- District Heating
- Posted
Economy of scale
In recent months there has been a frenzied growth in the heating of new apartment blocks and housing estates, from a single heat source. This is being driven by the realisation that fossil fuels are finite and rapidly dwindling, by political instability in the energy producing countries, by international fluctuations in energy costs and by our own needs to reduce our carbon footprint. For an increasing number of developers, district heating, often combined with large scale renewables and CHP have emerged as an attractive means of circumventing all of these constraints and uncertainties, whilst also offering an opportunity of delivering a more marketable product. At the same time management companies have evolved to facilitate these projects by fostering new relationships between the energy provider and the consumer, with many now starting to provide tailor-made solutions from the provision of finance, design and build, to the supply of fuel, maintenance and finally billing the client. Thanks to the ESCo model, one school in Donegal has gone green, seen its heating bills reduced by 15% yet has not had to outlay one cent in capital expenditure. John Hearne investigates an emerging trend that is bringing low carbon energy into another realm.
Size matters. The bigger you get, the greater the available efficiencies. With renewable technologies now mainstream in domestic construction, developers are eyeing up the options for large scale heat and energy production.
Property developer Ronan Meeley made the decision to utilise renewable energy-based district heating for a 67 house development in Moate when he read about district heating in this magazine. He was already a veteran of Sustainable Energy Ireland’s (SEI) House of Tomorrow programme, the scheme for promoting greener practises within the building trade. “It was [Construct Ireland editor] Jeff Colley who put me in touch with the people who’d be the experts in this field. I went up to SEI the same as normal and I got approval for the houses under the House of Tomorrow. I had intended putting in individual pellet boilers, the solar panels and the high level of insulation. The usual. Then I made contact with one of their experts and I worked out that putting in the district heating wouldn’t cost me more than putting in the individual boilers. Then I said yeah, why not?” The advantages, he says, are obvious. “It doesn’t take much working out that one boiler is better than sixty-seven. It was wood pellet boilers I was going to put, they’d be going in sheds out the back, so I don’t have the cost now of putting in the little base or the shed or the individual boiler.” With thirty houses on the estate sold before the possibility of district heating arose, Meeley called a meeting of future residents to see how the idea would go over. “I explained to them that I was delaying closing off these houses because I wanted to put in a district heating system. All but one of the residents were there…They said yeah, we’re all for it. Everybody was very, very positive towards the idea.” Despite the fact that it was an entirely new departure, and the fact that it delayed completion Meeley is still convinced that it’s the way to go. “I’m going to be building around here for a long time. If I get a name for building quality houses, I can always say to them when the market quietens down – which it’s starting to do – I can say to them, go over to Moate, look at those houses, that’s the way I leave an estate, that’s the way I do it. Knock on the door, ask the people living there what they think.”
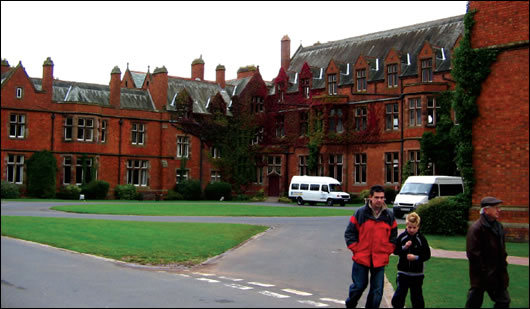
A Powertech wood chip boiler heats Belfast's Campbell College
The biomass boiler for the Moate project is being supplied by Powertech, a company who work with the full range of renewable heating technologies as well as CHP, have been involved in many large scale biomass heating projects throughout Ireland including schools, colleges, hotels and leisure centres.
“The success and the delivery of all these schemes are due to the pioneering work of many design engineering firms in Ireland who are putting their head on the block by coming up with solid plans that allow for these developments” says Powertech Ireland MD Francis Martin. “We have been fortunate at this early stage to have Noel Walshe of Logstor with his knowledge of district heating to partner on the pre-insulated pipe work and a number of mechanical engineering firms competent in this type of large industrial installation.
