- Design Approaches
- Posted
In Transit
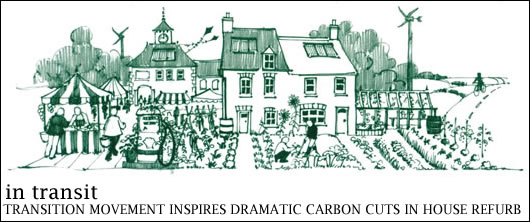
The Transition Towns movement has recently come to the fore as a model for sustainable development, with communities around the world signing up to reduce carbon emissions and build resilience in a world where climate change and energy security are emerging as real threats. Leading eco designer Joseph Little of Joseph Little Architects describes how the recent refurbishment and extension of a Dublin house addresses many of the movement’s concerns.
It’s probably fair to say that one of the fastest growing movements in the world today is the ‘Transition Towns’ network.
Drawing on the ‘Energy Descent Action Plan’ he developed at Kinsale, Rob Hopkins and his team launched Transition Town Totnes (in the UK) one and a half years ago. There are now 64 recognised transition communities and 600 other groups (and counting) are in communication with Rob’s team to launch their versions of this initiative in their communities worldwide.1 The Transition Ireland Network is coordinated by Davie Philip of Cultivate and several transition initiatives are underway here.2
Davie says the movement is growing so fast because it’s growing in a void. As a society we are all increasingly aware of the bad news about climate change and peak oil, but much of the resilience of our communities to deal with this (for instance local food production and self-help skills) has been dismantled. The Transition movement provides a loose framework and support to help people re-build communities and face these issues together through positive action.
As Rob says: “if we plan and act early enough, and use our creativity and cooperation to unleash the genius within our local communities, then we can build a future that could be far more fulfilling and enriching, more connected and more gentle on the earth than the lifestyles we have today”.
The key ‘mantra’ at the centre of the Transition movement is that from now on everything we do must be rooted in two things: reducing carbon and building resilience. Just think how many actions, how many decisions of ours will change when we each, and collectively, apply those standards.
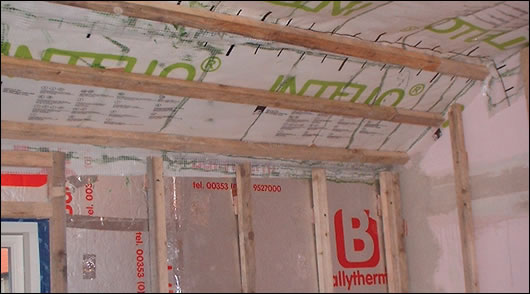
Dry-lining and air-tightness measures to improve the existing house
A ‘Transition’ home specification
While the Transition movement is fundamentally about people, their
actions, relationships and core beliefs, it of course spills into the
world they need to create. What would a Transition home, new build or
refurb-extension, look like? The four headings below are this author’s
attempt to prioritise the key decisions from a Transition point of
view. The reasons extend far beyond those listed here.
1) Live close, commute less
a) We need to build or buy close to a community and, if possible, close to where we work. This is important for so many reasons: for the financial and social viability of the community, to maximise family time and to allow time to partake in community, to reduce urban sprawl and commuting.
b) We need to reduce the amount of time in the car (particularly to work but also to shop or school). The shocking thing is that if you choose to live where you can’t avail of public transport and are too far to cycle comfortably to key community facilities, you are committing yourself to a high carbon lifestyle and increasingly high fuel costs in the future, regardless of whatever other steps you take listed below.
c) A recent study the author conducted exemplified this. The annual commute to work in two cars (excluding social or shopping expeditions) by a couple from their new low-energy house generated 7.7 tons of CO2 - more than twice the national average. It was also twice the CO2 emitted for space heating and hot water in their low energy house. So, in this case, low energy house: high carbon lifestyle.
