- Retrofit
- Posted
Coastal cottage reborn
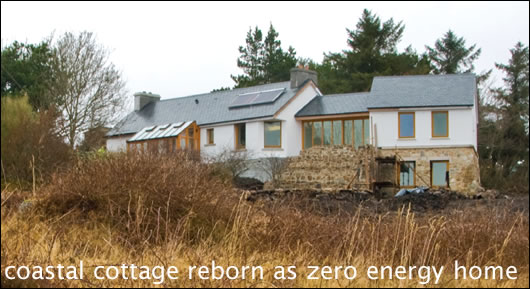
Any building, no matter how cold and draughty, no matter how remote, can be improved to world-class energy performance, as an upgraded and extended Donegal cottage dating back to the 1800s proves.
In planning the refurbishment and extension of his nineteenth century cottage, architect Cathal Stephens set himself an ambitious challenge; to bring the entire structure to passive house standards. In the process, he has blended air-tightness, super-insulation and a range of renewable technologies to create what is highly likely to be a net energy positive house.
“Sometimes I think it’s three jobs in one,” says Stephens, “because, there’s a refurb, and the extension has a basement and an upper floor. The basement is partially in the ground so it’s of masonry and concrete construction, and the above ground addition is timber frame, so in terms of insulation, air-tightness and all the different things that you think about when making the building energy efficient, we have three different conditions.” The project was also complicated and delayed by the fact that Errigal Construction, the main contractor, went out of business part of the way through.
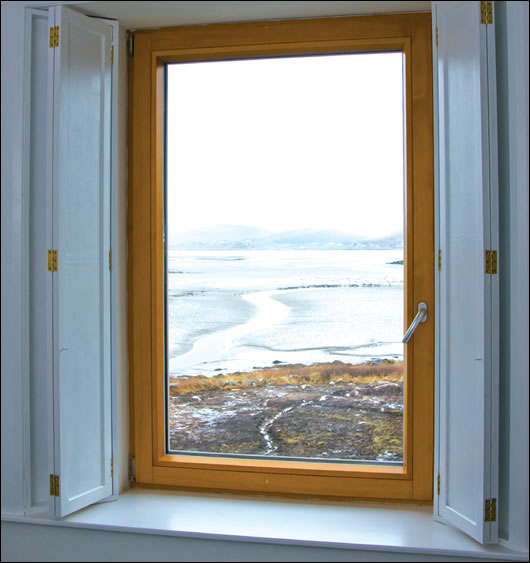
Large windows make the most of impressive views of the sea
Beginning with form, design and layout, the existing orientation of the building did not present a problem. Overlooking a tidal bay at Meenacross in south Donegal, the main views lie to the south. “We were well positioned to have good solar orientation; big windows in the south, no windows in the north except for the existing ones, so that part of it fell into place fairly naturally.” The existing building is typical of vernacular architecture – long, narrow and of stone construction. The extension is cranked slightly, and extends the footprint of the building by about only about a third. The layout here too is uncomplicated. “It’s not a cube,” says Stephens, “but it is a fairly simple shape. We have almost no ins and outs, just one at the junction of the old and the new.” A glazed sunroom connects the new timber frame structure with the old stone cottage, while the concrete and masonry lower floor, which sits partially into the ground, is self-contained and is accessed solely by an external door.
Patrick Daly, who acted as energy consultant through the project, emphasises the importance of getting the glazing right on passive builds. “Glass on the north,” says Daly, “particularly when you’re going for passive standard, has a huge impact. You really need to reduce it down. We try to go for 60% on the south if possible and try not to go over 15 or 20% on the north.” He points out that with wall U-values of 0.15 W/m2/K and best possible window values around 0.8 W/m2/K, a north elevation window loses more than five times the heat of the high performance wall, and gives zero passive solar gain returns. As a result, any north elevation windows are heavily penalised in the Passive House Planning Package software.
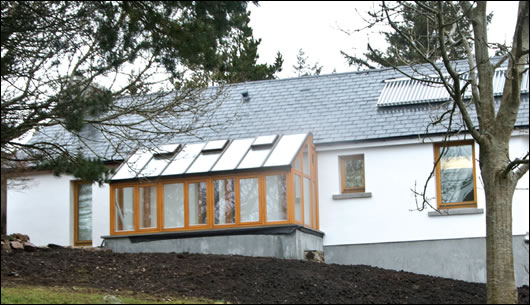
The south facing solar conservatory makes the most of passive solar gain
It was also important to Stephens that the design be sympathetic to the landscape and the traditional architecture of the area. To that end, the masonry extension was faced with granite excavated from the site.
