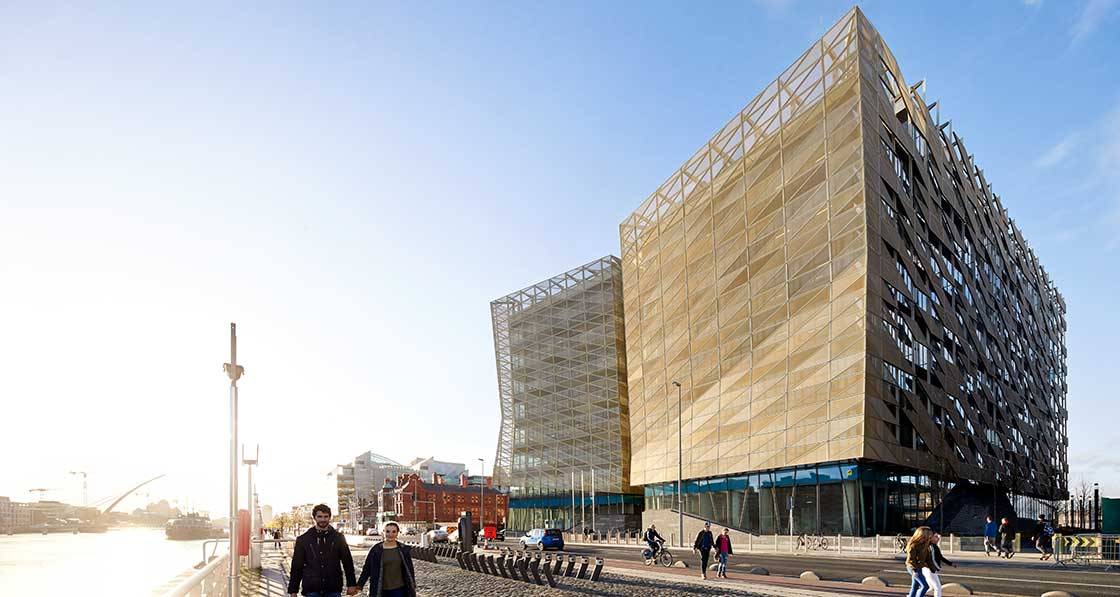
- New build
- Posted
Ireland's new central bank hits nZEB & BREEAM outstanding eco rating
Rising from the shell of the stalled riverside headquarters of Anglo Irish Bank, Ireland’s financial regulator could be accused of insensitivity for choosing as its new home a site that became a toxic symbol of the banking crisis, but the building is not without virtue: it comfortably surpasses the proposed nearly zero energy building standard while achieving the onerous Breeam ‘Outstanding’ rating for sustainability.
Click here for project specs and suppliers
Building type: 37,000 sqm public office building
Location: North Quay, Dublin
Method: Glass skin & aluminium mesh panels on pre-existing concrete frame
Budget: €140m
Standard: Breeam Outstanding
After having stood as a bare skeleton for seven years, the eight-storey concrete structure on Dublin’s North Quay initially meant for the now-collapsed Anglo Irish Bank has been transformed from the downcast symbol of Ireland’s recession into the country’s first office building to achieve the highest Breeam sustainability rating, Breeam Outstanding.
Liam McMunn, the organisation’s environmental, health & safety manager, explains how the project came about: “One challenge we faced was that when working out of multiple buildings, we found we were operating in silos, with departments not getting to talk to each other as often as they may like. So from an operational perspective we needed to enhance collaboration, and we needed to decant into a single campus.”
It was no easy task finding an office building big enough for 1,450 employees, and completing the concrete skeleton of a building at North Quay was deemed the best option.
The brief had several key drivers: accessibility, creating a healthy and productive work environment, encouraging collaboration, and achieving ambitious energy and sustainability goals. According to Liam McMunn: “We needed to create an optimum working model for an organisation that has heretofore found itself operating in isolation at times… It was also very important that we created a future-proof building because we know that what’s the sustainability target in 2015 is going to be different in 2020.”
When you compare this new building with the Central Bank’s former headquarters, Sam Stephenson’s imposing brutalist tower on Dame Street, it’s evident that the organisation has made significant efforts to modernise.
Flexible, intuitive workspaces
“We were moving from a lot of people having offices and the very hierarchical approach that many public sector organisations inherit to a much more open plan and accessible workstyle,” says McMunn.
A laptop can consume up to 80% less electricity than a desktop computer, a notinsignificant energy reduction given there are 1,450 staff in the building.
The building was designed very much with its end users in mind — a variety of flexible, intuitive collaboration spaces with different spatial arrangements and furniture types clustered around the building’s central atrium, with offices and meeting rooms in the middle of the floorplates and the main desk areas placed alongside the facade, to take advantage of natural daylighting.
