- Insulation
- Posted
Ireland's most airtight house?
An experienced timber framer with an eye for detail, Tim O'Donovan set about building a low energy stick-built home in the Cork countryside and achieved a staggering level of airtightness. Words: Lenny Antonelli
When it came to building his house in Timoleague, Co Cork, Tim O'Donovan only really considered stick-built timber frame. "I've been timber framing for the last 15 or 20 years,” he says. “I didn't really consider anything but timber frame."
O’Donovan built his first timber frame house with his brother in 1995. Returning from a year of traveling with his family in 2004, he started talking with Toby Hatchett, now of low-energy timber frame company Greenhus.
"At the time he was a cabinet maker by trade, but he had this dream to build a low energy building," O'Donovan says. The two built a timber frame workshop together, and O'Donovan's interest grew from there.
"I got a lot of info from Toby on low energy building and set off on a mission to build the ideal building," he says. "My inspiration came from the building techniques Toby was looking at."
Work on O'Donovan's house in Timoleague, Co Cork was nearing an end as Construct Ireland went to print. If O'Donovan was looking to create the ideal house, he's certainly got it in one regard: airtightness. His house is phenomenally well sealed - it boasts an air changes per hour (ACH) figure of 0.11 (ACH) at 50 pascals, and an air permeability of 0.29 m3/h/m2 at the same pressure. The ACH figure is the best Construct Ireland can recall publishing, and looks all the more impressive when compared against the Passivehouse Institute’s famously tough standard – 0.6ACH.
For O'Donovan, the result is proof that stick-built can beat prefabricated timber frame for airtightness if the builder pays careful attention to detail. "Things can get torn in transport. I've seen frames come to site with membranes damaged," he says of prefabricated systems. "As you build [on-site] you close and you seal, and you see every joint as the builder."
But he says that regardless of the method of timber framing, care and attention yield good results. "There are some very good timber frame companies out there that pay a lot of attention to detail," he says.
O'Donovan used membranes and tapes from Siga throughout the build. For the wind tight layer externally, he used Siga's Majcoat membrane and Wigluv tapes. All Siga's exterior products have been certified as driving-rain proof by the TU Berlin technical institute, says Siga's Jason Byrne. "The trick with Majcoat is that it's really breathable but it's also driving-rain proof," he adds. He says Wigluv is the only water-based, solvent-free tape on the market that’s driving-rain proof, breathable and 12--months UV-stable.
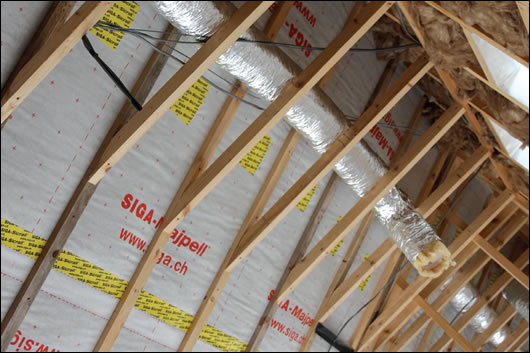
Siga’s Majpell membrane was used on the inside of the build-up, as were the Swiss manufacturer's (bottom) airtightness tapes
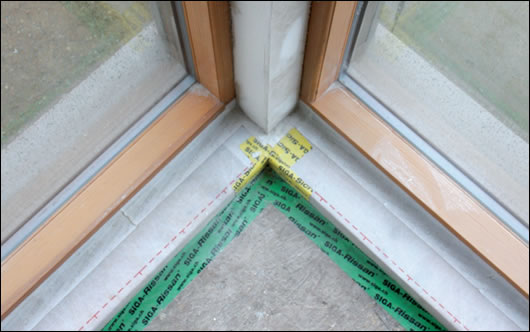
On the inside of the build-up, O'Donovan used Siga's Majpell membrane with Rissan and Corvum tapes. Rissan is used for circular penetrations, while Corvum comes in two forms: a folded 48mm-12mm tape for window and door frames, and a folded 30mm-30mm tape for corners, joists, purlins and skylights.