Air-tightness and insulation in the new part of the building were quite straightforward. The lower section of the extension has a reinforced concrete retaining wall below-ground, with Quinn Lite B5 blocks on top. The Quinn Lite blocks also provide the outer leaf on the u sections above ground, which is then faced with the recycled granite. In the cavity there’s 150mm of Kingspan TF 70, specified to achieve a total U-value in these walls of 0.12 W/m2/K. The basement floor has 100mm of concrete screed on 300mm of insulation and carries a U value of 0.11 W/m2/K. All of the concrete used in the build was low carbon, with a 50 per cent GGBS mix provided by Muckish Sand and Gravel. On the upper floor of the extension, a double timber frame was used. “We’ve got a 100mm stud on the outside,” Stephens explains, “we’ve a 150mm gap and then a 140mm stud which is the structural stud carrying the load. The cavity lines up with the cavity below, so you have a continuous run of insulation. The double frame allowed us to have almost 400mm of insulation. That goes up the wall, up to the roof ridge and down the other side.” The insulation used is Warmcell 500 cellulose, provided by Brendan McGee insulation. In shallower cavities, this would be damp sprayed in, but because of the depth, McGee elected to turbo fill – holes are bored and the product is blown in dry. The full wall build up, which delivers a U-value of 0.13 W/m2/K runs as follows: 12.5mm plasterboard, 25mm battens to form service cavity, 10mm Plywood sheathing, 140mm insulation/timber frame, 150mm insulation, 100mm insulation/timber frame, 50mm cavity unventilated, 50mm Heraklith board, 28mm lime render. In the new wing, the roof U-values comes in at 0.1 W/m2/K. Ecological Building Systems provided the Intello air-tightness system, including membrane, tapes and adhesives.
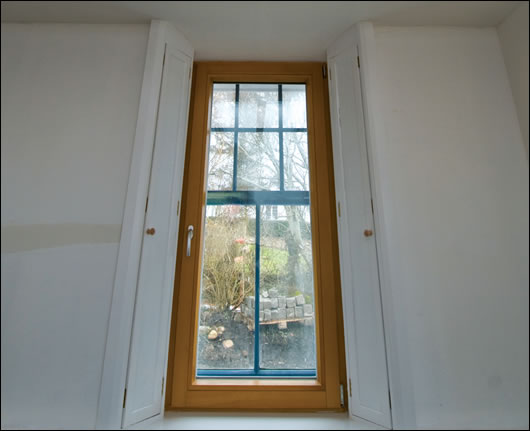
Old style wooden shutters were made and fitted by a local joiner, with triple-glazed uits installed inside the original windows
One of the central challenges of the project lay in securing good air-tightness results and super-insulation on the old wing of the building. The first step was to insulate. Stephens’ choice of Greenspan’s Brillux external insulation system came in part as a result of a desire not to encroach on already limited internal space. Chris Scanlon of Greenspan explains that given the requirement to achieve ambitious results and the absence of a cavity, the 200mm of Platinum EPS insulation was particularly appropriate to the Meenacross job. The board is adhesively and mechanically fixed to the external wall, followed by a base coast, mesh and primer before a finish is applied. The 200mm alone provides a U-value of 0.14 W/m2/K.
The design team had the luxury of being able to create both a continuous insulated layer and a continuous air-tightness layer in the new building. That option wasn’t available in the old. Internally, the walls were dry-lined extensively but not comprehensively – again losing space was an issue. “We had cold bridges at the bottom and at the top of the wall,” says Stephens, “where the insulation on the outside couldn’t be continuous with the insulation under the floors, or couldn’t be continuous with the insulation in the attic because, so we had some complicated details to get us round the eaves.”
