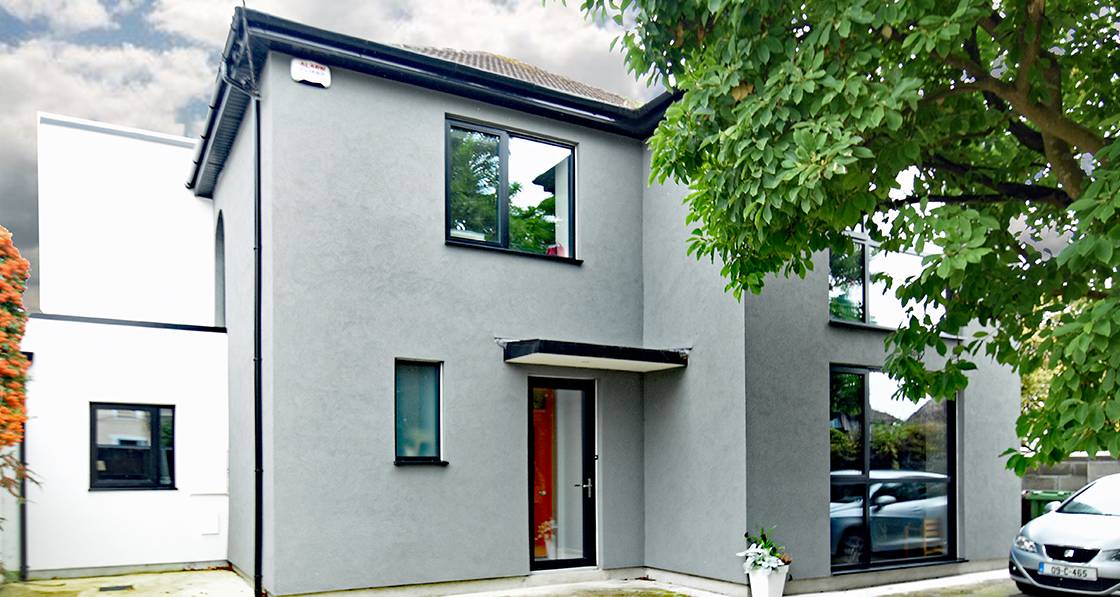
- Upgrade
- Posted
It's a lovely house to live in now
Click here for project specs and suppliers
Building: Deep retrofit & extension of 212 m2 detached 1930s house
Method: External insulation, timber frame, cavity wall, air-to-water heat pump
Location: Cork City
Standard: Enerphit (certified)
Heating cost: €41/month*
* Space heating only, based on estimate of average electricity prices over last five years.
See ‘In detail’ panel for more information
When Maeve McHugh and her husband Brendan Fitzgerald found their forever home a twenty-minute walk from Patrick Street in Cork, they were delighted with its 1930s charm and character.
The house had once been owned by a timber merchant and retained some beautiful panelling from that time. They quickly discovered however that spending the winter in the house was something of a 1930s experience as well.
It wasn’t just cold and draughty; it was also leaky. Maeve talks about setting out pots on Christmas morning to catch the drips coming in. The gas-fired central heating, supplemented by an open fire in the living room and electric blankets on the beds just couldn’t dispel the cold.
She says, “We had a thermostat heater in the sitting room, which gave some heat when the door was closed, and plug-in radiators in the kids’ bedrooms to stop the temperature from dipping below 16 degrees, but the kitchen? You couldn’t heat it. The air coming up through the floorboards made it feel like you were out of doors. You felt like you were taking your life into your hands making a cup of tea.” Brendan concurs, recalling having to microwave the Nutella to be able to spread it. And the damp could not be kept at bay.
“There were built-in wardrobes in our bedroom. I remember putting a pair of leather boots into the back of the wardrobe and when I took them out the following winter, they were covered in mould.”
So, it was clear from day one that a refurb would be necessary. Maeve has been an EPA inspector for twenty years, and Brendan is a pathologist at a local hospital, and the couple wanted a house which would match the family’s science-based green mindset. So, she got in touch with Paul McNally of the Passivhaus Architecture Company in Cork city and discovered that she already knew Paul from schooldays in Clonmel, where they’re both from.
