- Renewable Energy
- Posted
On the plus side
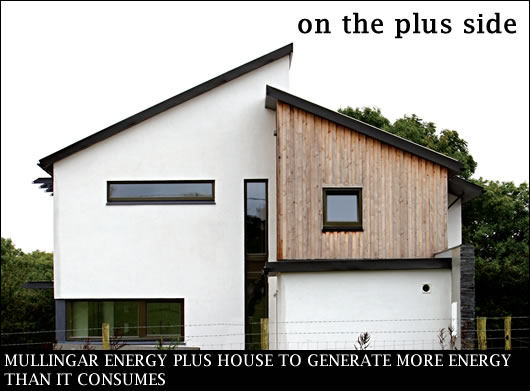
Nothing focuses the mind like a target. The growing impact of Building Energy Ratings (BER) is increasingly encouraging Irish people to aim for the highest energy rating they can. Patrick and Niamh Daly’sJohn Hearne house in Mullingar takes this trend to the next level, using a myriad of sustainable green materials and technologies to become a net energy producer and go beyond the limit of the BER scale. visited the nearly completed house to find out more.
At his site in Clonkill, Co. Westmeath, Patrick Daly set out to build the lowest energy house in Ireland. As the project approaches completion, he anticipates a negative energy consumption of between 25 kW/m2/a and 30kW/m2/a. His home will generate rather than consume energy.
Daly, an energy consultant with his own practice, BESRaC, and former lecturer in environmental design at DIT is calling the project the Integrated Low Energy and Environmental impact Design (iLEEiD) demonstration house. It incorporates Passive House Institute (PHI) principles of passive solar gain, super insulation, air-tightness and heat recovery ventilation, and is targeted to substantially exceed the PHI space heating target of 15 kWh/m2/yr, thereby removing the need for space heating.
A solar thermal array is the primary source of domestic hot water. This is backed up by a small heat pump fed by dual collectors; a ground source array and an innovative warm grey-water recycling tank. Systems integration will boost the efficiency of the renewable solutions, while a network of photovoltaic (PV) panels is expected to comfortably meet the house’s residual energy requirements, all of which have been reduced to a minimum.
Daly is also keen to stress that the project has not sought the zero energy target at other environmental costs; he has also made extensive use of ecological materials and local tradesmen in order to minimise the building’s carbon footprint and embodied energy.
On first glance, the building’s form is not passive house textbook – this is a large, diffused house including home office with a split level interior, and a stair core that will ultimately be glazed off. Orientation and layout however combine to override the anomaly of the building’s form. The long, narrow site lies just five degrees off the north/south axis, with the front elevation facing north. Office space, all bathrooms, utility, plant-room, the stairs and some bedrooms have been concentrated here, with just 16 per cent of the house’s total glazing. By comparison, 62 per cent is found on the southerly elevation and 22 per cent divided between east and west. “Low temperature based rooms are all north,” says Daly, “and all the main living spaces and the bedrooms are south. So living, kitchen and dining areas have a complete south aspect.” The site itself is unobstructed on all but the south west side, where a bank of mature ash trees shelters the house from the prevailing wind.
The front door is housed within a glazed air-lobby, a semi-external area which lies outside the conditioned space. In addition to the main front door, there’s an additional ‘informal’ access door which gives direct access to the utility room. Here, within this block, all of the house’s ‘wet’ areas are found. Ensuite and main bathroom are upstairs, with the plant room, utility room and downstairs bathroom directly below. Containing these facilities in such a compact space eliminates long wet service runs and consequent heat losses. Downstairs, the kitchen and living room run the full length of the southern elevation and are extensively glazed to maximise solar gains. Upstairs, the traditional long, dark corridor is avoided by opening up the landing space with an open-plan, fully-glazed family den which lies between the two bedroom wings. Here too, high level opening vents provide additional natural light and summer ventilation. Because of the risks of thermal buoyancy in summer, Daly intends to close off the stairs using glass doors. “Otherwise,” he says, “in the summer particularly we could end up with much higher temperatures up here.”
