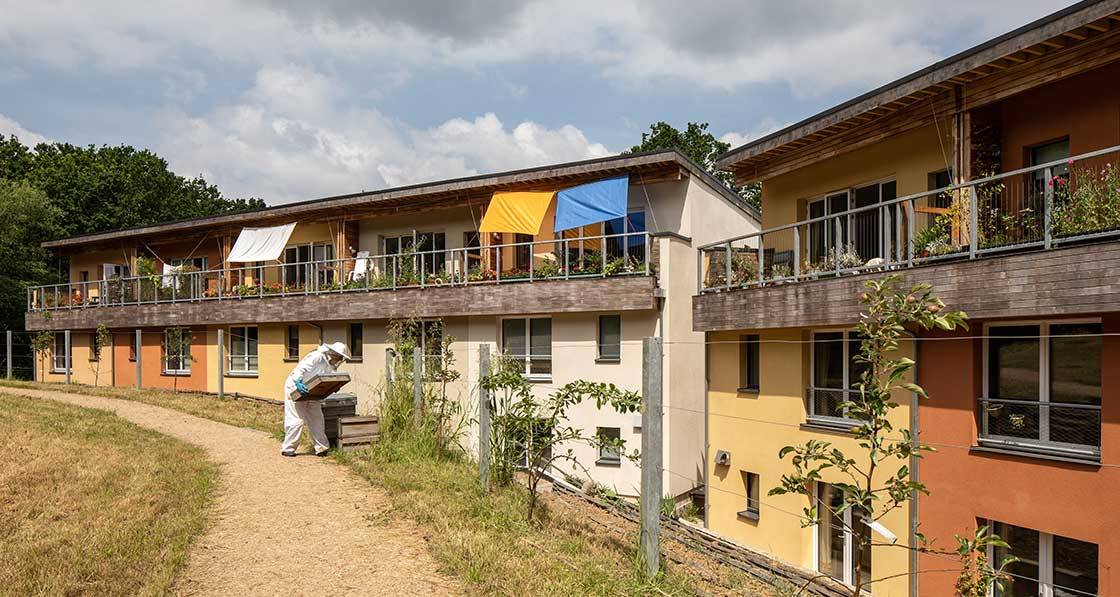
- Feature
- Posted
Grist to the mill
The pioneering Cannock Mill development in Colchester is just the second cohousing project in the UK to achieve passive house certification, making it a leader not just in terms of its thermal performance, but in demonstrating the vital role shared living can play in both building vibrant communities, and in mitigating the climate crisis.
Click here for project specs and suppliers
Building: 23-unit cohousing scheme across three buildings
Method: Timber frame
Location: Colchester, Essex
Standard: Passive house classic certified
Energy bills: £9 per month for space heating & hot water (excluding standing charges).
See ‘In detail’ for more.
Cohousing developments, where a group of people lives in a supportive community, are still quite rare in the UK. Even more unusual are cohousing projects with passive house certification like Cannock Mill Cohousing, in Colchester, Essex.
It is only the second such project to earn the distinction following Lancaster Cohousing, in northwest England.
The new Colchester community of thirty people has twenty-three properties, a mix of one, two and three-bedroom dwellings, some with garages. The age profile is on the older side. “One of the reasons there are only over 50s living here is because so few young people can afford to buy a house in the southeast,” says project architect, and Cannock Mill resident, Anne Thorne.
The profile of Cannock Mill’s residents, however, is also connected to how the idea was born. Anne and her friends in London began discussing the idea of cohousing 15 years ago. One of the major considerations was avoiding isolation as they aged. “We were concerned about being isolated in our houses in London,” Anne said. “But we also liked the idea of sharing a lot of things which reduces expenditure and carbon emissions and makes it more sustainable. Most of the residents gave up larger houses when they moved.”
