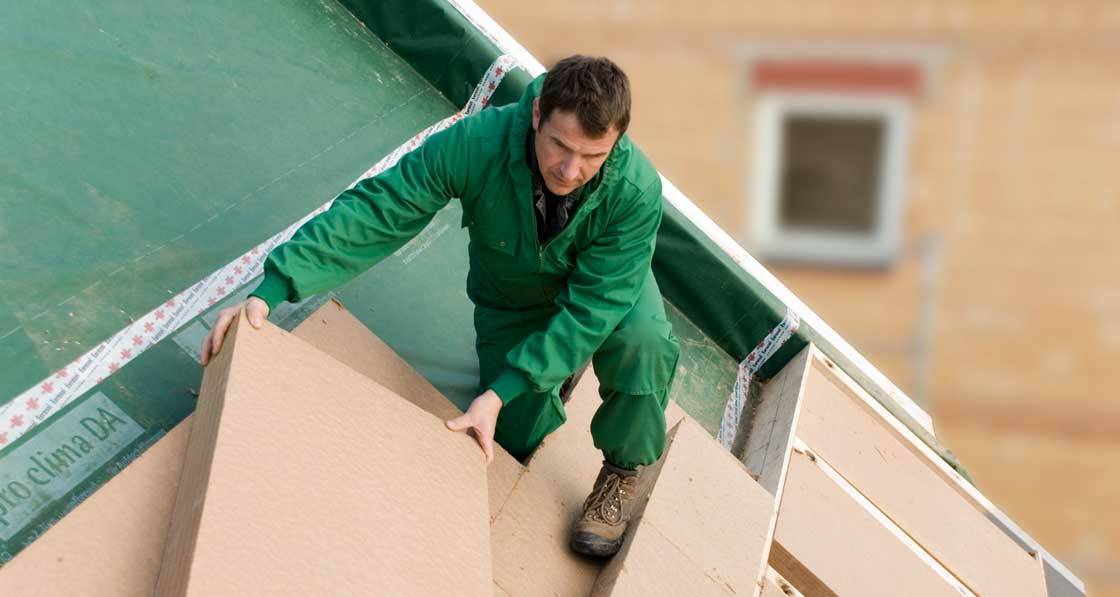
- Product News
- Posted
Insulation material choice key for thermal comfort — Ecomerchant
This article was originally published in issue 16 of Passive House Plus magazine. Want immediate access to all back issues and exclusive extra content? Click here to subscribe for as little as €10, or click here to receive the next issue free of charge
To illustrate the point, the company describes two buildings on a hot day: one is a caravan, the other a stone-build house.
“In the caravan, as soon as the outside cladding starts to warm up, heat output is recorded within minutes on the inside face as heat quickly transfers through the aluminium and lightweight insulation composite,” said Ecomerchant’s Will Kirkman. “As the face of the stone wall heats up the heat progresses much more slowly from the outside to the inside.”
The interesting, and often baffling, aspect of this phenomenon, argues Kirkman, is that the two materials can have very similar U-values, so that in steady-state conditions where heat is applied at a constant rate over a period of time to the external face of both materials, there is an equally constant flow from the inside surfaces of diminished heat.
“What’s different about the caravan and stone house example is that the heating is not steady-state: real life heating from the sun varies throughout the day,” he said. “This variability is known as periodic heat flow, and fortunately for the purposes of building design, it is almost entirely predictable.
It doesn’t take much to rapidly heat a building through a lightweight structure such as a roof. Pitched roofs are efficient solar collectors and large in area compared to the internal volume of the internal space. Vaulted ceilings and rooms in the roof are often the hottest areas within a building.
Timber roofs are lightweight with low thermal storage capacity, so heat from the sun will quickly transfer into space below, just like in the caravan.
“So we end up with bedrooms and living spaces that get too hot and create uncomfortable sleeping conditions,” said Kirkman. “By the time we find this out it’s normally too late. The key here is density, because mass acts as a heat buffer, and this leads to a phase shift, the time span between the highest external temperature and the highest internal temperature.” The aim, Kirkman explains, is to delay the heat transfer through the fabric of the building so that high external temperatures only reach the internal side when it is already cooler outside.
“A proven answer to the problem is to use wood fibreboard insulation materials with high levels of diffusivity, meaning performance can be more closely mapped to traditional masonry construction, thus moderating internal temperature through the materials,” he said
Technopor all-in-one insulating floor slab
Ecomerchant is also the longest-established supplier of the all-in-one insulating floor slab material Technopor. Technopor is a pumicelike material made from 100% recycled glass — glass that would otherwise go to landfill — and is used to form an insulating solid floor slab as an alternative to concrete and foam insulation. “It is clean to handle, lightweight and exceptionally strong,” Kirkman said. “When locked in place, en masse, as a solid floor slab, Technopor has remarkable technical credentials.”
With a certified compressive strength of 0.5N/mm² it can carry loads of 50 tonnes per square metre. The closed cell structure of the granules prevents moisture being drawn up by capillary action into the building structure. It is frost resistant, and has class-leading Euroclass A1 certification for fireproofing. Floor screeds can be cast directly onto the compacted sub-base.
But, perhaps most importantly of all, with a lambda value of 0.08 W/m2K, it can deliver passive house standards of insulation (the U-value required determines the depth of Technopor used).
“Independent evaluation of installation costs show that using Technopor to form a solid floor slab is up to 24% cheaper than traditional hard-core, concrete and foam insulation and 3% cheaper than beam and block,” Kirkman said. “Technopor can be be laid in any weather conditions and requires no matrix or curing time; it is extremely quick to install.”
Technopor foam glass aggregate is LABC approved and certified as a load-bearing and insulating building material by the German construction authority, DIBt, and carries the CE conformity mark enabling it to be sold throughout the UK. A range of sectional construction drawings are available for most applications.
To read more on Technopor and view the Steico range of wood fibre insulating boards and batts please visit www.ecomechant. co.uk. You can also download the Steico heat protection brochure from http://tinyurl. com/h4wte2y