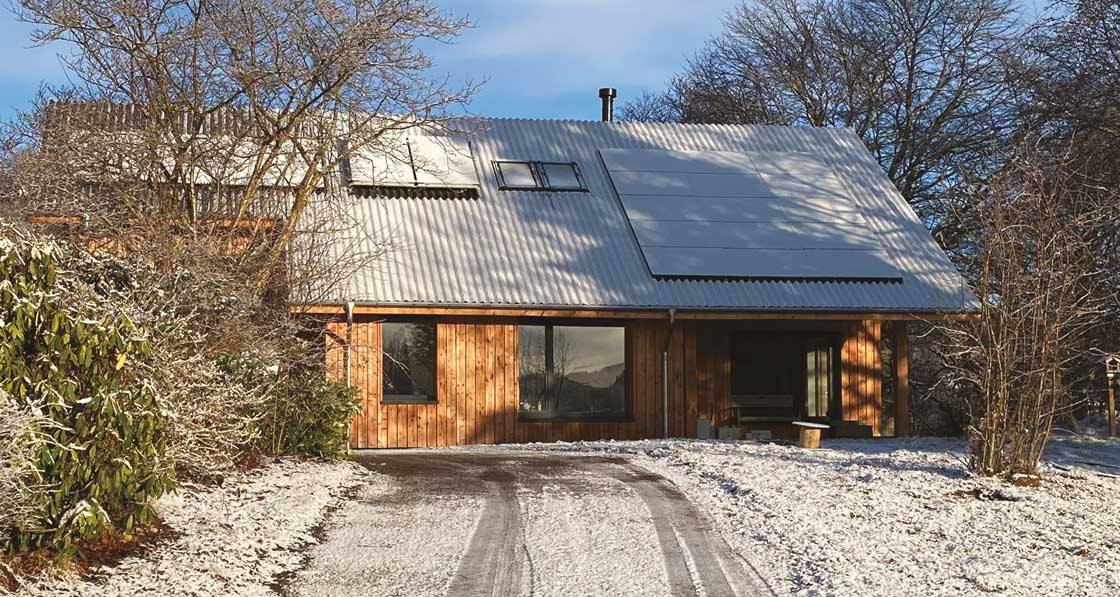
- New build
- Posted
Scottish passive house built with an innovative local timber system
A beautifully detailed and rustic new passive house in the north of Scotland was built with a unique off-site construction system using local timber, and was created by a design-and-build firm that aims to put sustainability at the heart of everything it does.
Click here for project specs and suppliers
Energy bills £35 per month average bill for all energy
Building: 137 m2 fully prefabricated timber frame dwelling
Site: Strathpeffer village, Easter Ross
Standard: Passive house classic
If you wanted to build a house to the passive house standard but with the strongest possible nod to sustainability, timber frame construction would probably rank high on the shortlist of build methods.
But what if you were concerned about the sustainability and carbon footprint of imported timber? That’s the predicament that Tim Dawson of Strathpeffer in Scotland found himself in after receiving inheritance from his late father in 2015, enabling him to fulfil a dream of building a new home.
After a long search, he had found a local site with full planning permission for the replacement of a derelict bungalow. It also came with planning permission in principle for a second dwelling, but he liked the site so much he bought it in 2018 with the firm intention of building only one house on it.
His other firm intention was in relation to the brief for his new ‘forever’ home. He wanted a modest, two-bed dwelling with generous office space, a utility room and adjoining workshop, and built to fully certified passive house standard but with the lowest possible carbon footprint, and constructed with local timber.
One of the two local architects that Tim consulted during his research was a unique design and build firm in Inverness called Makar. Tim felt that Makar founder Neil Sutherland was very much on his wavelength, despite the fact that the firm had never previously built a passive house (though they had designed a community centre in nearby Gairloch that is passive house certified).
Tim was particularly impressed with the standard Makar system, an off-site, timber-based panel system very similar to a SIPS (structurally insulated panel system).
SIPS is essentially insulated timber panels assembled together, often without the need for separate structural elements, but a typical build-up is likely to have its fair share of synthetic materials like adhesives, timber preservatives and polyurethane foam insulation.
