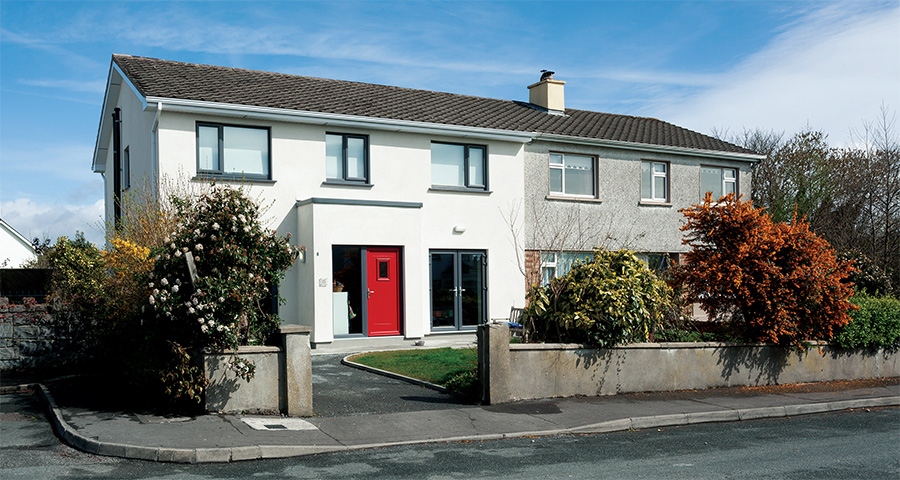
- Upgrade
- Posted
Ireland’s first fully passive retrofit
This 1960s Galway home was turned into a passive house - and is costing just €55 per year to heat.
A new retrofit project in Galway has shown just how far the retrofit of a typical Irish home can go, by bringing a 1960s semi-detached house up to the full passive house standard. The house in Salthill is home to Ciaran Ryan and Mary Hodkinson, who had been living west of Galway City in Furbo, where they had built an energy efficient home in the 1990s.
But they were keen to move to the city, and wanted a comfortable home they would never have to refurbish again. “We’re not going to move again after this. We want it to be really cheap to run, we want it to be warm and dry,” Ciaran says. They planned to buy an existing house and retrofit to a high standard.
Ciaran had met Irish architect Simon McGuinness through their mutual connections with Cuba — Ciaran runs a piano tuning workshop in Havana, while Simon is involved with the Irish Cuba Support Group. McGuinness had previously built a passive house in Ballymun, Dublin, and came on board as project architect.
McGuinness advised the couple to look for a house with a southerly orientation. Ciaran and Mary sold their house in Furbo and rented another while they looked for an ideal retrofit property. With Ireland’s property market having crashed, they didn’t expect this to take long. They looked at seven or eight houses, but none were quite right, and house prices were starting to creep up again.
Finally they found a semi-d for sale in Forster Park, Salthill for the right price — and with the front facade facing due south. McGuinness came down to see it. “It’s got a nice compact plan, which is very important. The nearer to a cube you can get the house, the easier it is to satisfy the requirements of passive house,” McGuinness says. This was crucial, because the budget wouldn’t stretch to making up for a lack of solar gain with, say, extra insulation.
But for McGuinness, the project was about more than one house. He also saw it as a chance to demonstrate how far deep a retrofit could go on a typical lrish semi-D. “I was interested in doing it for the sake of proving it was possible to do on a budget,” he says.
At the outset, he didn’t think it would be possible to achieve full passive house certification. The airtightness target of 0.6 air changes per hour (ACH), he felt, would simply be too onerous. “I didn’t think that was possible in a retrofit, because there was no record of anyone having done it,” he says. He did, however, guarantee the house would get under 1.0 air changes per hour, the Enerphit standard for retrofit.
Airtightness tapes and membranes were fitted to windows and doors, then taped to the walls on installation before being wet plastered over to ensure a total seal
The job came with a contractor in tow. Michael Nally & Sons had already built an extension to Ciaran and Mary’s house in Furbo, and the couple had been impressed with their workmanship. “Nallys had never built to the passive standard before but were quick to learn. They did the one-day training at Ecological Building systems and quickly got to grips with the specification,” McGuinness says.
McGuinness also produced an extremely detailed set of drawings for the builders. He felt these details would be useful long beyond this project. “The tender drawings that I produced were very, very comprehensive,” he says. “I knew that this was a house type that I would see in my career over and over again.” In fact, he actually produced two sets of drawings — one specific to this house, and another more generic set, which can be applied to similar houses in future.
The ground floor was insulated with 200mm of XPS insulation; the masonry walls were insulated externally with Webertherm mineral wool
When it came to insulating the building fabric, external insulation was the only real option for the walls. Dry lining internally would have sacrificed too much floor space, and would have risked causing condensation behind the insulation. McGuinness specified an external mineral wool system from Weber, which is breathable and capable of draining moisture away. The flexibility of the material also meant it could be fixed tightly against the pebble-dashed house without plastering first.
