- Retrofit
- Posted
Malahide tennis club
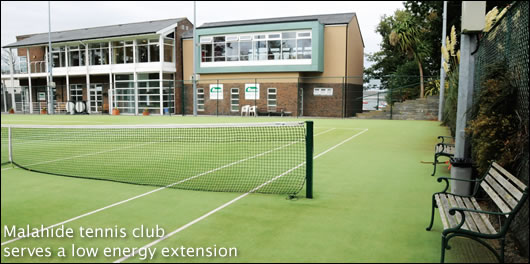
The new extension to Malahide’s tennis club boasts stunning views over the local harbour and the Irish sea through its glazed facade. It also features generous insulation, abundant natural light and a minimalist approach to ventilation — and plans are afoot for an extensive solar thermal array too. Words: Lenny Antonelli
Here’s a challenge: how do you create panoramic views down both sides of a long, narrow building — using extensive glazing — while still making the building energy efficient? Malahide Lawn Tennis and Croquet Club faced this dilemma when it set about extending its clubhouse earlier this year. Though the club was founded at Malahide Castle in 1879, its brick-clad home in the centre of the County Dublin village was built in 1991 – one half was single-storey changing rooms, the other a two-storey structure with a steeply sloping roof that restricted space in the dark first floor bar.
The club considered overhauling the bar a few years ago, but it was too expensive — the collapse of the building industry meant now was a cheaper time to build. The brief to architect O’Dwyer & Associates (ODA) was clear: extend the bar while maximising sea views to the north and maintaining views over the tennis courts to the south, and create a new room for kids over the existing changing rooms, again with extensive views on both sides. So ODA designed connecting glass boxes – one to sit above the single-storey changing rooms and another to add to the existing first floor bar, with a common room in between.
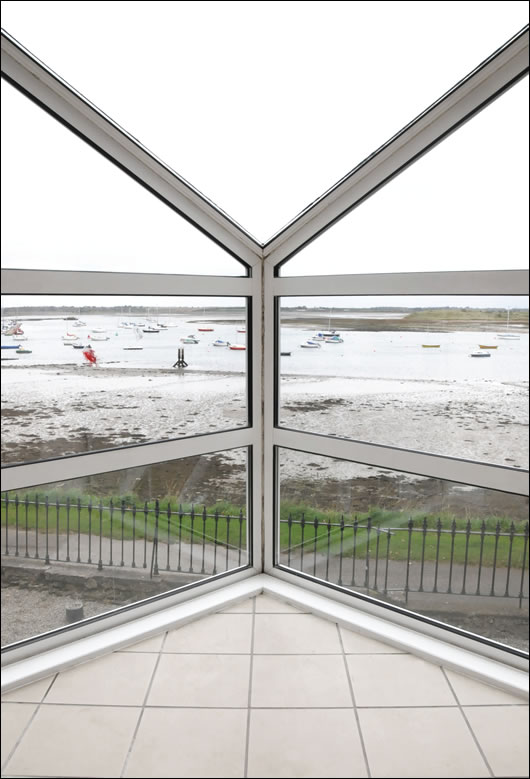
The glazed curtain walling with a centre-pane U value of 1.2 W/m2K provides excellent views over the harbour to the north, and over the tennis courts to the south
From the outside, the new sections add a contemporary look to the clubhouse without jarring with the original building as glass box extensions often do. “It’s kind of contemporary, but it still fits in,” says project architect Nuala Burke of ODA.
The new parts are mostly steel framed, with glazed curtain walling and externally insulated block. Walking by the courts, I ask engineer John Melvin of House Energy Efficiency – who oversaw the energy design – why he went with such extensive glazing considering the potential drawbacks: excessive heat loss in winter, and the risk of overheating and glare in summer. “When you get up there you’ll see why we’ve done the glass,” he assures me.
And he’s right: inside the new spaces, the extensive glazing provides a stunning view over the harbour and Irish Sea to the north, and over the tennis courts to the south. Nuala Burke says that to help foster the social life of the club, it was key to create a space that club members would actually want to use.