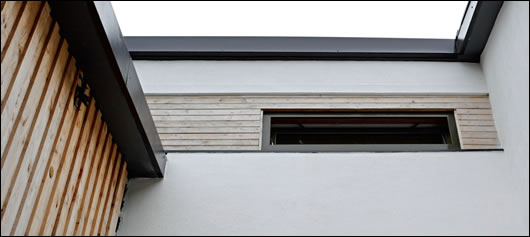
Glazing is kept to a minimum to the north
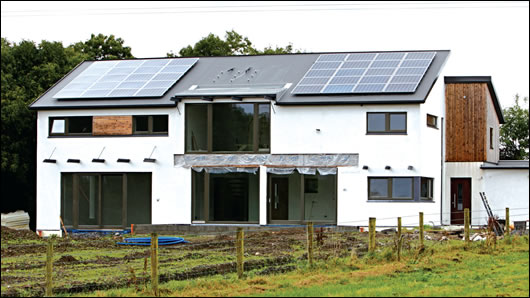
Substantial glazing to the southerly elevation to maximises passive solar gain
To reduce the risk of summer overheating, brise soleil has been specified over south facing glazing. The brackets are steel, while the screens themselves, of Kilkenny cedar, will keep out direct sunlight for three months during the summer. Downstairs, the flat roof of a conservatory to be built in front of the kitchen, but outside the conditioned space, will function in the same way.
The house has several standard construction features. There are strip foundations, a blockwork rising wall and a 140mm timber frame provided by Riverview Timber Frame Systems in Westmeath. Daly insisted on using Irish timber, and that only baseplates be chemically treated. “In a very air-tight house I’d have a concern about toxicity.” He says. “Anything that might leak out as a gas would stay in the house, so we’ve tried to keep chemicals to an absolute minimum in the house.”
The frame however is non-standard. There’s an external structural 140mm stud, while a separate, internal, non-structural 89mm stud serves three purposes. It provides depth to take insulation, it carries the internal finish, and vitally, it removes the risk of thermal bridging. This approach also has the advantage of being lightweight. “Although we’ve a wide wall construction,” says Daly, “we don’t need a wide foundation. This is a half-meter wide wall…A 300mm cavity block wall would need a metre-wide foundation. We’ve half that, so the whole construction technology has been based around reducing the footprint as much as possible. We’ve more than halved our concrete use in the foundations and by using low carbon cement from Cemex we’ve halved the carbon content of that again.”
Panelvent from Ecological Building Systems is fixed to the outer stud. This is a wood fibre board which gives the structure racking strength and wind resistance. It’s also vapour diffusion open, and in keeping with the design ethos, contains no manmade glues, relying on lignum, the natural glue that occurs within wood. To boost wind-tightness, all external joints were taped using Pro Clima Tescon tape, also supplied by Ecological Building Systems.
External wall insulation is a soya-based foam spray, BioBased 501 provided by Econstruction Products in Dublin. “It behaves like a polyurethane foam,” Peter Woodcock of the company explains, “but it’s open cell as opposed to closed cell. Traditionally, polyurethane foams would have been rigid, closed-cell foams, which were used in a lot of refurb work, applied between rafters. The problem with that was because it was closed cell, there was little vapour diffusion and the timbers were smothered, eventually resulting in dry rot.” The foam is water rather than gas blown and expands to 100 times its volume. Altogether, 400mm of BioBased 501 went into the stud.
The Pro Clima Intello Plus intelligent vapour check and air-tightness membrane was fitted to the internal stud, and taped using the same Tescon tape used to seal joints on the external Panelvent board. “This achieved a very air-tight construction,” says Niall Crosson of Ecological Building Services. “But also, Intello is an adaptive membrane, and rather than staying permanently vapour resistant, it can alter from being vapour resistant to vapour open, depending on the direction of the vapour within the construction.” A service cavity of 25mm for electrical services and 38mm for water was installed outside the Intello membrane, with the internal wall finished with Fermacell from Richmond Building Products. This is a fibre board composed of recycled paper and recycled gypsum which provides excellent racking strength, as well as enhanced acoustic properties. Fermacell doesn’t require skim coat but comes with its own proprietary, quick drying treatment. Unlike conventional plaster finishes, it doesn’t introduce large amounts of moisture into the construction.
