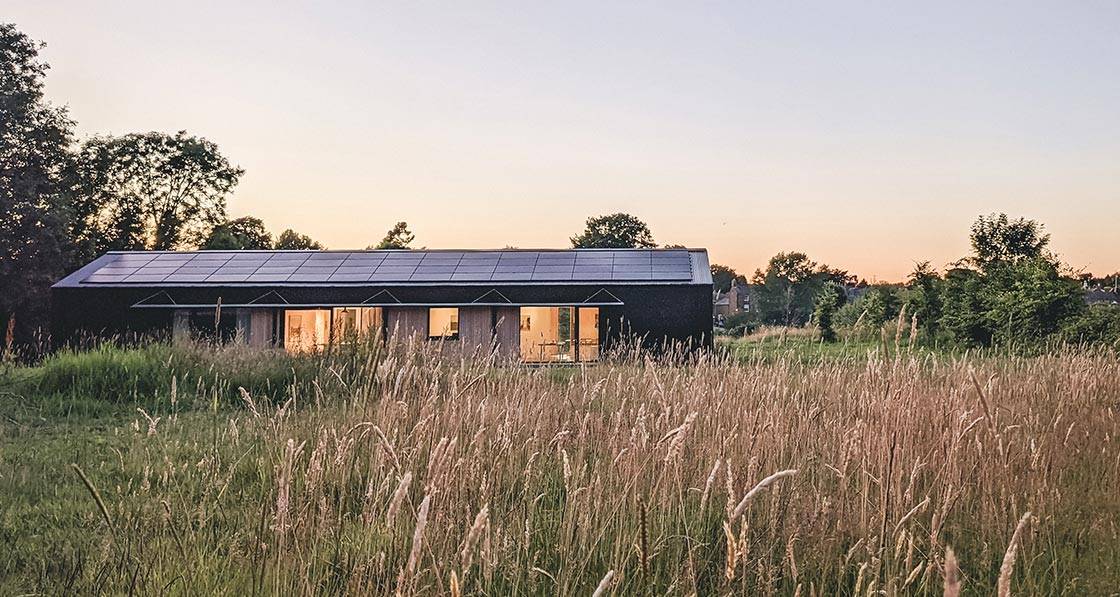
- Upgrade
- Posted
From small screen to deep green
The new Oxfordshire studio of Charlie Luxton Design, the practice of the well-known TV presenter and architectural designer, is deeply impressive for its exhaustive attention to sustainability across every facet of the project, from energy use and embodied carbon to the reuse of materials and the ecological restoration of the three-and-a-half-acre site. It’s a gorgeous building, too.
Click here for project specs and suppliers
Building type: Steel barn converted into 204 m2 office and recording studio
Method: Flat pack I-beam timber frame, wood fibre insulation, material reuse and biodiversity focus
Location: Oxfordshire
Standard: Uncertified passive house
Energy use: Beyond net zero. Net export of 1,400 kWh from Jan to mid July 2023, excluding EV charging.
Embodied carbon: Meets LETI 2030 target and RIBA 2025 target
If you’re a fan of architectural TV shows, you will know Charlie Luxton from programmes such as Building the Dream, Homes by the Sea, and Building a New Life in the Country. What you may be less aware of is the sheer depth and breadth of his knowledge of — and commitment to — sustainable building.
Charlie heads his own small practice, Charlie Luxton Design (CLD). When the firm decided to build a new studio just outside the village of Hook Norton in Oxfordshire, it was a chance to push the envelope across a swathe of sustainability metrics in a way that is often difficult when working for a client. “If I’m going to do a project for me, I have to make it a massive education piece,” he says.
His commitment to environmental protection stretches back to his childhood in Australia, when protests to save some of the country’s old growth forests made a lasting impression on him. He moved to a farm in England at the age of nine and says playing in streams and climbing trees helped to foster his love of nature.
Charlie and his wife Kate, who is CLD’s studio manager, were finishing their own house next door when this three-and-a-halfacre plot came up for sale. It had been used to keep horses and had a steel-framed barn surrounded by heavily grazed paddock. The CLD team had been working in Charlie and Kate’s old thatch cottage down the road, but this site offered the perfect opportunity to create a purpose-built studio.