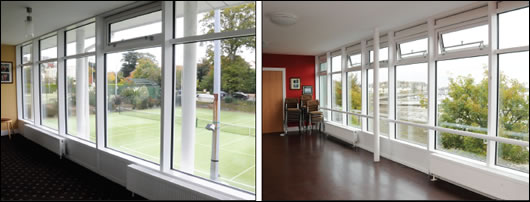
Of course the views come at a price – it’s impossible to maximise energy efficiency with all that glass, as no window can keep heat in better than a well-insulated wall. Melvin – himself a club committee member who co-ordinated the project free of charge – acknowledges the drawbacks. “The reason why this can’t be passive is because of the amount of windows,” he says.
But the building doesn’t need to be as well insulated as a house, mainly because it will rarely be occupied in the middle of the night when temperatures are coldest. House Energy Efficiency specialises in home energy assessment and upgrades. Melvin’s been enthusiastic about energy efficiency longer than most — in the mid 1990s he built a home to the Canadian R2000 standard with Irish timber frame pioneer Gerry McCaughey.
Melvin aimed for non-glazed walls to meet the German passive house standard of 0.15 W/m2K, and he got pretty close. These walls are solid concrete block with 200mm of EPS insulation externally and a 37.5mm insulated plasterboard on the inside – they have a U-value of 0.16 W/m2K. Builders Mallerwood Construction used a Weber EPS external insulation system, with an acrylic finish. The new sections are partially clad in green copper on the outside, matching the tennis courts. “It’s a little bit of tennis in there,” Melvin says.
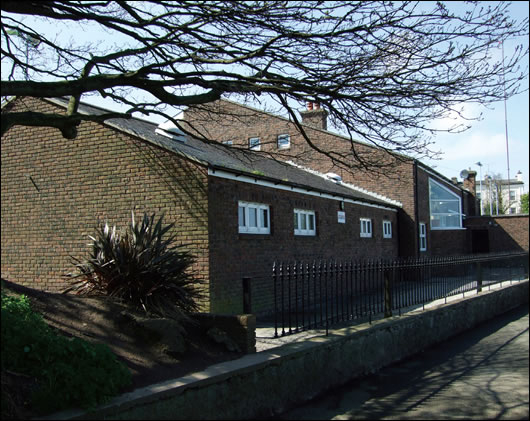
A rear view showing both sections of the building before the upgrade
An insulated plasterboard of 37.5mm was installed under joists in the attic, with150mm of Isover’s Metac glass wool insulation between joists and a further 100mm over this. There’s another 180mm of Metac between the rafters of the pitched roof — essential to prevent the water tanks in the attic from freezing in winter. Cooper Insulation installed the Metac, a glass wool insulation made from a mix of silica sand and up to 80% recycled post-consumer glass. The overall roof U-value is 0.16 W/m2K.
Cooper Insulation also installed a Siga Majpell airtightness membrane under the joists. “We supplied and fitted the Siga airtight system,” says the company’s Kevin Lynch. The company used an extensive array of Siga products — including Corvum tape around windows and doors, Rissan tape for circular holes, and Primur glue. Cooper Insulation also did a provisional airtightness test before finishing to help find any leaky spots they’d missed. The attic space also features sealed Fakro hatches designed for airtightness.
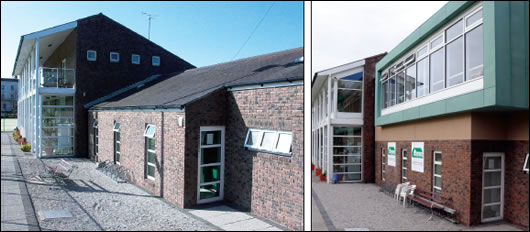
Before and after shots of the front facade, showing the new glazed extension with green copper cladding over the changing rooms
Mark Shirley of energy consultants 2eva.ie was conducting the latest blower door test the day I visited. He was testing two areas separately — the bar and the common room together, then the junior room and the common room together. The week before, both areas had an airtightness of around 5 air changes per hour (ACH). John Melvin had overseen a lot of sealing u since, and was hoping for a better result.
