- Retrofit
- Posted
Log House Renovation
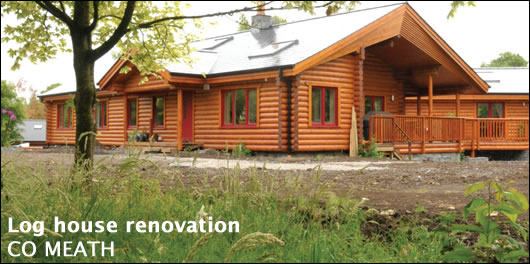
A log bungalow in rural Meath has been extended and given a total energy upgrade – and wood is at the heart of the renovation, with a timber frame extension and external insulation system along with a fresh log finish. Words: Lenny Antonelli
Bungalows built in rural Ireland over the last 20 years were almost always constructed with some form of concrete – finding a timber bungalow built in the early 1990s is rare. Finding one built with a single layer of solid log is even rarer. Originally built from solid Finnish pine log, this 1,300 square foot house near Batterstown, Co Meath was bought by its current owners in 1998. The couple decided to upgrade last year.
Paul Sinnott of Stewart Sinnott Studio Architects – a partner of TV presenter Duncan Stewart – oversaw the renovation. The homeowners had various reasons to upgrade: for a start, driving rain was rotting part of the house's south west corner. Sinnott says that while solid log walls might be fine for the cold Scandinavian climate, they’re perhaps not the best option in rainy Ireland. "Wind driven rain will find its way into the exposed external log corners and ultimately it'll cause a problem," he says.
The homeowners were keen for more space too – they wanted a master bedroom, extra living accommodation and a granny flat with a self-contained kitchen. The ground drops steeply behind the original bungalow, so the obvious option was to put a south-facing extension here to create a split-level house. The extension connects to the main house via a new glazed central link before fanning out towards the drop and wooded view at the back.
Stick-built extension
Timber building specialists JV Ledwith built the timber frame for the extension's upper floor on-site. The build-up of the wall from the inside out includes 12.5mm of Fermacell (a board produced from gypsum, cellulose and water), a 50mm service cavity insulated with Thermohemp insulation, a Pro Clima Intello Plus "intelligent" airtight vapour membrane, a 200mm cavity insulated with Thermohemp, 9mm of Panelvent woodfibre sheathing board, a Pro Clima Solitex breather membrane and a 50mm external ventilated cavity. The U-value of the walls is 0.18 W/m2K.
Ledwiths then clad the extension externally with Finnish red deal timber, which is derived from Scots Pine. “The profile of this board replicated the original round logs,” Sinnott says.
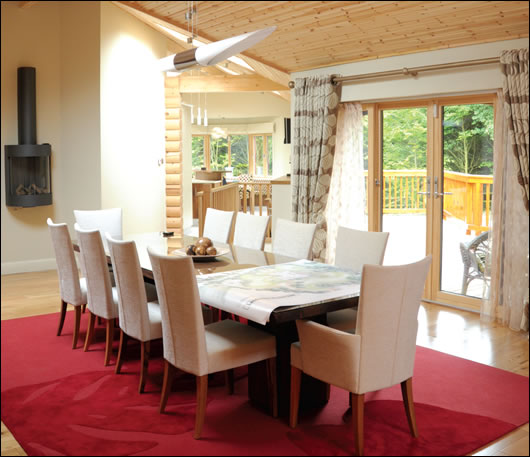
"I feel that timber always looks better when it's contrasted with painted surfaces," says architect Paul Sinnott
The external log corners of the original house were replicated with sections of solid round log secured on a vertical timber frame, which the cladding neatly dressed into. Ledwiths developed this detail working closely with Sinnott to eliminate future problems in this area – if there is any difficulty, they can be simply replaced. All external cladding was finished with a three coat Sikkens water based preservative.