The existing cavity wall was also insulated with platinum polystyrene bead. Meanwhile the concrete roof tiles were removed, and the roof insulated with Rockwool between and above the ceiling joists. A small porch extension was built with externally-insulated Quinn-Lite block, and Munster Joinery’s passive-certified Future Proof PassiV PVC windows and doors were installed throughout the house.
As you might expect with a passive house retrofit, airtightness was the biggest challenge. During the design stage, McGuinness drew the airtight layer in blue on all plans, sections and details. Photos were included in the tender demonstrating how to sequence airtightness works. When the builders were on site later, they would upload photos to Instagram for McGuinness to review workmanship remotely.
The airtightness strategy was guided by five principles: a complete wet-plaster finish from floor-to-roof on the inside of the walls, no chased services on the external walls, an airtight membrane under the first floor ceiling, passive house certified windows and doors taped to walls under the wet plaster, and a total removal of the chimney down to the foundations.
The house’s humidity and temperature sensor
All the internal walls were cut back, and skirting boards removed, to ensure total coverage of plaster on the inner face of the external walls. Nally & Sons decided to remove all the internal partitions upstairs, which made it much easier to fit the airtight membrane above. McGuinness wrote about all of these issues, plus airtightness challenges with the slab-to-wall junction, attic hatch and ventilation system, in a previous article for Passive House Plus (‘Airtightness: the sleeping giant of energy efficiency’ in issue seven).
PHPP, the passive house software, told McGuinness that if the team got the airtightness down from 1.0 to under 0.5 ACH — not as easy a feat as it might sound — the house’s space heating demand would drop from 19 to 15kWh/m2/yr, low enough for full passive house certification. This focused minds on site. “I knew the difference was going to come down to airtightness,” he says.
The outdoor unit of the Thermia air-towater heat pump system
Ultimately, all the detailed drawings and photos paid off. “We only did one blower-door test and we got 0.37 air changes per hour,” McGuinness says. “So on that day we all had a pint.”
Radon was another challenge on site. “The building is in the highest radon gas risk area in Ireland and has exposed granite bedrock rock present in the subfloor void,” he says. To deal with this he specified a stack-based extract system beneath the ground floor slab connected to a radon sump, plus the installation of a radon membrane that’s adhered to the airtight layer.
When it came to heating, Ciaran and Mary had originally planned to put in a wood pellet boiler and solar thermal. But when M&E specialist Damien Mullins of Heat Doc came on board, he steered them away from that idea, and towards a Thermia air-to-water heat pump, for the sake of simplicity.
“The cost per kilowatt hour of their machines is very good,” Mullins says of Thermia. He says the controls are also excellent, and that the system heats the top of the buffer tank first, so hot water is available instantly. Mullins explains his preference for heat pumps: “They’re nearly like white goods. You don’t have to worry about topping it up with anything. So it’s very clean from a homeowner’s point of view.”
At Forster Park choosing a heat pump meant just one device, with one installer, and less maintenance, and this helped to save money too. The heat pump heats a 210 litre thermal store, which has an internal coil that sends instant hot water to all of the taps, as well as supplying two radiators on the ground floor, a towel rad in the upstairs bathroom, and a post heater in the Zehnder MVHR supply ducting.
The heat pump gathers information about heat loss from the house, and uses this to decide when it needs to come on, and at what temperature. Often the rads might just come on at 25C for half an hour. “[The heat pump] decides itself what the flow temperature should be,” Mullins says. “Once you commission it, there is a short period of tweaking. The short period of tweaking tailors the heat pump to the house, and after that it’s matching the heat loss of the house.”
The team can monitor the heat pump online to check when it comes on and off, how long it’s running for, and what the internal and external temperatures are. In their first year (or 12.3 months, more precisely) since moving in, Ciaran and Mary — who have two grown children living at home — spent just €190 on space heating and hot water, which breaks down as €55 for space heating and €135 for domestic hot water (including €127 from the heat pump and €7 worth of immersion). As McGuinness explains, this is based on applying an average Irish electricity price to the heat pump’s metered energy use of just 1117.45 kWh, and excludes VAT, levies, standing charges and utility company special offers.
McGuinness, who lectures at Dublin Institute of Technology, tasked one of his MSc students with working out how much the passive house elements of the upgrade had cost, discounting ‘do anyway’ items like the new bathroom and kitchen, and changes to the internal layout. He student produced a figure of €84,000, excluding VAT. “That was lower than I expected certainly,” McGuinness says.
He believes he can get this down even lower next time. For example, he says creating a zone for MVHR ducting under the first floor ceiling would have been cheaper and easier — from an airtightness perspective — than running all the ducting through the airtight membrane. He had worried about lowering the height of the first floor rooms, but says in hindsight this wouldn’t have been an issue.
Ciaran and Mary have been living in the house now for over a year. “There’s been no space heating on, probably since the middle of February,” Ciaran Ryan says.
“We were almost looking forward to the cold snaps, just to see how does the house behave.” His verdict? “It’s just spectacular. Everything is a constant temperature. You get up to go to the loo in the middle of the night and the hallway is the same temperature as the bedroom, and the bathroom is the same.” One of the biggest challenges when they moved in was finding a duvet thin enough to not overheat under.
