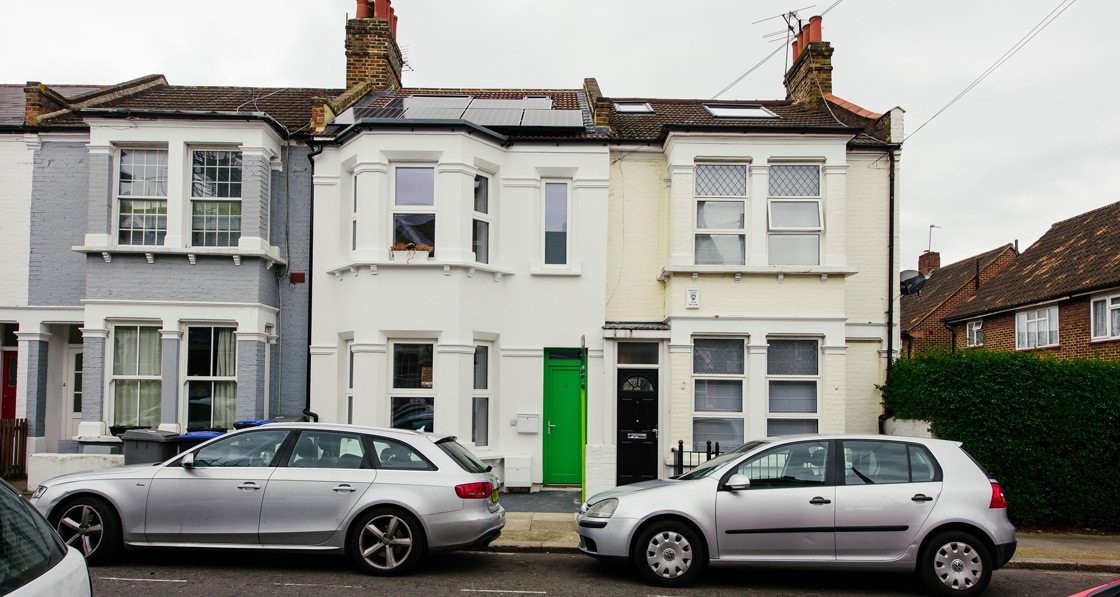
- Upgrade
- Posted
Sensitive passive retrofit transforms Victorian North London home
Upgrading a historic home to the passive house standard typically means leaving the façade untouched to preserve the building’s historic appearance, but the team behind this fully passive retrofit in Kensal Green took a totally different approach.
Click here for project specs and suppliers
This article was originally published in issue 17 of Passive House Plus magazine. Want immediate access to all back issues and exclusive extra content? Click here to subscribe for as little as €10, or click here to receive the next issue free of charge
In an ordinary street in an ordinary part of north-west London, stands a very ordinary-looking Victorian terraced house, one of thousands like it.
Except it is not ordinary at all. In fact, thanks to an epic retrofit to full passive house standard, it is one of the most energy efficient houses in London – and probably one of the most energy efficient Victorian houses in the country. The impetus for the project was the vision of the property owner, Peter Land. He planned to sell the house, but before he did so, wanted to make the house as energy efficient as possible.
“As an environmental scientist I am acutely aware of the need to reduce carbon emissions, so I feel I have a responsibility to cut the emissions from any property I have an influence over,” he explained.
“It made financial sense to do up the house before selling it. Because of the way London house prices have changed I realised that I could justify spending quite a bit on the improvements, and still recoup that in the increased market value. Hopefully I would effectively be able to achieve a ‘free’ low energy retrofit – and feel happy that I had done the right thing with the property.”
The original plan was to retrofit to the Enerphit standard, “but as I was going to have to borrow money anyway to get to Enerphit, I thought ‘in for a penny, in for a pound’ — why not go the extra distance and go for full passive house.” Peter admits that he “slightly naively” hoped full passive house certification would add a premium to the sales price as well.
He brought in architects Eco Design Consultants and contractor Bow Tie Construction, who advised him that though Enerphit would undoubtedly be simpler, passive house would be achievable too.
As a mid-terrace dwelling the form factor for the house is relatively good, though rear and loft extensions mean it is closer to 2.3 than the 1.7 that you might get with the simplest terrace form. However, there were significant losses through the thermal bridging and the glazing.
As is inevitable in a retrofit, thermal bridges were significant but again relatively fixed as they form the structure. Extensive analysis also confirmed that the floor junctions and party wall connections in particular contributed significant thermal bridging losses.
In a retrofit like this, the glazing openings are also relatively fixed, especially to the front.
To the rear, north-facing window openings were to be retained to bring light into the back of a deep kitchen. The kitchen also sports east-facing floor-to-ceiling double glass doors, seemingly de rigeur in a London retrofit (and unquestionably very nice to have) but expensive both in terms of cash and energy losses.