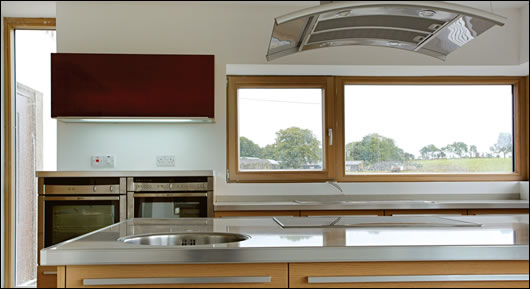
The Cucine Lube kitchen from Collier Kitchen Supplies was chosen because Lube uses only certified ecological panels in their cabinets and have a zero waste policy

One of the two banks of solar photovoltaic panels, supplied by CareyGlass Solar, which will play a key role in achieving energy plus status
“We air pressure tested the house a number of times during construction,” says Daly, “and kept close track of that. The first test was done when we had windows and doors and just taped Panelvent externally. We got a Q50 of 0.68 at that stage, so it’s wind-tight on the outside as well as being air-tight on the inside, which is really important for insulation performance. A lot of people focus on an internal air-tight and ventilation control barrier but if cold air is getting into the insulation zone, it ceases to function.” Following the addition of the internal barrier together with the various finishes, the Q50 dropped to 0.55. “I’m expecting to get to the passive standard of 0.37,” says Daly. “We don’t have all the services sealed yet, plus the windows have to be readjusted.”
The house has three separate external finishes. Kilkenny cedar – also used on the brise soleil – is used extensively, alongside limestone cladding and lime render. On rendered areas, the external walls are first battened and fixed with Heraclith-BM, a magnesite-bound single-layer wood wool slab from Skanda in the UK. The lime render, from Hempire, is another natural, breathable material. “The material is hydroscopic,” says Marcus McCabe of Hempire in Co. Monaghan, “which means it allows moisture to move through itself, so this helps to keep buildings dry.” The product is Irish made from local materials – hemp, lime and recycled aggregates. “There are some very simple advantages. One is the weight. Our material is about half the weight of a sand and lime or sand and cement plaster…and because it’s lighter, it doesn’t pull itself off the wall…The hemp fibres in there are acting as part of the matrix of the plastic mass. They’re helping to hold it together so that it doesn’t cleave.” In addition, as the material dries out, some of the lime migrates to the surface, giving a glazing effect which helps the weathering process.
As mentioned, low carbon cement was used in pouring foundations. The 50 per cent GGBS mix, provided by Cemex, was made in the plant in Ballymahon from GGBS imported from Poland. “We’d have a minimum of 25% GGBS as part of our cementitious content within the mix as standard, unless otherwise specified,” says Andrew Goode, Cemex’s central region sales manager. “We use it all the time. We find it gives better finishes, it gives a nicer colour and a nicer texture.” Above the conventional hardcore, sand blinding and radon barrier at foundation level, there’s 350mm of expanded polystyrene, topped with a 150mm rammed earth floor and 50mm of lime screed. Earth was used not alone because of its ecological credentials, but because it has a much greater thermal storage capacity than concrete.
Installing the earth floor brought the project its only major setback. “It went down twice,” Daly explains. “The first time, I wasn’t onsite and it wasn’t wet enough. The clay didn’t bind, so we had to take it up by hand and remix it outside in an industrial mixer. When we brought it back, it was much wetter. We compacted it as it was going down, and you could feel the firmness.” The delay had major programme implications. Speaking with the benefit of hindsight, Daly regrets only that he didn’t use the onsite subsoil rather than the brick making clay brought in by the manufacturer. “So it ends up a very low carbon floor that cost me a fortune. But that’s part of the experiment.”