Byrne says the external Majcoat membrane is much more vapour permeable than the internal Majpell – while the former has has an SD value of 0.1 the latter's SD value is 5, meaning any moisture in the building structure can migrate out. The SD value measures vapour diffusion resistance – the lower the SD value, the more vapour permeable the substance.
Mark Shirley of BER consultants 2eva performed the blower door test – his report sharply illustrates just how airtight the house is. It reads: "Prior to undertaking the actual test, the airtightness testing machine was run to enable us to identify areas of weakness. None were found."
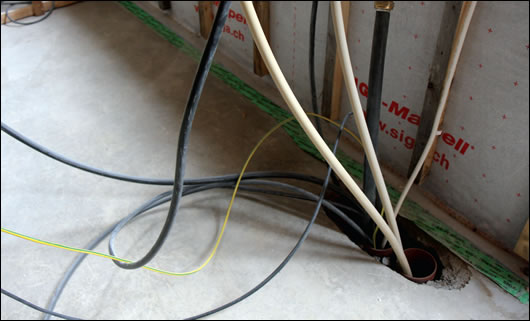
Mechanical and electrical services were run through the floor to avoid compromising the envelope airtightness
It adds: “There were only two areas where minimal air leakage was identified. These were at the junction of some window sections and also in the window in the room shown as the wine cellar on drawings.” Sorting these should improve the final result even more.
Shirley says O'Donovan's attention to detail on the project was "incredible". "The placement and the folds were exceptionally good," he says. At this stage of any project Shirley points out there's a danger a tradesperson will come on site who isn't familiar with airtightness and damage the airtight layer – but he says this is unlikely considering O'Donovan's quality control.
Shirley calculated his results by doing pressurisation and depressurisation tests and averaging the two results, and he says O'Donovan's house is the most airtight he's ever tested.
Sustainable energy consultant Xavier Dubuisson of DW Ecoco, a friend of O’Donovan’s who looked over the U-values and overall energy performance of the house design, was equally impressed. "He was very meticulous," he says of O'Donovan. "It's very difficult to apply airtightness if the site is not tidy and clean. It's part of his way of working. Anytime I've been there on a Friday afternoon the lads are cleaning the machines, cleaning the house. It's part of an overall quality approach to construction."
From the inside out, O’Donovan's wall build-up features 10mm Rigadur board, a 10mm unventilated service cavity, the Majpell vapour control layer, 230mm of Warmcel, 15mm OSB board, a Majcoat wind tightness membrane, followed by a 35mm ventilated cavity. The walls have a U-value of 0.20 W/m2K. The building is finished with Tegral Bluclad cement board, and clad variously with Douglas Fir, stone and a Weber render on different parts.
The roof features 10mm Rigadur board internally, followed by a 20mmm unventilated service cavity, the Majpell vapour control membrane, 230mm of Warmcel insulation, a Majcoat wind tight membrane, a 20mm ventilated air cavity,18mm OSB sarking board, and another Majcoat membrane. One section of the roof is finished with Ecostar slate, the other with zinc.
O'Donovan used Warmcel insulation in both his roof and wall build-ups, and it was blown-in by McHugh Insulation. Produced by Excel industries, Warmcel is made from recycled newsprint. Excel manufacture Warmcel in Wales from returned newspapers – those that don't sell in shops. "We have a difficulty getting clean grade paper from households or other recycling processes because they get contaminated," says Excel's Chris Scott.