The friends gathered up more enthusiasts and drew a map of potential locations within 90 minutes of London. Colchester emerged as a likely candidate. It had relatively affordable local land values and offered a balance of local amenities and access to countryside. The avoidance of rural isolation was an important consideration. Anne says the history and attractiveness of Colchester, Britain’s oldest town, gave it a “wow factor” that many other locations lacked.
The group purchased the Cannock Mill site for £1.2 million in 2014. It was just a 15-minute walk to the town centre, from where regular trains depart for London’s Liverpool Street station and the seaside, a journey of about 45 minutes either way.
Anne’s architectural practice, Anne Thorne Architects LLP, had designed both individual passive houses and larger housing developments for London authorities, such as Lambeth Council. “Over the years we designed the buildings to higher and higher insulation standards until it eventually made sense for them to be passive houses. Then some of the people in the practice qualified as passive house designers,” she said.
Anne had always wanted to design the Cannock Mill cohousing scheme, and it was clear she had the skills required. But the group still had to officially appoint her at a meeting in accordance with their democratic principles. She set about drawing up plans for a development of twenty-three homes because the site already had outline planning permission for that number. The homes were split across three buildings: one with twelve houses, one with five houses, and one with six flats.
This article was originally published in issue 40 of Passive House Plus magazine. Want immediate access to all back issues and exclusive extra content? Click here to subscribe for as little as €10, or click here to receive the next issue free of charge
To help create a sense of community, the properties are built around the existing 19th century mill building, and its pond. The mill became a communal space for guest bedrooms, a laundry and shared kitchen. “The common building is a focal point for the community, where we participate in sharing meals. You don’t have to eat them if you don’t want to, but you are expected to help out in making meals when it’s your turn. It’s a basic principle of cohousing that you act sustainably and share things,” she says.
The cohousing group always intended to convert a second building on the site, the mill house, into flats. But they delayed doing so in case it turned out to be difficult to sell all the homes in the first three blocks. “If it had come to the worst, we could have sold the mill house to help pay for the development. But in the end, we sold all twenty-three well before the contractor finished, and we’re now developing the mill house. There’s a waiting list for the new homes,” Anne says.
Anne worked closely with landscape architects who designed a sustainable urban drainage system (SUDS) that takes rainwater from the green roofs down into tanks under the road and rain gardens, which store it temporarily. It then goes into the mill pond and from there, it flows into the river.
“The drainage scheme is a fundamental part of the project as it prevents flooding from heavy rainfall,” she says. The design also had to consider an 11-metre north-facing slope from the top of the site to the bottom. As a passive house development, the scheme needed to be south facing. “Our solution was to turn the houses upside down and put the balconies and living rooms on the top floor. It means you get the sun coming in through the windows,” she says.
Most of the residents gave up larger houses when they moved.
The unusual design, however, discombobulated the local planners. They had originally given permission for twenty-three standard houses on the site, and they dug their heels in. “It took a long time to persuade them as they wanted a more conventional development, but they changed their minds when we persuaded them to visit the site. They could see why we couldn’t just have traditional cul-de-sacs because of the slope, as well as the type of community we were creating. The concept of cohousing is still so new.”
The scheme reached practical completion in October 2020. The total cost, including the £1.2 million fee for the site, came to around £10 million. All homes were sold at cost according to the non-profit principles of the community-led cohousing movement.
The new owners began to move into their homes in December 2019. The homes were all sold with 999-year leases and whenever a new owner buys a lease from the Cannock Mill Cohousing Company, they become directors. “It means we’re all leasing to each other, so we’re responsible for managing ourselves and everything else on the site, including the land,” she said.
The houses have living green roofs and are constructed in timber frame cassettes with cellulose (recycled newspaper) insulation, wood fibre and sheep wool insulation, while the flooring is made from renewable bamboo. On the outside, the dwellings are finished with ‘self-coloured’ lime render in different natural mineral colours that won’t need to be repainted. They are designed to Lifetime Homes space standards, meaning they can be made accessible at any stage, for example with the installation of lifts, or stairlifts.
