- Retrofit
- Posted
Limerick farmhouse reborn
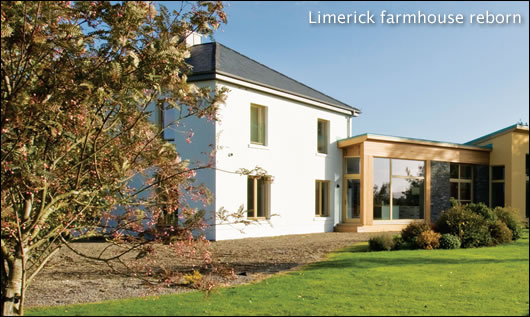
In her latest project in rural Co Limerick, architect Eva Murphyova of Imago Architectural Services has taken a traditional farmhouse, renovated it and added a substantial timber frame extension to create a modern and sustainable take on the traditional farm settlement. Words: John Hearne
Old farm structures in Ireland were always built using local skills and materials. They were often in clusters and orientated for maximum shelter and solar gains. Responding to site and climatic conditions only broke down with the arrival of cheap energy, when it was no longer necessary to use building form and orientation to help heat and protect buildings. At Eva Murphyova’s project in Limerick, the original farm buildings were laid out in a pattern informed by the site and its environment, but a new dwelling house, built twenty five years ago, corrupted the original intent. Old and cold and poorly orientated, Murphyova set about re-engaging the building with its environment, using a highly insulated building envelope together with a blend of sustainable technologies to minimise the building’s energy profile. “I tried to recreate a courtyard,” says Murphyova, “and renovate the house. The client wanted an extensive extension, to connect the extension to the original house and retain the two outbuildings to give us the full courtyard.”
This is a large building. The original house is 200m2, while the timber frame extension doubles that footprint to 400m2. “It’s a working farm,” says Murphyova, “and first of all, the client wanted to keep the character of the farm. He has quite a big family, so you get big gatherings, and we needed to cater for that. And on the other side, he wanted to have a comfortable house, with good air quality and a healthy structure. He wanted it well insulated and well heated at reasonable cost.”
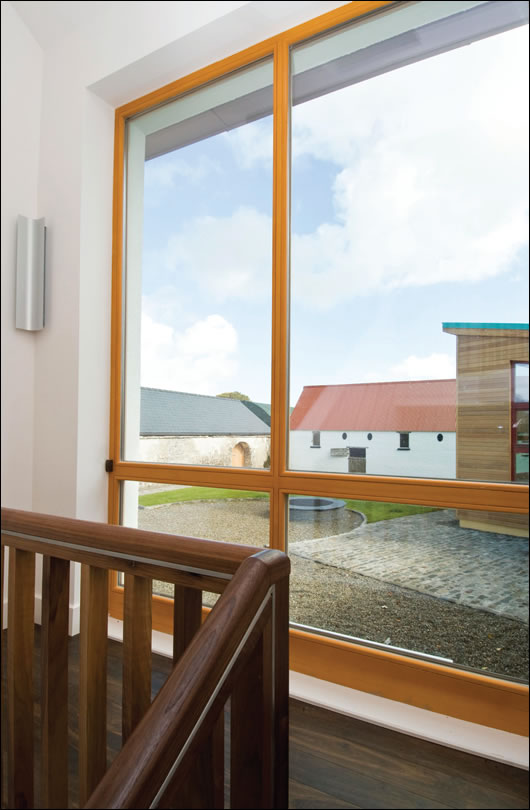
The custom made Czech windows are triple-glazed with an argon fill. Due to their size and weight, the fitting of the windows was one of the biggest challenges of the project
One of the first design challenges was to come up with a layout which would once again address the site’s environmental profile. “Number one was to angle the new part of the house to give it a southerly orientation, and secondly to have it in such a position to enable the existing house to enclose a courtyard,” says Murphyova. The original house with its unfavourable west-east orientation is now divided by an entrance hallway leading from the main front door. Utility and plant-room are housed on the northern side of the building, while the large living/dining areas on the southern side are divided by a partial wall. Murphyova characterizes this space as a bad weather living area; it houses the wood burning stove. In line with the client’s brief, she retained the tall, narrow windows – though replacing the units themselves – in order to keep the character of the house. The new timber frame extension joins the old building here at the dining room. The kitchen in the extension now becomes the centre of the new structure, and the anchor of the court yard. This faces full south and features very substantial glass sections to maximize solar gains.
