- Social Housing
- Posted
High & mighty
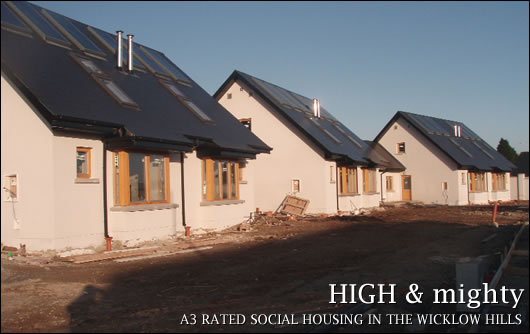
An advocate of sustainable building long before it was fashionable, Bill Quigley of NuTech Renewables has subsequently seen the mainstreaming of sustainability at first hand, having input into substantial projects for Leahy Bros, MKN and GEDA Construction amongst others. In their latest project, NuTech are working with Wicklow County Council on a social housing scheme with impressively high energy performance targets to meet, as Quigley explains.
The site in Knockananna on which these twenty-two houses are situated is interesting from the energy design viewpoint for two reasons. Firstly, a really good point is that the site slopes gently to the south which makes it attractive for the utilisation of solar energy, but secondly, the site is high in the Wicklow hills which will have a negative effect on the ambient temperatures that will be experienced in winter. Because of these two points the designer and project manager of this housing scheme for Wicklow County Council, Stephen O’Sullivan, approached NuTech Renewables to carry out a full energy analysis of various house types and construction to ensure that the houses would perform in practice as low energy, low CO2 houses.
In early meetings with Marc Devereux, senior engineer, housing section in Wicklow County Council and Stephen O’Sullivan, it was clear that as part of this project the council wanted to understand the principles of effective low energy housing and how it could be replicated throughout the county in future projects.
It was decided that the project should be divided into three parts, beginning with the design and analysis stage, carried out by NuTech Renewables with the help of Marc Devereux and Stephen O’Sullivan. This stage would be concluded when the houses were going out to tender. The build stage would be the next part, where NuTech Renewables would be closely involved in the build process to ensure that the houses and systems were meeting the criteria as set out in the analysis stage. The final part would the monitoring stage where NuTech Renewables would monitor the energy performance of the houses to report on the energy balances and ensure that the design was functioning correctly.
Approval for the project to proceed was received from the Department of the Environment on the basis that phase one of the project, which involved the first ten houses, would be built and monitored prior to phase two, the last twelve houses, being completed.~
The design phase
From the outset NuTech pointed out that thermal energy use in housing is essentially divided into three thirds. The first third is by way of heat loss through the fabric. The second third is by way of air infiltration and the necessary air for ventilation, and the final third is the energy demand for domestic hot water.
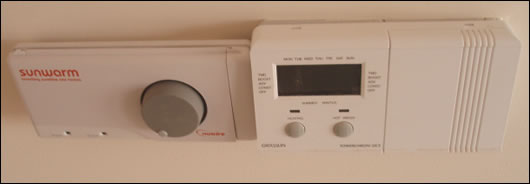
The heating control system, as designed by NuTech Renewables, is vitally important in achieving a genuinely low energy house and greatly improves the efficiency of the solar collectors
To save energy by adding more and more insulation in the fabric runs up against the law of diminishing returns. Hence, it was determined that the design U-values for the fabric would be considerably better than the Building regulations but not down to Passive House standards despite the elevation of the site. It is worth remembering that adding a massive amount of insulation to the fabric will not achieve a zero energy house as this measure is only attacking one third of the house energy demand. The following U-values were adopted:
• The external wall U-value was calculated at 0.179 W/m2K
• The ground floor U-Value was calculated at 0.176 W/m2K
• The sloping roof U-value was calculated at 0.16 W/m2K
• The windows U-Value was calculated at 1.50 W/m2K
The houses were designed to be constructed using timber frame construction. It was decided to use closed panel construction with factory fitted insulation. The walls were further battened out to create a service area on the inside face and this service area was also further insulated on site - hence the reasonably low U-value achieved in the external walls.
The energy savings that can be achieved by attacking energy use in the area of air infiltration and the necessary air for ventilation is known as the ‘low hanging fruit’ area. This is because measures to achieve energy saving in this area can yield far greater returns for clever design because it represents a full third of the typical design load. A specially designed heat recovery ventilation (HRV) system was arrived at to drastically reduce energy demand in this area.
Finally, a design to utilise solar collectors to reduce not only the energy demand for space heating but also to reduce the domestic hot water load was determined. Linking energy from the solar collectors into the HRV system and the heating system makes great use of the solar collectors and improves their annual solar yield enormously.
On the energy supply side it was decided to use a wood pellet stove/boiler in the house to provide the back-up energy for space and water heating. The stove chosen by NuTech had a maximum output of 10 kW with 20% of its energy going directly to the room by way of radiant and convection heat while the remaining 80% is delivered to the hot water circuit.