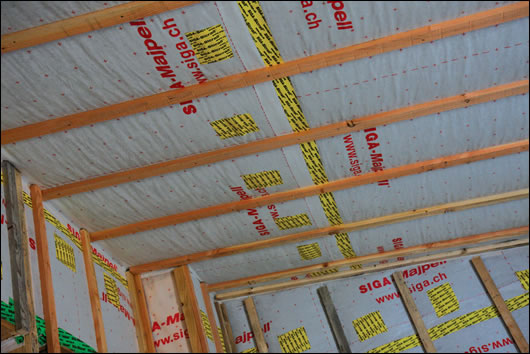
Great attention to detail was taken with the airtightness layer on the inside of the construction
The company is currently taking part in a pilot project in the UK midlands to collect newspapers from homes. A charity oversees the collection, asking householders to keep their newspapers clean and dry, and then selling them to Excel to raise funds.
According to Excel, Warmcel has a “global warming potential” of less than zero, an ozone depletion potential of zero, and that it's VOC and CFC free. The BRE gives blown recycled cellulose insulation an A+ rating in its Green Guide to Specification.
O’Donovan used Warmcel 500, which can be blown damp or dry – the latter is used for close-panel timber frames, the former is sprayed on in open-panel systems. "The moisture releases natural starches in paper that helps the fibres bind to each other and to the back boards," Scott says.
Scott says that Warmcel used in Ireland is manufactured from Irish newspapers, and that he's noticed more demand for sustainable building products in Ireland compared to the UK.
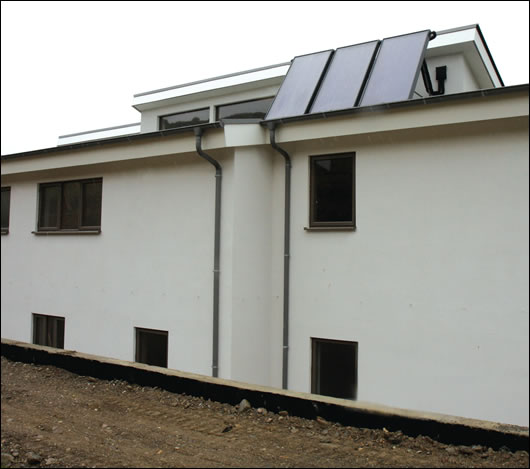
Hot water is partially supplied by six square metres of Gasokol solar panels supplied by Universal Solar, with an electric immersion as back-up
He also says Warmcel offers an airtightness advantage. "Any blown material will fill the space much better than a hand cut applied one,” he says.
In Timoleague, O'Donovan's timber frame system uses Canadian lumber size (CLS) timber, supplied by the Murray Timber Group. CLS is a u smooth timber standard that originated in Canada but is now popular worldwide. "If you go to a builders suppliers and ask for a six by two, you can buy a hairy six by two or a six by two CLS," he says. "It's a nicer timber to handle and it's a lot straighter. The cutting is a lot more precise and it's more uniform." All the wood used is from Irish-grown pine, and Murray Timber Group is a member of the Forest Stewardship Council.
O'Donovan installed double-glazed timber-aluclad windows throughout, made by Estonian manufacturer Viking. The windows – supplied by the Cork Window and Door Store – are double-glazed, argon-filled and have an overall U-value of 1.4 W/m2K.
Not surprisingly given how airtight the house is, O'Donovan is planning to install heat recovery ventilation. He hadn't chosen a system as Construct Ireland went to print – he's leaning towards one from Dutch manufacturer Brink – but he has installed Sonodec flexible insulated ducting.
O'Donovan says it's the "Rolls Royce of flexible [ducting]". He adds: "I went for flexible because I have a truss floor downstairs and it was easier to get flexible through the truss floor."
He opted for solar thermal too – six square metres of flat plate Gasokol panels supplied and installed by Cork company Universal Solar. The panels heat water that's stored in a 300 litre dual coil cylinder, backed up by an electric immersion.
"They're of the highest quality performance wise," says Universal Solar's Paul Heaphy. The company has been supplying and installing the Austrian manufacturer's solar panels for seven years.
Heaphy says that because Universal Solar both supply and install the panels, there's tighter control over quality."We supply and install – when you do that you know what you're doing and can stand over the system."