Building-within-a-building
From the outset, Charlie was keen to make use of the existing barn. “We stripped it back very carefully and engineered it so we could work with the existing concrete slab,” he says. “We took down the walls, took all the wood out of the stables for reuse, and basically tried to design a [new] building that could use as much of the existing structure as possible.”
Building on the existing slab required extra thick walls to spread the load of the new studio. But with a goal to get close to the passive house standard and a preference for natural insulation, the walls were always likely to be quite thick.
Charlie served as principal contractor and recruited as many local trades as he could. The team laid a thin layer of levelling screed and then set out to build a new timber-framed studio within the structure of the old barn.
“The idea was very much to build a building within the building,” he says, “so that we didn’t put any additional load on the frame, because the frames of those buildings are really only designed to take themselves, and the wind.”
But the barn did provide a sheltered space within which to build the studio. The CLD team chose a timber I-beam system from German wood product specialist Steico. Each of the beams was digitally modelled and precut before being delivered to site. It’s a low-waste system Charlie had grown to like on previous projects.
-
Charlie Luxton in the old building. The slab and steel frame were retained, and some blocks were reused Charlie Luxton in the old building. The slab and steel frame were retained, and some blocks were reused
-
Battened and counterbattened wall awaiting the powder coated corrugated iron cladding and roofing. Battened and counterbattened wall awaiting the powder coated corrugated iron cladding and roofing.
-
Levelling screed to existing slab Levelling screed to existing slab
-
Steico I-beam frame going up Steico I-beam frame going up
-
Steico I-beam frame going up Steico I-beam frame going up
-
Caberfloor chipboard on 100 mm Platinum EPS, including channels cut for 75 mm semirigid Airflow ducting, with a further 150 mm EPS beneath Caberfloor chipboard on 100 mm Platinum EPS, including channels cut for 75 mm semirigid Airflow ducting, with a further 150 mm EPS beneath
-
25 mm battens on Durelix Vapourblock airtight vapour control board and Pro Clima airtight tapes, after the Steico Zell woodfibre insulation was blown in 25 mm battens on Durelix Vapourblock airtight vapour control board and Pro Clima airtight tapes, after the Steico Zell woodfibre insulation was blown in
-
Fermacell boards Fermacell boards
-
Luxton and the Airflow Flexi DV1600 MVHR system Luxton and the Airflow Flexi DV1600 MVHR system
-
Panelvent under Solitex Fronta vapour permeable breather membrane Panelvent under Solitex Fronta vapour permeable breather membrane
https://passivehouseplus.co.uk/magazine/upgrade/from-small-screen-to-deep-green#sigProId3fb304f57d
“The thing about going with these precut systems is you can get an entire building on one lorry,” he says, and this was one of many ways he sought to reduce the carbon footprint of the build.
Steico laminated veneer lumber (LVL) — a mass timber product that takes dozens of thin layers of wood and glues them together to create a structural timber panel — was used for posts and beams, and around the building’s Internorm timber aluclad triple glazed windows. Durelis VapourBlock, a structural chipboard that also provides airtightness and vapour control, frames the walls and roof internally, and serves as the main airtightness layer too. The walls and roof were pumped with blown cellulose insulation (Charlie brought his local labourers down to PYC Systems in Welshpool for training in how to install it), and then lined internally with Fermacell board, which is made from recycled gypsum and paper.
The team clad the structure in dark, powder- coated standing seam steel and British- grown larch and fitted a cap of EPS insulation — salvaged from another project — above the LVL ridge beam to stop thermal bridging down through the steel joist hangers. “We were really careful about that level of detailing,” Charlie says. The roof is finished with a 20 kW solar PV array.
Design for reuse
This article was originally published in issue 45 of Passive House Plus magazine. Want immediate access to all back issues and exclusive extra content? Click here to subscribe for as little as €15, or click here to receive the next issue free of charge
Inside, the team fitted 250 mm of EPS insulation over the existing slab. This was laid without any glue so that it could be easily reused in future. “We planned it all out on a computer so that we could do it with as few cuts as possible,” Charlie says. The team also used a hot wire cutter to cut the insulation as cleanly as possible, to stop microplastics from breaking off. The floors are finished with boards made from English elm.