Before and after
This article was originally published in issue 43 of Passive House Plus magazine. Want immediate access to all back issues and exclusive extra content? Click here to subscribe for as little as €15, or click here to receive the next issue free of charge
When Maeve and Brendan sat down with Paul, it didn’t take too long to figure out what needed to be done. The detached house comprised a central two-storey block which had been extended twice, to the side and to the rear.
“They were both late twentieth century, single-leaf cavity block extensions,” says Paul, “but they were very poorly built, with problematic layouts. We made the decision to demolish these and retain that central two-storey core.”
They then agreed to new rear and side extensions, creating a modern living space that would connect the downstairs with the garden and provide additional bathroom and bedroom space upstairs.
“We’d lived in an apartment in Toronto for three years,” says Maeve, “and had our first baby over there, so we were used to open plan, family friendly living. We were reasonably decisive about layouts and things like that.”
(inset) Before
I grew up in a house where my father was always saying ‘Close the door!’ but you don’t have to do that here
They also decided early in the project that this would be a certified Enerphit retrofit. “If you do something to a standard that is verifiable,” says Maeve, “you know what you have. You’re paying a little more, but you know what you’ve got.”
Paul McNally agrees. “My recommendation is always to try to go for certification. It’s a carrot that you can dangle just to get the performance out of everybody involved. Service providers see it as feather in the hat. They all want to have a certified passive house under their belt, and Enerphit even more so.”
Had the site been more accessible, Paul would have opted for blockwork extensions, but there were issues around access, particularly on one side, and for that reason, the build team had to go with a combination: blockwork where possible and a lighter timber frame construction where access was limited. The old extension had sat on a party wall on the side, but the new extension had to go inside it. The timber frame was deployed here, so that the gap between frame and party wall became an external cavity.
As any practitioner will tell you, hitting the airtightness target on an Enerphit project is always challenging, particularly at the junctions between old structure and new. “We were hoping to rely on the existing plaster for internal masonry details,” says Paul, “but in certain locations, the contractor had to take off the render and put in a membrane instead.”
In addition, there were airtightness challenges around an existing masonry-built porch and the original 1930s stairs, both of which were retained. Plaster had to be stripped back and tapes used to maintain the continuity of the seal. Paul notes too that since the project was completed back in 2017, a range of airtightness products – including sprays – have come on the market. These have made dealing with issues of this nature far easier and much less time consuming. In total, it took the contractor between two and three weeks to move from that first, failed airtightness test through to achieving 0.94 air changes per hour (ACH) at 50 Pa.
Eliminating thermal bridges is of course the second big challenge in retrofits. Here, the build team took one unusual measure. Similar to so many buildings of this era, the house is of single-leaf, hollow block construction. Paul points out that at the foundation of existing buildings, there is usually a thermal bridge that is not fully resolvable.
The standard way to mitigate it is to extend the external wall insulation down below ground level – 500 mm below in this case. In addition, the build team also drilled into the void of the first course of hollow blocks above the damp proof membrane and pumped them with foam.
“You’re just trying to get foam into the bottom course,” says Paul. “Because of mortar between each course of block work, these voids are not reliably interconnected, so you can’t pump in bead and expect it to fill the whole thing as you would when pumping a cavity. It is simply a means of getting insulation within the wall to deal with thermal bridges in the foundation.”
You couldn’t heat it. You felt like you were taking your life into your hands making a cup of tea
One further thermal bridge issue arose. A new steel super structure was introduced to support parts of the existing building. Where this steel meets the foundation, a Plate thermal break was installed to maintain the structural continuity but provide a thermal break. This is not unusual, but on this project, the foundation ended up slightly lower than anticipated, which meant that the thermal plate in the steel did not coincide with the floor insulation as it should have. “We had to introduce a fix,” Paul explains, “so we encased the steel in a vertical sleeve of PUR (rigid polyurethane) insulation in order to connect the floor insulation to the plate.”Features and materials were retained whenever possible, including the existing roof, slates and timbers. Working from the inside, the contractor installed a breather membrane facing outwards to allow ventilation under the existing felt, then used a combination of mineral wool and wood fibre to achieve U-values.