“From the beginning we have engaged the services of Dick Bradford of Barnsley Council in England to advise and vet all our work to ensure we start at the standard Barnsley have reached after thirty years of district heating - originally with coal - now with biomass”.
Powertech working with the Co-op Bank are currently involved in a number of projects including the Ronan Meeley district heating scheme and are now forming new partnerships with biomass growers such as the Miscanthus growers of Ireland. “We’ve formed close associations with leading manufacturers throughout Europe of large heat and CHP biomass plants.” Martin says. “This is a very exciting time and a great opportunity for Irish growers and developers to lead Europe in the beginning of a new fresh way forward. It is a time for leadership and commitment; the beginning of a new era involving everyone open to producing and using both heating and a portion of our electric requirements from home grown fuels”.
In public housing developments meanwhile, district heating has been taking off at a rapid rate. Emerald Housing, a new development of thirty-seven apartments in Ballymun will get its primary space heating from a 100 kilowatt wood pellet boiler while domestic hot water will come courtesy of a semi-centralised solar system. Clusters of panels will take care of the hot water needs of discreet groups of apartments, while the pellet boiler will provide backup support when the sun doesn’t shine. Igneus, based in Enniscorthy, Co. Wexford is providing the telemetry units in each apartment. These will allow individual householders on the district heating loop to monitor and control their heat requirements. While these systems will rely on conventional billing technology, innovation promises substantial change in this area. “You can now pay for your heat with a calling card.” Gerald O’Donoghue of Igneus explains. “You go down to the local shop and charge up your card, then shove it into the unit at home. You buy credit basically.” Alternatively, householders can buy heat using a credit card, while an internet hook-up facilitates further monitoring and control. “You can actually look at your energy usage online. Each house gets a password, you can buy credit online, but the main thing is you can actually see what you’re using and how much you’re spending.”
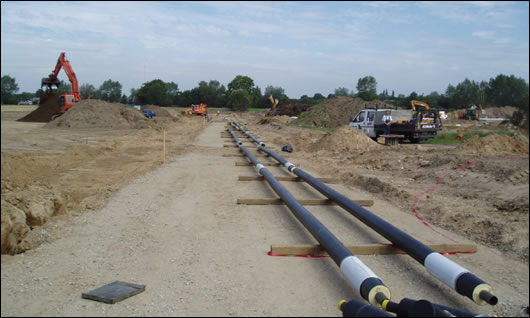
District heating pipework being laid by Igneus
In a public housing context, where ongoing maintenance and operation remains a local authority responsibility, the advantages of district heating are particularly compelling. O’Donoghue echoes Ronan Meeley’s central argument: “The main attraction is you’re putting in one boiler, you’ve only got the maintenance on one boiler. If you’re doing 50 houses, you take that collectively, you’ve got maintenance on 50 different boilers.” Contingency may require a second unit, but vitally, all that plant remains in one centralised, easy-access location. Moreover, the telemetry options available to control these systems get local authorities over what has been a particular difficulty in the past. “The big bone of contention up until now with local authorities is they didn’t want to be sending out bills to customers. But now with this prepaid card system, they can provide heat without having to bill anyone.” In addition, going the biomass route has major cost advantages over the fossil fuel alternatives. “You can get woodchip for at least 40% cheaper than oil, so if you’ve got 50 houses running off it, you’re going to be using a lot of fuel yes, but you’re also going to be making big savings.”
Large district heating installations aren’t really suited to retrofit. In order to make the thing work properly, says O’Donoghue, it’s essential that the system is worked into plans at the design stage. “You have to get in at the initial stages and stake your claim, to say look, I need a plant room here, I need a storage area and I need a lorry to be able to reverse in along here - especially with wood chip. Wood pellet is easier because you store it in a silo, and you blow it into a silo. Woodchip usually involves tipping so you have to reverse up a ramp. Ideally, it involves excavating underground. The whole idea is you get in and get out quick with the fuel. The fuel logistics are vital – maybe the most important part of the whole project – because if that goes wrong, it’s going to be a running nightmare all along because of the continuous need to refuel.”