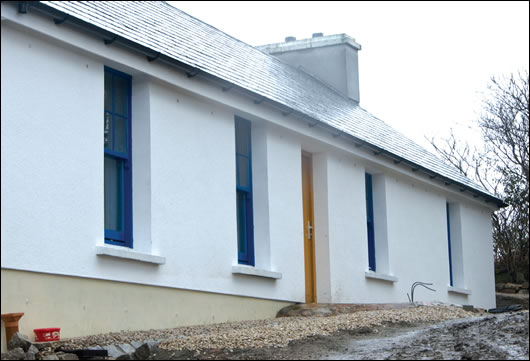
The existing house was insulated externally so as not to reduce internal space
“We insulated the roof in the plane of the ceiling,” Patrick Daly explains, “which allowed us to put almost 400mm of insulation in the ceilings of the old building, but where the ceiling meets the thick wall, that reduces to only about 125mm, which is the depth of the rafter across the top of the wall. It’s a half a meter thick wall and there’s 125mm rafter sitting on it, so we did some innovative detailing around the eaves, to get thickness into that junction u using different materials, and in so doing created a service zone for the heat recovery ventilation system.” The cottage wall with the internal dry lining gives a U value of 0.12 W/m2/K while the unlined sections give 0.15 W/m2/K.
Daly and Stephens became concerned that, if there was any build up of water vapour in the stone wall between the internal dry-lining and the external insulation, it would have no way to get out. This would of course lead to mould growth. Calculations suggested that this would not be a problem, but just in case, they decided to take action. “We scored the old sand cement rendering on the outside wall,” says Stephens, “top to bottom and put a vent top and bottom every 600mm all around the outside of the old building. These are tiny little vents, the same size as a cavity weep hole, only 12mm, and we found little caps that are designed for weep holes and used those to cover each vent, so there’s a very subtle little pattern of these things all the way round.”
Air-tightness in the old wing presented similar headaches. “We tried a few different things on the walls,” says Daly. “We re-pointed some of the joints in the random rubble, we actually air pressure tested and went around the whole envelope, spraying the wall where we could find leaks; that gave us some limited success.”
“In the ceiling,” he goes on, “we had a membrane to help give us our air-tight layer but when that came across internal cross walls, we had problems. In some cases, we tried to put it over existing cross walls that went into the attic zone. In other cases we tried to bond it to the wall. The cross wall was very porous itself coming down through the joists so it was a very challenging context in which to try and get air-tightness.”
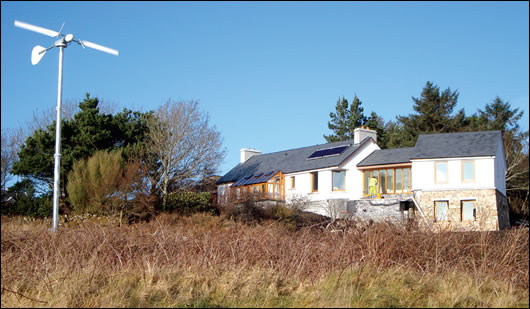
Due to a combination of available wind resource and energy efficiency measures, the turbine may provide more energy than the household’s total demand
Three air-tightness tests took place over the course of the build. The first, in September of last year, gave a result of 7.6m3/hr/m2 @ 50Pa, while the most recent one last October came in at 3.8 m3/hr/m2 at 50Pa. Both Stephens and Daly hope that additional measures will see that figure fall further, to a target of 3 m3/h/m2.
Further issues emerged in the old wing. When the construction team began to probe beneath the floor, they hit rock at a depth of only 100mm. In addition, part of the floor lay below the level of the ground outside, giving rise to dampness within. The rock in the floor therefore had to be broken through to create sufficient depth for damp proofing, radon barrier and the 150mm of insulation required to deliver the requisite U-value. Because rock breakers could not be brought in, Stephens harnessed local knowledge and used the traditional skill of ‘plug and feather’ to break out the floor. This was a laborious and time consuming process, in which sledge hammers are used with wedges to break the stone piece by piece. As if that were not enough, a slope in the floor had required the use of a suspended wooden floor in part of the old wing. In the refurbishment, a new floor was constructed on top of this. Overall U-values in the floor come to 0.10 W/m2/K in the suspended floor and 0.12 W/m2/K in the solid floor.
