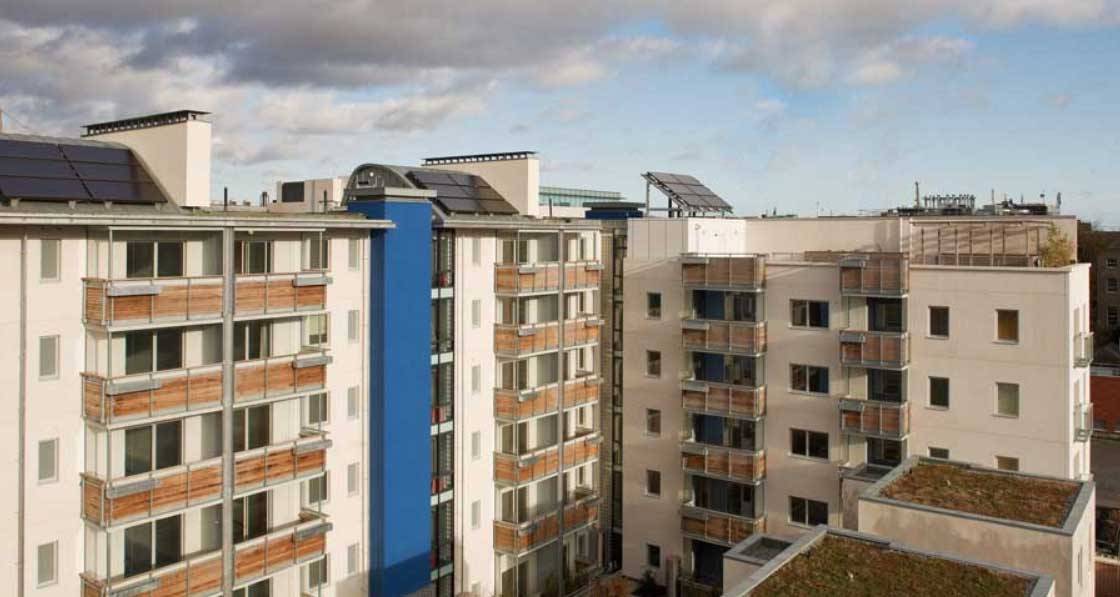
- Social Housing
- Posted
Public good
Until recently the York Street flats had been a living legacy of failed past approaches to social housing – a slum of mainly north-facing flats dating from Victorian times, and poorly rebuilt in the year Ireland became a republic, 1949. John Hearne visited the recently redeveloped York Street and found a thoroughly sustainable set of buildings that should inspire thoughts of future progress rather than past failings.
Dublin City Council’s York Street housing development gives the capital a landmark in sustainable design. It answers all of the challenges of a tight, urban footprint to deliver sixty-six apartments, many of which are either dual or corner aspect. In addition to the highly insulated building fabric and extensive use of sustainable materials, the development includes a group heating system, high efficiency condensing gas boilers and solar thermal panels. Sedum roofs, together with roof gardens and communal ground-floor gardens maintain a strong green presence, while a specially commissioned pavilion provides state of the art waste management systems. The glazed balconies are a subtle innovation, combining a familiar feature for the tenants with a major source of passive solar gains. In addition to meeting residents’ needs, the building transforms the York St/Mercer St block, giving the city a vibrant design that addresses the street and restates key elements of the Georgian architecture that was destroyed in the forties. Designed by Seán Harrington Architects, the development is comprised of five apartment blocks and three mews-style dwellings.
Jim Roche, project architect with SHA explains that the practice was approached by Dublin City Council in 2003 and asked to do a framework plan for the area. The existing tenement-style flats were faced in red brick, looked Georgian but were not. All had been remodelled in 1949 when most of the original Georgian features were destroyed. These flats were arranged off single-stair access, with three flats per landing and up to twelve flats per staircase. They were large, but unsafe and unhealthy. All were single aspect and forty-five of the ninety-nine faced north into York Street. To finance the proposed redevelopment, Dublin City Council sold one third of the site to the College of Surgeons across the road, thereby reducing the land available, and presenting an even more restricted site to the design team.