Murphyova set out to eliminate dead spaces and where possible, to connect spaces and maintain good flow through the entire structure. Internal windows facilitate this. An office and hallway adjoin the kitchen along the courtyard’s southern axis, leading to a large living area, again extensively glazed and providing views of and connection to the extensive mature gardens which surround the house. This living area then flows north into an atrium and atelier, which form the eastern arm of the courtyard. In addition, to the east of this living area, a granny flat and sports/sauna area are divided from the main structure by another partial wall.
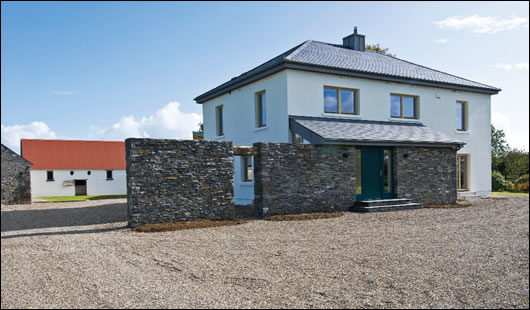
The externally insulated farm building; the extensively glazed timber extension affords views into the courtyard and beyond
Despite its size, there are only three full bedrooms – separate to the granny flat – in the upstairs of the old farm house. “We didn’t increase the number of bedrooms because we didn’t need to. Every space needs to be used, and there is additional sleeping space if needed in the granny flat and in the atelier,” she says. Though Murphyova sought to include smaller windows on northern facades, she had to concede a large window in the atelier in order to make the most of northern light. Bathrooms are also kept to a minimum. “We didn’t want to overload the house with en suites, so we have one big bathroom upstairs and one en suite,” she says.
“The form of the extension is very simple. It has a lean-to roof. Irish planners don’t tend to like low pitched roofs, but this form works very well with a big space. Look at a barn, it uses a very low pitched roof. If the space is big, you u can’t have a big slope or it looks like a cathedral, it looks overpowering.”
The original house was of traditional cavity construction and poorly insulated. Instead of trying to tackle the cavity, Murphyova decided instead to install external insulation. She used Greenspan’s Brillux external thermal insulation composite system (Etics). "It's a tried and tested system that's been around for over 40 years," says Greenspan MD Mike Cregan. "Brillux is one of the leading external insulation companies in Germany and market leader in Germany for the professional painting sector. All their testing facilities are up to Eota standards. Their level of expertise from a prequalification and specification point of view is second to none.”
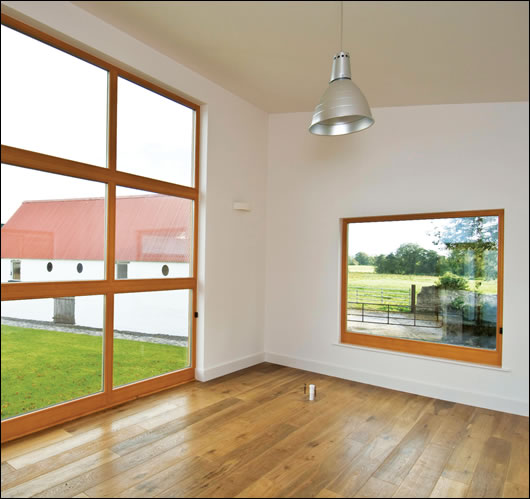
150mm of Aerobord Platinum EPS was both mechanically and adhesively applied to the external leaf by McCauley and Bird of New Ross in Co Wexford. Niall McCauley of the company says that the job was the easiest and most straightforward he has ever done, thanks to the extensive preparatory work carried out by the main contractor, Cumnor Construction. “There are always loads of miscellaneous jobs before you can start,” says McCauley. “You have to take down downpipes, shift gutters and gulleys, strip off around windows. All this was done for us. They had their own plasterers come in and straighten the walls for us…All we had to do was go in and fit the system itself, which happens to be one of the best systems on the market.” The EPS comes in block form and is installed very much like concrete blocks are laid, while cuts for reveals and corners are made using a hot wire system. “Once you have the surface prepared, you’re basically starting at the plinth line level at the bottom. You set up a starting track and work up from that. You start from the corner and you stagger every single block of insulation.” The insulation is then mechanically fixed in place using special Etics steel fixings. A base coat is applied to the insulation, followed by a glass fibre reinforcing mesh to give the system its strength. This is followed by a second base coat, which is then primed and a mineral finish is applied, then finally a coat of silicate paint.