2) Reduce the building’s energy requirement & carbon penalty
a) See if you really need all that space! If you can make each room of your new build or extension 10 per cent smaller the impact on your construction budget, on your later fuel bill and on the environment will be equally reduced. You probably won’t even notice the difference spatially. It goes without saying that an ensuite for every bed room is profligate.
b) From July 2008 thermal peformance standards are rising by 40 per cent and a minimum airtightness level will be mandatory. It’s expected that the next upgrade to Part F will effectively eliminate undesigned ventilation. As there are more and more architects and builders experienced in this way of constructing and the systems are multiplying, this is becoming easier.
c) Design with an awareness of solar orientation. A good distribution of windows and rooflights will ensure artificial lights are unused during the day. A majority of windows facing south and as few as possible on the north side will help capture free heat from the sun. Some thermal mass where the sun shines most frequently will help store some of that heat for later, evening out the diurnal cycle.
d) Install 100 per cent long-life, low energy bulbs. Try to eliminate use of standby power: there are more and more intelligent controls to help with this. Replace white goods at the end of their natural life with the highest rated appliances possible (note: A++ appliances are available). Use hot-fill washing machines fed from the water heated by the solar array: less work for the boiler to do.
e) One UK water company (SWW) states that treated water generates 177g of CO2 per 1000 litres used and sewage (flushed using that same drinking water) generates another 322g per 1000 litres. The cost of this won’t hit household pockets till rates are introduced but the wastefulness and carbon impact should effect our decisions now. Avoiding power showers, fitting aerated taps and installing a rainwater harvesting tank should save several tons of carbon a year. Rainwater harvesting doesn’t need to involve expensive pumps and underground chambers. My practice recently specified a 555 litre above ground Titan Aqua tank costing e272 including diverter kit. It simply links to an existing downpipe.
3) Use carbon neutral fuels and/or install on-site energy generation
a) Wood pellet-fired central heating system: a 12.5kW boiler should be sufficient in a low energy house (note: pellet storage using a hopper is advisable for cost effectiveness). The full package can range from e5K – e15K.
b) A 2 kWp photovoltaic array can generate circa 1600kWh of carbon-free electricity per year. This is twice the new (TGD L) renewable energy requirement for a 200m2 house. We have been informed that installing less than this amount of PVs is not economically viable. While this array would cost about e16K to install it could generate 50-70 per cent of all electricity required (for a house with 100 per cent low energy light bulbs and conscientious owners). In carbon terms offsetting electricity is more important than offsetting oil or gas (through use of solar hot water panels), because of the transmission losses, the inefficiencies of power stations and the fuels used (including coal).
c) A 4m2 evacuated tube solar array with 300L cylinder should supply 100 per cent of hot water in summer and circa 40 per cent in winter. Nutech Renewables install a clever system including whole house heat recovery for about e13.5K. The solar array is used as a ‘solar assist’ to heat the house’s air rather than water in winter thereby increasing the array’s efficiency and halving payback time. We used this specification in the study house.
4) Choose construction materials that have a lower carbon impact
a) Use materials the production of which uses as little carbon as possible. Hemp-lime timber frame, hemp wool and blown cellulose insulations are good examples of this.
b) Where you believe you can’t replace the material find out how to use less! Using 70 percent GGBS in the cement is a good example of this. We do believe there are viable options for cement-free, even concrete-free floors for typical low-rise buildings.
c) Build with local materials whenever possible: reduce the transport miles. Where you have already dealt with the two issues above this is the next in line. For now we are content to use a form of hemp-lime bio composite called Tradical Hemcrete brought in from the UK as the best way of assuring quality in a relatively new building product. In time we would like to see the volume of hemp growing in Ireland increasing and lime kilns re-opening so that a similar quality can be manufactured in Ireland.
d) Underwrite, stimulate or change local industry to suit a low carbon future! Talk about it, ask about it, order it. Put your money where your mouth is and change will occur.
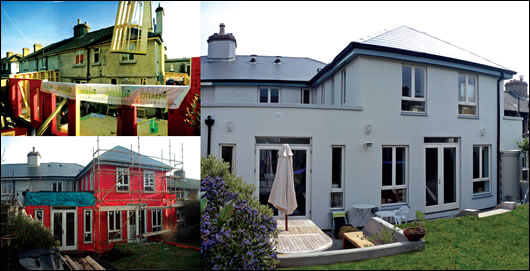
Figure 1: Views of the study house before, during and after
A low energy, low carbon case study
Joseph Little Architects recently completed the refurbishment of a 110m2 house from 1929 on the Malahide Road, Dublin and extended it by 105m2. We had several aims, broadly following the four lists above. They included creating (& upgrading to) a low energy enclosure, a high level of air-tightness and reducing carbon. Good light distribution, heat recovery ventilation, solar arrays and rainwater harvesting are all important features of the design.