One of the central elements of Daly’s design philosophy has been to marry two often divergent schools within the environmental buildings movement; low energy design and environmental impacts of materials. He presented a paper on the project at last year’s Passive and Low Energy Architecture (PLEA) conference in Dublin. “There’s a tendency to achieve low energy with high energy materials, which might make sense when you’re at a certain level of energy consumption, but when you’re starting to get to passive and beyond, there’s a number of papers out there which show that using high energy materials to get energy performance reductions can actually have a net energy disadvantage, even over a 25 or even a 50 year life span.”
“One study looks at increasing insulation thicknesses and it’s shown that not far beyond a U-value of 0.2 W/m2K, over a 25 or 30 year period, you can have a net energy disadvantage by using high energy insulations. We’re actually getting to what I call a threshold, where energy in use and embodied energy are starting to impact on each other.” He points out that in a high energy consumption context, embodied energy is only 10 to 12 per cent of lifespan energy usage, but in a low or no energy context, embodied energy has the potential to increase massively as a proportion of the house’s total energy consumption. “We’ve applied that principle to try and offset carbon and offset high embodied energy materials, so all the foundations for example are low carbon cement and were designed to be sufficient to do their task, but small.”
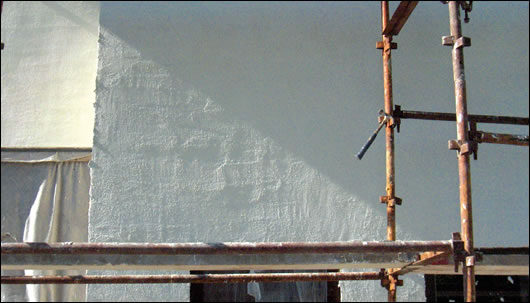
The freshly applied hemp lime render
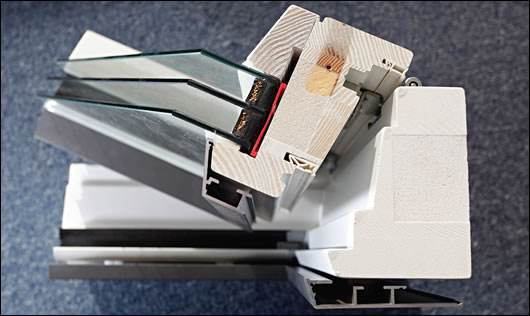
The windows are triple-glazed, of timber construction with an aluminium cladding
Roof build-up is similar to wall build-up, except instead of aligning two studs parallel to each other, they cross diagonally. As with the walls, BioBased insulation is pumped to a depth of 450mm, completing the insulated envelope to deliver a U-value of 0.09 W/m²K. 24mm Hunton Bitroc, a breathable, bitumen impregnated board provided by Polycomp Products in Dublin is installed outside the stud. “It’s a high performance sheathing board manufactured from 100 per cent sawmill waste,” says Peter O’Sullivan, director of Polycomp. “The product is unique because it’s a bituminous fibreboard with a waterproof coating, manufactured from recycled newspaper combined with bitumen. There are no other additives, so it’s totally environmentally friendly.” The board, which has a K-value of 0.050 W/m2K, is overlaid with another breathable membrane and counter-battened. As with the external walls, there are three finishes. In addition to natural Welsh slates and a green roof section provided by Moy Materials, Daly decided to use sintofoil, a non-PVC ecological TPO membrane, also from Moy Materials, on the extensive areas of the roof where PV and solar thermal panels are mounted. “That ended up being quite a simple strategy.” He says. “We put the PV panels on top rather than try to integrate them into a slated roof. Given the amount of services that were going up there, the flashings that would be required would have been very expensive. It was a simple job just to membrane the whole roof, apply everything to that and just flash it…And with the amount of walking around up there, it was much easier to work on than a partly slated roof.”