This article was originally published in issue 35 of Passive House Plus magazine. Want immediate access to all back issues and exclusive extra content? Click here to subscribe for as little as €10, or click here to receive the next issue free of charge
But Makar describes its unique system as ‘n-SIPS’ because of its use of all natural materials, including untreated timber, Warmcel cellulose insulation (made of recycled newspaper) and wood fibre board (made from timber waste).
The timber used for the frame is untreated Scottish-grown spruce, while Scottish-grown larch or Douglas fir is the choice for the cladding and post-and-beams. Although their system didn’t initially meet the passive house standard, Sutherland and his architect colleague, Catriona Kinghorn, were keen to take up the challenge of designing and building a passive house as they felt confident it only needed minor amendments to meet the standard. But given its northerly highland location, it was necessary to achieve even more onerous U-values than normal for a UK passive house.
If you’ve been out on a Scottish site in the middle of winter, you really begin to appreciate how important is to have a facility that is well lit and heated.
Kinghorn had qualified as a passive house designer a year before she and Sutherland met Tim. “And, actually, at the time we met Tim,” recalls Kinghorn, “I was due to be away that summer in Japan and New England visiting other passive house designers — I had a travel grant awarded by the Winston Churchill Memorial Trust — so this was always on our mind. And I guess Tim really appeared at a very fortuitous moment for the company, because it was a real meeting of minds.
“Tim’s brief was very clear. It was a really well written brief. He didn’t try to design the house itself, but he was clear on what he wanted and he didn’t want. And he really understood passive house principles; he’d made the effort, he had the technical understanding of passive house to understand why it was supported and he’d made that decision. He wanted to reach that standard.”
The site also lent itself well to passive house design, as it was well orientated with a good southerly aspect, slightly sloping downhill, with deciduous trees to the east and an area of high ground to the west — perfect for low sun shading.
It’s clear that part of the meeting of minds that Kinghorn describes is Tim’s attraction to the Makar commitment to deliver buildings that are healthy and sustainable, while also attaining his prized goal of a certified passive house.
“Passive house is an energy-balance calculation, with no comment on how the energy balance is achieved,” says Kinghorn.
The Makar prefabricated timber frame system being built in their workshop, showing 1 the frame, 2 the postbase, 3 the roof panel, and 4 the cladding; 5 & 6 assembly of the frame on-site; 7 the panels are built complete with insulation, doors, windows, roof and cladding; 8 18 mm OSB board was used as an internal airtight layer, and taped at all junctions; 9 the walls are fi nished inside with plasterboard enclosing a woodfi bre-insulated service cavity.
“We would not have been comfortable delivering a passive house project relying solely on materials we felt are harmful to the user or the environment.”
The solution was the Makar standard Warmcel-insulated timber frame but boosted with a 180 mm (compared to the normal 60 to 80 mm) outer layer of tongue-andgroove wood fibre insulation board. Careful detailing at junctions ensured a continuous insulation jacket. The result is a ‘breathing’ wall construction, which allows moisture vapour to dissipate naturally through the wall. All timber is untreated, while an 18 mm OSB board was used as an internal airtight layer, and taped at all junctions.
“We worked really hard to reduce the timber content of the panels as much as possible [to allow more space for insulation], and to develop standard off-site panel joints that maintain the thermal envelope,” says Kinghorn. She adds that they plan eventually to use Scottish-timber-produced wood fibre products in order to reduce reliance on insulation materials imported from abroad.
Interestingly, all Makar-built houses today are specified with MVHR (mechanical ventilation with heat recovery) but Kinghorn points out that even 10 to 15 years ago the build-up of moisture was far less of an issue with its breathable walls than other modern build methods. “Once you get to a certain level of airtightness, like passive level airtightness, you do need the MVHR ventilation,” she says. “So that goes into all of our houses as standard anyway.”
Underlying Makar’s commitment to a wide-ranging sustainable rural economy in the Highlands is that as well as tying in interests in forestry, regeneration, timber use and healthy construction and design, Neil Sutherland’s family also run an organic farm on the same site as the company’s factory. Needless to say, being able to build its wall panels off-site conferred several advantages in meeting the challenge of building Tim’s passive house, not least a high degree of quality control.
“Our drive is to do things off-site as much as possible, simply because when you’ve been out on a Scottish site in the middle of winter, you really begin to appreciate how important is to have a facility that is well lit and heated, and everyone’s working on benches, tables and the panels are laid horizontal.”