Construction in progress
https://passivehouseplus.co.uk/magazine/feature/grist-to-the-mill#sigProIdb71c4eb636
From the start, the residents shared gardening, e-bikes, cars, a “library of things”, and shopping. Unfortunately, the pandemic struck only a few months after the residents moved in. Although the virus stunted the development of community life, it also meant people were less isolated than they might have been elsewhere. “During the lockdowns we collectively bought vegetables from local suppliers and shared them out. And we’ve met outside and done things together like maintaining the grounds, which has been a lot of fun because you can dig together and spend time chatting. There have also been a lot of zoom meetings with neighbours.”
With restrictions having eased, some of the community’s nervousness has diminished. And while the Covid situation was looking less certain at the time of writing with the emergence of the Omicron variant, as of mid-November Anne said that residents had begun to feel more comfortable with each other in smaller gatherings. “That’s especially true when there is plenty of fresh air. One of the good things about passive houses is they have a constant flow of fresh air. A lot of people have been happier to meet indoors in recent weeks and the meals in the common house are better attended now,” she says.
We were concerned about being isolated in our houses in London.
Increasingly, the spontaneous interactions that are part of the cohousing spirit are becoming a way of life. “If you see someone having a cup of tea on the common house deck overlooking the pond, you go and join them. Designing the terrace of the housing around the pond makes it a more sociable environment. Just this afternoon, the fish man arrived in his van, and everyone rushed out to buy some,” she said. “The intermediary spaces are important in encouraging the sense of community when you’re chatting by the coffee machine, or the pond.”
As time goes on, the community, which advocates a policy of “active ageing”, hopes to take advantage of everyone’s skills. Anne says the residents enjoy many hobbies, though they were temporarily frustrated during the lockdowns. These include artistic activities, such as carving, ceramics, textiles and painting, music and singing, gardening, cooking, walking, cycling and swimming.
Everyone in the development belongs to at least two subgroups, working on areas such as building, finance, communications, membership and social activities. The executive, which includes a chair, secretary, treasurer and subgroup chairs, plus a ‘lay member’, reports to the monthly board meetings at which subgroups also present reports. Members attend meetings in person or by video conferencing and cooperate through email. The community has set up an “ever after” subgroup to think up creative ideas for the future management of the site.
Anne worked on the project with Japanese- born passive house designer Junko Suetake, who she has collaborated with for many years. “We worked closely as a team, with Anne and several very talented architectural assistants. I was in charge of all three PHPPs [passive house design files], which was the same as applying the principles to other passive houses I’ve worked on, but on a massive scale,” Junko says.
The scheme was certified as three separate buildings. Junko says one challenging aspect of the project from a passive house point of view was the requirement for garages. The planners insisted on a minimum number of car parking spaces, and due to the nature of the site, the most efficient option was to install some of these as garages within the thermal envelope of the houses.
“That was really challenging, because normally garage doors are not airtight and perform poorly from a thermal point of view,” says Junko. The solution was to install Lacuna triple glazed bifold doors across the garage openings, and now, because car ownership on the site is low, residents tend to use these large open spaces as workshops or studios rather than for car parking. “It’s quite nice, if you walk in front of the houses you can see all the various activities going on,” she says.
Each dwelling has heat recovery ventilation, and there is a solar PV array that provides electricity for the communal spaces. There has been no embodied carbon assessment of the project to date, and while the timber frame walls and natural insulation material should reduce the whole life carbon footprint, on the sloping site there was also a structural need for higher carbon materials like reinforced concrete in the foundations, and a steel frame for the balcony.
At first, Junko was sceptical about the cohousing approach. She says it seemed like such a lot of effort with meetings every weekend, tight budgets, and endless decision-making. “I thought I wouldn’t be able to bear it myself. But I’m now a total convert. I have seen the many fantastic things they’re doing on site and the strong sense of community that’s developing. They have a lot of people from different backgrounds and they’re great at problem solving together. And now I think what they’ve achieved is a triumph.”