He got it: the common room and junior area together scored 2.42 ACH, while the common room and bar together got 2.84 ACH. “These retested values are approximately half those of the original tests,” Shirley says. They offer clear proof the further sealing work was a success, he adds, and will help ensure the extension’s heat recovery ventilation system works effectively.
Galway-based HRV manufacturer ProAir Systems installed two PA600 units, which each delivers 550 metres cubed of air per hour at full speed. The PA600 has a certified efficiency of up to 90%, according to the independent database Sap Appendix Q.
One PA600 unit serves the junior room, the other the bar area. Each unit will ventilate its respective space at a low level when the clubhouse isn’t busy, and ventilation to the junior room can be manually boosted if it fills up. When the bar is full, staff will be able to flick a switch to increase ventilation there through a damper arrangement that will direct the full power of both units to the bar. But air extraction will still continue in the junior room, and some of the fresh air in the bar will naturally exit into that space too.
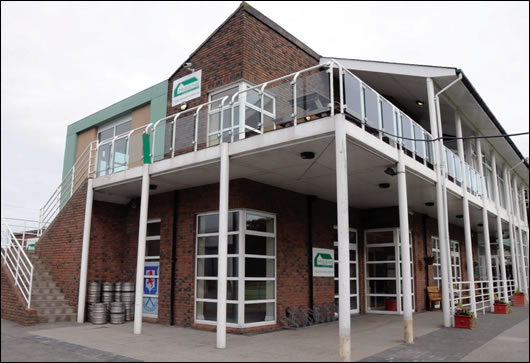
Ppart of the original balcony has been retained, and part has been enclosed inside the new glazed curtain walling
McHugh says ProAir’s strategy was to “achieve maximum benefit from the ventilation system and avoiding heavy HVAC [heating, ventilation & air conditioning] plant with cooling attached, with all the carbon emissions which this type of solution involves.” He says there’s a growing trend in HVAC design to specify minimalist systems, preventing unnecessary energy use. In summer the ProAir units will operate in extract-only mode, with fresh air drawn in through high-level openings on the glazing.
The main curtain walling is double-glazed, and the glass has a U-value of 1.2 W/m2K. The system features an EPDM thermal break gasket between the outer elements and inner framing.
The existing south wall of the bar was knocked, and the curtain-walling used here to enclose most of the original balcony behind glass, bringing it into the interior. The kitchen behind the bar features a triple-glazed Velux roof window, a crucial source of natural light in this enclosed space.
With so much glass there’s clearly potential for overheating and glare on the south facade. But the well-insulated envelope and openable windows will help to prevent overheating. And an existing overhang on the south facade of the bar provides shade there. “Glare could potentially make it difficult to watch people playing tennis,” John Melvin acknowledges. He’s going to wait to gauge the views of club members before deciding whether to put a brise soleil on the south facade of the junior room, and whether to put an anti-glare film on the glass.
A new 100kW high efficiency condensing gas boiler – supplied and installed by Heat-tec – now heats the entire building, with Quinn Compact radiators throughout. The clubhouse is divided into four heating zones: the original section downstairs, the junior room, the bar and hot water. Each radiator has a TRV, and there are two central controls for programming temperature and timing in the different zones.
A pre-existing 600 litre tank currently stores hot water, but Melvin plans to install two new 1,000 litre pre-insulated tanks along with a 20 square metre solar thermal array. The extensive solar array and storage will help meet the clubhouse’s heavy demand for hot water.
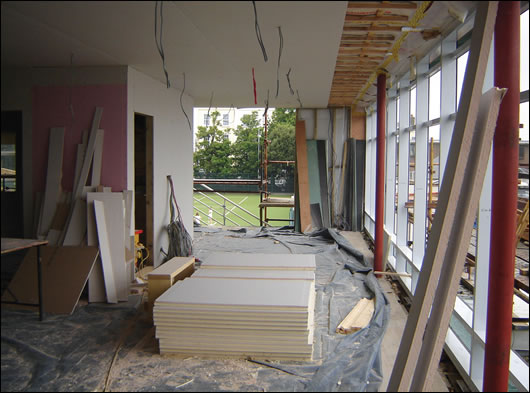
The curtain walling going up, and the ceiling showing insulated plasterboard, battening, and Siga Majpell membrane
When I visited the site in mid-October, it was a hive of activity: decoration was starting, NTL and CCTV installers were both on site, the airtightness test was underway and some scaffolding was still up. The whole entrance road u was blocked with vans, and an important delivery was on the way. “They’re supposed to be testing [the bar] tonight.” Melvin told me. “The Heineken is in but Guinness is supposed to be coming today.”
