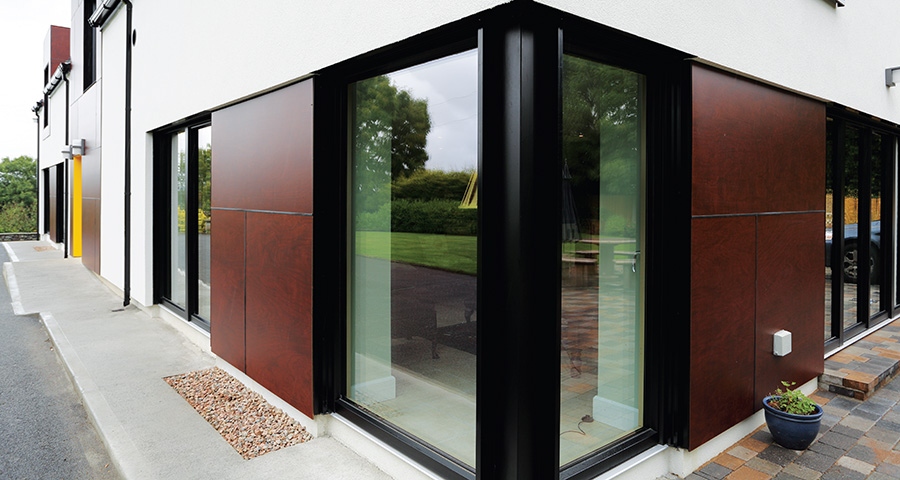
- Upgrade
- Posted
How to rescue a 1970s bungalow
A passive retrofit in Co Meath offers a template that could be applied across much of the Irish housing stock: a long, dark, 1970s bungalow was transformed into a bright modern home that’s now warm and comfortable.
Homeowner Paul Tully says that he and his wife Deirdre spent ten years trying to figure out what to do with their old house.
“It was cold and draughty and very expensive to heat. And we didn’t have enough space; we needed more bathrooms. So we watched Grand Designs and all of the building shows on TV, we went to all of these building and energy exhibitions, and we also went to see a couple of passive houses being built. We realised then that that was what we wanted. Something cheap to run and warm.”
The planning process did not go smoothly, however. The Tullys started out looking for a modern extension on the site of the bungalow, but the planners rejected the idea, saying that it would look out of kilter with the surrounding houses. Though it would have presented the builders with a more straightforward proposition, demolishing and rebuilding was also out of the question.
The Tullys then suggested to the planners that they convert their elongated bungalow into a modern dormer house by extending the house upwards by half a storey. This plan was accepted.
Stephen Young of Young Design Build was contracted to design the house. While Young is a veteran of passive building, this was his first project to aim for Enerphit, the Passive House Institute’s retrofit standard. It’s not quite as exacting as the new build standard – the airtightness threshold is a little lower, as is the space heat demand – but refurbishing an old house to achieve these targets can be considerably more challenging than starting on a greenfield site.
Moreover, the design brief extended well beyond achieving passive thresholds. Stephen Young explains: “The client wanted to increase the area in the house, he wanted to make it more open, he wanted the bedrooms to be enlarged, and ensuites added to all of them. Because we were going to undertake a huge amount of work, it made sense to remove the roof and go for a storey and a half.”
The existing bungalow’s roof was demolished along with all of the internal walls
The house was stripped back to its bare bones. The roof was demolished along with all of the internal walls, to leave just the foundation and the external walls. While retaining these features did help limit the cost of the job, working around them created other headaches.
“The demolition and removal process was very time consuming,” says Young. “Also, you have to be very careful on a building site where there’s tarmac in place, and existing landscaping.” Taking the care required to preserve all of these features, he says, tended to slow everything down.
As is frequently the case in refurbs like this, unforeseen issues arose. After the roof was removed, the team discovered a concrete ring beam that extended right around the house. It had been poorly installed and sections of it had to be removed, which further slowed the work. The house also featured a combination of floor slab and suspended floors, all of which had to be taken out.
