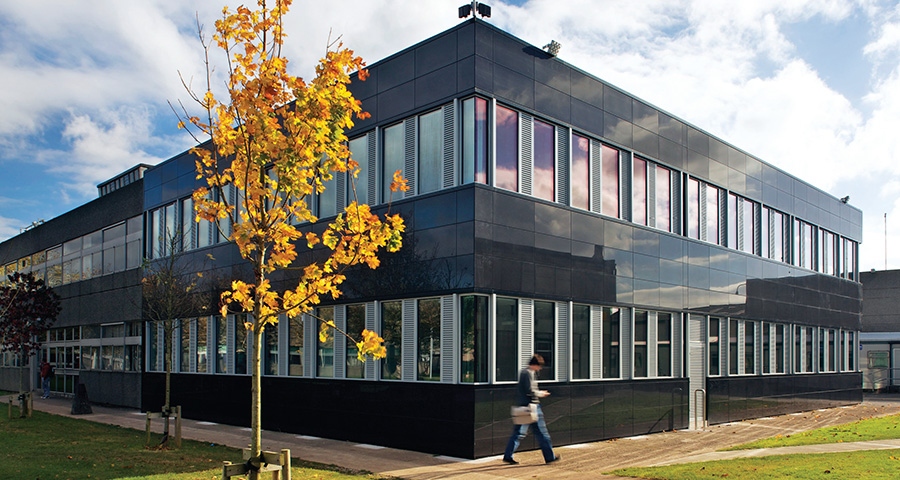
- Upgrade
- Posted
Cork engineering school pilots deep energy upgrade
A recently completed pilot project by Cork Institute of Technology may be a model for bringing untenably inefficient and uncomfortable office buildings up to near zero energy performance levels.
When the Regional Technical College network sprang up around Ireland in the late sixties and early seventies, energy was cheap. Ensuring that the building envelope delivered a high thermal performance was not a priority. As a result, the school of mechanical and process engineering at Cork Institute of Technology has not been a particularly comfortable place in which to work or study.
Designed in 1967 and completed in 1974, the 24,000 sq m building is a modular precast concrete structure, with uninsulated external aggregate panels and single-glazed aluminium windows. CIT architectural researcher Marc O’Riain says that the building doesn’t retain any heat in winter. “Everyone wears jackets all the time. You have cleaners mopping the floors, you have all these people milling around inside of it, so you get a lot of moisture in the air that just clings to the windows in the winter time.”
Meanwhile, overheating is a major problem in the summer. Extensive over-glazing means that temperatures in excess of 36C are common, even on mild summer days, and glare is an issue.
The refurbishment project did not originate as a low energy pilot, rather as a means of establishing a research space for two school of mechanical and process engineering research entities, Medic and Camms. But when external consultants submitted a specification for a conventional retrofit, engineers within the school identified a greater opportunity and the Net Zero Energy Retrofit 2020 test bed project was born.
As the name suggests, the plan is to deliver a full building retrofit leading to the consumption of zero net energy by 2020 – an ambitious target, given that the EU has set a seemingly less onerous “nearly zero energy” requirement for new public buildings by 2018 on the recast Energy Performance of Buildings Directive.
Energy consumption will be minimised through fabric upgrades, while any additional energy required will be sourced using renewable technologies. In addition to transforming the comfort and environmental performance of the building, the project will also provide a live, controlled test bed environment for building services researchers within the school. Moreover, it’s also envisaged that the fabric improvements piloted in the retrofitted section of the building – which represents less than 1% of the original building footprint – will act as a template for a phased full building retrofit in due course.
In its execution, the project brought engineers within the college together with external experts, as well as local businesses, to create an innovative solution to building fabric issues.
Successful deep retrofits invariably call for a return to ‘core and shell’. In Cork however, the institute’s building management authority insisted that the design team restrict itself to the removal of non-structural elements. “They felt if they removed the concrete panels and other structural elements,” says O’Riain, “that it would cause a lot more cost in terms of re-wiring sill line trunking. Scalability and modularity were important.”
Keeping those panels in place meant the design team needed a more innovative approach to remediating the wall build-up.
