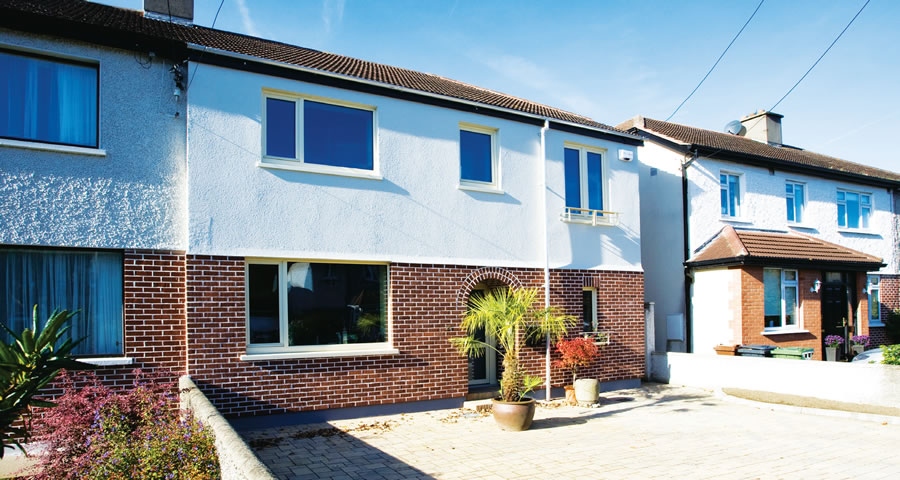
- Upgrade
- Posted
Monkstown semi-D sets deep retrofit example
A house in south Dublin recently became the first Irish building to become EnerPHit certified. Architect Joseph Little describes the challenges of meeting the Passive House Institute’s standard for upgrading existing buildings.
Deep retrofit is the future, but we’ve a lot to learn. The term deep retrofit refers to an energy-efficiency upgrade that achieves dramatic savings on existing use of between 50 to 90% using an integrated approach with attention paid to airtightness, summer overheating and ventilation – and not just super insulation.
While new buildings can be sequenced to maximise thermal continuity, airtightness and speed of construction, several factors complicate the works and impinge upon the performance possible in deep retrofits. Sub-optimal orientation and constructon methods, old rising walls, intermediate floors and decorative features of a bygone era – the list is long and formidable. The more of the old fabric that’s stripped away, the more ‘sins of the past’ become evident – and the more control is gained to ensure the desired standard is met. Yet the building becomes less and less an old building and if the issue isn’t addressed the associated embodied carbon emissions can rise significantly in spite of a great reduction in energy in use.
Though energy costs are constantly rising, they may still be too cheap to prompt enough owners to take the action needed to meet national climate change targets and provide sufficient security against future fuel prices. Highlighting the value gained in comfort, health and quality now – with greater financial security thereafter – will only galvanise so many private building owners. Governments know deep retrofit is the most sensible approach and they know this needs to be implemented everywhere. Shallow retrofits are problematic in that earlier measures may prevent – or have to be stripped-out to facilitate – later measures. If the EU’s building stock is to be made nearly climate neutral by 2050 yet the building fabric of most buildings is only retrofitted every 30-40 years, it’s clear that all retrofits undertaken now should meet the targets and compensate for those buildings that won’t or can’t. Philip Sellwood of the UK Energy Saving Trust1 estimates that one dwelling must be retrofitted per minute – and the interventions done right each time – if the UK’s 2050 targets are to be met. Ireland must be similar. Yet Irish energy efficiency grants end in 2013 and the government is following the UK in obliging energy providers to take a central role in this space while encouraging energy users at every scale to get the right works done, and done right. Not an easy task.
The rear extension orientates exactly to south then curves away to frame a dining table within and a deck without
As scale is a great way to make deep retrofit more affordable, the authorities could focus on terraces and districts with building types that allow a collective approach – many in older suburbs and disadvantaged areas. Such work could be used as a key way to reduce our dependency on fossil fuels, while aiding community resilience and alleviating fuel poverty – a chronic condition that’s under-reported in Ireland. This is not to mention the value in upskilling construction workers, increasing tax take and encouraging local innovation in this sector. Another challenge is to carry out retrofits without losing the character of traditional buildings and the districts or urban blocks they’re in2. It’s clear that deep retrofit to EnerPHit standard or equivalent throws up a host of issues. To understand and start to resolve these we need built examples.