The ground floor was insulated with Xtratherm Thin-R PIR insulation
Once the house was reduced to a shell, there was sufficient space to begin installing the insulation required to bring it up to spec. The existing cavity walls had been pumped with a fibre insulation in earlier years, so it was decided to leave the cavity untouched and to externally insulate the walls with EPS. The windows were moved to the outer leaf to help accommodate the insulation, which created a continuous envelope all the way round the house and helped to limit thermal bridging.
Removing the bungalow feel from the house was central to the whole design process. With the internal walls gone, the team could completely revamp the internal layout, creating the openplan arrangement that the client sought.
Externally, the facades were realigned to render them unrecognisable compared to the original design. “We changed the orientation of the windows,” Young explains. “Instead of the long, horizontal windows, we broke out openings and used vertical windows in the west elevation. In the south, we went with floor to ceiling window heads. That changed the dynamic of that whole facade.”
The dwelling was extended upwards by half a storey as part of the refurbishment
The original bungalow featured an extension from the eighties, which simply added to the length of the building, making it even longer and even narrower. This made all attempts to modernise the look and feel of the house that much more challenging. “We brought in Parklex cladding to the main entrance in order to break up that elevation,” says Young. “Instead of screwing the Parklex boards back to the substrate, we went with an adhesive system, so there are no visible fixings.”
Heating is delivered via an external Dimplex air to water heat pump and underfloor heating. There is also a 4kW solar photovoltaic array split between the east and west roof elevations. The combination of upgraded building fabric and renewable technology has propelled the house from a E2 building energy rating to a conservative A3. The BER assessment was done prior to the airtightness test, and without using the Irish methodology for calculating thermal bridges, meaning punitively bad air leakage and thermal bridging defaults were used.
To prevent summer overheating, the design team installed external fabric blinds, which were incorporated into the external insulation. Made of a semi-transparent material, the visual connection with the outside is retained even when the blinds are lowered. They filter out the sun’s UV rays and limit the solar gain that might otherwise overheat the house during the summer months.
The walls were externally insulated with platinum EPS
“The client felt that because we were doing that to the outside,” says Young, “they didn’t need to install blinds or curtains to those windows, so it left the internal spaces looking a lot more pure. The client found it aesthetically very pleasing.”
While 0.6 air changes per hour is the required airtightness standard for new passive buildings, 1.0 is deemed sufficient for Enerphit projects. The team nevertheless managed to achieve a very impressive result of 0.448 air changes per hour on the first attempt.
This was largely achieved through a wet plaster finish internally. “No top of the range additives or systems,” says Young, “we didn’t use any of the airtight plasters or anything like that.”
External blinds help to prevent overheating
That said, the process of achieving such a high standard of airtightness did require careful detailing and scheduling, with everything worked out ahead of time on paper. Once external walls were chased, the cavities had to be sealed ahead of the first electrical fix. Similarly, all airtightness details had to be completed before moving on to creating the first floor. Galway-based company Partel supplied Ampack airtightness tapes and membranes for the roof construction and windows.
The ventilation strategy required to complement this airtightness is largely delivered by a Paul Novus mechanical heat recovery ventilation system, installed in a soundproof closet adjacent to the master bedroom. Homeowner Paul Tully says there are no noise issues with the technology. In fact, one of the big advantages of the passive standard building envelope is noise reduction.
“We live on the N2,” he says, “which is a very, very busy road. You get lorries going up and down the road from five in the morning. Now, with the triple-glazed windows, you can’t hear them. It’s only a gentle sound in the background.”
He goes on to say that in delivering the project, there were two major difficulties. “Planning and money. They were the hardest. The actual construction of the building went very, very smoothly.”
The family moved in at the beginning of the year, and so far, so great. “It’s been brilliant,” says Tully, “warm, spacious, comfortable...We don’t know about the economics yet. Once we get into the winter we’ll find out, but we haven’t put on the heating yet.”