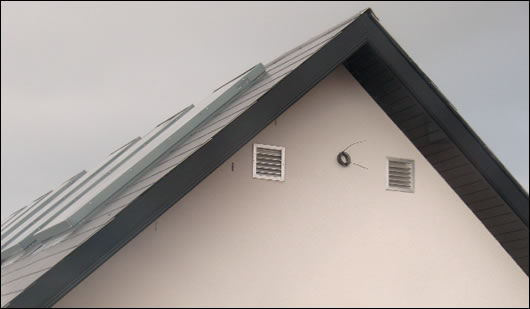
Solar collectors are linked into the heating system
The control system design for the integrated space heating, ventilation, hot water and solar heating system was carried out by NuTech. Mark Forkin of NuTech Renewables designed the controller such that the homeowner only has to dial up the required temperature and set the boiler timer to run the wood pellet stove as and when desired to provide back-up energy for space or water heating. The control system is vitally important in achieving a genuinely low energy house. This is particularly important in the case where there are integrated systems such as solar collectors, HRV systems and wood pellet boilers.
In summary then, in the design phase we had arrived at a design solution involving the following:
• appropriate levels of insulation to reduce heat loss through the fabric
• details to reduce the amount of linear thermal bridging in the construction
• a designed level of air tightness which could be achieved on site
• a specially designed HRV system which was utilised as the heating system of the house
• a specially designed air handling unit with an inbuilt control system that integrated the HRV system with the air solar collectors, the heat distribution system and the wood pellet boiler
The analysis of this overall system showed that this was a indeed a low energy house design saving of the order of 64% of the energy required for space and water heating including ventilation and lighting. The carbon savings, over the base case reference house were much higher due to both the reduction in energy demand but also to the use of the wood pellet stove on the energy supply side. When analysed using the DEAP software from SEI the houses achieve an A3 rating. This is actually very good when it is considered that wood pellet boilers will be some 10% less efficient than a condensing gas or oil boiler (based on calculations using the Gross calorific value for relative fuels). From Wicklow County Council’s viewpoint we now had a system design that was repeatable on any site in Wicklow. This concluded the work done on the design phase.
The build phase
The building of the houses started in May 2007 and the first phase of ten houses are now fully erected on site. The builder is Kevin Mahon of Donnelly Installations Ltd – a company that specialises in building timber frame houses. Armstrong Timber Frame supplied the house timber frame kits. Both of these companies are based locally and are now fully committed to building houses that incorporate low energy features.
It is worth noting that these houses are dormer bungalows. The significance of this is that NuTech has always found that one of the most difficult roofs to effectively insulate are the standard ‘room in the roof’ type trusses so commonly used in dormer bungalows. At least of equal importance is the fact that these type of roofs are notoriously difficult to air-tighten. Normally in other countries such as the Netherlands a SIPS type roof panel is used but there were problems in using any of these systems in this case, including the span length from wall plate to ridge and the cost of a SIPS type roof. The solution used in these houses in Knockananna was the use of sprayed Icynene insulation – a system widely used in Canada. This had the effect of not only insulating the roof but it also air-tightened it particularly as the roof was insulated from the wall plate to the ridge. This meant that we had the benefit of a low cost trussed rafter roof with a fully integrated insulating and air-tightening membrane.
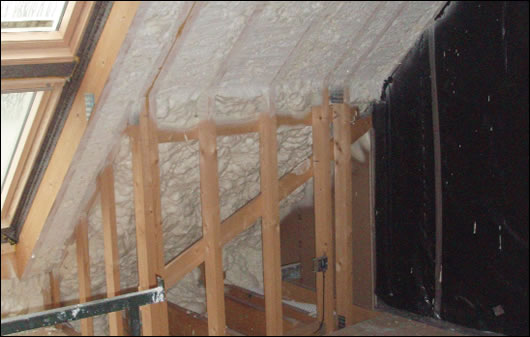
Sprayed Icynene insulation was used to insulate the roof, which also improved the air-tightness of the building
NuTech carried out blower door testing on site during the build process in order to ensure that the houses would achieve their design adroitness level of 0.1 air changes per hour at normal pressure. The sealing of the timber frames to the concrete floor along with specialist sealing tapes around the windows was also addressed. Sealing around the Velux windows was particularly important, and was achieved by sealing the window in its ope first and then sealing the roof vapour barrier to the window with proprietary tapes. The importance of detailed design and the follow up inspection and testing on site to achieve air tightness cannot be over emphasised. The enthusiasm and effort put into the project by Stephen O’Sullivan of Wicklow County Council who is acting as project manager for the council is of vital importance. This enthusiasm has also spread to the builder Kevin Mahon. In short, the whole team is determined that the houses will be built to the specification and to achieve the energy targets.