Ireland’s first certified EnerPHit
My practice recently completed a good example of the issues at the centre of deep retrofitting to a clear standard: a 111 sq m 1950s semi-D in Monkstown, Co Dublin upgraded to the EnerPHit standard, with a 48 sq m extension built to the passive house standard. The building has just been certified Ireland’s first – and the world’s fifth – EnerPHit project. The house’s owner Pauline Conway first approached us because we were the first practice to be accepted into Éasca – an Irish green building association that approves companies with sufficiently strong sustainability credentials. She wanted partners in a plan to make her house an educational tool and an example of genuinely sustainable retrofit. The project started on site in April 2011.
While we knew that achieving this standard would set an important example for ordinary semi-detached houses, we also wanted to promote healthy ventilation, water conservation and low carbon forms of construction, as we strongly believe energy should not be pursued in isolation. Pauline grew up in a remote part of rural Ireland. “Until the age of eight years I lived in a house without piped water,” she says, “where we had to carry buckets of drinking water from a nearby stream and harvest rainwater for laundry”. She therefore gained a keen sense of the importance of natural resources. Later she spent 13 years working in African countries. In Ethiopia she saw at first hand the horrific impact of recurrent droughts which are increasing in frequency due to climate change, largely caused by developed countries. She wanted her home to be an example of genuine sustainability.
The design
Our aim was that from the street the retrofitted, extended semi-detached house would continue to fit into its suburban context, while small elements such as the juliette balcony and anodised rainwater goods would suggest that something special was within. The rear extension is more clearly different as it orientates exactly to south then curves away to frame a dining table within and a deck without.
Sunpipes, roof lights and windows extended downwards to become patio doors, a glass screen between hall and kitchen and an open riser stairs with glass balustrade all contribute to even light distribution throughout the house. All services are clustered in the extension, simplifying services runs. A solar panel faces south west on the rear roof.
The stick built timber frame extension being built
Before and after, values, monitoring
Given the project’s aspirations we established a baseline with a before Building Energy Rating (BER), an airtightness test and thermographic study. Architect Helena McElmeel is carrying out a study pre and post-works as part of the RIAI 3Twenty10 research project. Despite the more than three hundred thousand published BERs there is extraordinarily little known about how Ireland’s dwellings actually perform and are actually used after retrofit.
We established that the initial airtightness of the house was 5.6 air changes per hour at 50 pascals. While this seems an amazing value for an old house, levels close to this may be more common than realised for older buildings that were well built and have not been interfered with. The AVASH study3 of thirty-two social housing dwellings in Leinster established an average airtightness for the existing, untouched housing stock it studied (mostly from the 50s and 60s) of 7.98 ACH, while those that had been retrofitted averaged an appalling 13.3. Heat can be lost quicker through gaps and cracks than in conduction through insulation, especially in windy countries like Ireland, so it’s very important that baseline conditions are understood and improved upon in retrofit work.
The air barrier of the semi-detached house is mostly the original wet plaster. The attic had been very carefully-insulated in the 1980s, with now mostly collapsed mineral wool, and had been carefully re-glazed more recently. Surprisingly, for the airtightness value achieved, the timber floors were suspended: presumably the underlay was thick and dust-filled!
Low carbon and timber
A key low carbon approach in the project was using wood-based products when possible. Using wood in construction ensures that carbon captured through photosynthesis (becoming the very stuff of trees) remains bound-up, and it’s also a great insulant. We love the fact that cellulose insulation was newspapers which had been trees: well-read material saved from burning and landfill. We used 220mm FSC-certified timber studs for the extension’s walls, clad internally with 18mm OSB3 as a racking board and airtightness barrier, and slabbed externally with 80mm thick Diffutherm woodfibre external wall insulation. We then blew cellulose into the resulting cassettes between4. The flat roof was similar except that Gutex woodfibre slabs were used over joists. The main cold roof buildup featured 400mm of cellulose. In all 56 m3 of cellulose and 11 m3 of woodfibre were used.
Higher embodied energy – low carbon response
Before adopting EnerPHit we had intended to insulate under the suspended timber floor in the usual manner for retrofits. In moving to EnerPHit we realised that the resulting U-values wouldn’t be good enough. In any case as the insulation depth increased beyond the joist depth the repeat thermal bridges would get worse. Instead we stripped out the joists and tassel walls, laid a radon barrier on the original subfloor and built up 300mm of EPS300, then poured 150mm of concrete with 70% Ecocem GGBS on top. This gave us a retrofit floor U-value of 0.11 W/m2K.