In completing the insulated envelope, care has been taken to eliminate cold bridging at every turn. The expanded polystyrene in the floor meets 150mm of high performance Xtratherm perimeter insulation, which meets the BioBased 501 polyurethane in the stud. Thanks again to the twin frame, this runs unbroken through the roof, maintaining that same envelope U-value of 0.09 W/m2K. In addition, because floor insulation is discontinuous, measures had to be taken to deal with the potential cold bridge. “We’ve rising walls effectively breaking the insulation in the floor zone. This doesn’t mean huge heat loss; most heat loss tends to happen at the perimeter in a floor anyway, but for additional reduction in that loss, we used Quinn lite blocks and Foamglas Perinsul SL blocks. All of the internal lode-bearing walls are done like that.”
“Perinsul is a DPC product,” says Denis McGill of suppliers Encon Insulation Ireland. “Irish building regs state you need to use a DPC, but Perinsul can be used on its own as a DPC because it’s basically insulation. It’s made from cellular glass, which is 66 per cent recycled, from old glazing, car windscreens, that sort of thing. It’s heated up until it’s molten, then it’s blown with various gasses, carbon being one, then it’s cooled down over a long period of time, under compression. That gives it its structural strength.”
In order to further boost thermal mass and improve the wall’s acoustic properties, Daly filled all the downstairs studs with the same tamped earth/hemp mix that went into the floor.
The windows are Energyframe and the doors are Thermosafe, both supplied by Variotec in Germany. “I chose them,” says Daly, “mainly because of the sliding door. There are very few passive standard slider doors out there.” Of timber construction with an aluminium exterior cladding, the U-value of the whole window including the frame is 0.72 W/m2K, while the value in the triple glazing is 0.6 W/m2K.
With energy demand driven as low as possible through passive design and material specification, the next step was to look at servicing the house’s energy needs. “The individual systems themselves are fairly standard,” says Daly. “The new thing is that they’re being put into such a low energy context that they make a huge difference, plus we’re trying to get them integrated in some measure and thereby increase their efficiency.” Under both DEAP and PHPP methodologies, total space heating design load is 10 W/m2, giving a total of 2.7kW. With space heating requirements so low, the biggest energy demand in the house is hot water.
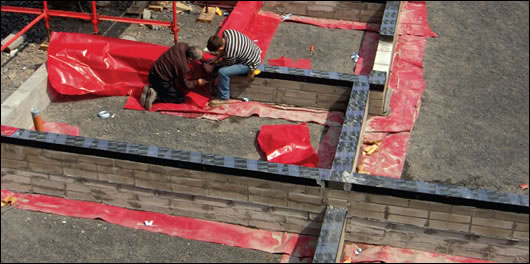
Perinsul blocks were laid on top of Quinnlite blocks to support all load bearing walls
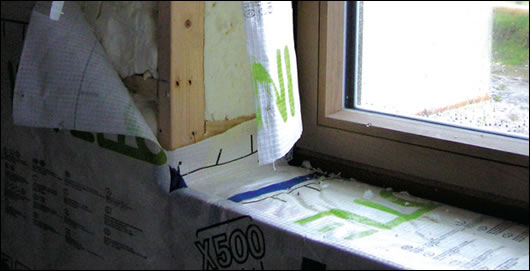
Biobased soy foam insulation still visible prior to air-tighness sealing
The solution is 7m2 of evacuated tube panels, set to be supplied and fitted by CareyGlass Solar just after Construct Ireland’s site visit. Daly explains that he chose evacuated tubes over flat plate panels in order to achieve maximum winter efficiency. “The roof is quite shallow in order to fulfil planning restrictions on height, which gives us a pitch of only 23 degrees.” The optimal pitch for Irish latitudes is closer to 40 degrees. “So we’ve split our solar water system into two banks. We’ll have a roof bank and a wall mounted bank to give us an average of 40 degrees…Between the two, we’ve got a reasonable orientation; it’s slightly geared towards winter, because that’s when we want to maximise solar gains.”