The orientation and fixed window opening sizes, plus shading from neighbouring buildings, meant that little solar gain would be available to balance heat losses. Internal gains were limited too for the purposes of PHPP calculation.
“The house was modeled and certified under PHPP version 8. For a house of 110m2, PHPP assumes an occupancy of 3.2, but for a four-bedroom house this may be an underestimate,” Patrick Osborne of Eco Design explained. Nonetheless the calculations allowed some useful heat from internal gains. Taking all of these factors together, very low U-values needed to be achieved in the walls, floor and roof in order to reach the passive house standard.
However to begin with, the planners said that external insulation would not be permitted. The team then explored the option of rebuilding the front wall with external wall insulation, but set back to retain the original line of the façade – which would have been difficult and expensive. But as Peter Land explained: “The architect would not take no for an answer and after some digging around confirmed that what the planners were saying was not a good interpretation of the planning laws.”
The team went back to the local authority and the external wall insulation was clarified as a ‘permitted development’. Peter Land said: ““In the end the local authority was happy to agree to the plans, even though we were adding an unusually thick layer of insulation, provided the appearance was maintained. I’m very proud of the precedent we set for the area.”
The choice between internal and external insulation, “was a combination of the building fabric issues, such as the moisture risks with internal wall insulation [IWI] if we were to insulate to the required levels, and the reduction in useful floor area with IWI,” Patrick Osborne explained. “Given that we could get a better U-value with external wall insulation, plus the fact that there would be no decrease in space —which would affect the property value — it made sense to pursue this option.”
Nonetheless, given the very low wall U-values required (around 0.08W/m2K) in order for the house to meet passive house, insulating externally was not easy — 250mm of external wall insulation (EWI) was needed, which Bow Tie managing director Rafael Delimata described as a “builder’s nightmare” to install. The fixings into the existing structure were very difficult given the depth of the insulation, and the fact that to reach that depth three layers of board were needed. Fixing the insulation around the two-storey bay window at the front of the house was a particular challenge.
As Rafael Delimata explained, there were also difficulties in sourcing the right components: “We could not use standard anchors because the EWI was so thick, so we had to source specialist longer ones.”
Specially constructed airtight ply boxes were installed to receive the new windows, and also allow for preliminary airtightness testing to more accurately reveal air leakages elsewhere in the house
Airtightness detailing around windows
Fixing the external insulation around the two-storey bay window at the front of the house was a particular challenge.
“A risk we always highlight with projects going for an extremely high specification is the need to source specialist components. These often involve long lead times – then sequencing can start to go wrong. When subcontractors get held up because something has not arrived, they get very fed up.”
The experience highlighted the importance of close collaboration between builder and designer. Where possible, Rafael Delimata says, Bow Tie try to persuade designers to stick to standard components and tried and tested techniques, as this reduces the risk of unforeseen delays and extra expense. “Working through these issues with the contractor is important, so in future projects we would ensure that we go through this process thoroughly,” Patrick Osborne added.
The EWI at the front was finished with render, and the string courses were replaced using Sytex profiles, matched to the profiles of the originals. Patrick Osborne was happy with how it turned out. “It was quite easy to do and we think it has given a great end result,” he said.
Insulation elsewhere in the building was not as technically challenging – but it was certainly thorough. For example, unusually for a retrofit with external insulation, the window reveals were also insulated internally. With EWI there should be no issues with cold internal surfaces, but in order to pare a little more off the heat losses through the window frames, a layer of insulation was added to the internal reveals, butted up to the inside of the frames.
(clockwise from top left) the ground floor was excavated and rigid insulation placed around the perimeter to cut thermal bridging here; airtightness taping around joist ends; new roof rafters insulated with Icynene spray foam insulation; airtightness detailing to the roof, with Pro Clima Intello membrane under internal battening.
At loft level, party walls were insulated (internally, obviously!), as they adjoin an unoccupied, unheated space. Party wall returns were also internally insulated to one metre, to tackle the thermal bridging at the junction.
The roof too achieved a very low U-value of below 0.1 W/m2K. New 150mm roof rafters were insulated with Icynene spray foam insulation, with 120mm insulation boards above. “Rafael installs the spray foam, and I was impressed with the continuity – with boards there is a risk of gaps and then air movement, so this should represent an improvement in actual building performance,” said Patrick Osborne.
With most of the fabric having external insulation, moisture was not as much of a concern as it can sometimes be in the retrofit of old buildings. The fabric was also, happily, already very dry. “There were no signs of moisture in the fabric of the existing building, although there was some mould in the bathrooms caused by poor ventilation. We felt that as the majority of the insulation was external, and outside the airtightness line, the moisture risks due to interstitial condensation would be reduced,” Patrick Osborne explained.