Clearly the thermal performance and ability to control quality greatly increased, but the amount of floor and sub-floor materials going to landfill also increased because of this decision. We knew the use of low carbon concrete, wood fibre and recycled products would compensate but it is striking that the EPS300 slab insulation had a greater carbon impact than expected. Its density means that the amount of EPS contained is much greater. In subsequent projects it’ll be interesting to see if alternative insulants below slab can improve on that carbon impact, and at a reasonable cost. The embodied carbon of the uPVC window frames is also worth noting.
Figure 1: Embodied carbon in materials used
Figure 1 should only be considered a rough, incomplete estimate of associated CO2 (equivalent) emissions: the impact of the membranes, renders and finishes, for example, are omitted. We deliberately show a few alternatives such as mineral wool in the attic or brick rain screen (highlighted in red) to illustrate how swapping approach and specification can allow an equal or better performance, yet less carbon. We look forward to the imminent publication of SEAI’s embodied energy and carbon measurement methodology and database which should make this kind of analysis, and resulting low carbon-focused specification, more common and more Ireland-specific.
The steel column – a key point thermal bridge
A key technical issue that had to be resolved was how to bring the load of the rear corner of the first storey to ground in a ‘thermal bridge free’ way6 once the ground floor walls were removed to make way for an open plan space below. Figure 2 shows the column, the wall it’s supporting above and the footing below. It also shows how the line of thermal continuity and water management are separated at the rooflight, minimising thermal bridging and airtightness issues there.
Figure 2 – detail showing how the upper floor of house is supported and differentiation of weather barrier and insulation continuity at the roof light
We worked closely with engineers Malone O’Regan to arrive at a final solution featuring an unusually large base plate that transferred a uniformly distributed load of the column onto a 100mm Perinsul Foamglas layer onto a concrete pad. Figure 3 shows an output from a point thermal bridge evaluation using the newly translated Psi-Therm software. Note the temperature at the junction of floor and column (19.36C) is only 0.5 K cooler than the floor elsewhere.
Figure 3 – point thermal bridge analysis of column base plate. χ-value = 0.041 W/K Note: air temp. 20C, ambient ground temp. 10C
Managing airtightness & delivering quality
For this project we ensured that only builders who had built to an n50 of below 2.5 air changes per hour could tender. We provided a detailed airtightness specification, clear red-lined drawings and toolbox talks with technical support from Ecological Building Systems. Prime cost sums were allowed against each of three tests: one just after the air barrier had been formed but before first fix, the second after second fix and the third before practical completion was certified. Signing the latter certificate wascontingent on the builder meeting the design values.
Because the focus on airtightness was consistent and clear, and because the builder was facilitated and supported to reach the value through the support material and process created, there was little wriggle room allowed. It’s critical that builders understand this beforehand, price soberly and put their A-teams forward. Design teams and clients need to judge this equally soberly and recognise that skilled teams and great care on site don’t come with bargain basement tender prices. Perhaps knowing that a project must reach the EnerPHit standard gives all sides support at the critical tendering and contract signing stages.
We realised early on during airtightness tests that there was air leakage through some parts of some of the 18mm OSB3 boards7. To avoid a costly variation to the client if new AVCL membrane and tape were applied to the boards we contacted Remmers, a company that delivers conservation and breathability focused treatments and plasters. They suggested two rollon coats of Induline ZW-400 might improve the airtightness of the boards. We advised the client and agreed to take a gamble on this approach. Airtightness tester Gavin Ó’Sé was able to prove that this improved the airtightness of the boards.
At the first construction stage airtightness test (an n50 of 3.67 ACH) it was clear that Bourke Builders had started to move ahead, slabbing insulated plasterboard at the party wall thermal bridges and first fixing. We instructed them to stop until the design airtightness value was reached. If it’s not reached at this stage, when the layers of buildups and number of penetrations are relatively few and easily accessed, it never will be. Later tests are to ensure the value is maintained. There was clearly a learning curve on the specific difficulties of airtightness in retrofits. Diagnostic airtightness tests were crucial in helping us learn where under-performance was occurring and Bourkes took the appropriate corrective actions. We graduated from whole house testing to room by room testing using our hands, anemometers and smoke. It was only after the fourth construction stage test (an n50 of 1.3 ACH) that we allowed them to proceed to first fix as there were a few areas where improvements could yet be made unhindered by other works. In the end there were seven formal tests during the project and many more informal tests by the foreman using a Wincon fan. Bourkes paid for the additional tests. Their commitment to getting it right was central to the team’s achievement of EnerPHit certification.
