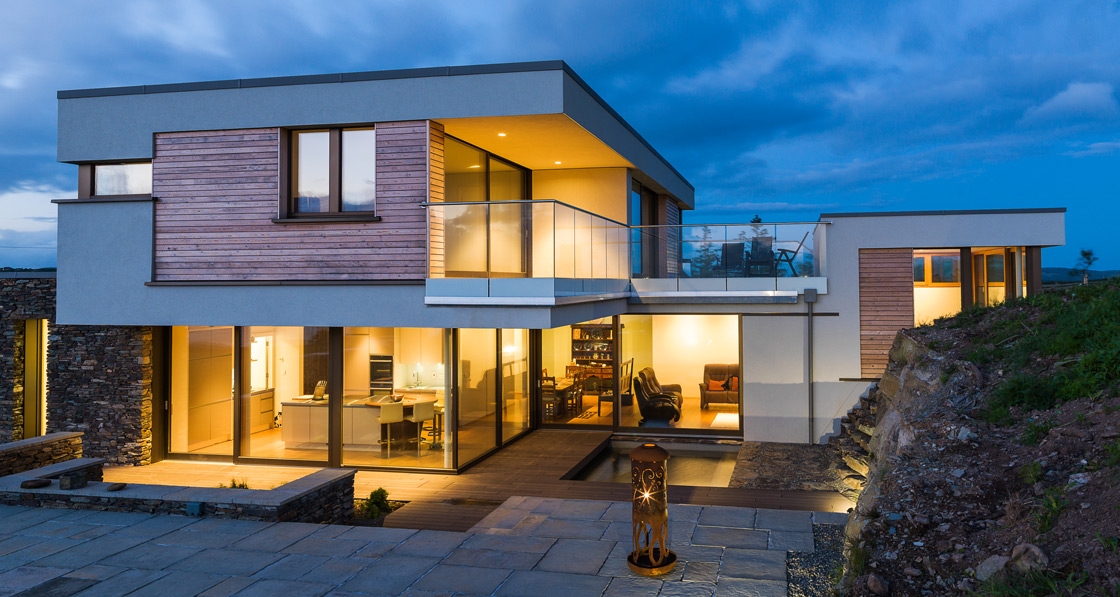
- New build
- Posted
West Cork passive house raises design bar
The most celebrated architecture of the 20th century belongs firmly to the oil age, a heady mix of glass and steel and no need to have regard to comfort, given the availability of cheap fossil energy to fuel heating & cooling systems. But in the 21st century our buildings must adapt to and mitigate against climate change. That needn’t mean compromising on design, as one West Cork passive house shows
Click here for project specs and suppliers
This article was originally published in issue 17 of Passive House Plus magazine. Want immediate access to all back issues and exclusive extra content? Click here to subscribe for as little as €10, or click here to receive the next issue free of charge
There is no such thing as a passive house aesthetic. As long-time readers of Passive House Plus will recall, the 100 or so passive house projects featured to date in these pages have taken in everything from arts & crafts style new builds and chic minimalist modernism, to more prosaic affordable and speculative housing.
That said, it’s undoubtedly true that simpler, more compact building forms make it easier and cheaper to build to the passive house standard – though this also applies when building to any standard – so the notion of the boxy passive house endures. Projects such as Wain Morehead Architects’ latest certified passive house prove that in the hands of the right architect, meeting the standard can inform rather than restrict architectural expression.
One would expect there to be at least a few challenges in the construction of a large house in an exposed location and with such a distinctive design. Resolving some typical construction problems might involve a compromise of some kind, but when the house is being built to the exacting passive house standard, there is arguably less flexibility in this regard.
That was the heart of the difficulty facing clients Nick and Annie, architects WMA and the construction team behind this stunning home situated right on the edge of a bay in West Cork.
Architect and designer John Morehead’s design for this 281sqm, two-storey four-bedroomed house included an expanse of floor-to-ceiling windows, particularly on the ground floor.
It’s easy to appreciate just how critical these windows were to the success of the design, given how it aimed to maximize the views of the beautiful location without compromising on thermal performance.
The project ran into difficulties and delays due to significant quality issues with the original window supplier, who subsequently appointed a liquidator. Austrian manufacturer OPTIWIN stepped up to the plate with replacement windows, though the absolute success of the project was ultimately down to the willingness of everyone concerned, including the clients and the main contractor, to “dig deep” and remain focused on the end result, says Morehead.