Western red cedar was used for external cladding on balconies
The departure point for the subsequent design, says Roche, was the consultation process with the residents, who would vacate the condemned building and ultimately be re-housed in the new development. “We went through a whole process of what was good about apartment living, what was good about the existing apartments and what was bad about them, and we began to develop a scheme based on single stair access, with two apartments per floor.” The design that emerged delivered a much shallower block, giving vastly improved light and air into living spaces. Reducing the depth of the building also facilitated dual aspect apartments, with bay windows facing the street and glazed balconies overlooking the courtyard to the centre. Dublin City Council sought variety, so there are a total of 17 three-bed, 29 two-bed and 20 one-bed homes, while a large variety of layouts and dwelling types were incorporated into the design. Most of the apartments are either dual or corner aspect, while several even manage dual aspect living spaces. The development also includes a corner retail unit at Mercer Street and York Street, as well as a shared community venue on Mercer Street. In addition to the five blocks which comprise the bulk of the development, the design team chose to not to close off the southern elevation, but instead to construct three lower profile mews-style dwellings. “There are a number of reasons why we went that route.” says Roche. “These structures needed to be low to let the sun in, and we came up with this notion of a brick plinth on the bottom, with a box on top and large gaps in between to let the sun into the garden.”
The demolished flats had substantial gardens to the back; this was one feature the residents were anxious to see retained. Fulfilling that demand, given space restrictions was not easy. The new gardens feature vegetable plots, fruit trees, bird boxes, water features, a children’s play area, communal seating areas, as well as a pergola fronted by two reclaimed Georgian granite doorways, these among the few Georgian features left standing after the forties rebuild. There are also six stainless steel water-butts into which rainwater from down-pipes is fed for use in watering the gardens. The balconies, which overlook this space also act as an extension of the green space. All have been fitted with built-in planters. The garden also houses the central waste pavilion, where residents bring all of their household waste.
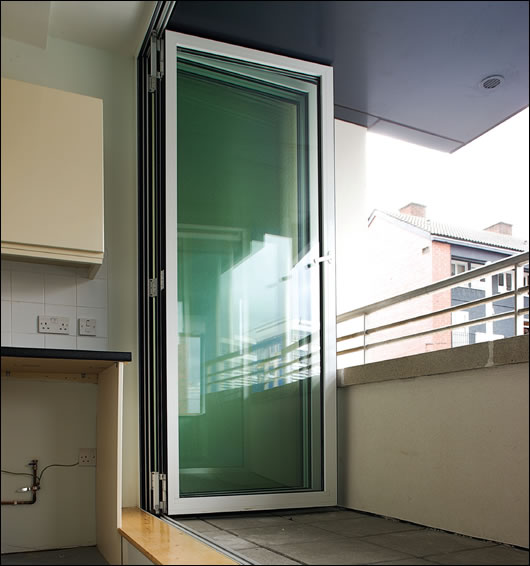
The Solarlux sliding glass system allows the balconies to remain fully exposed to the elements or, with the panels fully closed, gives the tenants use of the space during bad weather
Much of the building was prefabricated and assembled onsite. This approach cuts down on onsite waste and facilitates a speedier build, while construction in factory conditions rather than onsite protects against weather damage and delays and mitigates towards higher quality across the board. On the York Street elevation, the design team sought to recapture something of the street’s Georgian heritage. “Brick was very important to the feel of the street,” says Roche, “and important to the residents too, so we wanted to use brick, though in a modern way.” Techrete Group designed, manufactured and erected the architectural precast concrete cladding used to achieve the desired effect. On York Street, the brick-faced panels comprise a 25mm brick slip on a 150mm thick concrete backing panel and incorporate 60mm thick foil faced rigid board insulation. The insulation is fixed directly to the back of the precast panels before they leave the factory. These precast facades, which are non-structural, were then erected onsite. The remaining wall build-up consists of a 100mm cavity, a 75mm stud with rockwool infill, 12.5mm plasterboard and a skim finish.