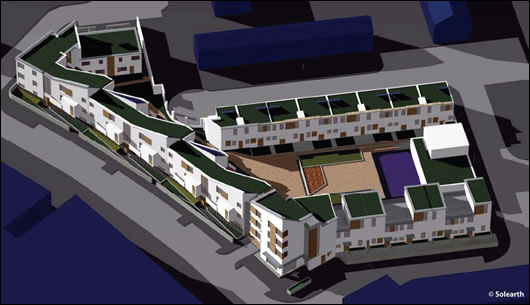
Emerald Housing, a new development of thirty-seven apartments in Ballymun will get its primary space heating from a 100 kilowatt wood pellet boiler while domestic hot water will come courtesy of a semi-centralised solar system
One company that has developed a specialism in this space is Fin Engineering, based in Belfast. “Traditionally,” says Liam Kearns of Fin, “plant rooms were built onsite. You shipped in the components, you had a whole pile of plumbers and they’d build the thing there. What goes out the window is quality and the cost is substantial because you lose a whole lot of materials. You lose time because there are huge delays, but the big thing is quality and performance, so what Fin perfected is building the entire thing in a factory environment and shipping it onsite and literally installing in a day or so. All the connections are there, the controls are there, even the lighting, the whole thing is painted and customised.” Currently, the company is installing a customised, factory built plant room for a district heating system at a major mixed-use development in Ballisodare in Co. Sligo. 110 apartments, eight retail units, offices and leisure centre will take their heat from a 1.45 megawatt biomass system. “The load is carried on two boilers.” Fin Engineering MD Stephen Moore explains. “One is 550kW, the other 900kW. All domestic hot water and space heating needs will be met using these two.” Fin is currently engaged in the development of a suite of factory-built plant rooms, graded by output and architecturally designed, which will house and integrate a range of renewable energy technologies.
In Dublin meanwhile, Clearpower is providing a 1.5 megawatt biomass boiler for a large McNamara development in Elm Park. Together with a range of complementary technologies, the boiler will supply heat to 230 apartments, a hospital, a day care centre, a hotel and 10,000 square metres of office space. Simon Dick of Clearpower points out that given Dun Laoghaire-Rathdown’s insistence on the incorporation of sustainable technologies in construction, planning permission is that much more attainable when developers go that route. The district system works through a main central ring supplied with heat by the boiler. That heat is then drawn off, monitored and controlled by individual heat exchangers and heat metres at each unit.
Clearpower has also been involved in a number of large scale biomass developments funded under SEI’s ReHeat programme. Launched in March 2007, the programme provides grant assistance for the deployment of renewable heating systems in industrial, commercial, public and community premises in Ireland. It’s administered by SEI and is an expansion of the previous Bioheat Boiler Deployment Programme which supported woodchip or pellet boilers only. In March however, the programme was expanded to include solar panels and heat pumps. According to SEI: “The Renewable Heat Deployment Programme aims to increase the deployment of renewable heating systems in commercial, industrial, public and community premises, achieve carbon emission savings and fossil fuel displacement and increase customer awareness and confidence in heating from renewable sources.” A range of community and commercial organisations have qualified for grant assistance under the programme.
“The business case for a medium sized user like a hotel switching to biomass is very strong.” says Simon Dick. “Say you’re spending e100,000 a year on oil. Roughly speaking if you swap to wood, you can halve your heating bill…and that that doesn’t take into account any of the other benefits; the environmental benefits, the CO2 reduction, the development of local fuel supply, the security of fuel supply…but the capital cost to get into that is around e100,000. You’re saving e50,000 a year, but the problem is your entry cost.”
This is where the Energy Service Company, or ESCo, comes in. An ESCo is essentially a business that provides energy management services to an energy user. Depending on the model, it finances, designs, builds and operates the energy source, then sells the energy under contract, according to an agreed pricing structure, to the energy user. Clearpower for example offers two business models to clients, the first in which the client pays for boiler and installation, the second in which Clearpower retains ownership of the kit but sells the heat to the client. “Owner manager type hotels who have good balance sheets at the moment are the ones who would generally buy it. Clients with capital constraints go for the ESCo model. Some might say I don’t have the capital now, but I want a buy option, and they might do that after a number of years.”