The main contractor, Kieran Crowley of CHOM Construction, said: “It’s been torture but I’m happy with the result. The house turned out very well. We do a lot of bespoke houses and we’re not afraid of anything in that sense, but when the windows gave trouble it delayed the project.”
The result that matters, of course, is the happiness of the clients. Having such a strong commitment to the passive house principle – and to sustainability in general – clearly helped Nick and Annie to keep them going during the period when things looked so bleak.
The couple, who held the passive house standard initially as a vague aspiration, bought a smallholding in 2008 and, during the lengthy planning application, the “opportunities to build to passive house designs economically and efficiently were increasing all the time, so we opted to go for fully passive”, says Nick.
They had felt the pressure to make the final commitment “because technologies were moving on, prices were coming down, and a belief that we needed to do something to be energy efficient and build for the future of ourselves and the planet, so we did that”.
From traditional to modern
Before they approached Morehead’s practice, WMA, they already had successfully secured planning permission for a four or five-bedroomed house of a “much more traditional design”, which had been designed by a local architect.
“We initially approached John with a view to building the original design, but to passive house standard and our research showed we could do it,” says Nick. WMA reviewed the design but it was decided to start again from scratch, mainly on the grounds that it would be cheaper to do so, than adapting the initial blueprint.
“We let John loose with very much the same brief in terms of spaces that we wanted, the concentration of the views that we wanted of the area, to the West and the North, and to make the best of the site that we got.” Crowley says John’s design and specifications, working with assistant architect Shane Fenton, were robust, although he wonders if it was necessary to have seven different wall types: “You won’t find too many passive houses with seven different wall types.” Morehead explains that there are three basic wall types in the building – cavity wall, timber frame and block on flat externally insulated with the Baumit system – with various rainscreens applied.
In addition, the structural design made things a little more difficult in terms of achieving airtightness. “But we got there,” says Crowley. Morehead’s design called for the integration of the structural components into the overall building envelope, but doing this without having to battle with unforeseen thermal bridges required some innovative work by structural engineer, Conor Coburn.
He used a product called Parallam, a form of engineered wood made from clipped veneer strands laid in parallel alignment and bonded with adhesive. “We had very large timber members providing the cantilevers, with the whole building effectively designed like a diaphragm,” said Morehead, who said Coburn “really thought outside the box and enabled us to get the large glazed areas underneath the overhang without too much structural interference.”
Once the windows were finally in place, WMA and CHOM worked hard to push down the energy demands, but it helped that the energy load itself is quite low.
Active heating and – if required – cooling is courtesy of a Nilan Geo 6 geothermal heat pump, while a Nilan Compact P heats the hot water using the exhaust air as well as powering the ventilation system. The heating and ventilation systems – and the building’s substantial PV array – were installed by sustainable energy specialists Energywise Ireland.
The PV system includes Sharp 250W polycrystalline panels with a SolarEdge inverter and power optimisers on each panel to increase output and offer full monitoring of the overall systems. “The ability to monitor the system arms the client with the knowledge of peak production times for electricity and therefore appliances can be timed to come on at these times, optimising performance,” explains Energywise director Berth Sheehy.
The Geo 6 is fed by 600 meters of 40mm horizontal collectors – half buried in a field, half buried in tight coils strategically located in the garden – about 180m in two layers under the rainwater soakaway, and then 60m vertically coiled surrounding the concrete septic tank. A genuinely hands-on client, Nick installed the 600m of collectors and associated septic tank himself, and had the foresight to incorporate an element of the loop in the percolation area, and the drainage area where rainwater is falling. Sheehy points out an additional energy benefit resulting from Nick’s approach. “The point is that there are gains to be had from rainwater – which at times has a higher temperature than ground water – and from waste energy from the house because of hot water usage.”
Sheehy adds that the Nilan unit comes with an integral secondary 250L cylinder for domestic hot water. “This cylinder can be preheated by the Geo 6 but also has a back-up electrical element. We’ve designed the system so that any excess energy generated by the PV that’s not required in the house is being dumped into this electrical element. Essentially you’re pre-heating the water with this free energy that would otherwise be lost to the grid in the absence of a tariff.”
Sheehy adds that although the building design minimised service penetrations to protect the airtight layer, continuous consultation with John Morehead also played a role.
“It’s impossible to foresee every scenario until you’re onsite. So your architect and M&E contractors have to be in constant consultation during the project to ensure that any decisions that are taken aren’t going to compromise the airtightness.”
As well as remaining true to the original sketch design, this passive house also managed to achieve an A1 BER.