An obsession with minimising the environmental impact of materials permeated the whole project. “We really tried to reuse as much as we can,” Charlie says. Timber reclaimed from the horse stables was reused for internal finishes. An oak-framed sliding door was salvaged from another project and re-purposed as an internal screen. Old walkways from the site were reused as solar shading. Recycled furniture and second-hand appliances were specified throughout. Outside, rather than completely dig up the concrete yard, the team simply broke up some areas of concrete and planted within it.
Charlie says that thinking about how to reuse materials at scale was one of the big takeaways from the project. “How do you use the things you’ve got to make the buildings you need?” he asks. “And how do you do that at scale? How do you find the materials, log the materials, test the materials, certify the materials?” These are some of the next big environmental questions for the building sector to get to grips with.
The CLD team also thought about how the building, and its components, might be used long into the future. “We sort of tried to imagine how you might minimise disruption for other phases of the life of the building,” he says. The building has been plumbed for future conversion to a house, and it’s been framed so that more doors can easily be installed in future. Cladding and roofing were also fixed to be easy to remove.
Minimalist heating
The finished studio achieved an airtightness score of 0.3 air changes per hour and is within the parameters for passive house certification. The building is both heated and cooled, when needed, by an air source heat pump that warms or cools supply air being drawn into the building through a Passive House Institute-certified heat recovery ventilation system from Airflow, the specialist ventilation supplier who suggested this project to Passive House Plus for this article. The system, along with the lighting system, is managed by a building automation system from Wiise.
It’s a fairly minimal approach to heating, and Charlie says it keeps the building sufficiently warm on all but the three or four coldest days of the year. But while the building was wired for infrared radiators to top up the heating, he decided against putting them in. “Given how little we would use it, I suspect the embodied energy would make no sense whatsoever,” he says.
So instead, on freezing winter mornings, an old electric radiator, covered in paint, is wheeled to provide some extra heat, and Charlie says this works well.
And what about comfort on hot days? The heat pump provides cooling too, and on the hottest day of 2022, when temperatures in Oxfordshire exceeded 38 C, the temperature in the studio was a warm-but-acceptable 26 C. An external shade limits solar gain from the high summer sun to the south-facing studio space.
The 20 kW solar PV array provides electricity to the studio, to two electric cars, and to Charlie and Kate’s own house next door. So far this year, as of 12 June, the three buildings have used 11 mW of electricity in total, but only 2.4 mW of this was imported from the grid, with the rest — almost 80 per cent — coming from solar power. Charlie is planning to install a battery next year.
Studio space
And what about the spaces inside? What kind of studio did a group of architects and designers want to create for themselves to work in? Kate says that while the old thatched cottage was a pleasant space, it wasn’t really suitable for an office. “For clients coming, it was slightly weird,” she says. For the new studio, the team wanted to have an open plan working area that fostered collaboration, but also separate rooms for calls, meetings, or quiet working. And with its light filled spaces and warm timber finishes, the new studio is certainly a beautiful space to work in.
“I know the team love coming here,” Kate says, “post-Covid there has been a culture of working from home, but we didn’t suffer from that. The guys wanted to get back into the office and be all together, and I think having this building is a huge part of that.” She adds: “It’s a place that we want our clients to come to, we want to have meetings here, we want to share it with people.” CLD does not use the whole building — about one third of the footprint is a music studio for writing and rehearsal, rented by a friend of Charlie’s, and some work was needed during the build to ensure this would be acoustically separated. “You can hear a little bit of drumming, but nothing bothersome, actually it’s really quite nice,” he says.
The needs of this space were factored into the design of the building management systems by Wiise. When musicians press record in the studio, the ventilation system – which is inaudible to the occupants but may be detectable in recordings – is temporarily turned off.