The pitched roof of the extension has a similar build-up to the walls, but with more insulation. From the inside out there's 12mm painted timber sheeting, 50mm of Thermohemp on an Intello Plus membrane, 225mm rafters with 200mm of Thermohemp insulation, 100mm of counter-battening with 100mm Thermohemp insulation, 9mm Panelvent sheeting, a Pro Clima Solitex breather membrane, a 25mm ventilated cavity, and a natural slate finish. The roof's U-value is 0.16 W/m2K.
Ecological materials
Sinnott used products from Ecological Building Systems extensively in the build-up – this included Pro Clima membranes and tapes, Thermohemp insulation and Panelvent external sheathing board. "We tried to utilize their systems because we believe they are well founded technically,” he says.
Pro Clima Intello is an “intelligent” membrane. According to Niall Crosson of Ecological Building Systems, it works as follows: in winter when there’s a greater risk of water vapour diffusing from inside to the outside and condensing as it meets cold building elements, Intello is highly vapour resistant. In summer the direction of vapour pressure may reverse from outside to inside, as the external surface absorbs radiant heat. Any moisture trapped within the structure will then drive inwards towards the membrane. In this case the membrane opens up, allowing any moisture in the wall or roof to u dry back into the building, helping to dry out the building structure. Crosson says Pro Clima offers the “highest performing intelligent membrane and tapes on the market today,” and says Intello can be over 50 times more vapour permeable in summer than winter.
Ecological Building Systems also supplied the Pro Clima Solitex wind tight membrane, which comes in two versions: Solitex WA for walls and Solitex Plus for roofs, which offers extra wind and water tightness. "Solitex Plus uses an intelligent technology similar to Intello," Crosson says. "It's non-microporous and completely air impermeable, but if ever moisture or condensate comes in contact with it, it becomes exceptionally vapour permeable."
The company also supplied the Thermohemp insulation used in walls and roof. Thermohemp is manufactured in Germany and contains 85% hemp – manufacturer Hock uses only the bast – or skin – fibre of the hemp plant, which Crosson says is "the highest quality part of the hemp plant for this purpose". He adds that, according to an independent study commissioned by Hock, each cubic metre of Thermohemp produced sequesters 13kg of carbon.
While Thermohemp is produced in Bavaria, Crosson sees lots of potential to grow hemp for building materials in Ireland. "There's no reason why one day it can't be produced in Ireland," he says. "Research and experience has shown that Ireland is actually one of the most suitable climates for growing hemp."
Concrete box
The lower ground floor of the extension comprises essentially a reinforced, insulated concrete box which retains the adjoining ground. The retaining wall and ground floor of this structure is kept watertight with a Voltex membrane under the floor slab and dresses up at the edges to lap with a bituthene layer. This entire box was wrapped in high density insulation – 150mm Kingspan around the walls and 125mm Xtratherm Thin R Polyiso XT/UF under the floor.
A metal frame stud partition system was erected inside the reinforced concrete walls – set back 25mm from the face of the wall – with 100mm ThermoHemp insulation, and finished with a 12.5mm Fermacell board internally. These walls have a U-value of 0.18 Wm2K.
Where it emerges from the ground, the rest of the lower floor has a cavity wall build-up that includes 100mm of solid concrete block externally (faced with random limestone cladding), a 150mm cavity fully-filled with rigid Aerogyp platinum insulation from Aerobord, and a 215mm plastered hollow block inner leaf.
"The house has a number of constructional systems and build-ups which is unusual but necessitated by the site conditions and by what we were trying to achieve,” Sinnott says.
Bungalow renovation
The homeowners didn't initially plan to renovate the existing bungalow extensively – just fix the problems they had with external log corners and make other minor changes. They felt the original log structure was fairly comfortable, but in the end chose to upgrade on the recommendation of Sinnott, who was keen to make the existing house as energy efficient as possible.
"They ended up doing much more than they originally intended – we replaced the original fibre cement roof finish, replaced an open fire with a cassette based unit, re-insulated and sealed the entire structure and it meant that they were getting a much better job and both the original and new extension tied in perfectly with each other," he says.
