- Case Studies
- Posted
Hidden Depths
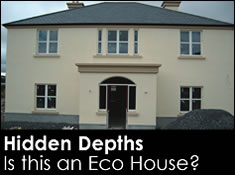
One of the main barriers against increasing uptake of sustainable building is appearances. The monopoly that traditional masonry construction has long held is certainly breaking up—even if most Irish timber frame houses include an outer leaf of blockwork—but this long held monopoly has affected everything from the regulatory situation to public perceptions of what houses should look like. Construct Ireland’s John Hearne discovers a low energy, low carbon house being built in Galway which is achieving sustainable results whilst not jarring with aesthetic conventions.
Developer James Kearney has chosen a site in Headford Co. Galway to construct a house which showcases a range of sustainable technologies. Standing on three-quarters of an acre, the house has been built to exceed current and future building regulations by some distance, yet retain a traditional look and achieve its ends using locally available products and expertise.
With a total usable floor area of 372 square metres including the basement, the house features a rainwater harvesting system, solar water heating, a wood pellet stove, wind turbine and photovoltaic electricity generation, a heat exchanger as well as a high insulation spec. Built with the technical guidance of Peter Keavney of Galway Energy Agency, the house, says Keavney, is special because it’s not so special. “There’s nothing unusual about this house…Yes it has a basement, but it’s still a typical two storey house in the countryside, but what we’re doing is introducing insulation and heating products that are available cost effectively at the local level. The point we’re making is because it’s cost effective and available locally, the opportunity and the potential for replicating this is immense.”
Under the European Water Framework Directive, domestic water charges are set to be re-introduced into Ireland within the next four years (and are tipped to be introduced after the General Election next year—Ed.). With this in mind, Kearney took the decision to design and install his own rainwater harvesting system. The water is collected in the usual way from the roof, then channelled via filter into a tank in the garage. “This is the primary tank.” Kearney explains. “The water in that will be used for toilets and any overflow from that will go into an overflow tank which is outside and which can be used for any outside use.” Approximately 50% of the water used in any domestic setting goes on things like watering the garden, washing the car and flushing the toilets and so does not need to be potable. Using the clean water available on the roof, household water consumption (and future bills) can be drastically reduced.
Inside the house, the first thing to consider was the insulation. In the walls, a wider cavity – 150mm – is pump filled with a platinum polystyrene bead. On the floor, there’s 100mm of polyiso, while the roof is insulated with 300mm of Warmcell cellulose fibre. Ecobead in Oranmore supplied and fitted all the insulation which delivers a U value of 0.2 for the walls, 0.13 for the roof and 0.18 for the floor. “If you take the walls, the outside value for building regulations is 0.37.” says Peter Keavney. “It’s similar for the floor and it’s actually 0.25 for the roof, so we’ve halved values basically, plus we’ve put in a product that’s available here in Galway that’s actually cheaper than fibre glass. Also, the contractor that’s installing the roof insulation is the same one that’s doing the walls so therefore he was in a position to buy the floor insulation and offer an overall insulation package to the contractor.” A supply and fit contract has the advantage of ensuring a better insulation performance through the use of qualified installation technicians, plus using one contractor for the entire spec offers a more cost effective solution.
Window U values also exceed building reg standards. Kearney chose Danish made Vrogum windows supplied by FGH Property Services near Glenamaddy in Co. Galway. Constructed using either Scandinavian pine or Victorian oak, all windows are built to order in Denmark, then fitted by the agent company onsite. “The standard product we do is a double glazed unit.” Darren Kearney of FGH explains. “It’s a super low e glass with an argon gas fill in the centre. It creates a U value of 1.2 on the pane of glass, then each window is different depending on how much timber is introduced. The average unit would rate between 1.4 to maybe 1.8 on the overall window.” Vrogum are now introducing a triple glazed unit with cork insulation throughout the frame which can deliver U values as low as 0.7. One of the key selling points of these systems is the fact that they’re low maintenance compared with traditional wood construction. “If you went with one of the timber stains that we do, you’d be talking between five and ten years maintenance free and with the paint finishes, ten to fifteen years is the guideline from Denmark.” In addition, the glass itself is fitted from the inside. “All your loose glazing beads would be finished internally,” says Darren Kearney, “whereas there’s been quite a few break-ins lately with burglars just popping off the glazing beads outside and taking out the glass. This is designed to prevent that. And it helps on the maintenance side as well because you’ve no joints externally where the water can penetrate.”
Window U-values in the house exceed building regulation standards. Built to order and constructed using either Scandinavian Pine or Victorian oak a U-value as low as 1.2 on glass and 1.4 on the overall window was achieved
Heating is provided by a 25kW modulating boiler made by Biotech in Austria and supplied by Total Energy Management in Ballybrit, Galway. “Modulating basically means that depending on the system demand,” says Kevin Devine of Total Energy Management, “the boiler is able to vary its output from 7kW to 25kW. It’s like volume control on a TV.” If you require heat in one room only, you will not have to draw down the full 25kW of power. “That is very important for any modern boiler but even more important with a pellet heating system. With our climate in Ireland, you have mild days and very cold days, so it’s very important for the boiler to be able to respond, because the greater the modulation, the greater the energy saving.” With a stated efficiency of 96%, the boiler is a little bigger than 10kW and 15kW units, standing just over 1.5M in height, 1.3M wide and 0.65M from the wall. It’s worth noting as well that for a house as large as Kearney’s, Devine would typically recommend a 35kW boiler, but given the high insulation spec, plus the fact that heat is delivered underfloor, the boiler does not need that extra power. For pellet storage, Devine recommends a guide storage footprint of 2.5M by 3M for a house of approximately 175 square metres. “Typically what the majority of people are doing, they’re assembling their own storage facility and we would supply them with the augur system that would take the pellets from the storage facility to the wood pellet boiler.”