Rewilding the site
Outside, the team’s attention to detail extended well beyond the boundaries of the building. The site was heavily cropped and packed with hardcore and rubber crumb, and as soon as they got the site, Charlie wanted to start restoring biodiversity. This included planting over seven hundred native trees — particularly elm, alder and black poplar — plus new areas of wildflower flower meadow, and native scrub with crab apple, dog rose, hazel and rowan.
Charlie estimates that it will take about twenty years for the surrounding site to sequester, in the soil and new vegetation, the building’s carbon footprint (excluding the PV array – see embodied carbon section below) of sixty-seven tonnes. He says this is based on back-of-the-envelope sums, but he’s having more detailed calculations performed soon, and developing a longer-term biodiversity management plan.
He says that in the seven years since they bought the site, it has gradually become richer in wildlife, and noticeably louder with the sounds of nature. “Last year waking up at certain times of day and in certain weather was extraordinary,” he says.
“That’s just been joyous to be honest with you… the sense of wellbeing it gives you to bring a land back to biodiversity health. It just feels amazing.”
The project was a winner of the sustainability prize at the 2023 Architects’ Journal Small Projects Awards. “That was a real vindication of what we’ve done and what we’ve worked towards,” Kate says. “To get that industry recognition was so exciting and we feel incredibly proud of it.”
I asked Charlie what the biggest challenge on the building was, but he says it all went pretty smoothly. “It went really well if I’m honest,” he says. “Do you know why? Because it was incredibly rational. And that’s the biggest lesson I think is, we just need to make things a lot simpler, to make all of our buildings a lot simpler.” He says that simpler buildings mean quicker and cheaper builds, less travel to site, lower embodied energy, and more flexible and longer- lasting buildings. It makes it easier to deliver airtightness and eliminate thermal bridges, too.
“And I think it’s actually really liberating to say I can make a really simple building, and if I concentrate and work really hard on that, it can be beautiful.”
Embodied carbon
by Jeff Colley
Embodied carbon calculations were conducted by passive house consultant Richard Bendy of The Healthy Home, using the AECB’s PHPP-based embodied carbon calculation tool, PHribbon. I amended these calculations to consider the effect of different product specifications in a couple of high impact areas. The project was then compared against the embodied carbon targets for offices in the RIBA 2030 Climate Challenge, and the LETI 2030 design targets.
The scope included the whole building, with the exception of reused/recycled items such as the retained concrete slab, steel frame and blocks for a first course of blockwork, along with brise soleil made from a recycled walkway. Groundworks were not included. Fixed furniture and equipment – including reused appliances – were also omitted, as were external works, along with ductwork, pipes, electrical fittings, and the Mixergy hot water cylinder, but the vast bulk of the building was included.
In the absence of quantified data on construction process-related emissions, the calculations rely on the default assumption in the RICS methodology, where construction process emissions are derived based on the value of the project. In this case, the construction process-related emissions, which are taken to represent 23 tonnes of CO2e, are likely an over-estimate, given the care taken by the project team to minimise emissions throughout the build.
In several cases, where the specified product didn’t have source data – such as an Environmental Product Declaration, default data, or CIBSE TM65 calculations in the case of building services – data was taken from EPDs or Product Eco Passports on similar products, to produce an indicative result. Most notably, this was the case with regard to the PV array, EPS insulation, air-to-air heat pump and heat recovery ventilation system.
Based on the precautionary principle, in the case of the building’s large PV array, where the specified product didn’t have an EPD, a similar product a with high embodied CO2 score was included in the calculations.
On this basis, the building scored a cradleto- grave total of 814 kg CO2e, meaning it meets the RIBA 2025 target for offices.
As Passive House Plus has shown previously, this total was dominated by the large PV array, which contributes a whopping 59.3 per cent of the total – albeit based on a panel with an EPD showing a high embodied carbon score, given the absence of an EPD for the actual panels used. If the roof mounted array is omitted, the total is just 332 kg CO2e/m2. This ignores the energy generated by the array, and is based on the conservative requirement set by RICS that any replacement materials/technologies within the 60-year study period for the building must be assumed to have the same embodied carbon emissions as the initial one – a highly questionable assertion given the rate of decarbonisation in industry. Based on the projected lifespan of 25 years in the EPD for the default PV array chosen, this meant two replacement arrays were included.