Nonetheless care had to be taken, particularly with the loft space. Because this had internal insulation, the U-values couldn’t be quite as ambitious as the externally insulated walls, in order to prevent the risk of interstitial condensation on cold masonry. The insulation here was also lined with a Pro Clima Intello vapour control membrane, Patrick Osborne timber as best as we can, given that moisture from construction could adversely affect it.”
The flat roof to the back extension potentially presented a tricky thermal bridge, because of the need to fix a gutter to a corner that was externally insulated, down the wall and across the roof. Contractor Bow Tie however came up with a solution. “Rather than inserting a timber, which would have created a thermal bridge, we bonded ply to the insulation with adhesive, to make what was in effect an on-site constructed SIP. This was able to support the necessary edging and guttering – and is something our roofer already knew how to do,” Rafael said.
The floor was excavated to the (somewhat shallow) foundation level, insulated with 300mm of Ecotherm PIR insulation laid on a damp proof membrane, and topped with a polished concrete slab holding the underfloor heating pipes. The thermal bridging from the ground where the walls ‘bypassed’ the floor insulation was ameliorated by adding insulation at the base of the walls to form oversized skirting boards, lengthening the cold bridge path though the brickwork as much as possible to minimise heat loss.
Airtightness strategy
Achieving passive house airtightness is a huge challenge for any retrofit, and even more so when, as in this case, the structure is shared with neighbouring buildings.
It helps a great deal to identify the main air leakage paths as early as possible in the project, so that the most effective airtightness strategy can be built in from the start. The air leakage paths need a pressure test to identify them, but when air testing in a Victorian building like this, fabric leakage may be overshadowed by losses through the windows and sash boxes, making it harder to spot the other issues.
Bow Tie’s solution to this was to remove the old windows early in the job, and build and make airtight plywood boxes for the new windows. “Once windows have been sized up, we construct ply boxes to receive the new windows, and make them airtight. We parge around them, and at the front we close them with ply for security, sealed with silicone, at the rear we put in polythene to admit some light – and seal that too,” Rafael explained.
“This then enables us to do some preliminary air-testing. We rent a fan for a couple of weeks and use our own smoke machine – the same kind that is used for discos! At this stage it isn’t about getting an expert measurement, it’s about finding out where the leaks are.”
These tests showed leaks in the plaster, the joints between old and newer parts of the structure, and in particular, through the party walls. “This told us that with an external airtightness strategy there was no chance of meeting the passive house airtightness level – and even Enerphit could not be guaranteed, so the strategy was changed to use an internal air barrier.”
Because the air barrier was internal, great care had to be taken with the junctions where internal structures joined the walls: such as the floor joists and staircase. Where individual timbers penetrate the masonry they were taped and the sealed into the parge coat. With the staircase, the entire structure was sealed to the wall with a structural grout, then parged. Although it required a bit of careful work, being able to do this also enabled the team to retain an attractive Victorian feature.
Overheating risk
Although the building is shaded both by surrounding buildings and by the 250mm window reveals, overheating risk was still a concern, especially in the light of the east/west orientation and the tall glass double-doors at the back. However modeling showed that even using very conservative assumptions, based on natural ventilation alone, the overheating stayed below the 10% of hours over 25C required for passive house certification.
Patrick Osborne explained: “The Paul Focus 200 does have a summer ventilation setting, but not a full bypass, and as there is no provision for this mode in PHPP, the overheating calculations were based on natural purge ventilation through the windows and top floor rooflights.
“We were careful with our assumptions, basing them on restricted hours of window opening, and overnight opening only of those windows that could be opened securely — for example, not those above a flat roof.
“On this basis the hours over 25C did come close to the 10% allowed. In practice however, more flexible window opening and the summer ventilation setting of the MVHR should make the performance better.”
Passive house vs Enerphit
The project had an overall budget of £230,000, which works out around £2,000 per square metre. Although it would doubtless have been out of the question on this site, Patrick Osborne agrees that a new build passive house – fitted out to a similar standard — would not necessarily have cost more, and might even have cost less.
But aiming to upgrade to Enerphit rather than full passive house would certainly have been cheaper and simpler, while still offering a great improvement over the existing building, he says. It would also have been easier to achieve, given the slightly less exacting airtightness requirements, and the likelihood that a more standard specification for insulation would have been feasible.
Rafael Delimata agreed: “The client would have been better off in terms of money and time spent on the project had they opted for Enerphit, but they wanted to go full passive house, so we were determined to help them achieve that, and we did.
Although Peter Land’s original hopes of securing a passive house retrofit “for free” were disappointed, he is extremely proud of what he, Eco Design and Bow Tie Construction achieved. “We have created something magnificent,” he says.