Maeve and Brendan didn’t want to give up the front door either, despite the fact that it no longer fit very well, but the design and build teams managed to retain it by moving the thermal line outwards at the porch, thereby transforming the door from an external to an internal one, now painted bright orange.
Living in a city, cleaning the filters is quite sobering. Houses around us are still burning solid fuels. The filters get black with tar
The family has been living in the house now for four years, and the novelty hasn’t worn off. “I grew up in a house where my father was always saying ‘Close the door!’ but you don’t have to do that here,” says Maeve. “There’s no variation in temperature, we keep it at 18 degrees upstairs and 21 degrees downstairs. It’s very, very comfortable.”
She notes too that even though it’s only a short walk from Cork city centre, the house is exceptionally quiet, and the air quality is great. “There’s no mould, and in the morning, you don’t have to throw the windows open to get rid of all the stale air. It’s just a lovely house to live in.” Tending to the heat recovery ventilation system, Brendan adds, shows evidence of how protected the family are against outdoor air pollution. “Living in a city, cleaning the filters is quite sobering,” he says. “Houses around us are still burning solid fuels. The filters get black with tar and stuff.”
How much has it been costing to heat the house? Maeve provided standing total electricity use data from the heat pump for this article. Assuming an average electricity cost of 20 cent per kWh over the last five years, it’s been costing under €500 a year to heat, and just under half that amount for hot water. (See a more detailed explanation in the ‘In detail’ panel.) As Brendan explains, that’s in spite of a very hands-off approach to operating the heat pump.
“The heat pump is on all the time, but only kicks in when needed,” he says. “You might notice it kicking in if two or three people have a shower. We probably should look at it now, the way energy prices have gone.” With the heat pump due for its first service from installers Energywise Ireland, Brendan plans to use the opportunity to look at ways to reduce reliance on increasingly expensive grid electricity for heating and the family’s EV, which is charged roughly once a fortnight. The house is wired for solar PV, which the couple may now consider installing – and the promising prospect of tweaking the house to make more use of cheaper, lower carbon night rate electricity, with PV taking the edge off daytime usage.
Selected project details
Architect and passive house designer: The PassivHaus Architecture Company
Structural engineer: James Kelly Associates
Main contractor: Grouville Developments
Quantity surveyor: Byrne & Co.
Mechanical & electrical contractor: Energywise Ireland
Airtightness tester: Clean Energy Ireland
External insulation system: Weber, via SIG facades
EPS insulation: Kore
Thermally broken wall ties: TeploTie, via Leviat
Airtightness products, natural insulation & thermal breaks: Ecological Building Systems
Thermal blocks: Mannok
Cement board: Aquapanel, via Greenspan
Windows and doors: Munster Joinery
Roof lights: Fakro, via Tradecraft
Heat pump: Daikin, via Energywise Ireland
Heat recovery ventilation: Brink, via Ian A Kernohan Ltd
-
150 mm PIR insulation under slab 150 mm PIR insulation under slab
-
PIR at window reveals PIR at window reveals
-
XPS insulation under threshold to sliders XPS insulation under threshold to sliders
-
The timber frame extension wall The timber frame extension wall
-
Intello membrane fitted to wall and ceiling Intello membrane fitted to wall and ceiling
-
Insulated MVHR duct in the cold roof space, with ductwork sealed during construction Insulated MVHR duct in the cold roof space, with ductwork sealed during construction
-
Battens to create a service void inside the airtight later for ductwork Battens to create a service void inside the airtight later for ductwork
-
370 mm mineral wool between studs and 22mm Gutex Multitop between rafters. 370 mm mineral wool between studs and 22mm Gutex Multitop between rafters.