It is worth adding, however, that if the value for what is currently the lowest emissions PV array on the market was used – the Sunpower Maxeon 3 – the totals for the PV array would have dropped by 73 per cent – or a cradle-to-grave total of over 26 tonnes, versus almost 98.5 tonnes. While this massive reduction owes mainly to the panel’s low carbon manufacturing – notably including the wafer and ingot being manufactured in Norway, using hydroelectric power – it’s also due to the panel’s higher output. For this calculation, 103 m2 of Maxeon 3 array had the same output as 120 m2 of the high carbon array that was assumed.
While thinking in terms of cradle-to-grave impacts is key, there is an argument that greater emphasis should be placed on reducing emissions now, provided it doesn’t lock in avoidable emissions over the lifespan of the building via operational energy use and avoidable repair or replacement of components. For this reason, LETI has set upfront embodied carbon emissions targets, alongside cradle-to- grave and operational energy targets.
On this basis, the building fares very well, registering a total of 217 kg CO2e/m2, comfortably beating LETI’s 2030 target for upfront embodied carbon target for office buildings of 350 kg CO2e/m2.
It’s also worth noting that because both RIBA and LETI – quite reasonably – have separate embodied carbon and operational energy performance target, the extra carbon invested in reducing emissions over time is counted, but the carbon saved through energy efficiency and generation of renewable energy isn’t. It may be the case that the upfront carbon pays back very quickly, which is precisely why it makes sense to have embodied carbon and operational energy targets, rather than trading one off against the other.
One factor which substantially helps: LETI’s targets don’t count roof-mounted PV arrays, instead regarding them as part of the grid, which drops the upfront total by 157 kg CO2e/m2.
Based on LETI’s definitions of upfront emissions alone – excluding the PV array – the biggest embodied carbon total comes from the standing seam galvanised steel cladding at over eight tonnes – an estimate which would have increased if the impact of the vertical steel ribs on surface area of materials was considered.
While LETI’s targets don’t permit CO2 sequestered in materials to be offset against the emissions released upfront, the reliance on timber and wood fibre insulation means that at the point of practical completion, the building’s materials had absorbed and stored 176 kg CO2e/m2 – over 80 per cent of the upfront total.
Another factor significantly affecting the cradle to grave totals is the life cycle assessment requirement to consider the sequestered CO2 in the building’s timber and timber-based materials as effectively being released into the atmosphere at the building’s assumed end of life. 35.9 tonnes of CO2 stored in the building become 40.8 tonnes at the end of life, through a combination of the emissions being assumed to be released, and the extra carbon spent in transporting and processing the materials at that stage.
Selected project details
Client, architect, main contractor: Charlie Luxton Design
Passive house consultant: The Healthy Home
Structural engineer: Varndell Engineering
Quantity surveyor: Andrew Bird Associates
Electric contractor: AMR Electrical Contractor
Airtightness tester: Aldas
Life cycle assessment: The Healthy Home
Building system supplier: Steico
Wood fibre insulation: Steico
Floor insulation (EPS): Kay-Metzeler
Windows & doors: Internorm, via At-Eco
Liquid airtight membrane: Blowerproof, via Ecomerchant
Airtight tapes & membranes: Pro Clima, via Ecomerchant
Corrugated metal roofing: Sandford Roofing
Fit out: Hook Norton Construction
British elm floorboards: Sutton Timber
Heat pump: Panasonic, via Airflow
MVHR: Airflow
Solar PV: Aspey Energy
Building management system: oxone, via Wiise
Landscaping: Katie Guillebaud Garden Design
Breathable sheathing board: Panelvent, via Ecomerchant
Insurance: The Build Store
Hot water cylinder: Mixergy
Lighting: Darklight design
Sanitaryware: Duravit
Insulating blowing machine and training: PYC
In detail
Building type: 204 m2 (gross internal floor area) timber frame building comprising architectural studio and music studio.
Treated floor area: 195 m2
Site type & location: Village edge site, Hook Norton, Oxfordshire.
