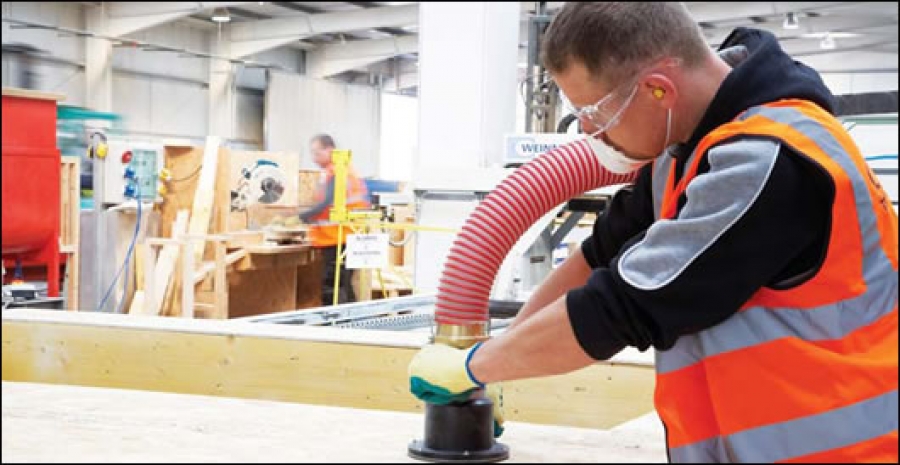
- Product News
- Posted
Cygnum innovation cuts costs on closed panel cellulose
Leading Irish timber frame manufacturer Cygnum is launching a pioneering closed low embodied carbon panelised building system that integrates cellulose insulation.
The Precision system has been developed by the company to drive down the costs of a building system that’s becoming increasingly popular due to its thermal performance, healthiness and low environmental impact.
Leading Irish timber frame manufacturer Cygnum is launching a pioneering closed low embodied carbon panelised building system that integrates cellulose insulation. The Precision system has been developed by the company to drive down the costs of a building system that’s becoming increasingly popular due to its thermal performance, healthiness and low environmental impact.
“Since the early days of Cygnum we have been building timber frame with cellulose,” Cygnum MD John Desmond said. “But we’ve found that cellulose has been confined to the upper end of the market because it can be quite costly. It’s an ideal insulation for timber frame because of the way it fills the panel once it’s installed correctly. We wanted to find a way to make it as cost effective as possible for our clients to use cellulose.”
Desmond said that the timber frame industry has been ramping up efforts to move more building processes off site and into the factory, due to the need for greater quality control to achieve stringent requirements for airtightness and consistency of insulation.
“When we looked at the cost of cellulose, we found a very significant portion of the cost build-up comes from the logistics model,” he said. “You have a fleet of trucks traveling hundreds of miles collecting waste newspaper, which is brought to a factory and turned into cellulose. That’s then brought to the installer’s depot, then to the site, and then the timber frame arrives separately, filled with nothing but fresh air. That’s a lot of unnecessary transport related carbon emissions and costs. By taking waste paper into the timber frame factory and producing cellulose with a micro processing line, we are avoiding that inefficiency.”
Desmond said that the company’s streamlined approach is effectively making a green product even greener, by further cutting the embodied carbon of cellulose – which is already a low embodied CO2 product compared to most other insulants. The company developed Precision as a twin frame system to enable the U-value to be adapted to meet a broad range of low energy specifications. The depth of the twin frame system – which is virtually cold bridge free – can be increased or decreased to offer any U-value required. The company recommends 0.15 W/m2K for passive house buildings.
The Precision system won the support of the EU Eco-innovation initiative, a scheme set up to bridge the gap between research and the market for innovative green products, services and processes.