Stephen Smyth of CareyGlass Solar says that the split systems required an advanced solar controller in order to optimise their performance. “One of the reasons why the T12 and T18 systems we’re installing are so efficient is because of the CPC backing on our tubes. This is a compound parabolic concentrator, which concentrates the sun’s radiation levels at fairly diffused angles to the centre of the tube.”
A Dimplex SI 5 ME heat pump with a rated output of 2.7kW fitted by Geothermal Solar provides back-up for space heating and hot water. “What’s different about the heat pump is its size,” says Daly. “It’s small and it’s geared towards hot water, so it’s designed for a higher temperature output.” The heat pump is fed from two separate collectors; a conventional ground array in the back garden and a second in the grey-water tank in the plant room. A sensor in the grey water waste pipe will divert all warm water run-off to the tank where the second collector is located. “The idea is to harvest the warm water and extract the heat. The temperature in the tank could be anything from 20 to 30 degrees, even up to 40 degrees at times, so that increases the coefficient of performance (COP) of the heat pump very significantly from 4.5 to 5 on average.” Based on analysis Daly has carried out, he expects to harvest 2,500 kWh a year from the grey-water system. Current provisional DEAP calculations and ratings exclude this anticipated contribution.
In a further innovation, excess heat generated by the solar thermal array during the summer will be used to charge the ground collector. Surplus hot water is sent to a heat exchanger at the heat pump. The heat pump will effectively go into reverse, bringing the heat out into the soil and storing it there. The logic is that the ground will retain some of that heat through to the winter months, thereby boosting the efficiency of the pump during the heating season. “Even if it’s only a couple of degrees, we will end up having a higher efficiency for a period of time,” says Daly. “This aspect of the project is very experimental; we haven’t modelled or calculated it in detail, but if we get a couple of extra degrees across the ground collector, it would really increase the efficiency of the system in the autumn and winter.”
Hot water is maintained in a 500L dual-coil solar tank. Because the heat pump in the normal course of events will produce 35 degree water only, the heat pump coil is set low in the tank, and is much longer to provide a more generous surface area. Purpose made for the project, the heat pump coil sits outside the solar coil.
The heat pump provides space heating backup through the HRV system rather than radiators or an underfloor network. A liquid heating circuit exchanger in the air supply unit carries the heat to the fresh air supply points throughout the house. The system itself is an Xpelair Xcell 301 unit from Dimpco, also fitted by Geothermal Solar. The ventilation system is also provided with an external subsoil heat exchanger. These are common on the continent in places where air temperatures routinely reach -10 degrees C, and lower during the winter. By drawing air from a ground loop, the system takes advantage of constant year round subsoil temperatures. Daly has installed the loop, but is not going to connect – and incur the fan penalty – until he has thoroughly modelled its functioning in a more temperate climate.
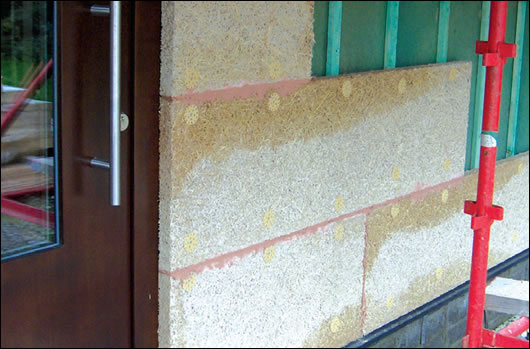
On rendered areas, the external walls are first battened and fixed with Heraclith-BM, a single-layer wood wool slab from Skanda
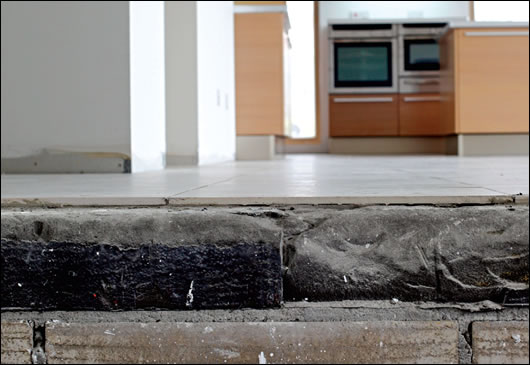
Much of the upstairs flooring is Marmoleum from Forbo Ireland, a biodegradable product made from natural materials
Integrating the grey-water harvesting collector to the heating system generated a control headache. The number of logic decisions required to optimise its use could not be handled by the heat pump’s circuit board. Since a logic board was required, Daly decided to commission a mini building management system (BMS) which would centralise all of the system integrations and deliver a level of control which would in itself make all of the systems more efficient. For example, the heat pump is programmed to go into disinfection mode and raise the tank temperature to 60 degrees periodically. A BMS would provide the integrated system with the memory necessary to bypass that disinfection mode if the solar collector had delivered 60 degrees to the tank within a preset time period. A BMS would also make the job of collecting data considerably easier – a key advantage given the level of experimentation and demonstration in the project.