The main structure in each of the blocks is provided by the cross walls, which are a lightweight twin-wall system. Two 65mm precast concrete panels were conveyed to the site and fixed in place, then the 125mm cavity in-between was filled with cement containing 20 per cent GGBS from Ecocem, achieving CO2 emissions reductions of circa 15 tonnes by displacing some Portland cement. Roche stresses that the twin wall system has the advantage of being easy to transport, while factory prefabrication ensures a higher quality end product. Within the apartments, all walls are stud walls. This lack of any internal structure engenders long-term flexibility in the building, facilitating changes of use over its lifetime.
On the York Street elevation, the design team sought to recapture something of the street’s Georgian heritage. “Brick was very important to the feel of the street,” says Roche
The three mews style dwellings to the rear of the development each contain one bedroom apartments on the ground floor with a duplex overhead. “We wanted a different feel here.” says Jim Roche. “So these were done with traditional brickwork, lime mortar, and timber frames with sheep wool insulation.”
The timber frames were provided and fitted by the Timber Frame Company in Wexford. “All our timber is imported timber.” says Ed Devereux of the company. “We’re members of NSAI and ITFMA so everything we use has to be graded, it has to be a specific standard of timber and it’s all from sustainable sources.” The 140mm frame was fitted with sheep wool insulation, provided by Sheep Wool Insulation in Wicklow. “For the York Street project,” says David Pierce of the company, “Premium sheep wool insulation was chosen…The insulation was installed between the studs and fixed permanently in place using a stapler”. Using sheep wool insulation in the walls gave a U-Value of 0.27 W/m2K, whilst also improving the project’s green credentials, combining low embodied energy manufacture, breathability, and of course, a constantly replenishing supply chain.
All internal floors are finished in Marmoleum, supplied by Forbo Ireland. “It’s a modern version of a traditional linoleum.” says Paul Carney of the company. “It’s a sustainable, environmentally friendly, fully biodegradable product, in that all the raw materials used are natural products.” All Forbo’s manufacturing operations are ISO 14001 certified, raw materials (including linseed oil, rosins, wood flour, jute and ecologically responsible pigments) and energy are used efficiently, waste is recycled and emissions are kept to a minimum.The walls were made air-tight by the use of LUP air-tight system, which Pierce also supplied. The membrane used was LUP Actiroll, a breathable vapour check which was taped and sealed with LUP tapes and glues. “This ensures that warm air does not escape from the living space into the envelope of the building and significantly improves the energy efficiency of the building,” says Pierce.
A good lime mortar offers several advantages over cement render, Edward Byrne of the Traditional Lime Company, who supplied the product explains. “It’s more sustainable than cement renders and plasters, it’s more environmentally friendly and it means the bricks are then recyclable. If you need to take the bricks down, the lime will come off without damaging the brick.” Lime render is naturally breathable, and depending on the type chosen, you use a third less CO2 in making a tonne of lime than a tonne of cement. But because hydraulic lime isn’t made in Ireland, shipping in from abroad reduces the environmental advantage.
In total, The U-values achieved in the build range between 0.177/0.178/0.27 W/m2K in the walls, between 0.16 and 0.19 W/m2K in the roof and 0.21W/m2K in the floor.
Limited use was also made of materials salvaged from the demolished structure. In addition to the doorways mounted in the garden, some of the red brick and wrought iron railings were retained for restoration work elsewhere by Dublin City Council, while all of the roofs in York Street were constructed from floor joists saved from the condemned building.