Turlough Clancy of architectural firm Henry J Lyons was brought on board together with M&E specialists, Arup Consulting Engineers, Kingspan and local manufacturer AMS/Westco Building Products. Working together with CIT’s engineers Paul O’Sullivan, Marc O’Riain and department head Daithi Fallon, the team came up with a bespoke curtain wall system which latched onto the existing structure. The new wall system, which incorporates a range of Irish technologies, delivers a passive standard U-value. Moreover, it’s a system that is modular and scalable and can easily be rolled out to the rest of the building, and indeed to other similar retrofitted projects around the country. Turlough Clancy at Henry J Lyons says that it is currently under consideration for deployment at two further projects.
“If you think of the prefabricated building stock that was built in the 60s and 70s,” says Clancy, “what you have is a tightly defined grid. The precast nature is repetitive. This system literally clamps onto the building and gives you a new skin effectively.”
Marc O’Riain says that one of the big challenges that they faced during the build centered on breaking the thermal continuity between the refurbished corner of the building and the remaining, uninsulated structure. “That was a huge problem,” he says. A void between the aggregate panels and the internal non-structural block wall runs continuously along the building. “We used an expanding phenolic foam in the cavity to provide us with an insulation and an air break, so we weren’t losing exponentially down the void. That solution turned out to be very successful.”
O’Riain is also keen to emphasise the importance of using simulation programmes to help arrive at the right building fabric solutions. “We spent a lot of time on simulation,” he says. “There is no way of delivering a low energy building without using simulation. Every single detail needs to be focused on and you can’t achieve robust solutions without thoroughly investigating each one.”
Paul O’Sullivan is a mechanical researcher within the school of mechanical and process engineering in CIT. He says that the team explored a number of different heating solutions before taking the decision to decouple from the existing gas boiler system and replace that with an air source heat pump.
“This was a great opportunity to allocate some of our heating to a renewable source,” says O’Sullivan, “which enhances us towards the zero carbon target. It’s fully controlled using a Cylon building management system (BMS).”
A mechanical heat recovery ventilation system was ruled out early on in favour of a natural ventilation strategy. This is effectively a combination solution, O’Sullivan explains. At sill level, a double louvred vent can be opened by the occupant to deliver fresh air. In addition, high level vents are controlled by the BMS system, which introduces fresh air depending on inside and outside temperature.
It’s early days, says O’Sullivan, who is still calibrating the system to deliver optimal living conditions. “In a passive house, it’s easy for the occupants to open the windows to flush the space out. It’s a bit trickier if you’re in an office with fourteen people. You also have more PCs, lights and so on, so you have a risk there that the heat generated has nowhere to go.”
This is an engineer’s project to its bones. In addition to the BMS system, the team also installed a data logging system. “It’s all wireless.” O’Sullivan explains. “We can move the instruments to any location we want for any period…We’re collecting a lot of internal temperature data, we’ve got external surface temperature data, humidity, CO2…We can use that to inform research and dissemination.”
Recognising the value of the research test bed under construction, Kingspan, with whom the research team is sharing the collected data, provided all of the insulation used on the retrofit free of charge.
Now complete, the project – which picked up the design sustainability award at the IDI Awards in November – has transformed a cold, leaky, overglazed building into a well-regulated, comfortable workspace. “The temperature is consistent no matter what the conditions are outside,” says Dathai Fallon. “The soundproofing is incredible; it’s quite shocking really sometimes when you open the window and realise how insulated from the sound you are.”
And as the students and lecturers work, they will also be facilitating the collection of a great deal of valuable data through the data logging system. “The occupiers are, to some extent, guinea pigs,” says Fallon. “Their use of the building will help the building services student projects that will be carried out within the centre in the coming years.”
Selected project details
Clients: CIT School of Mechanical & Process Engineering/ Zero 2020 research team
Project architects: Henry J Lyons
Project management: CIT Building & Estates
M&E: Arup Consulting Engineers
CIT team: Paul O'Sullivan, Fergus Delaney, Daithi Fallon, Marc O’Riain
Quantity surveyors: David McGrath & Associates
Main contractor: Summerhill Construction
Insulation: Kingspan
BMS controls: Cylon/Ace Controls
M&E contractor: KP Scanlon
Airtightness consultant: Building Envelope Technologies
Air source heat pump: Dimplex Renewables
Energy meters: Socomec/AEG
Envelope manufacturer:
AMS/Wesco Building Products
Windows, doors and roof windows: AMS
Flooring: W2W/Shaw Contract
Ceiling tiles: Ecophon
Additional info
Project overview:Building type: Modular grid optimised precast concrete building designed in 1967, completed in 1974
Area: Complete site: 24,000 sq m. Pilot project: 240 sq m
Location: Cork Institute of Technology, Bishopstown, Co Cork
Completion date: September 2012
Budget: €520,000 – including a €250,000 grant from the Department of Education and Science
Passive house certification: uncertifiable
Display Energy Certificate: to be calculated after one year of energy billing. Asset rating calculated using the Non-domestic Energy Assessment Procedure (NEAP) yielded a D3 for the existing building and an A3 for the refurbished section.
