2K
Heating system
Before: 16 year old oil boiler (Firebird Heating Solutions Popular 82, efficiency 85.5%) & radiators throughout entire building
After: 4 thermodynamic panels (COP 4.0) to heat 500litre tank which supply underfloor heating in the extension, main bathroom and ensuite and aluminium radiators in the existing part of the house. Fondis V80L inset stove, up to 11 kW. 1 thermodynamic panel for the hot water along with 50 solartubes.
Ventilation
Before: No ventilation system. Reliant on infiltration, chimney and opening of windows for air changes
After: ProAir 600 heat recovery ventilation system
Electricity:12m2 solar photovoltaic array with average annual output of 3kW
Image gallery
Passive House Plus digital subscribers can view an exclusive image gallery for this article. Click here to view