Budget: £340,500 (£1,669 per square metre). Inclusive of landscaping but exclusive of VAT, fees and loose furniture.
Completion date: January 2022
Passive house certification: Not certified
Space heating demand (PHPP): 12 kWh/m2/yr
Heat load (PHPP): 10 W/m2
Primary energy non-renewable (PHPP): 15 kWh/m2/yr
Primary energy renewable (PHPP): 13 kWh/m2/yr
Renewable energy generation (PHPP): 65 kWh/m2/yr
Heat loss form factor (PHPP): 3.6
Overheating (PHPP): 4 per cent of year above 25 C
Number of occupants (PHPP): 12
Embodied carbon: When assessed in line with requirements of the RIBA 2030 Climate Challenge, the whole-life cycle carbon footprint (A1 to C4, excluding emissions from operational energy and water use) calculated as 76.4 tonnes CO2e or 814 kg CO2e/m2 gross internal area in PHRibbon. 59.3 per cent of this total is based on the PV array alone, albeit based on conservative default data), meeting the RIBA 2025 target for office buildings.
Measured energy usage: 39.8kwh/m2/yr
Airtightness (at 50 Pascals): 0.3 air changes per hour
Ground floor: 22 mm elm floorboards, followed underneath by Caberfloor Chipboard flooring, 100 mm timbers at 600 mm centres with 100 mm platinum EPS, on 150 mm timbers at 1200 mm centres with 150 mm white EPS, on radon-proof DPM, on levelling screed, on existing concrete slab. U-value: 0.13 W/m2K.
Walls: Polyester powder coated corrugated iron cladding to existing steel frame, followed inside by ventilated cavity, breather membrane, Panelvent breathable sheathing board, Steico I-beam system with 300 mm Steico Zell wood fibre insulation, Durelos Vapourblock airtight vapour control board, 25 mm services zone, Fermacell board. U-value: 0.132 W/m2K
Roof: Polyester powder coated corrugated iron sheet on steel frame, followed underneath by wind-tight membrane, Panvelvent breathable sheathing board, Steico I-beam system with 300 mm Steico Zell wood fibre insulation, Durelis Vapourblock airtight vapour control board, 25 mm services zone, 12.5 mm
plasterboard to ceiling. U-value: 0.132 W/m2K Windows & doors: Internorm HF410 triple glazed timber-aluclad windows throughout. Plus, Internorm HS330 timber/aluminium lift and slide door. Installed U-value range: 0.70 to 0.82 W/m2K.
Heating & ventilation system: Airflow Flexi DV1600 MVHR system. Passive House Institute certified heat recovery rate of 86 per cent. Extracts up to 1,600 m3/h (0.44 m3/s) at 200 Pa. A Panasonic PACi Elite single phase inverter air conditioner/heat pump (with R32 refrigerant) provides heating or cooling to MVHR supply air via a DX coil.
Electricity: 20 kW solar photovoltaic array on the south-facing roof. Provides electricity to this building, three electric car chargers and to the house next door. Between 1 January and 12 June 2023, the PV system had supplied 8.6 mW out of 11 mW consumed on the site, with 2.4 mW imported from the grid.
Biodiversity and landscape: 2,100 m2 of land stripped of hard standing, rubber crumb and returned to wildflower and scrub. 180 tonnes of hardcore taken from land for local recycling. 25 m3 of rubber crumb reclaimed from menage for reuse locally. 1,800 m2 native scrub, 2,500 m2 of wildflower and over 700 native trees planted. The next step is to analyse the biodiversity net gain and develop a long-term management strategy with local wildlife trust.
Sustainable materials: Steico PEFC certified timber building system, steel barn and concrete slab retained, salvaged oak door reused as internal screen, salvaged timber from horse stables used for internal finish, walkways recycled as solar shading, rubber crumb reused locally, concrete blockwork and site hardcore reused. Floor insulation, cladding and roofing are designed to be easy to remove and reuse in future. English larch cladding, English elm floorboards. Recycled furniture and secondhand appliances throughout.
Image gallery
https://passivehouseplus.co.uk/magazine/upgrade/from-small-screen-to-deep-green#sigProId5af3e94e55