The new windows were moved out and fixed to the outer leaf, while the sills themselves were built from EPS in order to avoid cold bridging. In the roof, the fascias were removed to allow McCauley to build the insulation up to meet the rafters, again to address cold bridging.
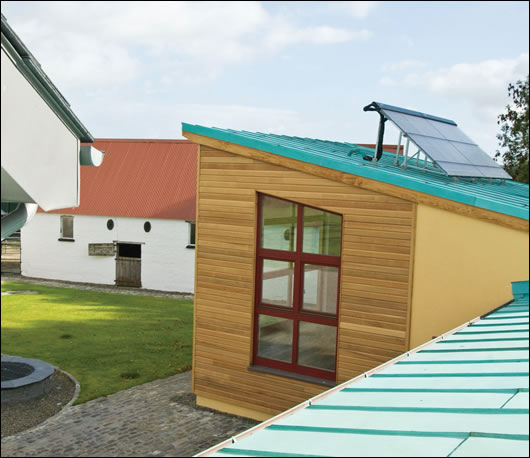
The Thermomax solar array mounted on the extension’s patinated copper roof
BioBased open cell foam was used in both the rafters of the old house and in the studs of the new structure. It was fitted by Foamworks and supplied by Econstruction Products in Dublin. “The main advantage over conventional materials,” says Barry McCarthy of Econstruction, “is that you get airtightness because it’s sealed to the studs.” He explains that fitters are trained up prior to certification, and that all fitters are audited on an annual basis by the BRE to ensure quality installations. “Fitters are continually audited. There’s traceability in the whole process.”
“We basically fill the stud with foam,” says Eugene Gallagher of Foamworks, “and shave the foam back with a specialized wire brush. It’s a semi rigid spray, and it’s breathable so it works with breathable materials. You spray directly against a breathable material or timber, and it allows the timber to breathe and move. It’s like a memory foam in that it moves with the building.” The foam expands to one hundred times its size in thirty seconds, bonding directly to felt and rafters. “Because it expands to such a size,” says Gallagher, “it fills every crack and crevice.”
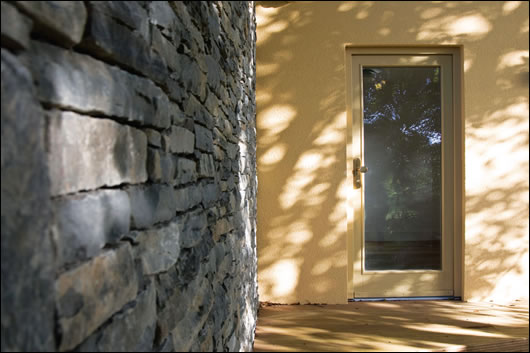
The contrasting finishes of the Aquapanel clad extension and stone outbuilding
The suspended timber floor in the old house u was taken out, and a continuous floor laid through the entire structure. Insulation comes in the form of 110mm of Kooltherm K3 on top of the slab, then the underfloor heating and a 50mm liquid screed.
The timber framed extension was built in situ by Atlantic Timber Frame in Cork. Florence O’Driscoll of Atlantic says the primary difference between his method of construction and conventional prefabricated timber frame construction is his use of plywood instead of OSB board. “We frame the house up before we put any ply on it. If you’re looking at the gable end of a house, that whole gable is one panel. You’re not putting a load of little panels together.” O’Driscoll says that this approach – using full panels rather than jointed panels – adds to the airtightness of the structure. Services are located within the standard 140mm stud and once first fix is complete, the BioBased foam is sprayed into the studs.
Both the walls and roof of the extension incorporate a breathable woodfibre board provided by Econstruction Products and installed on the external side of the plywood. Barry McCarthy of Econstruction explains that it’s used to maintain a breathable wall construction. “The combination of the BioBased foam and the Pavatherm woodfibre board gives you a fully breathable wall construction, plus you’re also getting a pretty good U-value when you bring them together. Because you’re putting the Pavatherm board on the outside of the stud, you eliminate any cold bridging.” Roof build-up is almost identical to wall build-up. In the roof, the woodfibre board – Pavatex Isolair – is thinner at 35mm, and denser. “It’s designed specifically for roof construction,” says McCarthy. “Again you’re eliminating cold bridging, you’re maintaining your airtightness and you’re giving yourself a breathable construction.” While the roof of the old house is slated, Murphyova chose a patinated copper roof for the extension.