-
Existing windows removed from front façade Existing windows removed from front façade
-
Bosig to electrical brackets Bosig to electrical brackets
-
Treated timber support wrapped in breather membrane Treated timber support wrapped in breather membrane
-
Windows bracketed proud of the walls, to sit in the new external insulation layer Windows bracketed proud of the walls, to sit in the new external insulation layer
-
200 mm EPS external insulation fitted to existing front wall 200 mm EPS external insulation fitted to existing front wall
-
Thermal break plate under steel column Thermal break plate under steel column
-
Mannok blocks and XPS insulation below DPC Mannok blocks and XPS insulation below DPC
-
Ancon TeploTies within wall cavity Ancon TeploTies within wall cavity
https://passivehouseplus.co.uk/magazine/upgrade/it-s-a-lovely-house-to-live-in-now#sigProIdf3441781ac
EMBODIED CARBON: DOES DEEP RETROFIT STACK UP OVER NEW BUILD?
It was decided very early on that this would be a retrofit rather than a demolish-and-rebuild project. In hindsight however, Paul Mc- Nally has come to question that decision. He says that both the time he needed to design and detail the project, and the time taken by the builders to execute that design were well in excess of the time it would have taken to demolish and start afresh. He notes that embodied carbon calculations were not conducted at design stage on this project, and that it was completed and certified Enerphit before the introduction of PHribbon, which calculates the whole life carbon generated by a project.
“I’ve gone from being very pro-retrofit to sitting on the fence until I see a lot more figures,” he says.
Passive House Plus commissioned embodied carbon calculations from PHribbon author Tim Martel, with Paul McNally providing detailed breakdowns of the materials used. The scope for the calculation included the substructure, superstructure and finishes, along with the heat pump and heat recovery ventilation system.
The kitchen fit out was omitted, as were sinks, baths, showers, and pipes, wires and ductwork. Given that the project is in Ireland, the EU’s Level(s) framework was used to determine the reference study period – i.e., assumed lifespan – of 50 years for the building. The building therefore came in at 86.7 tonnes of CO2e, or a score of 373.1 kg CO2e/m2 GIA. Notwithstanding the incomplete scope, the fact that the scope includes the elements which tend to count for the vast majority of embodied carbon of a project indicates that the house would very likely comfortably meet the 2030 target of 450 kg CO2e/m2 for dwellings larger than 133 m2.
Had the building been assessed against a 60-year lifespan instead, as per the UK’s RICS whole life carbon methodology, the total would have shot up to 458.4 kg CO2e/m2, principally because the assumed lifespan of windows was 50 years – meaning one full replacement after 50 years, and the assumed lifespan of the heat pump was 17 years, meaning three rather than two replacements. The scale of the embodied carbon totals for this project don’t necessarily appear to support the view that retrofit is always a lower carbon option than new build, but some major caveats need to be added. Firstly, this project is far more than a simple deep energy retrofit to an existing house. The new extensions are roughly the same area as the retained existing parts of the house. Secondly, the whole building was transformed – internally and externally, much of which had nothing to do with energy performance.
But embodied carbon calculation is still in its infancy, and Paul McNally is sceptical about whether the calculations capture the full impact of opting for Enerphit over new build.
“If a project takes four months longer to build and three months longer to design to achieve an acceptable retrofit standard, that means you have a builder and associated people and trades onsite for three months longer, plus you have the carbon emissions associated with me having to spend an extra three months designing the retrofit rather than working on a new building. That doesn’t get captured in carbon calculations, that’s outside the net. There is a whole raft of costs, labour and time that I don’t think is reflected in the analysis.” Paul teaches at the Centre for Architectural Education in UCC and says that these issues are coming under increasing scrutiny there.
“I don’t think enough research has been done, we need to look at real projects that would challenge the narrative. I’ve no doubt that there is a certain type of project where embodied carbon does stack up in favour of retrofit but in my own experience, I’d be very dubious about that being true across the board.”
There is also the issue of operational carbon. A seasoned passive house designer like McNally, starting with a blank canvas, could achieve the full passive house standard on a new build without breaking into a sweat, meaning additional carbon reductions via lower operational energy use. Clearly, it’s a topic which warrants further research.