There was also a strong focus on inclusive design, and the building’s accessibility features enhance the user experience of all staff. “If you create good clear circulation routes, that’s good for everybody, not just for the people who have specific needs,” he explains.
The new office is also a lot more inviting to the public — the ground floor is open to the public, and includes an exhibition space and three flexible rooms that can host large events.
The building has a highly-modern technology setup too. Laptops have replaced desktop computers, and employees can answer their phone from their laptop, or print a document and collect it from any printer in the building, or display slides on a meeting room screen in two clicks.
A laptop can also consume up to 80% less electricity than a desktop computer, a significant energy reduction given there are 1,450 staff in the building. Energy use was reduced in other small ways too, like with sit-stand desks that only have a manual crank to raise or lower them, not a motor. The building’s intelligent lift system also saves energy.
There are no traditional controls in the lifts themselves, but rather users select their destination floor on controls outside the lifts, and the system works out the most efficient lift to bring to the user.
The facade
The building’s outer skin, meanwhile, consists of a glass facade wrapped with a layer of anodized aluminium triangular mesh panels. The density and coverage of the mesh varies depending on its orientation; as well as maximising daylight, it minimises glare and passive solar heat gains, thus reducing the energy needed for cooling.
A unitised system of prefabricated panels was chosen for the glass skin, and facade interfacing was minimised. The team went a step further and brought a full-scale two-storey facade mock-up to a UK testing facility.
This article was originally published in issue 24 of Passive House Plus magazine. Want immediate access to all back issues and exclusive extra content? Click here to subscribe for as little as €10, or click here to receive the next issue free of charge
They carried out rigorous wind, temperature- change, thermal-bridging, water- and airtightness tests on it, even putting a jet engine in front of it.
Pat Kirwan describes it as “over 30 years of age testing over a 24-hour period.” Numerous on-site inspections were then carried out during construction. All these measures resulted in the facade achieving an air permeability of 3.7m3/hr.m2 – not a bad airtightness level for a building with so much glass.
What’s interesting is that the U-value of the overall facade isn’t particularly stellar at 1.3 W/m2K. “It was almost like a cost-optimal exercise — to bump up the facade’s thermal performance you could be getting into triple glazing, really chunky frames, and how does that impact on the cost, versus getting, say, a more efficient chiller,” Pat Kirwan explains.
“Yet we were able to get a very good energy rating even though we didn’t bump up the facade’s U-values; what we did was work that hand-in-hand with the overall energy management of the system — the mechanical systems, the electrical systems and how that all fed back.”
'Highly intelligent' heating, cooling and ventilation
The building’s outer skin, meanwhile, consists of a glass facade wrapped with a layer of anodized aluminium triangular mesh panels.
The complex heating, cooling and ventilation systems are monitored and controlled via a highly intelligent building management system (BMS).
A gas-fired combined heat and power unit provides all of the building’s space heating and hot water during the summer season, supplemented by a series of 105%-efficient gas condensing boilers during the peak demand of winter season. For space heating, hot water is fed through fan coil units, and air that is initially pre-heated via a rotary heat exchanger on the building’s air extract unit is then is passed over the coils to warm it further.
A chiller on the building’s roof provides mechanical cooling, availing of ‘free cooling’ when possible. “When the external temperature falls below a certain point, it’s naturally cooling down the liquid in the chiller’s coils, without any energy being used to run its compressor,” Pat Kirwan explains.
The coils then cool incoming fresh air that passes over them. However, when external conditions fall outside those required for free cooling, the chiller’s mechanical refrigeration element kicks in. Coincidentally, the building’s cooling loads are also reduced by the fact that the staff use laptops instead of desktop computers — laptops give off less heat, which means less heat gains to negate.
Interestingly, the original Anglo Irish Bank HQ design was for a chilled beam strategy supplemented by boreholes with geothermal collectors that could be connected to a heat pump. But the skeleton’s existing boreholes weren’t integrated into the new head office’s heating and cooling systems. According to Kirwan, by the time the Central Bank had bought the skeleton, fan coil technology had improved significantly and energy modelling revealed that it would be more cost-efficient to use fan coil units instead of trying to integrate the boreholes. There is also provision in the building to connect to the future line from the docklands district heating network, which will be powered by the incinerator at Poolbeg.
However, in low energy buildings such as this, it is important to focus not just on energy efficiency and airtightness, but also on an effective ventilation strategy, which is crucial for good indoor air quality. The building has a mixed-mode ventilation system which was tested via extensive energy modelling in BIM. When external conditions are favourable, the building management system opens the louvres in the building’s facade system to let in fresh air.