Internally, all of the apartments are laid out with reference to the sun, with dual aspect living spaces wherever they could be achieved. The glazed balconies featured in many of the apartments are a northern European idea. “I used to live in Finland.” Jim Roche explains, “and I saw these glazable balcony systems there seven years ago. It became a regulation in Finland that every new apartment had to have them so they could close in their balconies in winter.” The German Solarlux sliding glass system allows the balconies to remain fully exposed to the elements or, with the panels fully closed, to allow the tenants use of the space during bad weather. Effectively, it gives each apartment an extra room. “It’s a really ingenious system.” says Roche. “You pull a chord and that releases the lock at the top, which then opens the first panel. It hinges back, then all the others side along the frame and hinge out.” The system turns an open balcony into a winter garden, providing a highly effective source of passive solar gains.
Seven of the apartments were also fitted with Schüco bi-fold door systems to provide access out to non-glazed balconies. Jim Cogan of Produkt, who provided the systems, says that the glass used is double-glazed, low-e glass with an argon fill. “They feature 6mm laminated safety glass, the frames are thermally broken and the overall U-value is approximately 1.7 W/m2K.”
Two separate window systems were used. Scandun Vinduer Scandinavian redwood windows went into the mews style houses on Crabbe Lane. “It’s a Danish window and door system,” Michael Dunn of the company explains. “They’re double glazed, and have a U-value of approx 1.4 W/m2K.”
In the main development, the design team chose Velfac’s composite aluminum and pine window systems. “Effectively,” says Lorcan Murphy of the company, “you get the warm feel of timber on the inside and the low maintenance of the aluminium frame externally. The window has a design life of forty years. No moving parts need to be changed within that period.” The system differs from an aluminium clad window in that the two materials are kept entirely separate. “If you look at a clad window,” says Murphy, “it’s a timber window with an aluminium skin bonded on, whereas when you open one of our sashes, the entire aluminium frame moves away from the timber mainframe...It’s also a bi-modular system or a uniform sightline system, and that means that an opening vent appears identical to a closed vent from the outside…Architects are particularly fond of that because it gives everything a uniform sightline.” The thermal break between the two surfaces also boosts the window’s energy profile. “There’s also a thermal isolator within the aluminium frame to decrease the chances of cold bridge.” The glass itself is a low-e, high performance glass, and has an argon fill. The U-value in the unit comes in at 1.4 W/m2K.
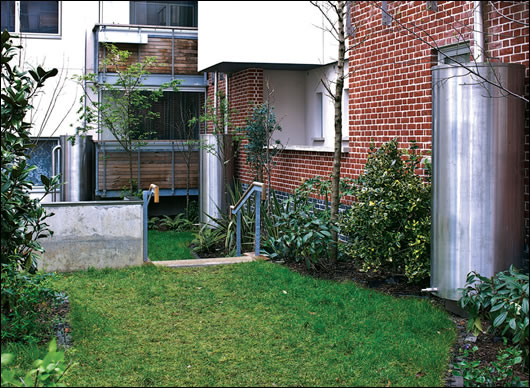
There are six stainless steel water-butts into which rainwater from down-pipes is fed for use in watering the gardens
A variety of external finishes were chosen. Stainless steel was used to frame the brick panels on the façade, while aluminium is used instead of PVC for down pipes. Western red cedar, provided from sustainable sources by Kiltown Joinery, was used for external cladding on balconies, on the waste management pavilion in the garden and on the entrances to the Crabbe Lane duplexes. The lift shaft areas were finished with 150mm of Sto Therm Classic external wall insulation, which allowed the structure to achieve the desired thermal performance without losing substantial internal wall space. Three of the five plant rooms, which are sited at the top of each stairwell and serve the apartments leading from it, are timber with a zinc finish, while the two corner structures are have a steel and timber frame with a white alu-carbon finish. The aim here was to allow these structures to be read as a white box from the street, and not conflict visually with the established contours and colours.