A number of the houses are now completed and the wood pellet boilers have been installed and tested. Included in this testing phase has been the design of the chimney. This work was carried out in conjunction with Schiedel Chimney Systems and the insulated flue is brought all of the way up through the house and terminates at a high level over the roof. This ensures that the flue will work well and that the residents should not experience any odours outside the houses. NuTech have now begun a phase of testing to ensure that the houses will perform to their designed energy targets. Final blower door testing will be completed to determine the air infiltration rate. NuTech will then carry out temperature monitoring and other measurements to determine the overall heat loss characteristic of the houses. Once we know this we can calculate and predict with much more confidence their actual energy performance. NuTech do this by using our hour-by-hour energy model. This model has hour-by-hour weather data built-in and so, gives a fairly realistic picture as to how the houses will perform in winter and summer. One snag of course is that we do not have weather data for Knockananna but we can, with the aid of Met Eireann, get some idea of what winter temperatures we will encounter and then base the calculations on that data. Because of the location of these houses at such an elevation over sea level and because of the exposure to high winds it makes good sense to ensure that they are as airtight as the design demands and to ensure that the insulation systems are as effective as possible. This is why so much attention = is being paid to the actual performance of all of the systems being used in the Knockananna houses, which show a designed A3 rating.
One point that is worth making in relation to houses designed an A3 rating is as follows: an A3 house will have a primary energy demand of, for instance, 70 kWh/m2/a. Let us assume the house has a floor area of 100m2. It will therefore use 7,000 kWh in a year for space heating, ventilation, hot water and lighting. Subtract from this total some 2,000 kWh that is associated with electricity for lighting, fans, and so on, and this leaves say, 5,000 kWh that is supplied by way of the heating system. Allowing for the calorific value of oil and the factor for primary to delivered energy this equates to approximately 400 litres of oil for space and water heating in a year.
This is a small amount, so everybody in the building industry should be aware that a 100m2 A3 house will use only a small amount of oil or gas – if it uses a large amount more then this could lead to serious dissatisfaction among home owners.
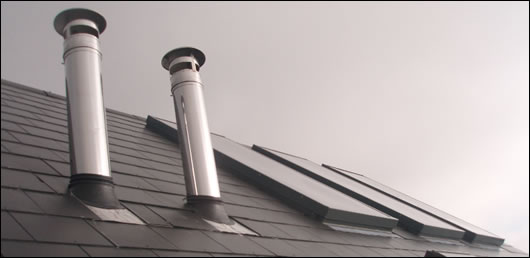
The insulated flue, supplied by Schiedel Chimney Systems, is brought through the house and terminates at a high level over the roof, ensuring that the flue will work well and that the residents should not experience bad odours outside the house
The monitoring phase
When the houses are completed it is intended to monitor both fuel usage and average house temperatures over a period of two years. NuTech will be endeavouring to check the variation due to numbers of occupants per house and their lifestyle in these low energy houses. It is well known that variances in types of occupancy can have a huge effect on the actual energy performance of houses of a particular design. It is intended to minimise this variation by way of explanation of the systems involved and how best to use the systems such that the occupants will achieve both high levels of comfort and a high quality lifestyle. As a part of this programme NuTech will be providing a demonstration of the operation of the systems to each resident. They will also have a telephone contact number for queries by residents and will be maintaining the systems throughout the monitoring period.
In summary
The design, building and monitoring of these houses in Knockananna has provided a unique opportunity to arrive at a system for low energy housing that is practicable, buildable and reasonably economical. The monitoring that is taking place in both the building phase and when the houses are occupied will provide excellent information on the heat loss characteristic of these houses and on the actual energy performance of the houses when occupied by different families.
Project details
Client: Wicklow County Council
Main contractor: Donnelly Installations
Timber frame: Armstrong Timber Frame
Energy consultants, renewables and HRV: NuTech Renewables
Roof insulation: Icynene supplied by GMS Insulations
Chimneys: Schiedel Chimney Systems
Windows: Rationel Vinduer Ltd
- Articles
- social housing
- High & mighty
- Nutech
- Quigley
- wicklow county council
- A3
- wood pellet boiler
- solar collectors
- bungalow heating
- Schiedel
Related items
-
Bonny in Clyde
-
From Nero to zero
-
Measure everything
-
Renfrewshire aims for 3,500 whole-house deep retrofits
-
Welsh social housing to embrace passive house, timber & life cycle assessment
-
Ecocel on site with 56 homes in Cork
-
Senior college
-
COP 26 & the future of the Glasgow tenements
-
Is affordable housing a policy blind spot?
-
Government announces €45m for social housing retrofit
-
Stirling Work - The passive social housing scheme that won British architecture’s top award
-
Higher costs, less benefits - Why the enhanced social housing leasing model is a bad deal