This cooler air is pulled through the floorplate and into the atrium via the stack effect, supplemented when necessary by a series of mechanical fans at the top of the atrium. The indoor air quality is also improved by the stringent selection of materials with a low volatile organic compound (VOC) content for the interior fit out.
The indoor air quality is tracked by CO2 monitors throughout the building linked to the BMS, which is programmed to alert when CO2 levels reach 900 parts per million, and the supply of fresh air into the building is then increased to counter this.
The building also allows its occupants some local control; if someone sitting near an open ventilator feels cold, he or she can press a button to shut it down, and the ventilator will automatically open again after a programmed amount of time. There’s also a temperature controller in each meeting room that controls the volume of incoming cool air, but the temperature range has intentionally been kept very narrow.
Ingeniously, to avoid the ventilator being left on after the meeting ends, a PIR motion sensor was placed on each ventilator, so that after the meeting room is unoccupied for a programmed period of time, the PIR will shut down the ventilator.
Similar local control features can be seen in the building’s LED lighting system. The lights in open plan office areas are fitted with photocells, and when natural light levels fall below a programmed LUX level, the photocell switches on the light. Staff can manually turn on separate task lights, which are fitted with a PIR motion detector that turns off the light after a given time of inactivity.
Every piece of timber that came on site had to be Forest Stewardship Council certified and accompanied by a full chain of custody certs. The project also benefited from the fact that the structure inherited from Anglo contains Ecocem (GGBS) - 50% in the superstructure and 66-80% in the foundations. However, Pat Kirwan explains that this couldn’t be included in the Breeam calculation, as the standard used “doesn’t consider the existing structural frame.”
1-3 Progress shots showing installation of a new façade, consisting of glass skin shielded by an outer layer of anodized aluminium triangular mesh panels, on the concrete from the stalled Anglo Irish Bank HQ, on Dublin’s North Quay.
Moreover, while Breeam awards points for use of building materials with environmental product declarations (EPDs), which include a figure for a given product’s embodied carbon, among a long list of other parameters – Breeam doesn’t use the data to attempt to quantify, say, the embodied CO2 emissions of the building. Given the building’s substantial concrete structure is heavy on the GGBS – a recycled material that can reduce embodied CO2 emissions of cement by up to 90% - a feature that is likely to be one of the building’s strongest quantifiable environmental benefits remains unknown.
The bank also encourages sustainable modes of transport - onsite car parking is minimised, and over 300 bike stands are provided, as well as shower facilities and lockers for runners and cyclists.
Real-world performance
The building’s primary energy demand is calculated to be 90kWh/m2/yr, 72% less than the original C2-rated Anglo design. But this doesn’t necessarily mean that this was its performance since the building opened in March 2017, as there is always a bedding-in period with such complex buildings and also, importantly, there can be a performance gap between the expected and actual energy use. In large and complicated non-domestic buildings, the performance gap can be enormous.
Passive House Plus was unable to establish the extent and frequency of any temperature or indoor air quality fluctuations within the building, or how quickly the building responds to spikes in CO2 levels in given areas to maintain indoor air quality.
It is noticeably a little warmer on the top floor of the atrium, due to the atrium’s glazed roof and the building’s stack effect ventilation strategy that encourages warm air to rise to the top of the atrium. But the building appears to have relatively good indoor air quality. Data presented on CO2 levels recorded at 4.30pm one weekday in November – at the time information was being first collated for this article - indicated that an average level of 810ppm was being maintained across all its occupied floors.
The building does seem to be performing well according to its staff. One staff member is “very satisfied with our new premises” while another praises its accessibility, stating: “the building’s accessibility features seamlessly integrate with the common infrastructure.. [which] enables me to independently access all of the building’s functions and facilities without having to even consider accessibility or usability challenges; this to me is the greatest gauge of an environment’s success in terms of inclusive design.” Liam McMunn adds: “It’s palpable the lift in staff morale and how they engage with the building and their workplace.”
The brief promised a revolutionary, highly-accessible working environment, that actively encourages collaboration and pushes the boundary in terms of sustainability, and from initial anecdotal feedback, it seems that the resulting building is living up to these promises.
However, energy was also a key driver in the brief, and whether the building fully fulfils its highly-ambitious and admirable energy performance promises, only time will tell.
Selected project details
Client: Central Bank of Ireland
Architect: Henry J Lyons Architects
Main contractor: Walls Construction Ltd.