Transforming the bar space was also part of the architects’ brief — while the glazed facades create a bright and airy space, putting the bar itself at the centre of the room was also key. It divides the room visually, giving it a more intimate scale and avoiding the creation of a large, empty space. It keeps the views free from obstruction too.
For Mallerwood Construction’s Donagh Higgins, the building held personal interest. “I had always admired the Tennis Club Building and facilities at Malahide,” he says. “I don’t think I have ever driven past it without taking a glance at it and admiring its design and appearance.”
The job was a chance for Mallerwood to boost their knowledge of energy efficiency in buildings. “With the way the industry is going everything is changing towards more energy efficient buildings,” Higgins says. “It was a good learning curve for us.”
A huge white curtain was draped over the external face of the junior room when I visited – it was set to be lifted at the grand opening on the following Saturday, just three days later. Work started early in June and there was just 19 weeks to finish the job, with the whole clubhouse taken over for the summer. “Yes we could survive a summer out in the open…but once the winter comes you can’t really do that,” Melvin says.
As I left the the club, Melvin’s mind was firmly fixed on one thing. “All I can think of is as far as Saturday,” he says. I suggested after that, he might finally be able to have a rest after five months managing the project. “Well yeah,” he adds. “I can have a proper game of tennis Sunday morning.”
Project overview
Location: Malahide, Co Dublin
Cost: €450,000
Building: 150 square metre extension to tennis clubhouse
Build method: Steel frame, externally insulated block & glazed curtain walling
BER: Not yet available
Carbon dioxide emissions rating: Not yet available
Airtightness: 2.42 & 2.84 air changes per hour
Walls: Solid concrete block with 200mm EPS insulation externally and 37.5mm insulated plasterboard internally. U-value: 0.16 W/m2K
Roof: From the bottom up: 37.5mm insulated plasterboard, battening, Siga Majpell airtightness membrane, 150mm Metac insulation between the joists, 100mm Metac over the joists, with a further 180mm Metac between the rafters. U-value: 0.16 W/m2K
Curtain walling: Double-glazed curtain walling system with argon fill. U-value: 1.4 W/m2K
Ventilation: 2 x ProAir PA600 heat recovery ventilation units, efficiency of up to 90%
Heating: 94% efficient 100kW Wolf condensing gas boiler. 20 square metre solar thermal array to be installed for hot water
Selected project details
Client: Malahide Lawn Tennis & Croquet Club
Energy design: House Energy Efficiency
Architect: O’Dwyer & Associates
Contractor: Mallerwood Construction Limited
Heating system: Heat-tec
Heat recovery ventilation: ProAir
Glazing: Eden Aluminium
Isover Metac insulation & Siga airtight system: Cooper Insulation
External insulation system: Weber
External insulation supplier: Facade System
- Articles
- Design Approaches
- Malahide tennis club
- External Insulation
- Natural Light
- Ventilation
- retrofit
- blower door test
- Acrylic Render
- heat recovery ventilation
Related items
-
Derelict to dream home
-
Lung disease patient: Zehnder MVHR “the best thing I’ve ever had”
-
Why airtightness, moisture and ventilation matter for passive house
-
ProAir MVHR unit achieves up to 95% efficiency
-
Traditional homes retrofit grant pilot launched
-
Dr. Barry Mc Carron appointed MD of KORE Retrofit
-
Bungalow Bills
-
New scheme offers up to €75,000 retrofit loans at low cost
-
Zehnder launches MVHR system for tight spaces
-
Phit the bill
-
Mainstreaming retrofit – a massive missed opportunity
-
It's a lovely house to live in now