Space heating demand
Existing metered thermal energy use: 99 kWh/m2/yr (based on natural gas metered data).
No metered data available on annual electrical consumption of the local electric oil fired heater located in most offices through the building. A typical day of 8hrs @ average 1kWe power output = 8kWhr per 10m2 office space @ 30% floor area useable office space = 29,542*0.3*0.8 = 38.4 kWh/m2/yr unaccounted for.
Calculated annualised thermal energy consumption: < 25 kWh/m2/yr (estimated)
Environmental assessment method: Preliminary LEED review completed – LEED Silver (desktop study only)
Measured energy consumption: not available yet
Airtightness (at 50 Pascals)
Before: air permeability of 14.77 m3/hr/m2 @ 35 Pa
After: air permeability of 1.76 m3/hr/m2 @ 50 Pa
Walls
Before: external concrete aggregate panel, well ventilated 80mm semi open cavity, 100mm concrete block inner leaf. U-value: 1.77 W/m2K
After: 125mm Kingspan Kooltherm insulation separated by 35mm well ventilated cavity by a 10mm granite composite panel externally, the existing 65mm aggregated panel, 80mm phenolic foam insulation, 100mm existing inner leaf block. U-value: 0.11 W/m2K
Existing roof: 150mm concrete slab, 25mm degrading polystyrene, 25mm locally failing asphalt. U-value: 0.48W/m2K.
Upgraded roof: features 200mm of Kingspan Kooltherm and 3mm Paratorch PIR foam composite bitumen impregnated Hunton fibreboard. New roof U-value: 0.09W/m2K
Original windows: single glazed milled aluminium framed windows
Replacement windows: AMS Windows with Saint Gobain glass. South & West: triple glazed, argon filled, with additional non glass layer on the internal face with interstitial blinds. G-value: 0.33 (to reduce solar gain due to occupancy loads). Shading coefficient 0.38. Light transmittance 0.71. North: triple glazed, argon filled. G-value: 0.61 (to increase solar gain). Shading coefficient 0.7. Light transmittance 0.62. Overall U-value of 1.03 W/m2K
Roof window
Existing: Coxdome Baselock continous roof light, aluminium frame with Perspex glazing. U-value: 5.7 W/m2K
No budget to replace this roof light, which had a 1.2m up-stand from the internal soffit. Instead insulated flanking sides of the up-stand with 80mm PIR insulated plasterboard & inserted a new double glazed horizontal window in line with inside of soffit, thermally broken, trapping 1m of unventilated cavity. Existing roof light taped for airtightness, with unventilated cavity acting as thermal buffer in winter. Summer overheating mitigated by blinds & ventilation. U-value: 3.68 W/m2K
Heating system: original building served by one low temperature radiator system on a time clock with no temperature control. Heating scheduled from 7AM to 10PM.
The refurbished offices are decoupled from the existing heating system. A new radiator system is installed with thermostatic radiator valves (TRVs) fitted to each rad, fed with low temperature heat from a Glen Dimplex air-to-water heat pump mounted on the roof.
Ventilation: the refurbished offices use a natural ventilation strategy with a combination of manual and automated control of the ventilation openings. Glazing incorporates low level manually adjustable insulated openable door sections with external architectural louvres to provide single sided ventilation. The BMS controls a separate set of high level insulated doors to allow for background ventilation (soon to be controlled based on CO2 during heating season) controlled using a temperature monitoring strategy in summer months with the aim of promoting night purging of the structure. The glazing ratio (glazed to solid) has been reduced from 1:1.7 to 1:4, significantly reducing solar gain. A daylighting study was completed to support the decision to reduce the glazing ratio.
Green materials: composite compressed granite facade panel with a long lifespan & low maintenance. Existing window frames recycled for carbon offsetting. Shaw carpet with Ecowork backing with high recycled content, no heavy metal dyes, low VOC & recyclable. Irish oak screens for durability and low embodied energy. Ecophon Solo suspended ceiling tiles with a 70% recycled content and fully recyclable.