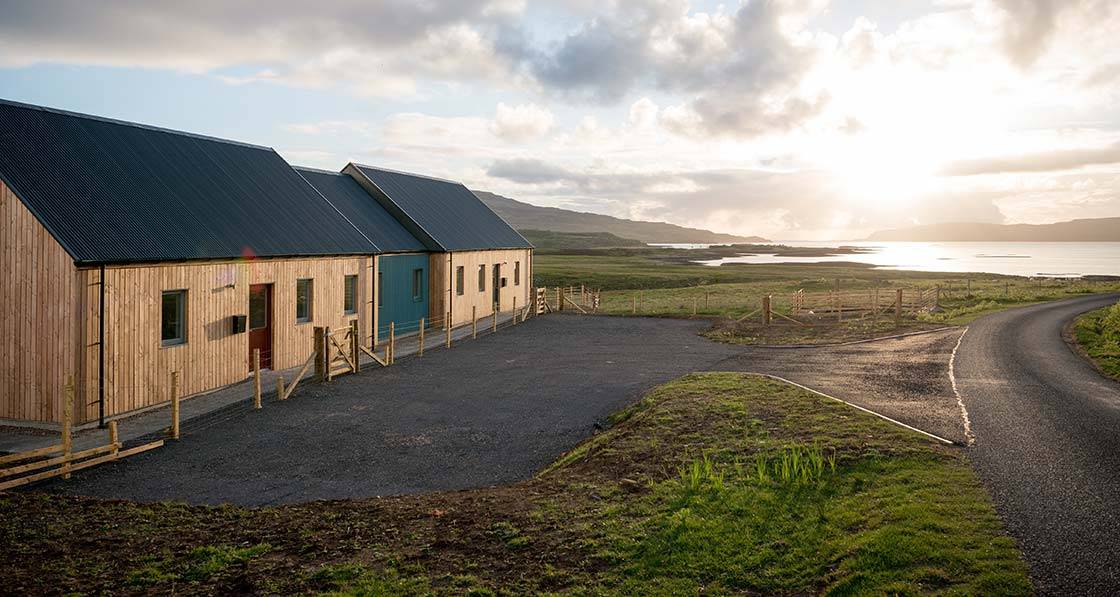
- New build
- Posted
Scottish isle eco cottages need no central heating
Two spectacular low energy social housing units looking out over Ulva Ferry’s breath-taking surroundings prove to be a superb response to local problems of fuel poverty and lack of affordable family housing.
Click here for project specs and suppliers
Building type: Two 89 sqm affordable timber frame cottages
Completed: June 2017
Location: Isle of Mull, Scotland
Budget: £417,000
EPC: B83
Standard: AECB Silver Standard
£20
monthly heating estimate
Located by the sea in a designated national scenic area on Mull, the community-led social housing project at Ulva Ferry consists of two semi-detached three-bedroom houses. Wrapped in larch cladding and sheets of corrugated steel, they are very much in line with the local aesthetic — and house bright, airy, open-plan spaces.
The project came about when Ulva School was threatened with closure, due to local population decline brought about by the area’s lack of affordable housing. This prompted the Ulva School Community Association to kick-start the affordable housing project, supported by the Mull and Iona Community Trust (MICT).
“Right from the outset, community members wanted energy efficient houses, because there’s a real problem with fuel poverty locally,” says Helen MacDonald, MICT’s local development officer. “There’s a lot of people living in very old, very poorly insulated houses, so they’re spending a lot of money on heating…I’ve heard of people spending £80-£100 a week.”
She explains that the emphasis of the project was on achieving an affordable and energy efficient building, and not necessarily on reaching a particular energy accreditation. However, as the chosen architecture firm Thorne Wyness has significant expertise in passive house design, it made sense to use the standard as a guide.
Architect Jenny Wyness chose cross-laminated timber – a smart engineered timber product which turns dimensional lumber into strong, rigid, dimensionally stable structural timber panels – for the building’s structure, alongside sustainably-sourced Scottish larch for the cladding, and corrugated galvanised steel roof sheeting, which is “a cheap, traditional roofing material in the area.”