Variotec windows were supplied by David Hopkins of Technical Architectural Consultants and Associates and fitted by Peter Loftus of Milltown Passive Builds. “It’s the Energy Frame II system.” Hopkins explains. “It’s a solid wood system with PUR insulation at the core and a pine frame, without any aluminium cladding.” A triple glazed system with an 85% argon fill, the overall U-value comes in at 0.79 W/m2/K. Installation is a three-day job, says Peter Loftus. To prevent cold bridging, an insulated strip is fitted across the sill, while instead of the usual brackets, the windows are held in place with a series of customised screws. An insulated foam is then used around the frame. The windows are also taped internally and externally.
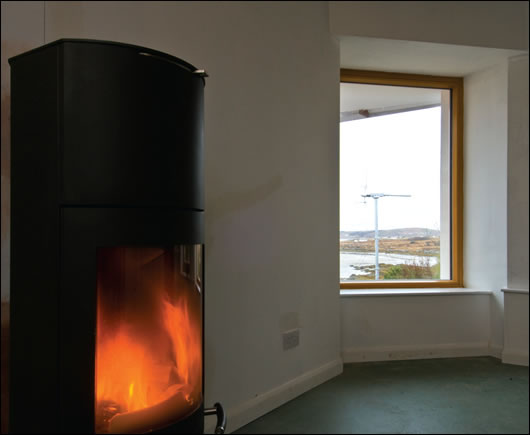
A wood burning stove is the primary heat source
Because of the thick external walls and the additional depth from the external insulation, Stephens decided to retain the old windows in the cottage and install the passive standard windows inside them, thereby allowing the cottage to retain its existing look and character. A customised sill – incorporating a narrow drainage slot should any moisture get caught between the two sets of windows – was moulded onsite. The deep reveal also facilitated the use of old style wooden shutters, which were made and fitted by a local joiner. u In addition to salvaging the original sash windows, all of the internal doors were also restored and reused.
Flooring for the house includes ecologically friendly marmoleum flooring from Forbo Ireland and polished concrete flooring, the latter being designed and installed by Uniqrete of Mountrath, Co Laois. “It absorbs heat very well and it lets it out slowly so it’s a very thermally efficient material,” says Vincent Fitzpatrick of the company. “And you’re not adding any other artificial material to the floor. Also, the light reflectivity is extremely good…You can considerably cut down on your lighting requirements because the polished concrete reflects the light much better.” Stephens has also made extensive use of fluorescent and LED light fixtures throughout the house.
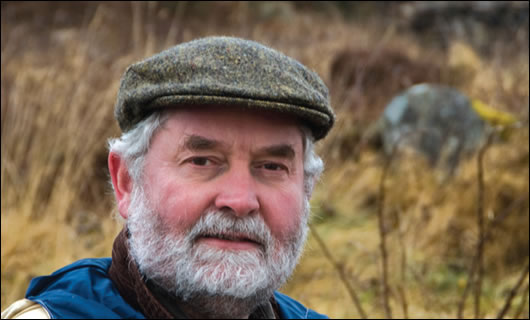
Client and architect Cathal Stephens
The primary heat source is a wood burning stove, an Austroflamm Tower Xtra, rated 4kW and with 80 per cent efficiency. It has an independent combustion air supply taken from the outside. The secondary heat source – wall mounted electrical heaters – have been facilitated but not installed. Stephens has decided to go through a heating season to see if they were necessary.
Heat distribution is facilitated by the mechanical heat recovery ventilation system. This is a MTD-ERV 350 Elite CO2 whole house MVHR system. It will provide continuous airflow of 100 to 400m³/h between normal automatic mode and high speed, with up to 95% heat recovery efficiency. The unit is fitted with brushless DC EC motors with integrated thermostats and CO2 sensors, it has an automatic 100% bypass and an automatic defrost cycle.
There are two eighteen tube Solarbayer CPC solar collectors, supplied by Maassen Sustainable Energy Ltd in Donegal, on the roof of the old wing, which connect to a 400L tank in the utility room.
A passive solar conservatory provided by Norman Pratt Conservatories, which sits outside the sealed envelope on the southern elevation, acts as a winter garden for the old wing of the building. Of FSC certified timber construction and double glazed, the use of metal on upper levels to retain the glass reduces the maintenance of the unit. Automated vents at high level limit overheating, while rain sensors facilitate automated closing.