Project managers: Cogent Associates
QS & civil, structural & facade engineers: AECOM
Environmental & sustainability engineers: O’Connor Sutton Cronin
Glazing: All glass processed by CareyGlass and installed by Architectural Aluminium
Concrete: Leinster Reinforcements
CHP system: Temp Technology
Underfloor heating: Unipipe
Rainwater harvesting: Waterways Environmental
Joinery & interiors: Woodfit
Mechanical & electrical services contractor: Winthrop engineering & contracting
Fire engineering: Maurice Johnson & Partners
Trench heaters: Advanced Technical Products
Air conditioning: Crossflow Air Conditioning
Air handling units: FläktGroup Ireland Ltd
Electric car charging: Electro Automation
Radiators: Merriott
Condensing boilers: Euro Gas
Landscape architects: Mitchell & Associates
GGBS: Ecocem
Carpets: Interface
In detail
Building type: 37,000 sqm public office building
Location: North Wall Quay, Dublin 1
Completion date: March 2017
Budget: €140m
Environmental accreditation: Breeam Outstanding
Other accreditations: RIAI Award for Accessible Design, and ISO 5014 and OHSAS 18001 integrated certification.
Space heating demand (calculated): 45 kWh/m2/yr Cooling demand
(calculated): 21 kWh/m2/yr Primary energy demand (calculated): 90 kWh/m2/yr
Building Energy Rating: A2
Energy performance coefficient (EPC): 0.28
Carbon performance coefficient (CPC): 0.26
Airtightness (at 50 Pascals): 3.7m³/hr/m2
Thermal Bridging: All key external envelope interfaces were modelled in line with ISO 10211:2007. The glazed facade underwent rigorous thermal bridging analysis and airtightness testing both prior to construction with full scale prototypes and following completion to test final airtightness figures. Glazed faced: Glass skin which is shielded from glare and solar heat gain by an outer layer of anodized aluminium triangular mesh panels. The density and coverage of the mesh is tuned to the specific orientation of the facade it protects. Overall U-Value 1.30 W/(m²K). G-Value Glass: 0.35
Solid walls: Overall U-Value 0.27 W/m²K
Roof: Overall U-Value 0.22 W/m²K
Heating: A highly efficient gas-fired combined heat and power (CHP) unit runs all year round, providing a base load (summer season) for the building’s heating & hot water requirements. At peak heating demand periods (winter load) the balance of the heating load is provided through a series of gas condensing boilers (105% annual efficiency). For space heating, hot water is fed to fan coil units with tempered air circulated over to provide heating. The tempered air is pre-heated via a thermal wheel on the mechanical air extract unit. The ground floor and first floor areas in the central atrium are heated via an underfloor heating network.
Provision has been made within the building to connect to a future line from the docklands district heating network which will be supplied via the Poolbeg incinerator. Once operational, the connection would ensure that the heating system demand load at peak times would be supplemented by the district heating network.
Ventilation & indoor air quality: Mixed mode ventilation system. Opening louvres at each floor level linked to the Buildings Management System (BMS), external environmental conditions are monitored via the BMS. The cool external air is pulled across the floor plate into the rising atrium via the “stack effect” and a series of mechanical extract fans located at the top of the atrium. Each bank of facade louvres are fitted with local controls. They can be locally closed or opened if required while also being linked to the BMS.
Mechanical cooling is provided by a high efficiency chiller, the chiller incorporates a free cooling module. Once the ambient external temperature reaches below a certain point, the chiller uses the external air temperature to cool down the fresh air intake to the required levels to provide a comfortable indoor working environment thus reducing the need for mechanical refrigeration.
The quality of the indoor air is monitored via CO2 sensors, these are linked back to the buildings BMS. In order to achieve optimum levels of indoor air quality, offices typically require fresh air supply at 10L/s, this represents a level of 800ppm – 1000ppm. The BMS is programmed to alert when the CO2 levels reach 900ppm, the supply fresh air levels are adjusted via variable air volume controllers on the supply intake to counter rising CO2 levels. CO2 levels recorded at 4.30pm on Wed 15 Nov indicated that an average level of 810ppm was being maintained across all occupied floors.
Lighting: All internal lighting is LED. Open plan office areas are fitted with photocells, once the natural light levels fall below a given lux level then the photocell will switch on the LED lighting. Task lighting is provided to given user control over local lighting levels, all task lights are fitted with PIR motion detectors.
Other eco-friendly measures: 300 bicycle spaces with shower and changing facilities, electrical vehicle charging points and carpooling spaces, LED lighting technology throughout, an extensive green roof was used throughout the external podium promoting biodiversity. Selection of fit out materials based on their VOC content, floor covering, and adhesive, paint, and timber engineered flooring with low VOC content were chosen. Products also included high recycled content where possible (Interface carpet with a total recycled content of 62%). All timber used throughout both the construction and fit out was FSC certified and was required to be backed up with a full suite of chain of custody certificates.
Image gallery
https://passivehouseplus.co.uk/magazine/new-build/ireland-s-new-central-bank-hits-nzeb-breeam-outstanding-eco-rating#sigProId9d22aa2e6b