As well as giving a young family a supremely comfortable home that will greatly reduce their carbon footprint, there are much wider lessons to be shared from this project – including from what did not go exactly as planned.
The project gave the team valuable insight into the relative difficulties and financial implications of achieving Enerphit versus full passive house. “Learning from this project, it will be easier to compare the two standards for future projects and give options,” Patrick Osborne believes.
He goes on: “There was nothing technically insuperable about achieving passive house standard on this retrofit, using knowledge, materials, and techniques that are available now. The key part of the equation missing for retrofitting large numbers of these quite common Victorian terraces, is the finance mechanism.
“The Green Deal helped fund this retrofit, but with the Green Deal now cut, and the mooted changes to reduced rate VAT for energy efficiency measures, this becomes more difficult.”
From a financial and a technical point of view, deep retrofit like this could come down in cost with a street-at-a-time approach. As Patrick Osborne pointed out, “if the whole terrace had been retrofitted, the task would have been very different, and potentially a lot easier.”
With everything in the UK up in the air after the EU referendum, it is hard to know what support for retrofit might be available in future. However, Peter Bonfield, who is advising the UK government on retrofit policy, has been clear about the need for more careful design, and better construction standards.
Projects like this are building an invaluable bank of knowledge – at the design stage, where calculation gives insights that could be shared across so many similar buildings, and on site, in the meticulous attention to detail that demonstrates how care and attention can bring about a leap in the performance of the finished building. Projects like this show that occupants of a typical Victorian terrace house can enjoy every bit as much comfort you’d expect in a brand new 21st century passive house.
Selected project details
Client: Peter Land
Architect, energy consultants & project management: Eco Design Consultants
Contractor, M&E engineering: Bow Tie Construction
Structural engineering: Watson Hallam Structural Engineers
Project management: Eco Design Consultants
Passive house certifier: Warm
MVHR + windows & doors: Green Building Store
Airtightness testing: Aldas
External insulation contractor: Make My Home Green
Phenolic insulation: Kingspan Insulation UK
Airtightness products: Ecological Building Systems, via PYC Systems
Roof & floor insulation: IBB
Wastewater heat recovery: Recoup
Roof windows: Fakro
Heating controls: Heatmiser
Lighting: Arrow Electrical
Additional info
Building type: 111 sq metre terraced Victorian brick townhouse
Location: Kensal Green, London
Completion date: April 2016
Budget: £230,000 inc VAT
Passive house certification: Certified
Before (estimated): 363kWh/m2K
After: 15 kWh/m2/yr
Heat load (PHPP):
Before: 126 W/m2
After: 15 W/m2
Primary energy (PHPP): 106 kWh/m2/yr
Airtightness (at 50 Pascals): 0.54 ACH
Thermal bridging: Party wall returns with insulation to 1m, and internal walls with insulated skirting board details. All thermal bridges individually calculated to provide psi values for PHPP calculation
GROUND FLOOR
Before: Uninsulated 100mm concrete slab to kitchen. U-Value: 4.64 W/m2K. Front rooms and corridor uninsulated suspended timber floors. U Value: 4.33 W/m2K
After: Insulated concrete slab with 300mm Ecotherm PIR. U-value: 0.075 W/m2K
WALLS
Before: Double-brick 215mm solid wall. U-value: 2.14 W/m2K
After: Existing solid brick wall with 250mm Kingspan Kooltherm K5 rigid phenolic insulation and render finish. U-value: 0.077 W/m2K
ROOF
Before: 100mm rafters to pitched and flat roof sections, both with 50mm EPS insulation. U-value: 0.68 W/m2K
After: New 150mm roof rafters were insulated with Icynene spray-foam insulation, and 120mm Ecotherm Eco Versal rigid PIR insulation above, with 50 x 25mm battens and tiles over. U-value: 0.097 W/m2K
WINDOWS
Before: Mix of single-glazed windows at back and poor performance aluminium double-glazed front units. Double glazing assumed with Ug value: 2.9W/m2K, Uf value: 2.2W/m2K
After: Green Building Store Ultra passive house certified triple-glazed windows, with glazing U-value of 0.65 W/m2K and a frame value of 0.84 W/m2K
Heating system: Fully designed and commissioned by Bow Tie Construction’s M&E division. The existing Greenstar boiler was kept and relocated, connecting to a new underfloor heating system on the ground floor, and radiators for the first and second. Recoup PIPE+ HE wastewater heat recovery system fitted to shower
Ventilation: Paul Focus 200 MVHR unit supplied by the Green Building Store, certified efficiency of 91%
Electricity: 4kWp solar PV array
Image gallery
Passive House Plus digital subscribers can view an exclusive image gallery for this article