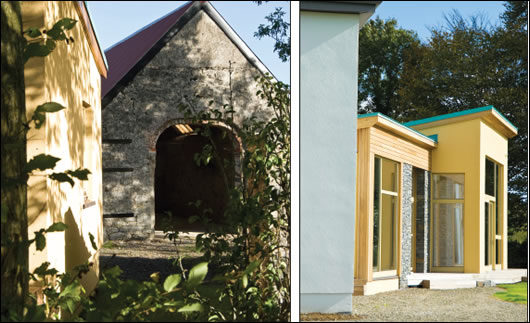
The extension features three separate finishes – cedar cladding, local stone and Aquapanel with the externally insulated house in the foreground
The extension features three separate finishes – cedar cladding from Adanack, local stone and Greenspan’s cement board, Aquapanel, which was also fitted by McCauley and Bird. The Aquapanel is finished in the same way as the Brillux external insulation system, using base coat, mesh, primer and mineral finish.
The windows are custom made by a small company in Murphyova’s native Czech Republic. They use triple-glazed Pilkington Insulight Therm glass with an Argon fill. They give a whole unit U-value of 1.14 W/m2K. John O’Donoghue of main contractors Cumnor Construction says the fitting of these windows – which was carried out by Atlantic Frame – was one of the biggest challenges of the project. “One of the windows in the living room was 24m2. Handling a window of that size was quite complex. They were triple-glazed and there was massive weight in them.” They were fitted during the cold snap earlier in the year, and had to be defrosted in the morning before work could begin. “It was a slow tedious process in that you couldn’t rush anything, because if you were to break any part of them, you’d be waiting months to get them again.”
“We spend as much time adapting the windows for installation as we do installing them. There’s a special technique: we dress our window opes first with paper, we put a polypropylene flange on the windows before we install them, and then we paper and batten the building. It’s a lot like slating a roof. Any water that comes in over the paper is thrown off over the flange of the window. This makes it totally waterproof and airtight.”
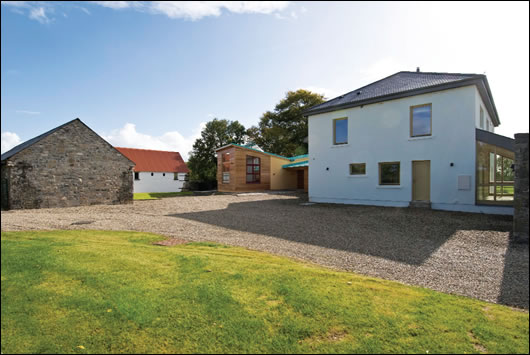
In selecting the right combination of renewable technologies for the house, Murphyova retained EDC – Engineering Design Consultants - in Cork. “I didn’t want to rely on suppliers.” She says. “I wanted someone independent who could give me good advice.”
Mark Nolan of EDC used the Deap software to model the house and provide data to assist in designing the heating and ventilation solution. “The entire house is heated via underfloor heating supplied from a Danfoss DHP-Opti-L 12kW heat pump system & extender solar tank for solar connection supplied by HSB Ltd,” says Nolan. “The heat pump has a COP of 4.75 and claims to save approx 75% of energy consumption. The system has been designed with a vertical collector strategy via two 150m boreholes.” Six square metres of Kingspan Thermomax HP200 evacuated tube solar collectors are installed on the roof. “The collectors provide solar thermal to the cylinder via a closed F&R loop,” says Nolan. “The system is used in conjunction with the heat pump to provide domestic hot water. The hot water services in the house are piped via a hot water secondary return loop which minimises dead legs at the outlet points, which provides instant hot water at each outlet without delay.” The heat pump heats an extender buffer tank and is distributed throughout the house to the underfloor heating manifolds and hot water cylinder. If the temperature in the cylinder is below a set point, the solar panels heat the extender buffer tank with a bypass to the hot water cylinder. Nolan says that incorporating a buffer tank for heating and a cylinder for hot water ensures a cost-effective and more efficient heating system than having a single tank for all systems, as it allows the user more control over each system.