Bauder sedum roofs were installed across almost 90 per cent of the development. Fitted by Crown Roofing, Gareth Downes of the company explains that installing fully 1,100m2 of sedum roof in a physically tight location in an equally tight time window proved a serious logistical challenge. “It came in a 40ft container, so you had pallet after pallet after pallet coming off, and it all had to be hoisted onto the roof and laid that day.” He details the roof build up: “There’s a vapour barrier, which is fully bonded down onto the plywood decking, then on top of that we have 150mm insulation, also bonded – not mechanically fixed – there are no penetrations through the vapour barrier. Then there’s an underlay, and on top of that there’s a cap-sheet, then we have a drainage mat and finally the actual sedum blanket itself.” In addition to replacing some of the greenery lost in the redevelopment, the green roofs will retain rainwater by storing it in the plants and substrate, allowing it eventually to evaporate back into the atmosphere. By slowing down and reducing the levels of rainwater entering the drainage system, less strain is put on sewage systems, thus helping to mitigate flooding. A green roof will retain 40 – 90 per cent of average rainfall, depending on the time of year. There are also sound reduction qualities, while natural colonisation and cross-fertilisation of plants allows a natural habitat to form. The roof is generally self sustaining and requires minimal maintenance. One of the key benefits however lies in the fact that it protects the waterproofing underneath from UV damage, thermal movement and weathering generally, thereby substantially prolonging its life when compared with conventional roofing systems.
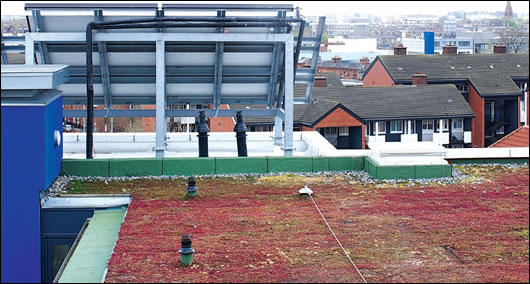
The sedum roof on one of the six storey blocks
Each block has its own dedicated plant room, featuring two high efficiency condensing gas boilers for space heating, with roof-mounted solar thermal panels taking the lead on domestic hot water. A preheat solar cylinder takes heat from the panels and conducts it to the main hot water tank, where, if it has not achieved the required temperature, it will be boosted by the gas boilers. Andrew Clifford of consulting M& E engineers JV Tierney explains the logic in using the solar preheat cylinder. “Rather than water going into the main cylinder at 10 or 12 degrees as you would normally find, the water is coming preheated by the solar. Depending on the weather situation and usage through the units, you can potentially have full temperature water coming through. In that situation, the boilers don’t kick in. Even on a cloudy day like this, you could have water coming in here at 30 degrees, so now you’re only heating from 30 degrees to 65 degrees as opposed bringing it up to temperature from a 10 degree start. That’s a 40 per cent saving right away.” The boilers are wall-mounted Remeha Quinta 61kW SEDBUK A-rated units, with the lead boiler periodically rotated to ensure a uniform usage profile. A low energy pump fitted to the main hot water tank powers a hot-water return system, which basically keeps hot water circulating at a low rate. This means that when one of the residents turns on a tap downstairs, they have instant hot water and won’t have to run the tap excessively.
The six solar panels per block cover a total area of 15.39m2, and are Viessmann Vitosol 100 flat plate collectors supplied by Precision Heating. Using DEAP calculations, it’s estimated that the solar system will provide 45 per cent of occupants’ hot water requirements annually. Mounted on fabricated horizontal A-frames, or on the roofs of the plantrooms, all enjoy a full southerly orientation.
“The heating system sends down hot water in a flow and return arrangement.” Andrew Clifford explains, “and in each of the consumer units in each of the apartments, along with a heat meter, there’s a plate heat exchanger. Essentially, the water comes in, loops through the exchanger and returns back up again. It’s a closed loop. We did that really for system security. If someone is having work done, if they have a leak, anything like that, they will not pull down the whole system.”
Each plant room has its own MCC panel, all of which are networked to a central BMS outstation to allow full remote monitoring and control, both of the heating system and the metering in individual apartments.