Sinnott opted to insulate the old bungalow externally with a timber frame system and clad it with a new pine cladding board with specially designed log corners – the same as those on the extension. The original solid log corners were first cut back and treated, and any defective wood cut out.
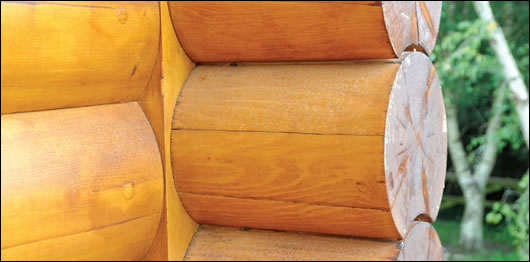
The external log corners of the original house were replicated with sections of solid round log secured on a vertical frame
From the inside out, the build-up here features the existing solid round log, an Intello membrane, 150mm of Thermohemp insulation with studwork, a Solitex breather membrane, a ventilated cavity with vertical battening, and then the pine log cladding. Sinnott estimates these upgraded walls have a U-value of between 0.18 and 0.20 W/m2K.
Sinnott chose to increase the pitch of the existing roof too, which had shown signs of rain infiltration over the years. Ledwiths installed 300mmm of Thermohemp on top of some existing fibreglass here – the roof's U-value is now 0.16 W/m2K.
The roof had originally been clad in bitumen tiles, then later cement fibre slates, both of which suffered because of the roof’s low pitch. The new roof pitch is more appropriate for natural slates, Sinnott says, and will allow rain to run off easier.
The existing timber flooring in the old bungalow was lifted and insulated with 200mm of Holzflex, a woodfibre insulation board supplied by Ecological Building Systems, and laid on a vapour barrier over existing insulation.
Triple-glazing
All original existing windows in the bungalow – double-glazed timber units with a further separate pane inside – were removed, and new NorDan NTech windows were installed throughout the old and new sections. The windows are all triple-glazed with two 12mm argon-filled cavities. "NorDan rarely use krypton," says NorDan's John McMenamy."There are two reasons. One is the cost, and the second is that the embodied energy of krypton is pretty high."
At the time of the project NorDan were only able to supply a U-value for a standard, "reference-sized" NTech Window – in u this case 0.97 W/m2K. But McMenamy says they can now provide exact U-values for every window supplied, allowing for more accurate calculations of a building's overall energy performance. All NorDan's U-values are certified by the Norwegian Building Institute, whose approval McMenamy says SEAI accept for the input of U-values when calculating building energy ratings.
NorDan's windows also feature warm-edged spacers. "This would be a thermoplastic spacer, he says. "As a rule of thumb the warm-edged spacer would lower the U-value of the whole window by around 0.1 W/m2K." He says the biggest difference warm-edged spacers make for householders is the "virtual elimination" of condensation that can occur around the perimeter of windows.
Timber in the windows is PEFC-certified Nordic pine. "NorDan as a company has PEFC [Programme for the Endorsement of Forest Certification] chain of custody certification," he says. "It's not just a case of buying in PEFC or FSC timber. Everything that leaves the factory gate is certified."
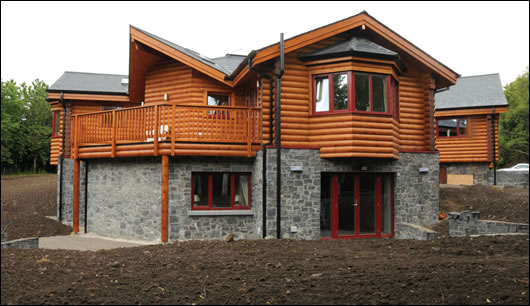
The extension features a timber-frame build-up with log cladding upstairs, while the lower floor here is comprised of reinforced concrete and cavity wall constructions
Airtightness, ventilation & heating
While Ledwiths sealed the whole construction with Pro Clima airtightness tapes and membranes, no blower door test was done. Sinnott explains: “There were no plans initially to substantially upgrade the original house, but as the project progressed the clients decided, bit by bit, to upgrade this area. It was not practical or indeed possible to seal the existing house to the same degree as the new section, particularly in the old suspended floor area, as it would have meant stripping out the floor completely. However, we did everything that we could that was practical and affordable.”