Kinghorn also appreciates the convenience of working right next door to the factory. “As a designer, especially as a passive house designer, working literally yards away from the person building wall panels means you can literally come out and talk through problems, solve them there and then and you don’t need to wait a week while someone gets out to the site.”
The panels, which are built complete with insulation, doors, windows, roof and cladding, are typically 2.4 to three metres wide by 4.8 metres high, and weighing one to 1.5 tonnes. House superstructures are assembled on site by a small team using a 40 or 55 tonne crane, and are usually made wind and watertight in less than a week – another advantage when building in remote rural locations.
In a bid to keep its use of concrete to a minimum, the company also usually specifies pier foundations on three-metre grids to support the four panels that make up a typical house. At the time however, the team decided to go with an insulated concrete slab for Tim’s house because they were unsure if their pier foundation would meet passive house criteria, leading to a “slight disappointment for us and for Tim”, says Kinghorn. “Looking back, we were maybe a little over-cautious as it was our first passive house build.”
The final result is a lovely, understated home that really blends well into its environment, while on the inside, there is a real character to the rooms, from Tim’s study / music room, to the roof-lit mezzanine level that brings light down to the dining area through a slatted timber screen.
“It really feels like a home, says Kinghorn. “I think we responded to Tim’s brief well — creating that strong link to the outdoors, and playing with height and light to make some areas cosier while other areas feel bigger and higher.”
“A really important part of the brief was a connection to the outdoors and the garden from inside, with sheltered outside space — commonly referred to as ‘sitooteries’,” added Kinghorn.
Although the house requires very little by way of space heating, Tim chose to install a wood burning boiler stove, which supplies hot water to two radiators as well as domestic hot water. The hot water is also supplemented by solar thermal panels and PV panels (the PVs are linked to an immersion heater, mostly used in the summer months).
The final result is a lovely, understated home that really blends well into its environment.
A rainwater harvesting system supplies water to the WCs, washing machine and garden, while an electric car charging point is located by the main door.
Tim has been living in the house since September 2019, and is delighted. “Where do I start? The house fits beautifully into the landscape. Everyone bar none has said that they like the look of the house. Its energy efficiency is looking promising in these early days. It responds very well to the weather and is warm in the winter and pleasantly cool in the summer. It’s easy to live in and to keep clean.”
He reports that since his smart meter was installed in February this year, he has used 684 kW of electricty from the grid and exported 2,106 kW. “The house is roughly twice the floor area of my old one yet the running costs are around a third compared with previously. Once I start to receive the export tariff the costs may reduce again.”
Kinghorn describes Tim’s house as a labour of love. It may have taken more than a year from start to finish, but the result is a passive house system that can be easily replicated, and likely to take less time to build for future clients. Furthermore, the firm won two awards for it from the Alliance for Sustainable Building Products in the Best New Build and Best Product categories.
“Now we have a passive-compliant off-site system that we can replicate time and time again,” she says.
Selected project details
Client: Tim Dawson
Architect: Makar
Civil & structural engineer: SF Structures
Build system: Makar
Contractor & project management: Makar
Passive House certifier: Passivhusbyrån Ingo Theoboldt
Electrical contractor: ICM Electrics
Airtightness tester/ MVHR installer: Airtight Build
Airtightness tapes: Siga
Windows & doors: Internorm by Scotia
Cellulose insulation: Warmcel, via PYC Group
Wood fibre insulation: NBT / Soprema
Floor insulation: Quinn Building Products / Kingspan
Thermal blocks: Forterra
Roof lights: Fakro, via Caley Timber
Boiler stove, thermal store & solar thermal: Ashburn Stoves
Solar PV: AES Solar
Heat recovery ventilation: Paul, via Airtight Build
Rainwater harvesting: Rainwater Harvesting Ltd
Kitchen: Howdens
Larch cladding: BSW
Flooring: Russwood
Roofing: Nu-Style Products
Drainage design: Caintech Ltd
In detail
Building type: 137 m2 (treated floor area) 1.5 storey 3-bedroom detached house built w/ prefabricated timber system.
Site & location: Strathpeffer, Easter Ross, Highlands. Built in garden of a derelict bungalow on the outskirts of the village.