“By going beyond the passive house standard, we’ve obliterated the space heating demand. The solar system has halved the hot water requirement, the grey-water system will provide another quarter, and the rest will be taken care of by the ground source heat pump: for every kilowatt we’re putting in, we’re going to get nearer four out. In addition, we have a low energy lighting strategy and low energy appliances, and we’ve met that load with a PV array on the southerly elevation. That’s estimated to generate between 6,000 kWh and 6,500 kWh a year, which is effectively more than the annual energy load of the house, which is why it becomes energy positive. On the DEAP scale, we’re way above the top bracket. If there was an A plus, we’d be there. We’re between plus 25 kW/m2/a and 30 kW/m2/a in terms of BER score and that’s ignoring the heat recovery from the grey water tank. In total energy terms, including appliances and cooking we estimate that we will still be energy and carbon positive.” Daly has written to SEI to ask whether the BER scale could be extended to include net energy positive buildings, perhaps with the introduction of scores such as A+ and A++ as seen in the white goods market.
Daly researched wind generation, but site conditions were sub optimal. The PV system, also supplied by CareyGlass Solar is divided into two separate arrays of twenty panels each, with a combined peak load of 5kW and a total surface area in excess of 40m2. The house is grid connected to accommodate seasonal variations in supply; this is a zero / positive net energy strategy.
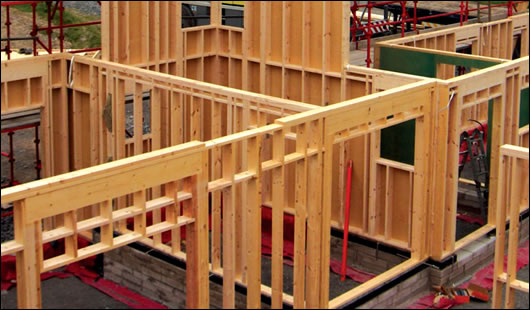
The timber frame system being erected
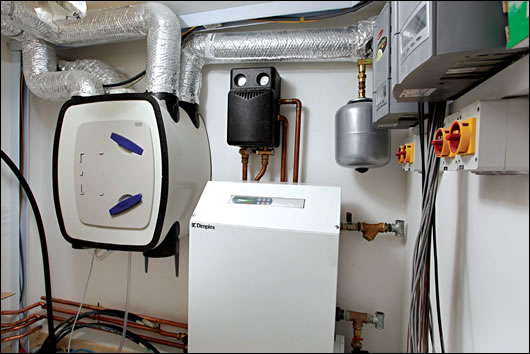
The Xpelair HRV unit and Dimplex heat pump, which draws energy from ground loop collectors
Internally, ecological materials are used wherever possible. Much of the upstairs flooring is Marmoleum from Forbo Ireland. A modern version of traditional linoleum, it’s a biodegradable product made from natural materials. Manufacturing operations are ISO 14001 certified, raw materials (including linseed oil, rosins, wood flour, jute and ecologically responsible pigments) and energy are used efficiently, waste is recycled and emissions are kept to a minimum. The Cucine Lube kitchen from Collier Kitchen Supplies was chosen because Lube uses only certified ecological panels in their cabinets and have a zero waste policy. Cabinet door frames are made of 100 per cent certified recycled wood. All paints used are ultra low VOC.