He did consider just testing the extension, but given the old and new sections are connected with a large open link area, it would have been awkward to seal this for testing. "We are satisfied that everything is taped and sealed to a very good standard,” Sinnott says. “Both ourselves and Ledwiths have had prior experience of this type of work and knew what was required.”
He adds: “All the internal vapour barriers were taped and carefully sealed around window and door opes and the reinforced concrete ground floor structure to ensure an airtight building. Equal care was taken at first floor junctions to ensure continuity of insulation and avoidance of cold bridging.”
The extension features heat recovery ventilation (HRV): a Vortice Prometeo HR400 unit here extracts warm, moist air from "wet rooms" such as the kitchen and bathrooms and uses it to pre-heat fresh air that's piped to bedrooms and other living spaces. Supplied and installed by Cedar Sustainable, the system is certified as having an efficiency of up to 92% by SAP Appendix Q, which certifies the efficiencies of HRV systems.
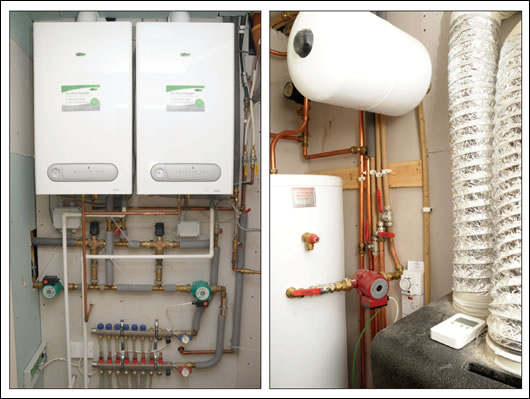
The extension features a heat recovery ventilation system (above right) which pre-heats incoming fresh air in the extension. This supplements the whole house's main heating source, a dual condensing gas boiler system (above left), which distributes heat via underfloor heating in the new section and rads in the old
Cedar Sustainable always install the Prometeo with rigid ductwork. The company's Gary Behan mentions concerns that flexible ducting can inhibit air flow, and says the system's efficiency is only certified by Sap Appendix Q if installed with rigid ducting. The Prometeo comes with a remote control that displays air temperature, relative humidity, and carbon dioxides levels, as well as the unit's speed and time settings.
The HRV system supplements the main heating source, a dual interconnected Vokera Mynute 29EHE condensing gas boiler system, which has a seasonal efficiency of 86.8% according to Sedbuk, the UK's boiler efficiency database. Heat is distributed by thermostatically-controlled underfloor heating upstairs and downstairs in the extension. Some original radiators in the old section were replaced with thermostatically controlled high efficiency Runtal units.
The householders also chose to install a rainwater harvesting system too, supplied by Carlow Precast Tanks. Rainwater is collected on the roof and delivered to the buried 15,900 litre rainwater tank, where it's filtered twice. "You have a standard leaf filter, and then you have your fine filters that are like balls of twine," says Carlow Precast's Chris Cleary.
The filtered water is then pumped to the attic, where a UV filtration system sterilises it to make it suitable for showers, bathing and u brushing teeth – though not for drinking. UV filtration doesn't come as standard, but if it's not added the filtered rainwater is only suitable for washing dishes or gardening.
Seamless integration
With rainwater harvesting in addition to a generous standard of insulation and the use of ecological materials the finished building is clearly quite green. Timber is a key part of the building, but it’s more than just a practical material here – it's at the heart of the design. Though it's common to see ultra-modern extensions beside older homes – the proverbial “glass box” – Sinnott was never tempted to go down that route. "We've designed many additions to various houses over the years, and if we feel the original structure has any merit or integrity, we would generally look to try and tie in the new with the old in a seamless way, rather than go for a more stark contrast,” he says.