An airtightness level of 3.25 m3/hr/m2 was measured in the blower door
test of the completed house. We estimate this will drop to 3.0 when
leaky gaskets in the new Scandinavian pine windows get replaced. This
is an excellent value for a refurb-extension and would be considered
best practice for a new build.
Using the DEAP software we calculated that the energy consumed (as
defined by DEAP) will be 82.00 kWh/m2 per year: this gives a building
energy rating in the upper regions of B1. It also calculates the
typical CO2 emissions as 2.62 tons per year or 14.1 kilograms per m2
per year. Finally we specified 70 per cent GGBS (from Ecocem) for the
floor slab at no extra cost. This specification offsets about 8.5 tons
of CO2 that would have been emitted using OPC cement. Ecocem state this
is equivalent to taking two cars off the road for a year or saving 2.4
years of electricity in the average house. Perhaps more to the point it
negates the carbon impact of 3.2 years of typical energy use in the
study house itself (as calculated by DEAP).
We now wish to focus on the walls of the extension to illustrate how design decisions can change when reducing carbon is fundamental.
The timber frame
Firstly, we chose timber frame over blockwork construction. We know timber frame is from a renewable resource and has lower CO2 emissions than the leading alternative wall construction, concrete block.3, 4 We also know it’s faster to erect. But it has another great advantage: because insulation can be packed into its entire depth we can use lower performing natural insulants that also have a lower embodied energy and lower carbon penalty and still create a high performing wall. We used 220mm x 44mm studs at 400mm centres, which are unusually deep, specifically to increase the insulation levels.
This author believes there is a large potential in the market for timber frame companies wishing to add value to their product by not only erecting the frame and fixing the sheathing board, but also installing the vapour control layer (VCL) on the room side (see item 9 on figure 2) and then blowing cellulose insulation into the void between the studs through neat holes made in the VCL. Architects and builders are always looking for clear lines of demarcation between trades: this increases the value of the framer’s package and gives just such a clean line. In this project Clarke Homes (an ITFMA member) erected the timber frame and Conor McManus of Greentek acted as their subcontractor installing the cellulose insulation and VCL membrane.
Depending on who supplies it, the blown cellulose insulation available in Ireland is either made from Irish newspapers in Ireland or made in Wales from Irish newspapers. It deals with moisture better than rockwool or glasswool and when blown into a confined space can have greater density thus a higher U-value and a reasonably high thermal mass. Finally it’s also comparable in price with those quilt insulants. The insulation we used for the services zone (inside the VCL) is hemp wool. Again it deals with moisture well, doesn’t collapse as some quilt insulants can over time and can be friction-fitted between battens and around service runs.
The services zone, VCL and sheathing board
The creation of a service zone between VCL membrane and plasterboard finish should mean that the former is protected. A ‘no-fault’ policy during construction can help ensure the membrane remains untorn. We used the Intello VCL membrane from Ecological Building Systems. This comes with a 60-year Irish Agrèment certificate and is far more sophisticated in its molecular makeup than a polythene sheet. The downloadable Agrèment certificate itself is a valuable education document showing many key details in 3D. Note the dashed red line in figure 2: if the designer can’t track the air-tightness line the whole way around every detail then they have thought fully about air-tightness!
The centres that the counter battens of the service zone are at can
have a big effect. This is because blown cellulose insulation can fill
the void between studs till it distorts the VCL membrane. While this
means more insulation, if it happens it also means that the
hempwool/services zone gets narrower. One result can be that the
hempwool can’t be used or that fixings of the plasterboard sheets can
be put under pressure from behind. It therefore makes a lot of sense to
fix horizontal counter battens at not more than 400mm centres. Another
clever thing to do is to install a horizontal picture rail running
around the room within the services zone.