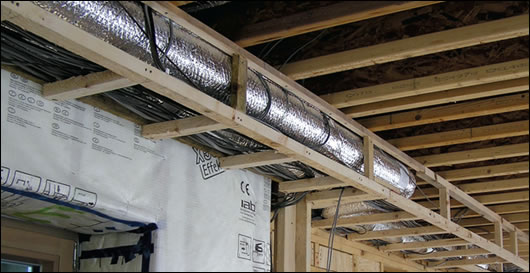
Heat is distributed the HRV ductwork rather than radiators or underfloor
While the house is plumbed for a rainwater harvesting system, installation was not feasible at this time. A well had to be bored to provide drinking water. “I believe if you have a system, use it to the maximum.” says Daly. “We’re going to have rainwater which goes into the ground which will go into the well. That’s where we’ll take it from.” Rainwater is to be collected for garden use, while a comprehensive list of water economy measures – including dual flush toilets and low water-use appliances – have been taken within the house.
Daly doesn’t have a firm handle on costings, but points out that the project was a self-build spread over an eighteen month period, and maintains that the level of sophistication, innovation and indeed experimentation he’s achieved could hardly have happened at cheaper cost. The house was one of the few approved under the SEI’s Low Carbon Homes Programme before it was suspended; that grant aid will go to cover some of the cost of the PV array.
“To get to the zero target, the strategy I’ve taken is to prioritise energy conservation, then energy efficiency, then renewables. Get solar design right, optimise the all-electric heat pump solution and get multiple functions out of the heat pump; therefore have less renewables. This project demonstrates that a building does not have to consume energy, it can be an energy producer; that’s technically feasible. The only reason we have buildings that consume energy is because that’s the way we have designed them.”
Selected project details
Project manager/design/energy consultant: Patrick Daly BESRaC
Structural engineer: Michael Murtagh Consulting
Architectural services: TACa
Interior consultant: The Design Network
Timber frame: Riverview Timber Frame Systems
Soy foam insulation: Econstruction Products
Windows & Doors: Variotec GmbH
Fermacell: Richmond Building Products
Sarking Board: Polycomp Products
Green roof/TPO membrane: Moy Materials
Air-tightness products: Ecological Building Systems
Low carbon cement: Cemex
Aerated concrete blocks: Quinn Group
Perinsul blocks: Encon Insulation Ireland
Heraklith board: Skanda UK Ltd .
Hemp lime render: Hempire Building Materials
Heat pump/MVHR supply: Dimpco
Heat pump/MVHR installer/integrations: Geothermal Solar
Solar thermal/PV panels:CareyGlass Solar
LUBE kitchen: Collier Kitchen Supplies
Marmoleum flooring: Forbo Ireland
- Articles
- sustainable building technologies
- On the plus side
- Skanda
- lowest energy house in ireland
- building energy ratings
- BER
- soy foam
- perinsul
- heraklith
Related items
-
New technology centre to break barriers to construction innovation
-
BERCerts.ie offering ventilation validation
-
Software errors create false NZEB compliance picture
-
BER data indicates national house building growth – except for Dublin
-
Is procurement stifling natural building materials?
-
The Jodrell Bank grand challenge
-
Foam glass a sustainable aggregate alternative — Mike Wye & Associates
-
BER data: sick buildings risk while new build surges
-
G-rated Meath bungalow aims for A rating — without renewables
-
Is building life cycle assessment about to become easy?
-
Dublin boiler house reborn as green building exemplar
-
Going A1-rated & certified passive lifts build costs by 0.1%