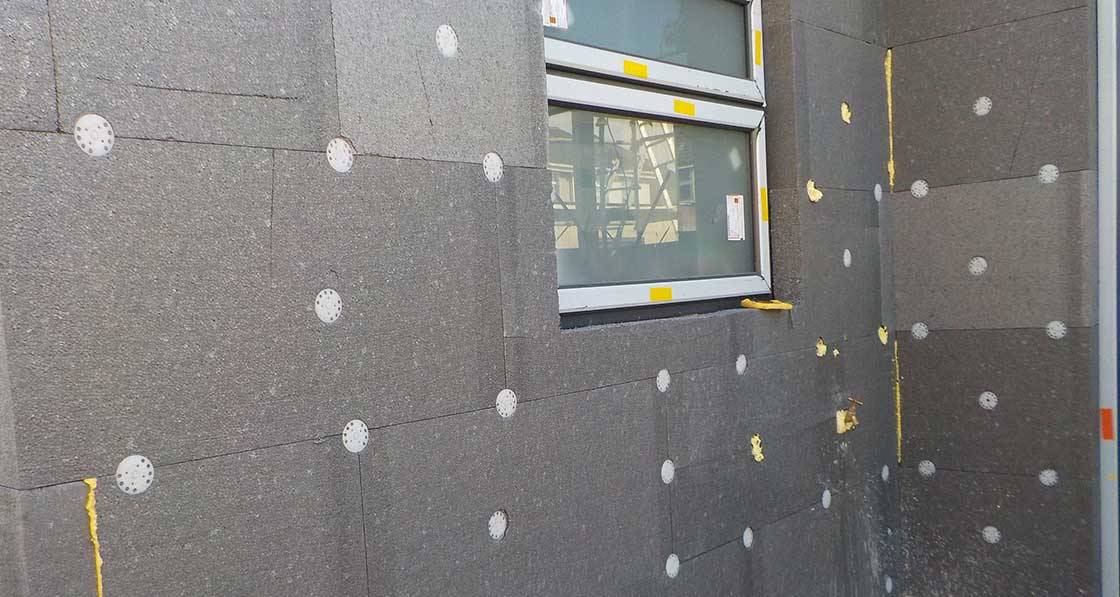
- Product News
- Posted
Quality EWI installation crucial for success of deep retrofit — MBC Project
MBC Project has warned that poor quality installation risks undermining confidence in the growing external wall insulation (EWI) industry — seen as crucial for bringing Ireland’s housing stock up to modern standards of energy efficiency. Dublinbased MBC Project supplies KABE Therm external insulation systems, which include EPS and mineral wool boards.
This article was originally published in issue 25 of Passive House Plus magazine. Want immediate access to all back issues and exclusive extra content? Click here to subscribe for as little as €10, or click here to receive the next issue free of charge
“While all EWI systems are installed in more or less the same way, according to NSAI standards, there are a few variations on this — predominately these would be around fixing patterns, essentially how the mechanical fixings are distributed across the surface of the insulation,” said Barry Boyce, senior technical advisor with MBC Project.
Boyce said that MBC Project’s standard approach for a typical EPS insulation board measuring 1,000 x 500mm is to install one fixing at the centre of the board, and one at each point where it meets the adjoining boards, creating a five point pattern of distribution, with an even distribution of fixings. This equates to about six fixings per square metre.
This is regarded as an ideal rate of fixing to ensure the board remains fixed, but Boyce said that using less fixings could potentially lead to insulation boards cracking at junctions if subjected to wind loads, and that this could potentially show through the render.
“In reality, on many projects you often see the bare minimum of four fixings per square metre,” Boyce said. He said this approach is often taken on site to reduce the time needed installing fixings, and to reduce the quantity of fixings required.
He continued: “Another area where there’s potential for corners to be cut is with adhesives. Generally there are two methods of fixing external insulation with adhesives, one is where you cover the board 100% with the adhesive, but that’s usually only applicable when the wall surface is very smooth and level.”
“More common than that is where you apply a strip of adhesive around the edge of the board and then dabs of it in the centre, so around 60% of the board is ultimately covered. But quite often, you see installations where the strip around the edge has not been applied, so you only have 40 to 50% coverage. Once something like that is done, it’s very hard to check without ripping the insulation off the wall. It’s easy to hide.”
Boyce told Passive House Plus that the KABE Therm range includes a variety of EPS types, including graphite-enhanced EPS, high-density hydrophobic EPS, and a breathable open-cell board. Along with traditional acrylic renders, the company is also now offering polysilicate renders, which Boyce said deliver the same quality as silicon renders — including stain resistance, breathability and low maintenance — while offering better affordability and greater durability.