Selected project details
Client: Cannock Mill Cohousing Colchester Ltd
Architect/passive house design: Anne Thorne Architects LLP
M&E engineer: Alan Clarke
Civil & structural engineering: Ellis & Moore Consulting Engineers
Main contractor: Jerram Falkus Construction
PH consultant to contractor: Etude
Thermal bridging calculations: Elemental Solutions
Quantity surveyor: Peter W Gittins
Airtightness tester: Paul Jennings
Passive house certifier: WARM
Landscape planning: Studio Engleback
Landscape architect & SUDS: Robert Bray Associates
Render system with wood fibre board: Lime Green Products
Wall & roof insulation: Warmcel, via PYC Systems
Recycled jute insulation & airtightness products: Ecological Building Systems
Sheepwool insulation: Thermafleece
MVHR, windows and doors: Green Building Store
Bi-folding doors: Lacuna UK and Ireland Ltd, via Passivhaus Store
European Oak cladding: Vincent Timber
Kitchens: Falkus Joinery
Flooring: Simply Bamboo
Green roof: Bauder, via the Urban Greening Company
Green roof design: Green Infrastructure Consultancy
Zinc roof: Nedzinc
In detail
Building type: 23 homes — a mixture of one, two and three-bed houses and flats — across three buildings: 316 m2 (six-flat block), 655 m2 (five-house block) and 1,200 m2 (12-house block). Figures are treated floor areas. Gross internal floor area of dwellings ranges from 52 m2 to 144 m2. There is also a common house, in the existing listed mill building.
Location & site: Cannock Mill Rise, Colchester, Essex
Completion date: December 2019
Budget: £7 million approx
Passive house certification: All three blocks are passive house classic certified.
Space heating demand (PHPP): Five-house block: 15.3 kWh/m2/yr; 12-house block: 10.6 kWh/ m2/yr; six-flat block: 14.3 kWh/m2/yr
Heat load (PHPP): Five-house block: 10.4 W/ m2; 12-house block: 10.2 W/m2; six-flat block: 10.2 W/m2
Primary energy non-renewable (PHPP): Five-house block: 83 kWh/m2/yr ; 12-house block: 81 kWh/m2/yr; six-flat block: 108 kWh/m2/yr
Primary energy renewable (PHPP): Five-house block: 72 kWh/m2/yr; 12-house block: 74 kWh/m2/ yr; six-flat block: 97 kWh/m2/yr
Heat loss form factor (PHPP): Five-house block: 2.63; 12-house block: 2.33; six-flat block: 3.53 Overheating (PHPP): Five-house block: 0 per cent; 12-house block: 2 per cent; six-flat block: 4 per cent
Number of occupants: 30
Airtightness (at 50 Pascals): Each dwelling was individually tested to be under 0.6 air changes per hour; for the purposes of passive house certification each of the three buildings was submitted at 0.6 ACH.
Energy performance certificate (EPC): B 82-89
Measured energy consumption: Based on monitored electricity and gas bills during 2020, the total energy consumption of the three blocks was: 41.28 kWh/m2 (five-house block); 40.85 kWh/ m2 (12-house block); 65.51 kWh/m2 (six-flat block). All of these are within the figures projected within PHPP.
Thermal bridging: Ground wall junction: +0.023 W/mK. Achieved using one course of AAC block Airtec 7 lined with XPS insulation to the bottom of the wall. Floor insulation PIR is above the concrete slab and below screed. Threshold: 0.047 Wm/K with single AAC block Airtec 7 in line of door. Separating wall bottom: +0.08 W/mK using one course of AAC block Airtec 7. Floor insulation PIR is above the concrete slab and below screed. Balcony wall bottom: + 0.076 W/mK, separating the steel connection from the timber structure and the insulation zone.