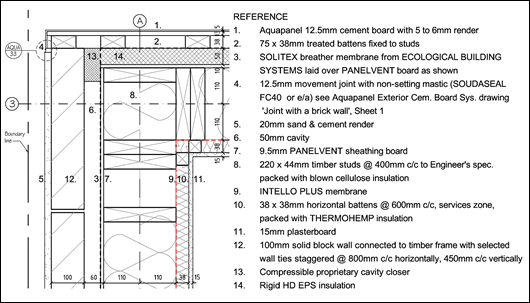
Figure 2: Plan detail of corner of timber frame extension of the study house
Outside the timber studs we used Panelvent as the sheathing board (see item 7 in figure 2). This is because we are very concerned about the vapour resistivity of sheathing boards. It’s very important that materials become more vapour permeable as one moves out through a timber frame wall build-up: this is to ensure vapour that has the potential to condense at one point will instead continue moving out. Trapped vapour can lead to timber decay in the worst cases. Panelvent’s manufacturer states it’s 5.8 times more permeable than ‘Sterling’ OSB3 board and about 11 times more permeable than most other OSB3 boards, but no less strong. The latter boards have a vapour resistivity of around 100 - 300MNs/gm. Given that plywood and some cheap OSB boards can have a vapour resistivity ten or twenty times worse again it is clear architects and timber frame specifiers need to look for and be focused on these figures just as much as on U-values or racking strength.
Beyond the sheathing board
One unusual feature of the walls facing the street and garden is that we used EPS insulation outside the sheathing board (see item 14 in Figure 2). This was because those elevations have a high percentage of opes (see Figure 1) and therefore a greater than normal thermal fraction – in other words repeating thermal bridges. This is because of studs occurring at closer centres around corners, window opes and so on. The EPS insulation thus makes the studs ‘warm’. While EPS is significantly more vapour permeable than other oil-based insulants, an improvement for the next project is to use fibreboard there. The latter has a lower embodied energy and is far more vapour permeable. For those interested in learning more about vapour permeability and good construction we have made a paper by Neil May of NBT 5 available for download on www.josephlittlearchitects.com.
The function of an outer leaf (if it need be said) is to be a long-lasting, robust surface, protecting the wall build-up behind it, creating a vented cavity between and taking a nice finish. In an Irish timber frame house this tends to be blockwork or brickwork. It needn’t be. The Aquapanel building system uses cementitious boards, meshes, tapes, renders and battens to create a vented cavity and an outer leaf with 60-year Agrèment certificate. In this project we choose to use blockwork outer leafs on party walls of the extension and Aquapanel front and back, and at first floor levels. The use of blockwork was specifically because of the risk of a future neighbour erecting a lean-to shed!
There were therefore three slightly different wall build-ups in the extension: timber frame with Aquapanel outer leaf, timber frame (EPS) with Aquapanel, and timber frame with blockwork outer leaf. The U-values achieved were 0.23 W/m2K, 0.17 W/m2K and 0.22 W/m2K respectively.
Assessing the wall’s carbon impact
To bring the general focus back to reducing carbon we wanted to assess the CO2 emissions associated with the wall build-up we specified and see if we could improve upon it. The 3D view (Figure 3) shows the extent of wall being measured and the construction detail (Figure 2) shows its general build-up.
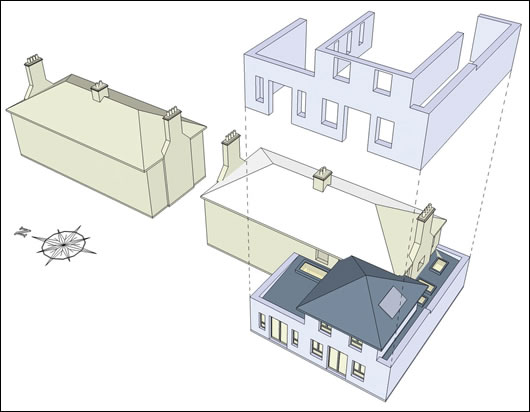
Figure 3: Exploded 3D view of study house focusing on new walls
It’s hard to obtain accurate, transparent carbon emissions data for building products. Right now it’s impossible to obtain these for Ireland. Some manufacturers regard CO2 emissions information as sensitive or proprietary and therefore secret, most others have probably never done the maths because till now if they were never asked to.