The design makes a feature of this stripped-back but beautifully detailed palette of materials. There’s heat recovery ventilation and solar thermal collectors too, while space heating is primarily provided by Dimplex 1kW electric heaters in the main living spaces — there was no need for conventional central heating in these small, highly energy efficient homes.
Pipe runs were further reduced by closely grouping wet services, reducing heat loss. The houses are situated on quite an exposed site, which caused the team some challenges during construction. “We had concerns about manoeuvring the roofing panels into place in such a windy location. The wind also led to problems with handling and fixing the Kingspan insulation,” Wyness says. “We also had problems when applying the Extoseal tape, because of the cold weather.”
This article was originally published in issue 23 of Passive House Plus magazine. Want immediate access to all back issues and exclusive extra content? Click here to subscribe for as little as €10, or click here to receive the next issue free of charge
Despite this, the building achieved an airtightness of 0.39 air changes per hour, well within the passive house standard of 0.6. But the project fell short of reaching the standard in other areas. “In general, we found passive house accreditation hard for a single-storey building,” says Wyness — this is because single-storey buildings have a greater surfaceto- volume ratio from which heat can escape, making it harder to reach the standard.
She believes the project’s tight budget also had a significant impact, explaining: “If we had upped our wall insulation by another 40mm, we may have reached passive house classification... But the budget wouldn’t allow it and we couldn’t justify it.” However, the two homes were certified to the less onerous AECB Silver Standard, which is based on passive house principles of fabricfirst design and high quality ventilation, and is designed using the Passive House Planning Package software. The homes also happen to meet the Passive House Institute’s standard for buildings which, for one reason or another, can’t quite make passive: the PHI low energy building standard.
-
Wire mesh in place to reinforce the concrete structural slab, below this is a DPM and 250mm Filcor 45 under-slab insulation Wire mesh in place to reinforce the concrete structural slab, below this is a DPM and 250mm Filcor 45 under-slab insulation
-
The houses were built with cross laminated timber panels which provide strength, reduced construction time, and can help in minimising thermal bridges The houses were built with cross laminated timber panels which provide strength, reduced construction time, and can help in minimising thermal bridges
-
Windows are Rationel triple glazed units with Extoseal Encors tape for sealing to the CLT panels Windows are Rationel triple glazed units with Extoseal Encors tape for sealing to the CLT panels
https://passivehouseplus.co.uk/magazine/new-build/scottish-isle-eco-cottages-need-no-central-heating#sigProIdab323c6c80
Since June 2017, the units have been home to two families with six children between them. And accreditations notwithstanding, it is clear that these two new homes at Ulva Ferry are warm, comfortable and extremely energy efficient — quite a world away from the draughty and poorly insulated Victorian- era farmhouses and cottages that some local families are used to inhabiting.
“The families are absolutely delighted with their new homes and have commented on how warm and comfortable the houses are,” says Helen MacDonald. “Having been in private rental housing beforehand, they couldn’t believe how low the heating costs would be.” The only minor issue experienced so far has been some summer overheating. “One of the families sleeps with the windows open at night, and have been opening windows in the evening due to a build-up of heat,” says Jenny Wyness.
We’re delighted with the project,” Helen MacDonald summarises. “The houses are beautiful, I think they sit really nicely in their setting. And they’re working well, we’ve had no problems since the occupants moved in.” All in all, the social housing in Ulva Ferry certainly proves that beauty, energy efficiency and affordability can all be achieved in unison, even in a landscape as harsh as Mull’s.
Selected project details
Clients: Mull and Iona Community Trust
Architect: Thorne Wyness Architects
Civil & structural engineer: David Narro Associates
Main contractor: Norman MacDonald Builders
Quantity surveyors: Allied Surveyors Scotland
Mechanical & electrical contractor: Ferguson Energy
Airtightness testing: Air Testing Scotland
Passive house consultant: Jenny Wyness
Energy rating assessment: Warm
Timber frame: Egoin
Wall insulation: Kingspan Insulation UK
Party wall insulation: Rockwool
Insulated foundation system: Cordek
Windows & doors: Rationel, via Architectural Doors & Windows Ltd
Airtightness products & Gutex insulation: Ecological Building Systems
Solar evacuated tubes & buffer tank: STI
Heat recovery ventilation: Paul Heat Recovery Scotland
Cladding: Russwood
Corrugated cladding: Accord Steel Cladding
Finance: Triodos
In detail
Building type: Two 89 sqm semi-detached cross-laminated timber houses.