Given recent fears over security of supply, Clearpower, like many other companies in the sector, also provides long-term fuel supply contracts to its clients. Through partnership arrangements in this area, the company currently has three fuel depots, with a fourth due online soon, spread throughout the country.
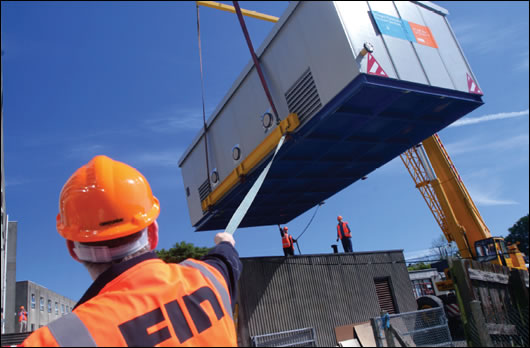
A Fin Engineering packaged heating and hot water plantroom is delivered at Ulster Hospital's Care of the Elderly Department. Currently, the company is installing a customised, factory built plant room for a biomass district heating system at a major mixed-use development in Ballisodare in Co. Sligo
Operating in the same space, Imperative Energy has also sought to address security of supply issues by entering into a partnership with private forestry company, Green Belt. “We have 175,000 acres of forest.” says Imperative MD Joe O’Carroll. “That’s essentially our oil well.” Under the ESCo model, Imperative Energy is now supplying biomass energy to Abbey Vocational School in Donegal town. It’s the first school in the country to use woodchip under an ESCo arrangement. “The school wanted to go green but had no capital budget.” O’Carroll explains. Imperative financed, designed and installed a customised biomass solution, retaining ownership of the equipment and selling the energy to the school. “We tabled a draft contract which included a cost per kilowatt hour of heat that we would deliver. That was acceptable to them, so once the contract was signed, we went ahead and deployed all of the equipment and did a complete installation, including tapping into the building management system…Because the heat from the biomass boiler is cheaper than the heat from the oil boiler, the biomass boiler has priority but if there’s a peak load and the biomass boiler needs help, then the oil boiler kicks in. The school pays for the oil directly, and they only pay us for every kilowatt hour of heat that we deliver across the heat meter.”
“The pricing model for different clients varies; there’s an element of negotiation in that. Some clients like the school wanted us to link to the energy price index as opposed to the general price index. They didn’t want to be in a situation where – it’s an unlikely scenario but it’s always a possibility – if oil prices dropped significantly in two or three years time, they didn’t want to be stuck paying for more expensive renewable energy, so basically we’ve given them an instant saving and essentially that saving is guaranteed across the seven years of the contract. If the energy price index goes down, our price goes down, and always maintains a 15% saving…It’s a risk free scenario for the school…If the boiler goes down for whatever reason, or we don’t have an appropriate maintenance schedule and there’s outages, the oil boiler kicks in automatically so the school will never be without heat.” The 220kW system works in conjunction with a 3000L buffer tank, which together should provide 80% of the school’s heat requirements over the course of a year. Imperative Energy has also just commissioned a similar system in the Abbey Manor Hotel in Leitrim. Solar panels combine with a biomass boiler to feed a buffer tank in the plant room which then links to the hotel’s existing heat = distribution system. “That’s the same model; an energy supply contract. We have carried all the capital costs, there’s no capital outlay at all on behalf of the hotel. There’s a heat metre so anything that we supply from the solar or the biomass system we get paid for.”
District heating will also form a central element of SEI’s Dundalk 2020 project. A 16Km2 area at the southern end of the town has been designated a sustainable energy zone which will boast a range of sustainable innovations including renewable street lighting, smart metering and the retrofitting of insulation on existing buildings. In addition, a 4 megawatt biomass boiler will fire a district heating system serving a range of commercial, domestic and community clients.