Water conservation
Dual flush toilets, low volume bath and bowls and sprinkler taps feature. We also worked closely with Ollan Herr of Reedbeds Ireland on the rainwater harvesting strategy. The location of tank and specification changed more than once but we were committed to a small gravity- fed tank within the building envelope. Herr is critical of the current vogue of overly large tanks buried in gardens requiring pumping over two storeys or more.
Located in an upper press of a walk-in-wardrobe, the system at Wynberg Park serves an outside tap and two toilet cisterns only. An outside leaf filter and two fine filters inside ensure the water is fit for purpose. Toilet usage typically comprises about 35% of a person’s daily water demand. By focusing on supplying water for this function the size of the tank could be reduced to 450 litres, cutting out the need for electrically powered UV filtration. Locating the tank below gutter level but above toilet cistern height meant the system could be gravity fed. Because the tank’s inside the house it requires no insulation. By using a simple water trap the supply is airtight. Finally fail-safe measures ensure the tank never overfills or empties. We liked the simplicity and technical elegance of this approach.
Moving forward
This project contained a range of innovations from timber frame wall system to overall performance specification, to rainwater harvesting approach. There was lots of learning – some through mistakes. The team got a number of things – such as meeting the EnerPHit standard – right and can prove it. That itself is a great message for building in Ireland.
The industry needs many more example cases of deep retrofit to a clear standard. All relevant bodies need to actively explore the challenges of deep retrofit and community scale retrofits, and then engage with others in transforming the construction industry. If we’re serious about the 2050 targets, about reducing our oil and gas dependency and about genuine sustainability, we need to make significant changes in focus, policy and building culture in the next two years.
An extended version of this article is available from the author
Selected project details
Client: Pauline Conway
Architect: Joseph Little Architects
Passive house consultant & BER assessor: Ann-Marie Fallon
Civil / structural engineers: Malone O'Regan
Quantity surveyors: Walsh Associates
Main contractor & timber frame:Bourke Builders Ltd
Airtightness tester: Greenbuild
GGBS cement: Ecocem Ireland
EPS 300: Kingspan Aerobord
Thermal breaks:Thermal Insulation Distributors Ltd
OSB3 board: Coillte
Breathable sealing coat for OSB3: Remmers
Blown cellulose: Ecological Building Systems
Cellulose installation: Clioma House
External wall insulation system: Baumit
Diffutherm external wall insulation: Natural Building Technologies
Brick slips: Ibstock Brick (Ireland)
Windows & doors: Munster Joinery
Airtightness products: Ecological Building Systems
Gutex woodfibre insulation:Ecological Building Systems
Roof windows: Velux
Sun pipes: Fakro
Solar thermal supplier: Kingspan Renewables
Heat recovery ventilation: Pure Renewable Energy
Rainwater harvesting: Reedbeds Ireland
Flow Limiters: Armitage Shanks
Water conserving sanitaryware:Sandringham Fittings
1 The Retrofit Challenge: Delivering Low Carbon Buildings, from Centre for Low Carbon Future and Energy Saving Trust, 2011. Available at http://www.energysavingtrust.org.uk
2 Several EU-funded projects have focused on exactly this, e.g. 3Encult, Susref and Refurban.
3 AVASH stands for Advanced Ventilation Approaches for Social Housing. DW EcoCo were the Irish partners of the three country project that ended in 2008. Papers can be found at www.brighton.ac.uk/avash/
4 This is very different to the poor practice of slabbing EPS insulation outside timber frame which has caused failures in Canada and Sweden. The BBA-approved Diffutherm system for timber frame has been extensively tested and simulated for use throughout the UK. We believe this is the first time it’s been used in Ireland.
5 Green bars show materials used, red bars show materials and emissions avoided. Concrete values came from Ecocem Ireland Ltd, woodfibre values came from Natural Building Technologies. All other values taken from Ökobilanzdaten im Baubereich 2009/1 jointly researched and published in Switzerland by KBOB, Eco Bau and IPB: www.kbob.ch
6 As the Passive House Institute and indeed many EU member states measure buildings from the outside, a junction that they consider ‘thermal bridge free’ (i.e. (0.01 W/mK) may have a higher value when measured from the inside as per UK and Irish regulatory standards
7 KU Leuven has carried out an interesting study on the airtightness of OSB boards from eight different manufacturers. They found that even within the same brand variation in airtightness can occur. It appears that even 18mm OSB3 cannot be expected to act as an air barrier at these design values.