Location: Ulva Ferry, Isle of Mull
Passive house certification: Meets PHI low energy building standard, but not certified.
Space heating demand (PHPP): 17.51 kWh/m2/yr (including storage area in roof)
Heat load (PHPP): 11.06 W/m2
Primary energy demand (PHPP): 111kWh/m2/yr
Heat loss form factor (PHPP): 4.38
Overheating (PHPP): 0%
Additional standards: AECB Silver Standard certified.
Airtightness (at 50 Pascals): 0.39 ACH or 0.378m3/m2/hr
Energy performance certificate (EPC): B83 (Scotland)
Measured energy consumption: 1,855 & 2,347 kWh for first 3.5 months of occupation (June to Sept 2017).
Thermal bridging: Cross-laminated timber construction entirely wrapped in Kingspan / Filcor resulted in the following Y-values (W/ mK): External corner -0.033, Eaves -0.017, Foundation -0.198, Gable -0.038, Party wall 0.010, Ridge -0.026
Energy bills: Estimated in SAP at £496 per year / £41 per month (for heating, lighting, hot water, ventilation but not appliances) & with PHPP at £240 per year / £20 per month for space heating only (based on electricity price of 15.4p per kWh, inc VAT but not standing charges).
Ground floor: 150mm Type 1 hardcore sub-base with 50mm sand blinding, followed above by DPM and 250mm Filcor 45 under-slab insulation. 200mm concrete structural slab, 22mm particle board on baby joists as floor finish. 18mm ply to wet rooms. U-value: 0.135 W/m2K
WALLS
Timber cladding: 27mm natural Russwood Scotlarch board-on-board timber cladding, on 25x50mm horizontal battens on 25x50mm vertical battens on build up as below.
Metal cladding: 3” sinusoidal cladding 0.7mm thick PVC Plastisol coated galvanised steel on 25x75mm vertical battens at 600mm centres with 50x50mm horizontal battens fixed at 600mm centres, with Timco 300INW 8 x 300 wafer head screw on build-up as below.
Build-up: Solitex Front Humida breather membrane, followed inside by 120mm Kingspan Kooltherm K12 rigid insulation, on Intello Plus airtightness membrane / vapour check, on 78mm cross-laminated timber panel. U-value: 0.149 W/m2K
Roof: Traditional 3” corrugated cladding consisting of 0.7mm thick PVC Plastisol coated galvanised steel externally, with 25x75mm vertical battens at 600mm centres with 50x50mm horizontal battens fixed at 600mm centres, with Timco 300INW 8 x 300 wafer head screw on 180mm Kingspan Kooltherm K7 rigid insulation, on Intello Plus airtightness membrane and vapour check, on 120mm cross-laminated timber panel forming main roof structure or 78mm cross-laminated timber panel kitchen roof structure. U-value: 0.10 W/m2K
Windows, external doors & patio doors: Rationel triple glazed Aura windows, 4mm-20mm-4mm-20mm-4mm with argon fill, resting on 87x50mm timber buttress with Extoseal Encors tape to seal window sill and frame to CLT panel. Typical U-values: 0.82 W/ m2K (windows) & 0.87 W/m2K (glazed doors).
Heating system: STI flat plate solar thermal collectors with Worldheat Superflow cylinder. Dimplex Q-rad 1kw heater in main space and Ecostrad TR 700W heated electric towel rail to bathrooms.
Ventilation: Zehnder CAQ 350 installed by Paul Heat Recovery Scotland with ComfoPipe Plus distribution systems. Summer bypass on systems. PHI certified heat recovery rate of 90%.
Water: Restricted waterflow showerheads. 200L water butts in gardens. Private water supply from bore hole and septic tank with infiltration bed.
Green materials: Russwood Scotlarch FSC-certified cladding sourced from sustainable forests in Scotland. FSC-certified cross-laminated timber structure by Egoin, timber sourced at factory forest.
Image gallery
https://passivehouseplus.co.uk/magazine/new-build/scottish-isle-eco-cottages-need-no-central-heating#sigProId16926b4e58