The figures we have used come from a range of places. As UK sources (from Bath and Oxford) predominate and as transport distances effect the carbon emissions of each material it can be said that the tables on the next page represent a house somewhere in middle England. While it isn’t Dublin and while the emissions cost of the Irish Sea hasn’t been allowed for, most of the CO2 emissions impact has been captured for each product and crucially the proportional impact of each build-up is shown. That is to say while it could take years of scholarship to conclusively determine the actual CO2 emissions associated with each wall build-up for a house in Ireland, what’s shown below should give us a good sense of what is a low or higher carbon approach to building the walls of domestic housing.
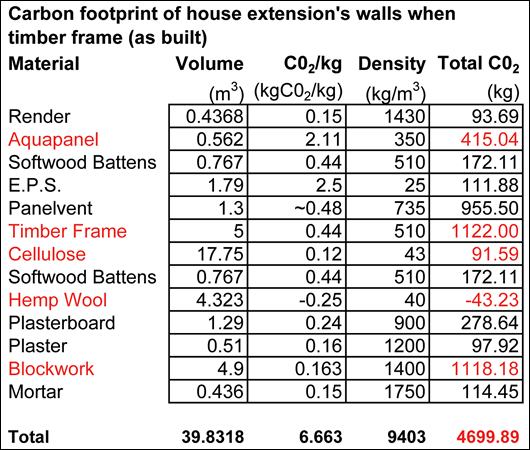
Table 1: CO2 emissions of wall using timber frame
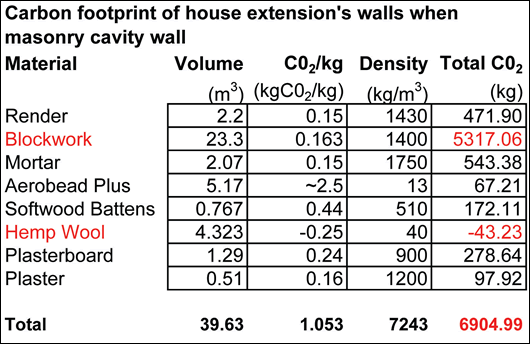
Table 2: CO2 emissions of masonry wall
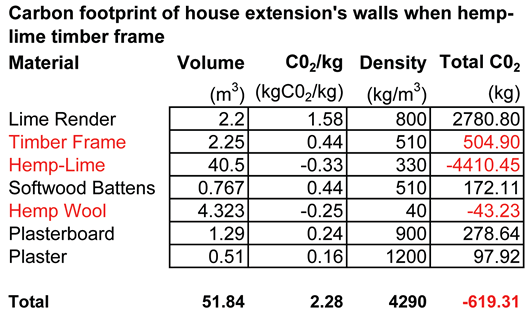
Table 3: CO2 emissions of wall using hemplime timber frame
The major source for most materials is the ‘Inventory of Carbon & Energy’ (ICE) by Prof. Geoff Hammond & Craig Jones of the University of Bath. This is downloadable from the university’s website. We could not obtain data for Panelvent so used equivalent data for particle board in ICE. We also used the inventory’s figure for rigid expanded polystyrene (EPS) in our assessment of blown-bonded bead EPS insulation. The emissions for lime render and hemp-lime construction came from Lime Technology Ltd. and the hemp wool data from Ecological Building Systems. Finally the figure for cellulose was derived from data from the American Cellulose Insulation Manufacturers’ Association.
Findings
We selected three alternate wall constructions; the specific timber frame build-up used, a low energy full-fill masonry cavity wall alternative and lastly another timber frame, this time with hemp-lime fill. U-values came in at circa 0.22 W/m2K (as discussed above), 0.24 and 0.15 W/m2K respectively. In all three cases the insulated services zone shown in figure 2 is retained. This author wrote about partial-fill cavity wall construction and hemp-lime construction for Construct Ireland before in Issue 8, Volume 2 and Issue 11, Volume 2 respectively.
For hemp-lime timber frame construction we followed the technical detail recently approved by the LABC, the representative body for all building control departments in England, Wales and Northern Ireland. In spray applications of hemp-lime biocomposite the frame and a sacrificial piece of formwork fixed to its rear are erected first. The hemp-lime is sprayed for the full thickness of the wall from the outside, encasing three sides of the timber stud. After setting the hemp-lime surrounds and supports smaller studs can be used, such as 100x50m studs – well below usual stud sizes. The lime of the mix helps preserve the timber, and the mix also has excellent vapour permeability, weather tightness, air-tightness and a good U-value. Lastly it is the same cost as masonry wall construction for multiple builds.