Completion date: September 2019
Budget: £365,000 ‘turn-key’ construction cost
Passive house certification: Passive House Classic certified
Space heating demand (PHPP): 15 kWh/m2/yr
Heat load (PHPP): 12 W/m2
Primary energy non-renewable (PHPP): 62 kWh/m2/yr
Primary energy renewable (PHPP): 145 kWh/m2/yr
Renewable energy generation (PHPP): 69 kWh/m2/yr (relative to building footprint)
Heat loss form factor (PHPP): 2.62
Overheating (PHPP): 0% of hours above 25C
Number of occupants: 1
Airtightness (at 50 Pascals): 0.34 ACH
Energy performance certificate (EPC): A 115
Measured energy consumption: From October 2019 to July 2020 inclusive (10 months), the house consumed 2,973 kWh of grid electricity. Over the same time period the solar PV array generated 4,324 kWh. A smart meter was installed in February 2020, and from then until July 2020 inclusive the house exported 2,106 kWh of solar electricity, consumed 1,618 kWh of solar generated electricity, and used 684 kW of grid electricity. House electricity consumption includes electric car charging.
Thermal bridging: Thermal bridging was largely avoided through the use of an external 180 mm wrapped wood-fibre board insulation. All bridges were calculated using Therm software, and checked by the PH certifier. Ambient thermal bridges: 159m at 0.003 W/mK. Perimeter thermal bridges: 48m at 0.007 W/mK
Energy bills (measured or estimated): Tim Dawson’s electricity bill averages to £35 a month for grid electricity, which includes some hot water generation but no space heating. He does not receive a feed-in-tariff for exported electricity. All wood used so far for the wood burning boiler stove has been from site offcuts.
Ground floor: Hardwood floor finish on 45 mm battened service zone, on 125 mm reinforced concrete slab, on slip membrane, on 300 mm Quinn Therm ground floor insulation, on 1200 g DPM, on 150 mm sand blinded hardcore. Perimeter load bearing Thermalite Aircrete Trenchblock insulated externally with NBT plinth board. U-value: 0.071 W/m2k
Walls: 150x25 mm vertical board-on-board heartwood larch cladding on 38x50 mm horizontal battens, on 25x50 mm vertical battens, on prefabricated wall panel comprising: 180 mm Pavatex Isolair insulation board on C16 kiln-dried regularised untreated 245 mm studs with cellulose insulation, with 18 mm OSB 3 internal lining board as airtight layer taped at all junctions. Internally there is a 45 mm battened service zone insulated with Pavaflex wood fibre insulation, finished with 12.5 mm plasterboard, taped and filled. U-value: 0.091 W/m2k
Roof: Anthracite grey big six profile metal roofing on 50x50 mm battens, on 120x50 mm Douglas fir secondary rafters screwed to prefabricated roof panel comprising: Roofshield membrane on 180 mm Isolair wood fibre insulation, on 245 mm C16 kiln-dried regularised untreated rafters with cellulose insulation, lined internally with 18 mm OSB 3 airtight layer, all junctions taped. 45 mm internal service zone insulated with Pavaflex wood-fibre batts. 12.5 mm plasterboard internally, taped and filled. U-value: 0.090 W/m2k
Windows: Internorm HF310 aluminium/timber composite triple glazed windows. Average installed U value average: U-value: 0.8 W/m2k
Roof windows: Fakro FTT U8 Thermo triple glazed roof windows. Average installed U-value: 0.94 W/m2k
Heating system: Verner 13/10.2 wood burning boiler stove linked to large thermal store feeding 2 x radiators and 2 x towel rails. The thermal store is also fed by the solar thermal panels and is topped up by immersion via the PV electric panels. The solar thermal array generated 2,000 kWh of energy between November 2019 and July 2020 inclusive. Ventilation: Paul Novus 300, Passive House Institute certified to effective heat recovery efficiency 93%.
Water: A rainwater harvesting system is installed, which supplies both WCs, the washing machine and garden taps. Electricity: 6.87 kW solar PV array. Once the thermal store is up to temperature the PV panels automatically divert to the electric car charging point. See ‘measured energy consumption’ above for PV kWh generated & exported.
Green materials: Dwelling uses natural materials in an off-site system that can be easily reproduced to meet the PH standard. Local timber for wall panels and cladding, wood fibre and cellulose insulation.
Image gallery
https://passivehouseplus.co.uk/magazine/new-build/highland-warrior-scottish-passive-house-built-with-innovative-local-timber-system#sigProId24ee667019