Combined heat and power (CHP) represents the next step in efficient energy delivery and it’s here that the ESCo model really comes into its own. In Ireland, the leading players in CHP delivered through ESCo are Dalkia. The company has just commissioned a trigeneration plant in AIB’s Bankcentre in Dublin, a 1 megawatt system that will provide heating, cooling and electricity to the client. “We developed it.” says Mark Coyne of Dalkia. “We financed it, built it, designed it, we commissioned it and now we still own it but it’s providing heat and electricity and cooling to the client in a fifteen year contract.”
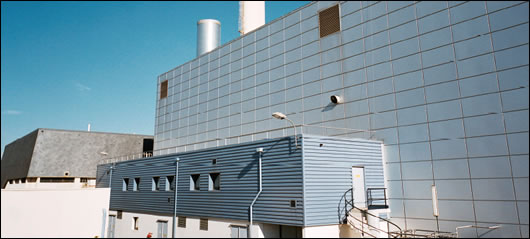
Since December 2001, heat and domestic hot water has been produced and distributed to residents of Les Ulis, near Paris , by one of the most efficient cogeneration plants in France. The facilities managed by Dalkia serve 88,800 homes.
Combined heat and power, though not a renewable technology per se, is attractive because it taps into the waste energy typically generated through conventional electricity production methods. = Coyne explains the principal behind the technology. “Every time you create a rotational force as in the engine of a car, heat is a by-product and in the case of reciprocating engines there are two sources of heat. One is the exhaust, so you recover some of that heat, and the second one is through the jacket of the machine.” CHP uses the electricity generated and siphons off the excess heat to be used for hot water and space heating requirements. “Typically you’d expect the CHP to offer a 25% efficiency improvement over electricity import and separate heat production…That’s why it’s considered to be environmentally efficient. That’s why you’ll find SEI promoting these and that’s why in the government white paper on energy there’s a target of 400 megawatts of CHP by 2010 and 800 megawatts by 2020.” In Ireland, CHPs typically run on natural gas; gas engines for CHPs of up to 5 megawatts and gas turbines for large scale installations. While both of these technologies are typically operated on natural gas, renewable fuel CHPs running on biodiesel and biogas are commercially available. “With renewables such as biomass, where you’re burning wood, you’re producing heat which creates steam which then drives a steam turbine.” says Coyne. “You’re into a different ballgame entirely, and the scale ratchets up. It doesn’t become economical to build biomass CHPs below about ten megawatts.”
That said, biomass CHP is currently under development. Brendan Marren of CES Energy says his company is currently working on a number of projects which he hopes will be up and running by the end of the year. “It will hopefully be just biomass – we wouldn’t limit it to just wood chip or wood pellet. The great thing about a gasification type process is that you’re not limiting yourself to a biomaterial that needs to be manufactured or produced. Readily available waste can be put into it.”
There is however another form of CHP technology which runs on entirely renewable materials. The process of Anaerobic Digestion (AD) involves the breakdown of organic waste by bacteria in an oxygen-free environment. It can take place in a specially designed AD plant or naturally at landfill sites. Duck processors Silverhill Foods run a unique AD combined heat and power plant at their headquarters in Emyvale Co. Monaghan. MD Stuart Steele says that it all started because of a waste disposal issue. “The problem is, because we farm everything ourselves we have an awful lot of slurry in a central location. Once we stopped thinking of that as a waste stream and realised it was an opportunity, that’s when our thinking changed.” Instead of spreading the slurry as is conventionally done, Steele decided to process it. The wet slurry is compressed to remove the liquid and the solid material is then pelletised and sold Europe-wide as a fertiliser. “The liquor that’s squeezed away, because we’ve taken the solids out of it, can go through a high rate anaerobic digester. Typical AD might take 21 days, and so the unit would have to be big enough to hold 21 days worth of slurry, which would be immense. With high-rate AD, the footprint doesn’t need to be big; you’re talking about a gas tanker as opposed to a football pitch. The liquor goes in and the bugs eat the remaining solids that are in the liquid under a vacuum, that generates gas, that gas in turn goes into our CHP and generates electricity through that. It’s just basically a generator in a box.” Currently in the process of commissioning the system, Steele says it’s vitally important to do the research and size the plant correctly. “We’re not really doing this as a commercial entity, we’re doing it because it solves our waste minimisation problem, and you do get the green energy associated with it. It appeals ideologically because that’s the ethos of the company, but it also appeals because we are generating about 20% of our electrical load here onsite.”