Energy bills (estimated): We estimated energy bills for a hypothetical average dwelling at Cannock Mill by taking the average electricity and gas consumption per m2 across the 23 units, and multiplying it by a hypothetical average sized dwelling for the scheme of 94.6 m2. We then fed the electricity and gas consumption figures for this dwelling into uSwitch.com, and the cheapest available tariff projected an annual gas bill of £113 or £9 per month (for space heating and hot water) and an annual electricity bill of £398. Both figures include VAT but not standing charges.
Ground floor: 10 mm bamboo flooring on 65 mm screed, on 150 mm PIR insulation (houses) or 150 mm phenolic insulation (flats), on 250 mm reinforced concrete, on 225 mm Cellcore HX S9/13 board. U-Values: 0.135 W/m2K (houses) and 0.108 W/m2K (flats)
Walls (flats): 20 mm fire retardant treated European Oak cladding over insect mesh (flats) or zinc cladding on underlay and 18 mm WPB plywood externally, on 25 mm ventilation void, on Solitex Fronta Quattro membrane, on 22 mm wood fibre insulation, on 400 mm Warmcel cellulose insulation between structural timber frame and sub-frame, on 12 mm Smartply Propassiv airtight OSB, on 25 mm services zone insulated with Thermo Hemp Combi Jute, on plasterboard and paint finish. U-values: 0.092 W/ m2K (flats)
Walls (houses): Lime render on 40 mm Steico Protect wood fibre insulation, on 350 mm Warmcel cellulose insulation between structural timber frame and sub-frame, on 12 mm Smartply Propassiv OSB, on 25 mm service zone, on plasterboard and paint finish. U-value: 0.108 W/m2K
Roof (houses): Vegetation externally, followed underneath by 120 mm growing medium & drainage layers, on Bauder waterproof protection, on 18 mm OSB3, on 125 mm ventilation zone, on Solitex Plus membrane, on 18 mm OSB3, on 360 mm Warmcel cellulose insulation between 360 mm I-joists, on Intello Plus airtightness membrane, on 50 mm battens, on plasterboard and paint finish. U-Value: 0.111 W/m2K
Roof (flats): Corrugated steel sheet galvanised or zinc standing seam on underlay externally, followed underneath by 18 mm WBP plywood, on 50 mm ventilation layer, on weather tight membrane, on 18 mm OSB3, on Warmcel cellulose insulation between 400 mm I-joists, on Intello Plus airtightness membrane, on 96 mm sheepwool insulation, on plasterboard and finish. U-value: 0.079 W/m2K
Windows & external doors: Green Building Store Progression timber frame internally, no frame externally, triple glazed argon-filled. Whole window U-value: 0.77 W/m2K. Green Building Store ULTRA timber frame windows and doors, triple glazed argon-filled. Whole window U-value: 0.94 W/m2K. Lacuna timber frame triple glazed argon-filled bi-fold doors. U-value: 0.95 W/m2K Heating system: Worcester Bosch Greenstar 28 and 36 CDi Compact gas boilers to each dwelling, distributing heat via radiators.
Ventilation: Zehnder Comfoair 160 heat recovery ventilation system for smaller dwellings — Passive House Institute certified to have heat recovery rate of 89 per cent. Zehnder Comfoair Q350 heat recovery ventilation system to larger dwellings — Passive House Institute certified to have heat recovery rate of 90 per cent.
Water: Water saving models of WC and taps. Sustainable urban drainage system across the whole site. Rainwater gardens.
Electricity: Solar PV array with 16 x 250 W modules.
Green materials: Timber frame lightweight structure except foundation and ground slab. The main insulation materials to the dry part of the construction are natural materials: Warmcel, wood fibre board, sheep wool, Jute insulation. The main external finish is timber or lime render
Image gallery
https://passivehouseplus.co.uk/magazine/feature/grist-to-the-mill#sigProId2ba04c60b0