With wood pellets taking care of the space heating, a series of solar panels provided by Nivektron in Spiddal looks after hot water needs. Kevin Noone of Nivektron estimates that the 10kW system should provide 66% of the house’s hot water needs throughout the year. “We’ve got four panels in all,” he explains, “with a total overall surface area of 10 square metres. It’s a high grade panel with anti reflex glass, a Teflon coating and an integrated absorber system, which means the pipe is just not stuck onto the back of it, the pipe and absorber are all the one unit.” Nivektron always size both hot water tank and coil to suit the system. “With some tanks, when you buy them off the shelf, they have a massive coils in them but because solar on average will give you 10kW, we put in a 10kW coil and not the 40kW that would be in most.” The system also features a space heating interface. An electronic control unit designed and built by Nivektron sets a target temperature for the hot water, and once that’s reached, any excess water is diverted to the heating system. “Lets say there’s nobody in the house,” says Noone, “and it’s a relatively good day. We had good sunny weather last February; bitterly cold but very good solar weather. The priority would be to the tank and once it’s reached that temperature, any excess would be diverted into the heating system. Once the solar cuts out at 2 or 3 o’clock in the winter time, the boiler can come in immediately and take advantage of the preheated water in the system immediately, so the boiler is hitting the ground running.” Noone estimates that the hot water system can contribute just under 20% of total space heating needs using this interconnectivity. “Even in the summertime, he’s going to have a certain amount of excess and that excess will keep a core temperature in the concrete so when winter cuts back in again, he’s not heating his ground up from pure cold.”
The final piece of the heating solution comes from a Temovex heat exchanger supplied by Scandinavian Homes in Moycullen. The system is fitted with a heat exchanger of the cross-flow type, made of aluminium plates. Two adjacent plates form a narrow duct for either supply or exhaust air. The supply air passes through on one side of the plate and the exhaust air on the other. The heat in the exhaust air is transferred to the supply air via the plate. When the exhaust air condenses, the heat effect increases on the supply air side. There’s no leakage between the different media, so odours and bacteria in the exhaust air can’t contaminate the supply air. The system boasts an efficiency grade of 82%.
The facade of the house has a deceptively conventional appearance
With electricity prices set to rise by a further 10% next year, Kearney decided to supplement ESB supply with micro-generated electricity from a combined wind turbine and solar PV (photovoltaic) system from Surface Power in Tourmakeady, Co. Mayo. John Quinn of Surface Power explains that the company’s ‘System Four’ is an SP800 watt system which is gives 400 watt-hour wind and 400 watt-hour solar PV at maximum harvest. “It’s a complete off-grid system. It’s running during the day and building up power for use during the evening time. You get the majority of your wind between March and October, during the day at ground level. In the evening time when the sun goes down and it gets dark, your turbine will stop.” The System Four comes with just under 10kW hours of storage with two inverters to turn stored energy back into usable power. “It’s wind and sun in one end and it’s ESB out the other.” Surface Power makes a point of supplying complete power solutions while Quinn cautions against overspending on one element of a system to the detriment of the whole.
“One of the things that happens in the DIY sector is people will blow their whole budget on a turbine and leave nothing for storage or equipment. Wind is only 15% of the total system, the rest being storage, electronics, inversion units and of course if you under-spend on any of the others…you’re really just starting to create weak links in a system.” Typical mast height he estimates at under 30 feet, adding that planning problems seldom arise. While it is possible to do without an ESB supply on a System Four, domestic self-sufficiency usually requires a System Five, which incorporates an extra turbine, double the solar panels as well as additional storage capacity.
The intestines of the heat recovery ventilation system. The Temovex heat exchanger, supplied by Scandinavian Homes provides an efficiency grade of 82%
Interestingly as Peter Keavney reveals, the primary energy rating for space heating and hot water for this dwelling is calculated as 49.5 kWh/m2/year—a figure which complies with the Fingal County Council energy standard. And though it's not a requirement for this project, the Dwelling Energy Assessment Procedure (DEAP) of the new Building Regulations TGD Part L has been conducted for this house to identify that the dwelling is well within compliance, providing a CDER, (carbon dioxide emissions rating) of 9.95Kg of CO2/m2/year, a 67% saving on the maximum permitted CDER.
"The overall primary energy consumption of the dwelling, again calculated with DEAP spreadsheets is calculated at 80.2 kWH/m2/year, relating to a typical A3 rated house, based on current issues of the label”, Peter Keavney stresses.
“The beauty of this,” Keavney concludes, “is that it’s a small developer, building one house for sale…Small builders have to think in this kind of way in order to increase the asset value of their labours.” James Kearney meanwhile is looking forward to completing the project. “I more or less did the whole thing for the challenge of doing it and to have a house that would be cheap to live in, that goes some way towards being self-sufficient.”
- Articles
- Case Studies
- Hidden Depths
- low carbon
- masonry
- James Kearney
- Galway Energy Agency
- European Water Framework Directive
- warmcell
- heat recovery ventilation
- heating solution
Related items
-
Lung disease patient: Zehnder MVHR “the best thing I’ve ever had”
-
ProAir MVHR unit achieves up to 95% efficiency
-
Zehnder launches MVHR system for tight spaces
-
It's a lovely house to live in now
-
IGBC launches updated sustainable homes rating system at Better Homes 2022
-
AirMaster’s flagship MVHR awarded passive house certification
-
New Brink Flair 225 MVHR unit launched
-
Draft development plan guidelines a “retrograde step”
-
Beam launch new app for easy heat recovery control
-
IG Masonry support claims 'carbon neutral' status
-
Good design key to heating & cooling via MVHR – CVC Direct
-
Beam announces next-generation HRV