A Jotul F 370 wood burning stove was installed in the living room of the old house. The cylindrical stove features a dedicated air intake through its pedestal and has a maximum output of 7kW. According to Mike Teahan of HSB, who also assisted with the design of the heating system, heat loss calculations showed that a 12kW heat pump would meet the building’s needs. “The building should have a heat loss of circa 30-35W/m2, which brings the peak load down to 12-13kW.” He says. “A standard built house of a similar size would need a peak load of about 20kW. This also led to substantial savings on the equipment – a 20kW would cost more, and would have required more boreholes to be drilled, bigger pipework and more labour. It proves that it makes sense to make a building better designed in terms of orientation, heat loss, energy management – to look at it from a whole building point of view – as the heating equipment costs and running costs are reduced.”
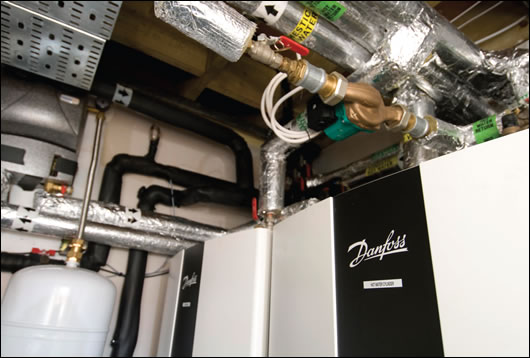
The Danfoss heat pump system
Two mechanical ventilation heat recovery systems were installed. These are Vent Axia HRE 350/B heat recovery units which boast an energy efficiency rating of 95%. “The HRE350 is factory set to 3 speeds – 100, 170 and 300m3/h.” Nolan explains. “A digital controller on the front of the unit can be used to set the speeds to any required performance. In addition, the operating temperature settings can be pre-programmed for automatic operation of the summer bypass, if desired, to just supply fresh, cool outside air.” Murphyova says knowing that the units would be going in from day one made working them into the design that much easier. “I tried to have the whole house open, so I have vaulted ceilings, but in the existing house, we blocked the ridge so the pipes can be run internally and it doesn’t interfere with the insulation.” In addition, recessed ceilings upstairs facilitate clean, straight duct runs. The second unit, which is housed downstairs, is also concealed in a recessed ceiling.
All lights in the house are supplied with energy saving lamps or LED lamps and external lighting is switched via photocells and timers. GU10 LED 3W bulbs, supplied by John O’Shea of Medlock u Electrical in Cork are used wherever possible.
Location: Co Limerick
Building: 400 square metre, two-storey detached home
Build method: Timber frame extension to existing cavity wall building
BER: Not required
Upgraded walls: 150mm Brillux system, platinum EPS U value: 0.18 W/m2K
Upgraded roof: 225mm BioBased Spray Foam/35mm Isolair board: U value: 0.152 W/m2K
Extension wall: 110mm BioBased spray foam/60mm Pavatherm board: U value: 0.18 W/m2K
Extension roof: 225mm Biobased/35mm Isolair board: U value: 0.152 W/m2K
All floors: 110mm Kooltherm K3/50mm liquid screed - U value: 0.15 W/m2K
Heating system: Danfoss DHP-Opti-L 12kW geothermal heat pump with two 150m bore holes & 6m2 Thermomax HP200 vacuum tube array providing domestic hot water and heating into a buffer tank. Additional space heating via a Jotul F 370 wood burning stove
Ventilation: Two Vent Axia HRE 350/B heat recovery units
Selected project details
Architect: Imago Architectural Services
M&E engineers: Engineering Design Consultants
Main contractor: Cumnor Construction
Timber frame: Atlantic Frame
External insulation system and Aquapanel cladding: Greenspan
External insulation installation: McCauley & Bird
EPS external insulation: Aerobord
Spray foam and wood fibre insulation: Econstruction Products
Spray foam installer: Foamworks
Heat pump, solar array & underfloor heating: HSB
Heat recovery ventilation: Vent Axia
- Articles
- retrofit
- Limerick farmhouse reborn
- Sustainable Heat Source
- Aerobord Platinum
- Argon
- timber frame
- Foam
- Breathable Material
Related items
-
Derelict to dream home
-
Ireland’s first 3D printed homes insulated with clay foam
-
Traditional homes retrofit grant pilot launched
-
Dr. Barry Mc Carron appointed MD of KORE Retrofit
-
Bungalow Bills
-
New scheme offers up to €75,000 retrofit loans at low cost
-
Up to 11
-
Phit the bill
-
Mainstreaming retrofit – a massive missed opportunity
-
It's a lovely house to live in now
-
Is it okay to retrofit heat pumps before building fabric?
-
New Licence Plus scheme undermines retrofit standards, experts say