Landscape integration
On the outside, the house integrates well into its immediate surroundings, through a combination of landscaping and finishes. “We incorporated natural stone from the site to make [it] blend in a bit better,” said Crowley. It turned out to be an ideal building stone.
On the upper floor, the living area opens out onto a sheltered terrace. Morehead said: “The use of site-quarried stone and opportunity to have external access from the upper floor, introduced an interesting dynamic to how the property and the gardens can be enjoyed. The building was conceived as a series of folding plates straddling the rock outcrop, which integrated large overhangs to address solar shading requirements.”
Inside, on the ground floor, which is south and west facing, the spaces are big and bright with floor to ceiling windows and spectacular views out over the bay. The living room, dining room and kitchen are all open plan, with the staircase acting as a central element dividing and defining the spaces.
The sheer extent of glass in this project is undoubtedly atypical of the sorts of passive house designs that predominate in Ireland and the UK. Morehead points out that location – and a particularly mild microclimate in West Cork that’s approximately 2C higher than Dublin temperatures – opened up the architectural possibilities. “Because it’s so mild, it enabled us to integrate unusually expansive areas of glazing for a passive house,” he says. A little design ingenuity also made substantial south-facing glazing possible without fears of cooking the occupants in warm weather. “The diaphragm structure enabled us to have very deep overhangs relatively easily. We were able to throw the shackles off – to take in the expansive views – and allow for a little overheating. We were aware that we may have overheating in certain instances, but were comfortable that having mechanical cooling – from a geothermal source – driven by our PV array and supported by our stack ventilation, we could deal with it. That then means that in the winter – when the sun is low – we can utilise far more of the solar energy that’s available in this mild environment with this large expanse of glass.”
Morehead used site-specific climate files to influence the design, but rather than paying to have it dynamically simulated by the Passive House Institute, defaulted to Cork City Airport climate data for certification – one of the five regional climate sets for Ireland now included in PHPP (compared to Dublin Airport data only in Ireland’s national calculation methodology, Deap).
Having now moved in, what do the clients like the most about it? “The ambience, the atmosphere and the comfort of the house; it’s a very contemporary design, we love the design, but it’s just a very comfortable space in which to live,” says Nick. “The views are obviously a very strong point.”
Morehead really likes the continuity of circulation that the stair placement has achieved through the ground-floor space. He is also happy with the penetration of sunlight throughout the dwelling, and the quality of finish that was achieved. “The workmanship was maintained at a very high standard and the contractors were able to embellish the designed details with their personal touches right across the trades.”
Crowley admits it took a little longer to ‘get it’. “It took a while to sink in, but I’m quite happy with the way it turned out. It is a good example of how you would make a modern design passive, because a lot of the houses they draw for passive standard are basic boxes. But he has a bit of shape and modern design to his.”
Bamboo finishes
The clients, in tune with their interest in using sustainable materials where possible, opted to use bamboo for the flooring, which is harvested at five years old from China and supplied by a German firm called Bambeau Gmbh.
“But we ended up not just with bamboo flooring. All the internal woodwork, staircases, handrails, [built-in] wardrobes, cupboards, cabinets and breakfast bar, apart from the kitchen units, are all bamboo,” says Nick. “It is a very sustainable, very durable, easily worked material which produces some aesthetically beautiful results.” A weather-proof bamboo–polymer composite - Bambeau Econudo, consisting of 60% bamboo, 40% polymer resins, which the company claim are ecologically sound – was chosen for external decking.
In addition to supplying and fitting the Noblessa kitchen – certified to the Blue Angel’s strict environmental criteria and featuring a 5 year warrany on all moving parts and a 7 year warranty on all finishes, with soft close mechanisms – Classic Kitchens used solid bamboo as the external finishes to the wardrobes, storage areas in hallway, dressing tables in two upstairs bedrooms and study desk. As Classic Kitchens’ John Russell explains, the experience of working with the material attested to its solidity: “It’s incredibly hard stuff so we had to get in specific cutters or blades – the resin in the bamboo was sticking to the blade and gumming it up. It’s a very stable product too – whereas a lot of flat sheets for making furniture can move or warp when you cut them."
Sustainable appliances
Unlike the Irish or UK national calculation methodologies, the PHPP software used in the design and verification of passive houses includes unregulated energy use – or plug loads – meaning that appliance selection can be critical. This house doesn’t disappoint. “We chose Neff ovens, partly because of their reputation for longevity,” says Nick. “We hear stories of them still going 30 to 40 years on.