The district heating units in each apartment are supplied by Symtech Integrated Control Systems. Eamonn McSweeny of the company explains how they work: “The primary flow goes into each unit through the plate heat exchanger where the water is mixed with the secondary circuit. That’s heating the apartment and providing the hot water. The flow of the hot water on the primary side is measured by a heat meter, delivering a consumption figure for each apartment. Those meters are then networked back to a central computer and that basically does the calculation on consumption for each apartment. Thereafter, subject to Dublin City Council’s decision on how to manage it, they have the capacity to bill based on that consumption.” Heat is distributed within the apartments by radiators fitted with thermostatic radiator valves while a wall mounted thermostat and electronic control unit allows occupants to set times and temperatures, along with a choice of heating programmes to suit their needs.
Within the apartments, fitted units under the sink facilitate waste segregation, with feeder bins provided in the waste pavilion in the garden. The food composter, which allows residents to dispose of all forms of organic waste, is also housed here. The Swedish made Jora 5100 food waste digester was supplied by Grow Green Solutions of Wexford. This two-chamber system, Paddy Macaulay of the company explains, separates the collection process from the composting process. “That means that when the compost comes out of the machine, it’s 100 per cent finished and passes every safety standard.” Food is deposited via a chute into the first chamber where it is shredded. Wood pellets are added, and when the chamber is full, it is emptied into the second chamber where the composting process is completed. In all, it takes four to six weeks at a weekly cost, between energy and pellets, of around e8. “From start to finish, you get a 95 per cent reduction in volume from what you put in.” says Macaulay. “There is no by-product of any kind except finished compost and we can make that compost wet, dry, light, fluffy, whatever we like, and it’s got amazing growing power.”
Lighting throughout is high frequency florescent lighting, while landlord areas are on rocker switches and external lights are linked to a solar clock.
York Street was awarded funding under SEI’s House of Tomorrow programme, with co-ordination provided by CODEMA, who acted as Dublin City Council’s energy advisor and compiled the energy data for the development. Using the DEAP methodology, the development’s energy demand comes in at 89 Kwh/m2/y, which equates to An average B1 Building Energy Rating, although some apartments attained A ratings. That average breaks down into 46.37 kWh/m2/yr for space heating, 30.6 kWh/m2/yr for hot water and 12.43 kWh/m2/yr for lighting. Carbon emissions work out at 17.65 kg CO2/m2/yr.
“We’re looking forward to seeing how it works out in practise.” says Des Eliot, architect with Dublin City Council. “We’ve great hopes for it. We’re looking at this as a flagship, as a pathway for the future. Sustainability is a very important element in our development plans from now on.”
Selected project details
Client: Dublin City Council
Architects: Sean Harrington Architects
M&E engineers: JV Tierney & Co
Energy consultants: CODEMA
Main contractors: Michael McNamara & Co .
Green roof: Bauder/Crown Roofing
Insulated render system: Sto
Precast cladding: Techrete
Wool insulation & air-tightness system: Sheep Wool Insulation
Timber frame: The Timber Frame Company
Windows: Scandun/Velfac
Marmoleum flooring: Forbo Ireland
Lime render: The Traditional Lime Company
Folding balcony doors: Produkt
Solar: Precision Heating
Condensing boilers: Eurogas
District heating consumer units: Symtech
Food waste digestor: Grow Green Products
- Articles
- social housing
- Public good
- York Street
- condensing gas boiler
- timber frame
- sheep wool insulation
- Schüco bifold door systems
Related items
-
Bonny in Clyde
-
Up to 11
-
It's a lovely house to live in now
-
From Nero to zero
-
We Build Eco flat pack timber frame partnership gathers pace
-
Mass timber masterwork
-
AECB conference to showcase timber innovation
-
Measure everything
-
Renfrewshire aims for 3,500 whole-house deep retrofits
-
Heart of oak
-
Welsh social housing to embrace passive house, timber & life cycle assessment
-
Cambridge chooses passive house comfort for Kings’ College students