Given the rock on the site, a conventional rainwater harvesting system with underground tanks was impossible. However, the house once had an over-ground system, fed directly by the gutters into a concrete tank. In later years this had become disused and had found a new role housing the oil fired boiler for the cottage. “We’ve returned it to its original purpose,” says Stephens. “We put two tanks in there and the gutters from the old house run horizontally straight into the shed. We have what the plumber called a weir, which is a little tank with an overflow on it, and a take-off at the bottom. That feeds into the rainwater harvest tanks. We’ve insulated the shed and put a stat on it so that in very cold weather a tiny electric heater will come on to prevent it from freezing.” The saved water is used for two purposes, to flush toilets, and to run through a rainwater garden which Stephens has built in front of the glazed sunroom which links the old and new sections. “Instead of putting all our surface water pipes underground, we gather the water and have it run through a visible stream, so when it rains you’ll see water trickling through here and the rainwater tank will continue to feed that for a few hours after rain stops.”
Stephens is also establishing a reed bed system, designed and with extensive consultancy from Ollan Herr of Herr Limited. “We’re using a separator to separate the solids from the liquids,” says Cathal Stephens. “Then a vertical flow reed bed and a horizontal flow reed bed. The toilets discharge into the separator, the solids are retained and compost in a chamber there, and then all the liquids go straight to the primary reed bed and are purified there, then they go to the secondary reed bed which is the polishing system.” Ollan Herr explains that the falls at Meenacross make it particularly well suited to a system that doesn’t require pumping. “Typically, you’d put in a reed bed if you wanted to avoid all electro-mechanical elements, so there are long term savings there.”
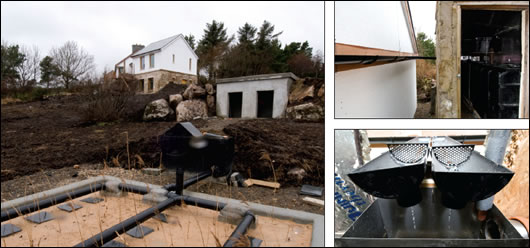
(above left) Wastewater will be treated by a reed bed system designed by Ollan Herr; (above right) rainwater will be collected by existing gutters on the old house that feed directly into the tanks in the adjacent shed
Patrick Daly estimates the primary energy demand of the house at 16,398 kWh/y, or 94.48 kWh/m2 y – which gives it a B1 rating. All this however is calculated before the turbine is taken into account. A conservative 12,500 kWh/y is anticipated from the turbine, which is designed and built by Chris Maassen of Maassen Sustainable Energy Ltd.
“It has a variable pitch mechanism in it,” says Chris Maassen, “so it pitches the blade according to the speed, for over-speed control. If the wind is blowing too strongly, it moves in a certain way to slow the machine down, and that’s all done automatically.” The turbine itself is bolted directly onto the granite.
“With the wind resource that Cathal has here,” says Patrick Daly, “it’s very likely that it’ll be a zero energy house. In fact, he should be generating in excess of his annual energy demand.”
Selected project details
Architect/client: Cathal Stephens
Energy consultant: Besrac
Structural engineers: Mitchell Murtagh
Main contractor: Errigal New Homes (ceased trading)
External insulation: Greenspan
Insulation: Kingspan / Warmcell
Air-tightness membranes & tapes: Ecological Building Systems
Windows: Variotec GmbH
Window installation: Milltown Passive Builds Ltd.
Block work: Quinn Lite
Marmoleum flooring: Forbo Ireland
Polished concrete Floors: Uniqrete
Low carbon concrete: Muckish Sand & Gravel
Passive solar conservatory: Norman Pratt Conservatories
Wind turbine & solar array: Maassen Sustainable Energy
Heat recovery ventilation: MTD Solutions
Wastewater treatment system: Herr Ltd
Related items
-
Derelict to dream home
-
Ecocem executive John Reddy becomes the first Irish President of the Institute of Concrete Technology
-
Traditional homes retrofit grant pilot launched
-
Dr. Barry Mc Carron appointed MD of KORE Retrofit
-
Bungalow Bills
-
New scheme offers up to €75,000 retrofit loans at low cost
-
Phit the bill
-
Mainstreaming retrofit – a massive missed opportunity
-
It's a lovely house to live in now
-
Is it okay to retrofit heat pumps before building fabric?
-
New Licence Plus scheme undermines retrofit standards, experts say
-
Government supported almost 27,200 home energy upgrades through SEAI in 2022