With over 60,000 district heating installations to its name, Germany company PEWO is a market leader on the continent in the supply of bio-energy and heat network solutions. Now partnering with Total Energy Management Limited (TEM) in Galway, the company plans to bring its extensive expertise to bear on large scale renewable heat projects in Ireland. “Central heating plants are excellently suited for the supply of large buildings and communities.” says Robin Petrick of PEWO. “Thus far, PEWO has equipped the communities of Reit im Winkl in Germany, Lech am Arlberg in Austria and Bruneck in Italy with energy solutions.” Also active in the combined heat and power market, the company’s CHP plants run on natural gas as well as biogas, landfill and sewage gas, while in stationary and mobile central heating plans heat, biomass is the preferred technology. Control systems also form a central part of the company’s offering. Similar to Igneus’s telemetry solutions, PEWO’s integrated, automatic control processes allow centralised monitoring and optimisation – essential elements of any district or large scale heating solution.
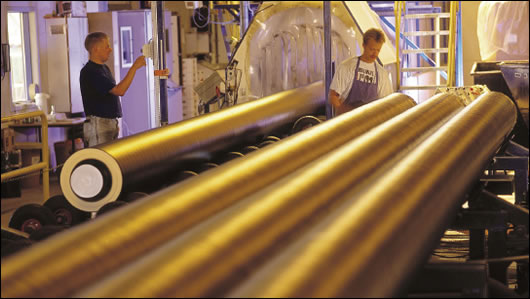
Logstor's preinsulated pipework for district heating is manufactured in a controlled factory environment
For companies with neither the resources nor the ideological motivation, the central advantage of the ESCo-run CHP is its impact on the bottom line. CES Energy has just commissioned a trigeneration plant for A&L Goodbody in Dublin. “The energy supply company model has zero capital costs for the customer.” says Brendan Marren of CES. “They then enter into an energy contract with us to supply them energy at a certain discount… Their electricity and their cooling would have been electricity obviously and then their heating was gas, so on both gas and electrical they’re saving around e50,000 a year.” In order to further bolster their product offering, CES are now looking into the provision of electricity generating Solar PV panels alongside gas and biomass fuel CHP.
Solar PV is the key speciality of renewable energy company, Coolpower. The company’s MD, Tim Cooper, is the man behind the landmark Green Building in Temple Bar. Incorporating a wide range of sustainable technologies, the Green Building is now in its fourteenth year, and it’s Cooper’s experience with PV panels there that lead directly to the establishment of the company. He explains why. “After twelve years I reviewed everything we had done in the Green Building, and what stood out to me as by far the best performer was the PV panel on the roof. I had neglected everything deliberately to try and determine how much maintenance they actually needed and everything required a fair amount; the turbines a massive amount, the solar thermal a fair bit of maintenance but the PV panels required not one single jot of maintenance – in fact the only thing I had to do in those twelve years was to replace three fuses, and that was after a lightning strike.” Interest in the systems, both commercial and domestic, he says, is intense. The company installed its first large commercial array at Newbridge Silverware in April. Given the levels of sunshine throughout that month, they could scarcely have picked a better time. “The output from that has been utterly staggering.” says Cooper. “Completely astonishing. It’s the first phase in a two phase project we’re doing. The whole installation is 35kW. It’s been completely astonishing. There are just dropped jaws all over the place.”
Also operating in the ESCo space, the company is currently installing a PV array on Limerick County Hall. “Our array is picking up 100% of the weekend load, and about 10% of the day load, so they will buy the 90% for weekdays on the market from whoever will give them the best price, and that’s the tariff we’ll charge for the electricity we generate.” In new-build situations, the company can also integrate PV into the glazing. “Part L of the building regulations demands that glazing be reduced to counter solar gain (to prevent overheating) and one way of doing that is putting PV panels in place of what would have been glazing.” Translucence is reduced and the sunlight that is prevented from entering the building is used instead to generate electricity.