In detail
Building type: Detached 212 square metre (treated floor area) cavity block wall house
Location: Cork City, Co. Cork
Completion date: August 2017
Budget: Not disclosed
Passive house certification: Certified Enerphit
Space heating demand (PHPP): 20 kWh/m2/yr
Heat load (PHPP): 12.14 W/m2
Primary energy demand (PHPP): 62 kWh/m2/yr
Overheating (PHPP): 0% of year above 25 C
Measured energy consumption: Data from the heat pump shows electricity use of 19,042 kWh from August 2017 to October 2022 – 12,936 kWh for space heating, and 6,106 kWh for hot water, averaging 2,462 kWh/yr for space heating, and 1,162 kWh/yr for hot water.
Airtightness: 0.94 ACH at 50 Pa
Thermal bridging: 0.15 W/mK for steel posts, columns in slab and at perimeter, 0.2 W/mK at existing internal walls, by calculations.
Heating costs: As standing charges are incurred for all buildings with electricity connections, and as the building would have had an electricity connection irrespective of the use of a heat pump, standing charges were omitted from the estimates. In fact, the decision to switch from gas to all electric would have removed an additional standing charge. SEAI five-year average consumer electricity price of 24.332 cent from 2017-2022 were considered, but this figure includes standing charges. Therefore, a rough estimate of 20 cent was used, assumed as a 24-hour rate, although the house has a night rate metre. Based on measured energy consumption from the heat pump (see above), the heating cost over the last five years likely came to circa €41/ month for space heating, and €19/month for hot water. With electricity prices rising to circa 44 cent per kWh for day rate and circa 22 cent for night rate as Passive House Plus goes to print, these costs may be in line to substantially increase – which is prompting the couple to look at ways to reduce costs, including the possibility of installing a PV array.
Ground floor: 150 mm PIR insulation with concrete slab. Mannok Aircrete block and extruded polystyrene at foundation U-value: 0.142 W/m2K
Walls: New build masonry: Render on blockwork, 250 mm graphite enhanced bonded bead insulation to cavity with Ancon TeploTies, blockwork and plaster finish. U-value: 0.137 W/m2K New build timber frame: Aquapanel render board on ventilated cavity with breather membrane, 30 mm Gutex Multitop, 225 mm mineral wool, 22 mm SmartPly, 50 mm mineral wool insulated service cavity, 20 mm skimmed plasterboard. U-value: 0.15 W/m2K
Existing walls: Weber acrylic render on 200 mm EPS external insulation on existing 400 mm hollow concrete blocks with plaster. Lower blocks drilled and pumped with foam insulation. U-value: 0.151 W/m2K
Roof: Pitched roof: Existing slates majority left in place. Airspace, 22 mm Gutex Multitop between rafters, 300 – 450 mm mineral wool, Intello membrane, plasterboard. U-value: 0.153 - 0.098 W/m2K Flat roof to new build: Ventilated cold roof, 30 mm Gutex Multitop, 285 mm mineral wool, Intello membrane, 100 mm service cavity with mineral wool. U-value: 0.119 W/m2K
Windows: Triple glazed Munster Joinery Passiv Aluclad tilt and turn. U-value: 0.81 W/m2K Roof windows: 2 x Fakro FTT U8 quadruple-pane glazed roof windows. U-value: 1.1 W/m2K. Heating system: Daikin 8kW split system complete with integrated 260 litre cylinder supplying underfloor heating and aluminium radiators. SPF 3.32.
Ventilation: Brink Renovent Excellent 400 (Plus), passive house certified component with an 84% certified heat recovery efficiency.
Electricity: n/a
Green materials: Retained existing front door, roof timbers and slates, and used salvaged roof tiles. FSC certified Iroko timber for external screen.
Image gallery
https://passivehouseplus.co.uk/magazine/upgrade/it-s-a-lovely-house-to-live-in-now#sigProId5aec855a21