“You come in at any stage, and you don’t have to worry about getting warm, or putting the heat on, or putting on a coat for the first fifteen minutes until the house heats up,” he says. The house received full passive house certification earlier this year, making it the first such retrofit in Ireland.
“Ciaran and Mary knew their budget was too tight but were prepared to compromise on everything except the works needed to achieve passive house certification. Their dedication has been justly rewarded,” Simon McGuinness says. “They have shown that the dream of living in a passive house is not the preserve of a wealthy elite. Passive house is for everyone.”
Selected project details
Architect: Simon McGuinness
Contractor: Michael Nally & Sons
Airtightness products: Ecological Building Systems
M&E design & installation: Heat Doc Ltd
External Insulation: Saint-Gobain Weber
Windows & doors: Munster Joinery
Thermal blocks: Quinn Lite
Rainwater goods: Wavin
Hot water cylinder: Dimplex
Cavity insulation: Certainfil
MVHR supplier: Zehnder, via Versatile
Heat pump supplier: Thermia, via Ashgrove
Mineral wool insulation: Rockwool
GGBS: Ecocem
Additional info
Building type: 142 square metre semi-detached house, built 1970. Full passive house retrofit with small porch extension to south elevation.
Location: Forster Park, Salthill, Co Galway, Ireland
Completion date: April 2014
Budget: €136,000 plus VAT
Passive house certification: Full passive house certification achieved (ref. no. 3173)
Building Energy Rating (DEAP)
Before: F (387.5 kWh/m2/yr)
After: A2 (42.9 kWh/m2/yr)
Space heating demand (PHPP)
Before: unknown
After: 15.14 kWh/m2/yr
Heat load (PHPP)
Before: unknown
After: 13 W/m2
Primary energy demand (PHPP)
Before: unknown
After: 84 kWh/m2/yr
Measured energy consumption (after): Total heating/DHW energy consumption for first year’s occupancy was 1117.45 kWh, or 7.87 kWh/m2 – or 18.65 kWh in primary energy terms.
Energy bills (after): €15.50 per month or €190 (excl. VAT, levies and standing charges) for space heat and hot water for the year.
Airtightness (at 50 Pascals)
Before: > 10m3/m2
After: 0.4 air changes per hour
Existing ground floor
Before: Uninsulated 150mm concrete floor slab (removed)
After: 22mm Plywood on 25mm SW battens, on 150 mm concrete floor slab, on damp proof membrane, on 200 mm XPS insulation, on radon barier. U-value: 0.116 W/m2K including an adjustment of 0.68
Existing walls
Before: 300mm plastered/rendered concrete block walls with 100mm unventilated air cavity. U-value: 1.82 W/m2K
After: 180mm Webertherm mineral wool insulation and Weber-rend mineral render finish externally to existing block walls. 100mm Certainfil blown platinum bead insulation into existing cavity. U-value: 0.12 W/m2K
Existing roof
Before: Concrete tiles on sarking felt, on battens, on timber trusses at 600mm centres with 50mm mineral wool between ceiling joists and plasterboard ceiling. U-value: 0.78 W/m2K
After: Concrete tiles on breather membrane, on battens, on timber trusses at 600mm centres with 300mm Rockwool above ceiling joists and 100mm between ceiling joists, on existing plasterboard ceiling, on Pro Clima Intelllo airtight membrane, on 25mm service cavity, on new plasterboard ceiling. U-value: 0.11 W/m2K
Extension walls (small front porch): 180mm Webertherm mineral wool insulation and mineral render finish externally on 215mm aerated Quinn-Lite block with plaster finish internally. U-value: 0.15 W/m2K.
Extension roof (small front porch): Single ply Sarnafil roofing on 50mm well ventilated air layer, on 200mm EPS insulation, on 100 SW joists at 600 c/c with 100mm mineral wool between, on 18mm
OSB airtight layer with 25mm services cavity and plasterboard ceiling. U-value: 0.11 W/m2K
Windows & doors
Before: Single-glazed, aluminium framed windows and timber doors. Overall approximate U-value: 5.8 W/m2K
After: Munster Joinery triple-glazed Future Proof PassiV uPVC windows and doors. Passive House Institute certified U-value (installed): 0.85 W/m2K
Heating system
Before: c.20 year old oil fired boiler & radiators throughout
After: Thermia DHP-AQ 6.7kW air-to-water heat pump with a CoP of 4.17 feeding 210ltr Dimplex thermal store with thermostatically controlled draw-off for two radiators and a towel rail.
Ventilation
Before: No ventilation system. Reliant on infiltration, kitchen extractor, chimney and opening windows.
After: Zehnder Comfoair 350 MVHR with a Passive House Institute certified heat recovery efficiency of 84%. Zehnder manifolds and 80mm diameter Zehnder ConfoTube flexible ductwork.
Green materials: Reused concrete block walls, timber and tile roof and timber intermediate floors; 50% Ecocem GGBS cement; mineral wool insulation throughout. Zero VOC ductwork to MVHR.
Image gallery
Passive House Plus digital subscribers can view an exclusive image gallery for this article. Click here to view