And their power consumption is very energy efficient.” Another factor was space: the ovens are facing the island – and the space between was relatively tight – so the Neff facility for “slide and hide” was critical. “As you open the oven, the door slides under.” A Neff energy efficient induction hob was also installed – a modestly-sized hob flush with the seamless stainless steel worktop.
Pictured from WMA’s team are (l-r) Jennifer Kenefick, John Morehead, Shane Fenton, Cathal O’Boyle and Alexandra Nedela
Nick and Annie also carefully selected a cooker extractor for aesthetic and energy performance reasons. “Rather than a cooker hood, which would lower the ceiling, and ruin the effect of the floor to ceiling windows, we opted for a Smeg extractor which glides up from an oblong panel in the worktop when you switch it on. It’s flush with the worktop when not in use.” The Smeg unit includes high performance carbon filters – so the warm air from the extractor is being filtered to such a high standard that it can be recirculated into the room. The MVHR extraction is concentrated on the kitchen and bathroom in particular. “This means any cooking smells are contained within the kitchen,” says Nick.
A Liebherr vertical 345L freezer was chosen, which Nick says is completely frost free – using about 130 kW per year of electricity. A low energy Liebherr larder fridge was also chosen – with controlled humidity Biofresh drawers. “I have a head of broccoli that’s lasted two weeks,” says Nick. The appliances are completed with a high efficiency Bosch dishwasher and washing machine – both of which use about 4 litres of water per wash.
The washing machine sits in a utility room, in the single storey section, and a raised tower of about 1.6m was included to take two dolly-style kitchen ceiling drying racks. At the top of the tower there are two extract vents for the MVHR system to draw air through the tower, aided by two remotely openable clerestory windows to assist with drying on a fine day. “We dry two loads of laundry overnight without going outside,” says Nick, adding that the returned energy from the wash – with warm wet clothes – is going back into the heat recovery system – so being retained in the house or used to generate hot water.
The clients are also very pleased with the specialist exterior lighting – which was supplied by Shane O’Byrne of As Light – and general lighting by ERCO, which rely on low energy LEDs throughout in both cases.
The net result of all of this is a building that’s not only extraordinarily energy efficient but easy on the eye. Passive houses feel different to ordinary buildings, which is one of the reasons the International Passive House Days – and the opportunity to experience passive houses first hand – are such a central part of the Passive House Institute’s efforts.
(clockwise, from left) Slab penetration detail with insulation around pipes; wall section showing Quinn Lite blocks and 250mm cavity with TeploTies to minimise thermal bridging; insulation detail at footing to prevent thermal bridging; roof service cavity with ducting, Nilair ducting housed in a service cavity inside the airtight layer; roof build-up features 120mm Xtratherm Thin-R XT insulation over vapour control layer.
Professional photographer Gabrielle Morehead – who is married to architect John Morehead – visited the house on a stormy June evening to photograph it for this article. “It was quite calm when I arrived down but soon, the weather turned. I got caught in the rain when I was shooting, and made a mad dash back into the house.” The sensation of being in the house had a palpable, visceral effect. “It’s very hard to put your finger on it when you’re trying to pinpoint exactly what you’re experiencing. The only thing I can come up with is that it’s calm and it gives you a sense of peace. There’s no drama. The drama’s outside.
For John Morehead, a standard such as passive house, in the hands of a skilled architect, can help to reconcile the seeming conflict between design for beauty’s sake and the needs of occupants. “What’s the point in having nice architecture if you’re uncomfortable in it?” Morehead knows discomfort all too well – his practice also offers services to assist owners of problem buildings. “We come across places that are miserable – where people are frozen to death or fried. We’re accommodating people – we’re not on an architectural ego trip.”