Additional info
Building type: 1960s semi-detached dwelling. EnerPHit retrofit to existing and passive house extension to side and rear.
Location: Wynberg Park, Monkstown, Co Dublin
Completion date: April 2012
Budget: €240k
EnerPHit certification: Certified
Building Energy Rating (BER) Before: G (494.88 kWh/m2/yr) After: A3 (51.19 kWh/m2/yr)
Space heating demand (PHPP) Before: n/a After: 17 kWh/m2/yr
Heat load (PHPP) Before: n/a After: 12 W/m2
Primary energy demand (PHPP) Before: n/a After: 109 kWh/m2/yr
Airtightness (at 50 Pascals) Before: 5.66 ACH After: 0.93 ACH
Original walls: Rendered 215mm concrete hollow block wall. On ground floor (front elevation only) uninsulated cavity wall with exposed brick. All internally plastered. Average U-value: 2.40 W/m2K
Retrofitted walls: Mineral render finish on 150mm Baumit Platinum EPS EWI on existing. On front ground floor cut-down brick slips to match existing brick over external wall insulation & cavity filled with platinum bonded blown bead. Renovated and extended existing wet plaster finish used as main air barrier. In rooms adjoining party wall 50mm insulated plasterboard internal wall insulation used additionally to minimise thermal bridging. Average U-value: 0.13 W/m2K
Extension walls: External render, on 80mm Diffutherm woodfibre EWI with mineral render, on 220mm open panel timber frame filled with cellulose, on 18mm OSB-3 board, on 50mm Thermafleece PB20 sheepswool service cavity, on plasterboard. Taped OSB-3 used as main AVCL. U-value: 0.12 W/m2K
Original roof: Pitched cold roof with 100mm mineral wool insulation between joists. U-value: 0.40 W/m2K
Retrofitted roof: 350mm cellulose blown between and over joists, on Intello membrane AVCL, on plasterboard. U-value: 0.10 W/m2K
Extension pitched roof: Pitched roof as per retrofitted roof.
Extension flat roof: Double butyl membrane on double layer of marine plywood, on 50mm ventilated air gap, on Solitex membrane, on 24mm Gutex woodfibre sheathing board, on 250mm timber joists filled with cellulose, on 18mm OSB-3 board, on Intello membrane AVCL, on 50mm insulated service cavity, on plasterboard. U-value: 0.13 W/m2K
Original ground floor: Uninsulated suspended timber floor over ventilated undercroft with tassel walls and sub-slab
Retrofitted ground floor: Existing sub-slab under 300mm Aerobord EPS 300, under 150mm concrete slab with 70% GGBS. U-value: 0.11 W/m2K
Extension floor: Clause 804 aggregate with radon sumps under, radon barrier under, 400mm Aerobord EPS 300, under 150mm concrete slab. U-value: 0.08 W/m2K
Original windows & doors: double-glazed, air-filled PVC windows and doors to most of house. U-value: ~ 2.80 W/m2K
New triple-glazed windows and doors: Munster Joinery triple-glazed Future Proof uPVC sash windows. U-value: 0.80 W/m2K
Roof windows: Velux GGL/GGU thermally broken triple-glazed roof windows with thermally broken timber frames. U-value: 1.9 W/m2K
Space heating & hot water system
Before: 20 year old oil boiler (circa 70% efficient) serving radiators in every room and two open fires. After: The primary heating involves post-heating the HRV supply air. A 12kW modulating gas boiler providing back-up heat to a network of three small radiators, and two towel radiators zoned separately due to daily use. A 3.2m2 Kingspan Thermomax HP 200 3M2 evacuated tube array on main rear roof facing south-west supplies hot water to a 300L 100mm factory-insulated cylinder (with triple coil allowing additional future heat source). A 12kW modulating gas boiler supplies the shortfall.
Ventilation
Before: rapid ventilation supplied by windows, no trickle vents, extract via pull chord unit in kitchen and chimney in living room After: Paul Novus 300 VL (Passivhaus certified) HRV system, with recovery rate of 92.4% as installed. Primary air ducts are limited to 0.5m long with 100mm insulation