O'Donovan's planning to put in two wood-burning stoves too, one in each of the house's living rooms. They won't be more than 8kW each, he says.
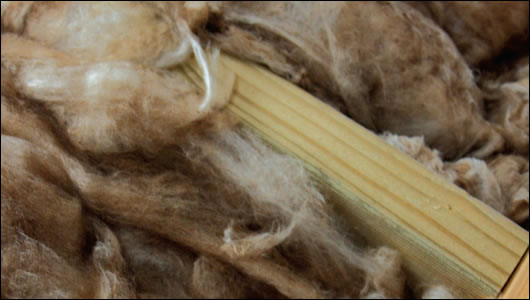
Knauf Loft Roll was used as acoustic insulation in part of the house
But he won't be putting in a boiler for central heating – at least not unless he finds he needs one when winter arrives. However he’s set up two space heating zones just in case. The house doesn't quite meet the Passive House standard, but O'Donovan thinks that HRV and the stoves, combined with any passive gains, could be sufficient.
He measured the temperature inside at 21C on a July morning when it was 14C outside, he says. "It's been 30C inside sometimes, there were days in there when it was a bit uncomfortable to work," he says. The house is plumbed for central heating if he does need to put in a boiler.
He chose some green materials for the house too: all concrete for floors and foundations contains Ecocem's ground granulated blast-furnace slag (GGBS), a derivative of steel industry waste that acts as a substitute for traditional portland cement (which is responsible for about 5% of man-made carbon emissions).
O'Donovan chose Ecostar slates instead of traditional slates as a finish for one of the two roof sections. The slates are manufactured by US-based Carlisle Construction Materials – the company says they’re manufactured from post-industrial recycled rubber and plastic, and that the slates themselves are completely recyclable at the end of life.
With the house sitting on a hillside, O'Donovan’s going to think about putting up a wind turbine in future. “We get a lovely breeze down the valley,” he says.
O’Donovan’s timber-framing company Sustainable Building Services is currently working on various projects in County Cork. He says the company is dedicated to “bespoke low energy building”, and that they aim to use as much “sustainable Irish material” as possible. “It’s attention to detail I want to get across,” he says. “We’re always looking for ways to improve the thermal efficiency. He also runs Housewrap, a company that provides a range of airtightness services.
Of course his house isn’t just green – it looks pretty good too, and the design takes a contemporary approach to the vernacular. "It fits in well with the landscape but is modern [and] has elements of vernacular architecture," Xavier Dubuisson says.
At 390 square metres, it’s certainly on the large size. But with its quietly contemporary design, palette of green materials and staggering airtightness, the house is a testament to O'Donovan's craftsmanship.
Selected project details
Builder/timber frame: Sustainable Building Services
Airtightness testing: 2eva.ie
Airtight membranes & tapes: Siga, installed by Housewrap
Solar thermal: Universal Solar
Wall and roof insulation: Warmcel, installed by McHugh Insulation
Timber: Murray Timber Group & Clonoe Timber
Window supplier: Cork Window & Door Store
Recycled rubber and plastic slates: Ecotech Recycled Products
- Articles
- insulation
- Irelands most airtight house?
- Timoleague
- Greenhus
- airtightness
- Siga
- membranes
- Majcoat
- 2eva
- Rigadur
Related items
-
Why airtightness, moisture and ventilation matter for passive house
-
Airtight delight
-
Ireland’s first 3D printed homes insulated with clay foam
-
Partel launches paper-based membranes
-
Unilin Ireland launches embodied carbon report
-
Ecological launches Retro EcoWall for internal wall insulation
-
Partel’s airtight membranes now certified for passive house construction
-
Xtratherm name changes to Unilin
-
Ecological Building Systems launch Retro EcoWall for internal wall insulation
-
Mass timber masterwork
-
Kore launches low carbon EPS
-
Partel obtains EPDs for airtight membranes