Selected project details
Architectural services & passive house design: Wain Morehead Architects
Structural engineer: Construct Engineering
Main contractor: CHOM Construction Ltd
Quantity surveyors: Richard Leonard & Associates Ltd
Mechanical consultant, heating & ventilation supplier: Nilan Ireland
Mechanical & PV subcontractor: Energywise Ireland
Electrical subcontractor: John O’Sullivan
Airtightness tester: Collins Energy Consultants
EWI system: Baumit
Bonded bead insulation: Warmfill
Mineral wool insulation: Rockwool
Wood fibre insulation: Ecological Building Systems
Thermally broken wall ties: Ancon TeploTie, via Longs
AAC blocks: Quinn Lite
PIR insulation: Xtratherm
EPS & additional PIR insulation: Kingspan
Airtightness products: Ecological Building Systems/Siga
Windows and doors: OPTIWIN
Lighting: ERCO Lighting Ltd
Lighting controls: Legrand
External lighting: As Light Ltd
Heating controls: Heatmiser/Nilan
Sanitaryware: Soaks Bathrooms
Kitchen design & supply: Classic Kitchens
Appliances: Bosch, Liebherr, Neff & Smeg, via Dwyers Electrical
Bamboo flooring, decking and furniture finishes: Bambeau
Roofing: Soprema Ireland
Dry lining board: Fermacell
Screed: Sika Ireland
GGBS: Ecocem, via Keohane’s Readymix
Bore drilling: Harte Divining and Boring Ltd
Additional info
Building type: 281 square metre detached two-storey dwelling
Location: West Cork
Completion date: March 2016
Budget: Undisclosed
Passive house certification: Certified
Space heating demand (PHPP)*: 10.4 kWh/m2/yr
Heat load (PHPP)*: 9.92 W/m2
Primary energy demand (PHPP)*: 60.1 kWh/m2/yr
*The above PHPP calculated values are provisional and based on Cork climate data Energy performance coefficient (EPC): 0.153
Carbon performance coefficient (CPC): 0.156
BER: A1 (23.7 kWh/m2/yr)
Airtightness: 0.59 ACH at 50 Pa
Thermal bridging: Externally insulated generally, all junctions thermally modelled, all external structural items thermally isolated from thermal envelope ensuring continuity of thermal envelope. All window reveals insulated. Raft foundation eliminates the need for any penetrations in the insulation at ground level, and ensures that thermal continuity is maintained between the wall and slab insulation. Y-Value based on ACDs and numerical simulations 0.0262
Ground floor: Insulated raft foundation consisting of 200mm Aeroflor EPS300, 250mm concrete, 80mm Kingspan TF70 insulation (containing ventilation ductwork channels), 60mm Sika Viscocrete screed (containing underfloor heating), Bambeau Solid 3SF bamboo flooring. U-value: 0.09 W/m2K
WALLS
Stone wall: 200mm stone from site externally, over 100mm rendered blockwork, 250mm Warmfill Super Silver bead cavity insulation, 215mm blockwork, 15mm airtight plaster internally. U-value: 0.116 W/m2K
ETICS wall: Baumit Nanopor render system externally, over 250mm Kingspan Aerowall, rendered 215mm blockwork, 15mm airtight plaster internally. U-value: 0.121 W/m2K
Timber walls: Larch cladding or rendered cement board externally, over 50 x 50mm treated battens and counter-batten, Tyvek UV facade membrane, 60mm wood fibre board, 190x50mm timber stud with full fill Rockwool flexi,18mm OSB3, Pro Clima DA membrane taped and sealed, 50mm service cavity insulated with Kingspan TW50, finished with 15mm Fermacell board internally. U-value: 0.111 W/m2K
Roof: Soprema Flagon TPO membrane, over 120mm Xtratherm Thin-R XT insulation, vapour control layer, plywood deck, 300mm timber I-joists laid to falls (200mm air cavity & 100mm Rockwool Flexi), Intello Plus membrane, service void, plasterboard ceiling. U-value: 0.118 W/m2K
Windows: OPTIWIN triple-glazed, alu-clad timber windows with argon filling achieving overall U-value of 0.83 W/m2K
Heating system: Nilan Geo 6 unit provides primary space heating with a COP of 440%. Air to water heating is provided by the Compact P by Nilan.180L water storage with a 250L buffer tank
Ventilation: Nilan Compact P Geo heat recovery ventilation system, Passive House Institute certified to have heat recovery rate of 77%
Electricity: Ten panel (16.2m2) solar photovoltaic array – eight at 30°, two on the flat later added to achieve A1 BER target – with average annual output of 2104 kWh/a
Lighting: Low energy LED lighting throughout. Generally ERCO LED Wallwasher, ERCO Starpoint downlighter/ spotlight. Exterior lighting integrated with overall lighting design
Green materials: Fermacell dry lining board, 27% GGBS in concrete, all timber PEFC/FSC certified, along with FSC-certified bamboo products.
Image gallery
-
West Cork 01 West Cork 01
-
West Cork 02 West Cork 02
-
TitleWest Cork 03 TitleWest Cork 03
-
West Cork 04 West Cork 04
-
West Cork 05 West Cork 05
-
West Cork 06 West Cork 06
-
West Cork 07 West Cork 07
-
West Cork 08 West Cork 08
-
West Cork 09 West Cork 09
-
West Cork 10 West Cork 10
https://passivehouseplus.co.uk/magazine/new-build/west-cork-passive-house-raises-design-bar#sigProId0b082666ae