It’s worth scanning tables 1-3 to compare the material used and their carbon impact. An interesting comparison is Aquapanel and blockwork in table 1. Note the large volume of blown cellulose but comparatively small CO2 emissions. Most importantly hemp wool and hemp-lime are shown to sequester carbon: even despite the manufacturing process, the finished product locks in more than was emitted in its production.
Jumping straight to the bottom line, the tables show that the same wall constructed in three different ways would be responsible for 4.8, 7.4 or -0.6 tons of CO2. The timber frame wall (with either concrete block or cementitious board outer leafs) was therefore responsible for 35 per cent less emissions than a wall where both leafs were concrete block.
The really exciting information emerges when comparing the hemp-lime timber frame wall with the other two. It is responsible for 112 per cent less emissions than the more conventional timber frame construction and 108 per cent less than the masonry wall. Putting it differently, in substituting hemp-lime timber frame for timber frame or masonry walls 5.4 or 8 tons of CO2 are offset!
Add this 5.4 or 8 tons of CO2 to the roughly 8.5 tons of CO2 already offset by using 70 per cent GGBS cement and it can be seen that changing the wall construction of this modest 105m2 extension could give a total CO2 emissions offset of between 13.9 or 16.5 tons of CO2 without a significant change in price. Going back to the DEAP assessment of 2.62 tons of emissions for primary energy annually, we can see the use of 70 per cent GGBS cement and a change to hemp-lime timber frame from timber frame or masonry would offset 5.3 or 6.3 years of emissions due to typical energy use.
Ian Pritchett of Lime Technology states that substituting hemp-lime timber frame for masonry construction can offset a whopping 50 tons of CO2 per house. This author hasn’t yet been able to confirm that, but that claim and the study above illustrate that the Transition movement’s mantra of reducing carbon and building resilience can be applied to the construction of a house as much as its energy systems and the occupants within.
In the next five years we, as a society, have the chance to make big changes to how we live as a community, how we use energy and how we build. The greatest obstacles are not technology but our mindsets and the degree to which we cling to the old paradigms. It is foolish to think we have limitless time or that change is someone else’s job. As Rob Hopkins says the world we build can “be far more fulfilling and enriching, more connected and more gentle on the earth than the lifestyles we have today”.
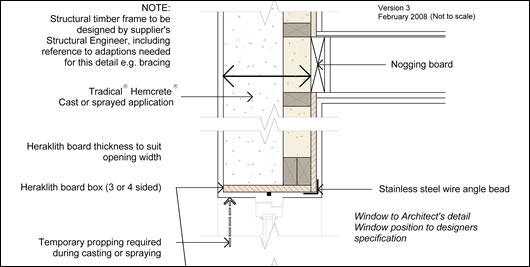
Figure 4: Excerpt from LABC detail showing head of window of hemp-lime timber frame for spray-application
References
1 Visit www.Transitionculture.org and www.TransitionTowns.org for more information
2 Visit www.sustainable.ie/powerdown for more information
3 Gustavsson, L. & Sathre, R. (2005). Variability in energy and carbon dioxide balances of wood and concrete building materials. Building & Environment
4 Prof. Hammond, G. & Jones, C. (2006). Inventory of Carbon & Energy. Bath, University of Bath
5 May, N. (2005) Breathability: The Key to Building Performance. Oxford, NBT.
- Articles
- Design Approaches
- In Transit
- Transition Towns
- Joseph Little
- Carbon Penalty
- photovoltaic
- blown cellulose insulation
Related items
-
Steeply sustainable - Low carbon passive design wonder on impossible Cork site
-
Focus on whole build systems, not products - NBT
-
International - Issue 29
-
Passive Wexford bungalow with a hint of the exotic
-
The House of Tomorrow, 1933
-
1948: The Dover Sun House
-
The dazzling Dalkey home with a hidden agenda
-
Mayo passive house makes you forget the weather
-
A1 passive house overcomes tight Cork City site
-
Norfolk straw-bale cottage aims for passive
-
Time to move beyond the architecture of the oil age
-
West Cork passive house raises design bar