It’s in the generation of electricity however that all of these technologies run into a bureaucratic speed bump. “There’s fantastic opportunities for CHPs in residential schemes,” says Dalkia’s Mark Coyne, “but unfortunately we can’t take advantage of it now because the regulator will not let you sell the electricity from CHPs to more than one end user…It’s a golden opportunity that’s being wasted. You’ve all these apartment blocks going up with individual gas boilers and they’re all consuming electricity of course, but you can’t put CHP in any of those.” It’s a frustration that’s evident across the industry.
Noel Walshe has for many years been representing Logstor, Europe’s largest district heating pipe manufacturer and he specialise in the supply of equipment for heating networks. He points out that the heat source for such systems on the continent is generally provided from municiple CHP plants. “As none of our generating stations are set up for hot water production, without the political will, district heating will continue to be reliant on large scale biomass.” he says. “In the meantime electricity can only be generated at around 35% efficiency - this is a thermodynamic limitation and is no reflection on the ESB. However, if we could also use the waste heat for both heating and cooling then our overall efficiency would rise to over 77%. This would give us a major reduction in energy consumption as no additional heating source would be required to heat of our buildings. This has to be our next move in reducing our energy requirements”. Of course the same limitation applies to cars with only 35% of the fuel used being converted to mechanical energy. The rest has to dissipate. “However,” says Walshe “if we used the Dart or Luas instead of the car and had CHP we could be very smug in the knowledge that the same energy that is being used to generate the electricity which propels us down the tracks is also being used to heat our homes”.
The government does explicitly support CHP however. In the 2006 Budget, presented to the Dail in December 2005, the Minister of Finance announced the allocation of e65 million over the period 2006 to 2010 to “launch several innovative grant schemes relating to biofuels, combined heat and power, biomass commercial heaters and domestic renewable heat grants”. An indicative allocation of e11m was made for a CHP programme to run in the 2006 to 2010 time frame. “The scheme is in its infancy,” says Ann Margaret Saunders of SEI, “however we have been actively marketing and promoting it since February 2007 so we hope to see an increase in uptake in the next couple of months.” Thus far, fourteen projects have been approved, two have been completed and the total amount of grant aid committed stands at e877,632.
Mark Coyne at Dalkia believes however that the CHP deployment scheme, because it concentrates on the capital expenditure element of CHP rather than the ongoing costs, is essentially misguided and ineffective. To explain why, he introduces the concept of ‘spark-spread’. “Spark-spread is the difference between the cost of electricity and gas, and because effectively CHPs are transforming one form of energy into another – in most cases, they’re converting natural gas into electricity and heat – there has to be sufficient differential between the cost of gas and cost of electricity, and not only that, there has to be predictability in the differential, and that’s one of the main detractors of CHP uptake. A tariff support mechanism or a price which would be underwritten by the Department of Communications, Energy and Natural Resources as a support mechanism to the industry is needed. Why would they do that? In order to promote an energy efficient mechanism that’s been proven in countries like Denmark where 50% of all electricity production is through CHP…If you want to accelerate the process, if you really want CHP to take off, you can do it very easily at the stroke of a pen…”
- Articles
- district heating
- Economy of Scale
- igneus
- wood pellet
- Fin Engineering
- Hot Water Plantroom
- cogeneration
- ESCOS
- chp
Related items
-
New heat pumps and pellet stoves from Waterford Stanley
-
District heating and passive house - are they compatible?
-
Affordable passive scheme that beggars belief
-
Ecological passive house built on tight budget
-
Viessmann to showcase pioneering fuel cell system at Ecobuild
-
Opinion
-
Thermal bridging
-
Isover awards
-
Carlow A1 upgrade
-
Zero waste
-
Clonakilty eco house
-
Cutting oil dependecy