Selected project details
Clients: Paul & Deirdre Tully
Architectural design, M&E, contractor & passive
house consultancy: Young Design Build
Electrical contractor:
Kierans Electrical & Security Systems
Airtightness testing: Greenbuild
External wall insulation: Kilsaran
Roof insulation (Metac mineral wool): Isover Ireland
PIR insulation (roof, floors): Xtratherm
Airtightness products: Partel
Windows & doors: Young Design Build
Roof windows: Velux
Solar photovoltaics: PV Tech
Parklex cladding: Elemental
Heat pump: Glen Dimplex
Heating contractor: Penarch
Underfloor heating: Unipipe
Roof slates: Tegral
Additional info
Building type: Single-storey 157.6 square metre bungalow from 1970. Enerphit refurbishment and extension to a storey and a half. Total floor area now 286.4 square metres.
Location: Beaupark, Navan, Co Meath
Completion date: Jan 2014
Budget: Not available
Passive house or Enerphit certification: Pre-submission
Building Energy Rating
Before: E2 (343.16 kWh/m2/yr)
After: A3 (70.84 kWh/m2/yr. The BER was processed before the airtightness result was input. If updated, it would improve to 55.21 kWh/m2/yr, on the cusp of an A2).
Space heating demand (PHPP): 15 kWh/m2/yr (provisional)
Heat load (PHPP): 8 W/m2 (provisional)
Primary energy (PHPP): 69 kWh/m2/yr (provisional)
Airtightness after retrofit (at 50 Pascals): 0.448 air changes per hour
Thermal bridging factor: A punitive default Y-factor of 0.15 W/m2K was used in Deap.
Floors
Before: A mixture of suspended and solid floors. U-value circa 0.65 W/m2K.
After: 200mm Xtratherm Thin-R above new radon barrier with a 100mm concrete floor screed. U-value: 0.107
Walls
Before: Original concrete cavity walls with 60mm cavity pumped with fibre insulation, U-value: 0.55. 1980s extension cavity walls pumped with white EPS insulation. U-value: 0.51
After: 200mm & 250mm Platinum EPS insulation and Ceresit acrylic render finish externally to original walls & 1980s extension. U-value: 0.095 & 0.082 to original walls, and 0.10 & 0.083 to walls of 1980s extension. Parklex-clad walls sections over 180mm Platinum EPS insulation to existing walls (south & west facades). U-value: 0.109 & U-value: 0.102
Extension walls (1st floor): 200mm Platinum EPS insulation and Ceresit acrylic render finish externally to concrete block walls with internal sand/cement render and skim coat finish. U-value: 0.128 Parklex rainscreen cladding externally followed inside by/ 220mm Metac insulation to timber frame walls filled with 140mm Metac insulation; Durelis air tightness racking board, 25mm Xtratherm Thin-R; 40mm service void and plasterboard. U-value: 0.099
Roof
Before (demolished): Insulated at ceiling level with 50mm mineral wool insulation on flat. Roof tiles externally, plasterboard ceiling internally. U-value: 0.68
After: New slate roof with sloped insulation and insulation on the flat. 220mm Metac Insulation with 25mm Xtratherm Thin-R to sloped roof areas. Ampatop Protecta Plus breathable roof felt with integrated windtight tapes externally and Ampatex DB 90 vapour check and airtight membrane internally (plus Ampacoll tapes for airtightness). Also 200mm Metac Insulation with 25mm Xtratherm Thin-R at ceiling level with a 40mm service void and plasterboard ceiling internally. U-value: 0.14
Windows & doors
Before: Double-glazed, timber windows and doors. Overall approximate U-value: 2.5
New triple-glazed windows: Energate EN1202 triple-glazed timber aluclad windows and doors. Passive House Institute certified. Overall U-value of 0.83, or 0.85 installed (PHI cert).
Roof windows: Velux GPU Class 5 airtightness thermally broken triple glazed roof windows with white polyurethane frames and installed with BDX insulation collar. Overall U-value: 0.85
Heating system
Before: 20 year old oil boiler & radiators throughout entire building
After: Dimplex LA9MI air source heat pump with Harp database registered SPF of 355% fitted with a Unipipe underfloor heating system.
Ventilation
Before: No ventilation system. Reliant on infiltration, chimney and opening of windows for air changes.
After: Paul Novus 300 heat recovery ventilation system. Passive House Institute certified to have heat recovery rate of 93%
Electricity: 26.72m2 solar photovoltaic array with average annual output of 4kW split east/west.