“Many contemporary glass additions added onto existing dwellings may look fine when they are first built, but I feel that they can start to date very quickly and within 10 years the house and extension can look very disjointed,” he says. “We try to ensure that the house looks well not just when it’s completed but also hopefully years later and that it will stand the test of time.”
With that guiding philosophy, he chose the same materials externally on the extension as the original house: Finnish red deal cladding for the external walls, and limestone cladding for the lower ground floor walls to tie in with the existing plinth. He specified a new natural roof slate for the whole house too.
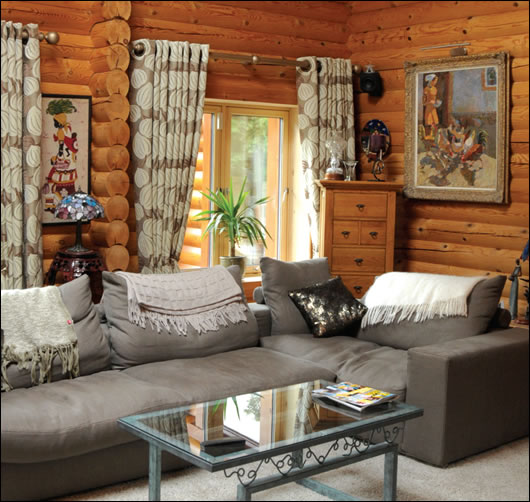
"Every material followed through," he says. “Inside we have introduced some solid log timber detailing at various points to tie in with the original solid log interior walls, however we have restricted the use of timber in the interior of the extension. Inside, I feel that timber always looks better when it’s contrasted with painted surfaces – too much timber can be dark and somewhat overbearing, particularly when you consider that the original structure was entirely timber inside and outside.”
Stewart Sinnott avoided the developer-led speculative office and apartment work that resulted from the building boom – Sinnott says it would have been difficult to remain committed to quality in such a commercially-driven environment. They also refused to expand at the pace some other firms did during this period. "Our interest was is in designing and making buildings that were well thought out and detailed – neither myself nor Duncan were all that interested in managing a big practice,” Sinnott says. "Perhaps it might have been more lucrative to have been involved in more commercial type work but I have never regretted the route we took – we can still make a living and we are doing what we want.”
“We have been very lucky over the years. We’ve had a steady stream of interesting commissions from many high profile private clients. It was low key work, bespoke design work if you like, but very satisfying and very varied,” he continues. “Our designs always featured an emphasis on energy, long before it became standard practice, and we have also tried to develop the use of timber in building in Ireland.”
Selected project details
Architect: Stewart Sinnott Studio Architects
Structural engineering consultant: Tom O’Neill
Main contractor: JV Ledwith
Membranes, tapes & insulation: Ecological Building Systems
Windows: NorDan /Carroll Joinery
Rainwater harvesting: Carlow Precast Tanks
Heat recovery ventilation: Cedar Sustainable
- Articles
- retrofit
- Log House Renovation
- Stick Built Extension
- timber
- Bungalow Renovation
- Voltext Membrane
- Aerogyp
- triple glazing
Related items
-
Derelict to dream home
-
Traditional homes retrofit grant pilot launched
-
Dr. Barry Mc Carron appointed MD of KORE Retrofit
-
Bungalow Bills
-
New scheme offers up to €75,000 retrofit loans at low cost
-
Timber in construction group holds first meeting
-
Phit the bill
-
Mainstreaming retrofit – a massive missed opportunity
-
It's a lovely house to live in now
-
Is it okay to retrofit heat pumps before building fabric?
-
New Licence Plus scheme undermines retrofit standards, experts say
-
Government supported almost 27,200 home energy upgrades through SEAI in 2022